

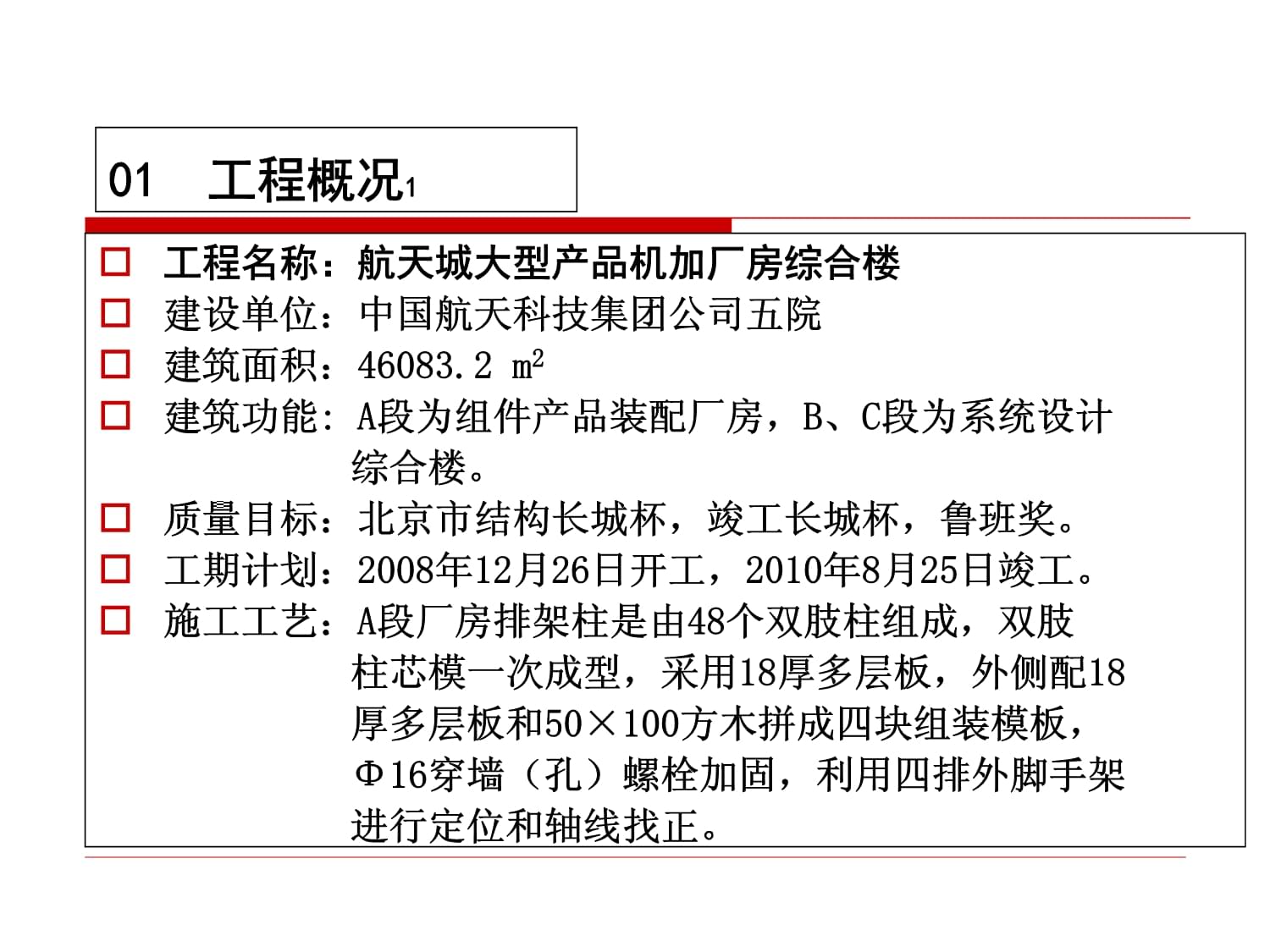


版权说明:本文档由用户提供并上传,收益归属内容提供方,若内容存在侵权,请进行举报或认领
文档简介
1、提高现浇混凝土双肢柱截面尺寸合格率 工 程 概 况01 小 组 概 况02 选 题 理 由03 现 状 调 查04 确 定 目 标05 原 因 分 析06 要 因 确 认07 制 定 对 策08 对 策 实 施09 效 果 检 查10 巩 固 措 施11 今 后 打 算12QC小组活动目录01 工程概况1工程名称:航天城大型产品机加厂房综合楼建设单位:中国航天科技集团公司五院建筑面积:46083.2 m2建筑功能: A段为组件产品装配厂房,B、C段为系统设计 综合楼。质量目标:北京市结构长城杯,竣工长城杯,鲁班奖。工期计划:2008年12月26日开工,2010年8月25日竣工。施工工艺:A段厂
2、房排架柱是由48个双肢柱组成,双肢 柱芯模一次成型,采用18厚多层板,外侧配18 厚多层板和50100方木拼成四块组装模板, 16穿墙(孔)螺栓加固,利用四排外脚手架 进行定位和轴线找正。01 工程概况2 工程特点单层工业厂房现浇混凝土双肢柱为薄腹多孔柱,柱高,断面尺寸大,芯孔位置不易保证。双肢柱结点核心区最多达三向六层钢筋重叠,如何既保证钢筋位置准确,核心区以下混凝土密实,模板加固用穿柱螺栓安装是本结构工程的重点。为了解决现浇混凝土双肢柱施工这个难题,公司成立了现场QC小组,由公司和项目共同研究,选择确定双肢柱施工难点进行课题攻关。 02 小组概况1小组名称河北建设集团北京公司航天城项目部Q
3、C小组小组类型现场型成立时间2009年4月1日注册编号BQ2009002课题名称提高现浇混凝土双肢柱截面尺寸合格率小组人数11人活动时间2009年4月1日至2009年8月30日活动次数/出勤率10次/98%循环次数1次TQC培训时间人均53小时 小组成员表序号姓 名年龄性别学历技术职称组 内 分 工TQC教育学时1王志义43男大专高级工程师组长:全面组织、协调552李贵良43男大专高级工程师副组长:方案策划553赵立如38男大专工程师组员:现场技术负责544刘新立43男大专高级工程师组员:现场技术负责535郑瑞恒40男大专工程师组员:对策实施526郝春霞34女大专工程师组员:对策实施537曹鹏
4、飞27男大专助理工程师组员:对策实施558梁福辉29男大专助理工程师组员:质量检测539霍 峰34男大专工程师组员:现场技术负责5210吴根顺42男高中技师组员:质量检查5511林 刚40男高中无现场操作50制表:刘新立 日期:2009.04.1502 小组概况2QC小组活动实施计划表时间内容4月5月6月7月8月P选择课题现状调查设定目标分析原因确定主要原因制定对策D按对策实施C检查效果A制定巩固措施总结和打算制表:刘新立 日期:2009.04.1502 小组概况303 选题理由1结构工程内坚外美创结构长城杯金杯塑造精品工程追求自我超越结构长城杯、竣工长城杯、争创鲁班奖统计同类柱截面尺寸合格点
5、率为89%选 择 课 题提高现浇砼双肢柱截面尺寸合格率质量目标现场问题顾客需求企业方针制图:刘新立 日期:2009.04.16921-3大件厂房80%100%60%40%20%088%90%项目 名称合格率平均值89%统计同类柱截面尺寸合格点率为89%03 选题理由204 现状调查1同类工程调查对921-3及D7建筑物柱截面尺寸偏差进行现场调查,结果如下表:检测部位项目名称检测值(共82个数据)检查 点数合格 点数合格率柱截面尺寸(允许偏差为(3mm)921-3工程中心区7号建筑物+2-10+2-1+3+2-10+2403587.5共检查82个点,其中合格73点,合格率89。+3+2+4+1+
6、20+1+7-10+50+3+2+5+3+2+3+1+2+3+2-10+6+2-1+3+2-1大型产品机加厂房综合楼(D7)+3+2+7-10+3+2+1+2+3423890.5+2+1+30+5+3-1+2+3+1-1+2+3+3-1+2+2+1+2+3+6+10+2+5-1+3-2+3+2+3+3混凝土施工截面尺寸偏差调查表表4-1制表:刘新立日期:2009-04-16柱截面尺寸偏差进行调查结果如下:本工程调查分析04 现状调查2调 查 表表4-2序号分析调查项目分析调查情况1截面尺寸偏差按结构长城杯标准(-3 +3mm),检查82点,合格73点,合格率89%。制表:刘新立日期:2009-
7、04-16 结论1.目前施工质量状况,截面尺寸合格率89%,有改进可能。04 现状调查3工艺流程分析根据本工程现状,对双肢柱施工工艺流程进行分析,确定影响截面尺寸偏差的因素。双肢柱施工工艺流程脚手架安装柱筋安装定位卡安装安装芯模预埋件安装柱外模安装柱模验收连梁钢筋安装柱筋验收浇筑混凝土上部柱段施工牛腿及上部横梁 项目部针对影响双肢柱几何尺寸的因素进行综合分析汇总,确定问题主要存在于以下几个方面:模板支设偏差较大;钢筋安装偏差较大;预埋件留设位置偏差较大;其它因素。影响因素分析04 现状调查4影响因素调查统计序号内容频数累计频数频率%累计频率%1模板支设质量差6667672钢筋安装误差大1711
8、783预埋件留设偏差大1811894其它1911100合计N9截面尺寸合格率低调查统计表表4-3日期:2009-04-16制表:刘新立 结论模板支设质量差占总频次的67%,是主要问题。04 现状调查5主要问题模板支设质量差占67%预埋件留设偏差大04 现状调查6截面尺寸合格率低具体问题排列图截面尺寸合格率低具体问题排列图存在问题0模板支设质量差110累计百分比(%)频数(次)其它钢筋安装偏差大978%89%存在问题0模板支设质量差60累计百分比(%)频数(次)N91累计百分比(%)存在问题0模板支设质量差频数(次)存在问题0模板支设质量差100%67%频数(次)75%50%25%53705 确
9、定目标1现状值目标值95%89%目标值的确定: 2009.04.16,我QC小组召开会议,确定控制目标为: 双肢柱混凝土截面尺寸合格率提高到95%。达到合格百分率%项目名称目 标截面尺寸合格率提高到95%目标可行性分析本工程设定的质量目标以往施工的历 史技术水平主要问题解决80%可能达到的水平确保结构长城杯、竣工长城杯,争创鲁班奖。(1-89%)X67%X80%+89%=95%以往项目截面尺寸合格率水平曾经达到90.5%。结 论经过努力,95%的目标可以实现。05 确定目标2模板支设质量差模板与砼柱顶接不紧人未设置混合工种环料模板变形模板体系受扰动变形马道搭设不规范自检不严格振模板的方式振实砼
10、横内钢筋、预埋件空隙小浇砼时踩支撑模板材质差模板进场验收不严未配备30棒配合振捣测机法作业人员不稳定校核不准确使用钢尺校核不熟悉使用经纬仪岗前培训不足木加工尺寸不准设备维修保养不及时未严格执行保养维修制度模板拼缝不严模板拼缝错台模板拼缝处漏浆模板与龙骨有缝隙模板龙骨尺寸不准模板体系刚度差模板散拼受力不均模板安装后移位06 原因分析107 要因确认1序号末端原因标准确认方法确认结果确认结论确认时间确认人1未设置混合工种定岗定员现场检查具体人员已确定非要因2009.5.3吴根顺、林刚2岗前培训不足考核合格查阅培训记录考核合格非要因2009.5.1霍峰、梁福辉3未严格执行维修保养制度按制度及时维护查
11、维修保养记录记录齐全有效非要因2009.5.5曹鹏飞、郑瑞恒4模板与砼柱顶接不紧模板与柱顶接严密现场调查明确竹胶板与柱身搭接宽度后,可更好保证顶接严密。非要因2009.5.5刘新立、赵立如5模板龙骨尺寸不准模板龙骨尺寸偏差小于1mm。现场调查偏差大于1mm 。要因2009.5.5李贵良、郝春霞6模板散拼受力不均模板缝隙高低差小于1mm。现场调查模板拼缝多,板缝高低差大于1mm,难于保证质量。要因2009.5.5赵立如、李贵良7模板拼缝不严模板拼缝严密不漏浆现场调查模板直接对接,易漏浆。要因2009.5.5曹鹏飞、王志义8模板进场验收不严按标准进场验收,有记录查阅物资验收记录物资进场已验收合格,
12、有记录非要因2009.5.5郝春霞、刘新立9自检不严格自检记录齐全有效查阅自检记录自检齐全有效,有整改,有结果非要因2009.5.5霍峰、梁福辉10未配备30棒配合振捣砼振捣密实现场调查振捣密实无缺陷非要因2009.5.5郑瑞恒、吴根顺表7-1制表:刘新立 审核:李贵良 日期:2009年5月10日07 要因确认2确认内容未设置混合工种确认方法现场检查确认过程 现场检查,双肢柱施工划分为3个流水段,每一列纵向柱为一个流水段。每个流水段安排一个相对固定的小组,其中包括木工、钢筋、砼、焊工等主要工种人员,确保每根双肢柱从基础到顶各工种均为相对固定的人员进行施工,易于质量控制。确认标准定岗定员确认结果
13、每个双肢柱参与施工的各工种人员均相对固定。确认结论非要因确认时间2009.5.3确认人吴根顺、林刚确认过程1表7-2制表:刘新立 审核:李贵良 日期:2009年5月10日确认内容岗前培训不足确认方法查阅培训记录确认过程 查阅2009年03月至2009年05月培训记录,3个木工班组全体员工共计组织集中培训26次(参加培训人员中包括新转岗人员,培训内容包括理论知识与现场技能培训)。查阅技术交底,已明确为保证双肢柱尺寸准确,必须采用经纬仪进行校核,保证尺寸精确。查阅培训记录,有关于经纬仪使用的相关培训,培训参加人员6人,培训时间2小时,现场考核全部合格,有记录。确认标准考核合格确认结果经现场考核全部
14、合格,满足施工使用要求。确认结论非要因确认时间2009.5.1确认人霍峰、梁福辉确认过程2表7-307 要因确认3制表:刘新立 审核:李贵良 日期:2009年5月10日确认内容未严格执行维修保养制度确认方法查阅维修保养记录确认过程 查阅2009年03月至2009年05月木加工设备维修保养记录,共发生维修2次,定期保养6次,日常维护保养有记录。其中1台设备发生故障未维修,已确定设备机件磨损严重做退场处理。现场使用的每台设备均固定人员,设备使用状态正常,基本执行维修保养制度。确认标准按制度及时维护确认结果设备按制度要求及时进行了维修和保养,记录齐全有效,满足使用要求。确认结论非要因确认时间2009
15、.5.5确认人曹鹏飞、郑瑞恒确认过程3表7-407 要因确认4制表:刘新立 审核:李贵良 日期:2009年5月10日确认内容模板与砼柱顶接不紧确认方法现场检查、查阅技术交底确认过程 查阅技术交底,模板支设时要求硬拼,顶在混凝土柱上,在柱上口施工缝位置粘贴宽10mm厚2mm的海绵条。交底中要求竹胶板在柱身上顶紧,未明确模板搭在柱身上长度,要求搭接宽度不小于300mm,经项目总工批准,同意将此列入模板作业指导书。确认标准模板与柱顶接严密确认结果明确竹胶板与柱身搭接宽度后,可更好保证顶接严密。确认结论非要因确认时间2009.5.2确认人刘新立、赵立如确认过程4表7-507 要因确认5制表:刘新立 审
16、核:李贵良 日期:2009年5月10日确认内容模板龙骨尺寸不准确认方法现场调查确认过程 现场检查进场的木模板厚度要求为18mm,实际最大偏差2mm,且厚度不一致;进场的木龙骨要求达到50X100mm,实际最小规格只有35X88mm,且规格不一。同时进场木龙骨还存在长度不标准、不顺直等现象,个别板面变形。确认标准模板龙骨尺寸偏差小于1mm。确认结果模板龙骨尺寸偏差大于1mm。确认结论要 因确认时间2009.5.2确认人李贵良、郝春霞确认过程5表7-607 要因确认6制表:刘新立 审核:李贵良 日期:2009年5月10日确认内容模板散拼受力不均确认方法现场调查确认过程 查采用模板散拼,模板拼缝多,
17、相邻板块受力不均,产生板缝错台可能较大,难以保证模板安装平整度,对混凝土外观质量有影响。且采用模板散拼,增加施工过程中安装和拆除次数,增大工作量,降低施工效率。确认标准模板缝隙高低差小于1mm。确认结果模板散拼缝隙多,缝隙处高低差难于保证。确认结论要 因确认时间2009.5.6确认人赵立如、李贵良确认过程6表7-707 要因确认7制表:刘新立 审核:李贵良 日期:2009年5月10日确认内容模板拼缝不严确认方法现场调查确认过程 模板采用直接对接安装,缝隙不严密,易产生漏浆和模板变形现象,很难保证模板拼缝处的截面尺寸。确认标准模板拼缝严密,不漏浆。 确认结果模板拼缝采用直接对接,导致缝隙不严。确
18、认结论要 因确认时间2009.5.8确认人曹鹏飞、王志义确认过程7表7-8制表:刘新立 审核:李贵良 日期:2009年5月10日07 要因确认8确认内容模板进场验收不严确认方法查阅材料进场验收记录、现场调查确认过程 查阅2009年03月至2009年5月材料进场验收记录,共进场多层板3批,验收记录为合格。现场检查模板板面平整,大部分无变形翘曲现象,个别板面变形严重者在施工时可以选出,对施工生产影响不大。确认标准模板进场按标准验收合格,有记录确认结果严格进场验收,有记录。确认结论非要因确认时间2009.5.2确认人郝春霞、刘新立确认过程8表7-907 要因确认9制表:刘新立 审核:李贵良 日期:2
19、009年5月10日确认内容自检不严格确认方法查阅自检记录确认过程 查阅2009年03月至2009年5月架工班组自检记录,每步工序脚手架安装完成后,有自检记录,对发现存在的问题有纠正和整改记录,有整改结果,均达到了整改合格。确认标准自检记录齐全有效确认结果自检记录基本齐全有效,能较好的达到自检整改的目的。确认结论非要因确认时间2009.5.9确认人霍峰、梁福辉确认过程9表7-1007 要因确认10制表:刘新立 审核:李贵良 日期:2009年5月10日07 要因确认11确认过程10表7-11制表:刘新立 审核:李贵良 日期:2009年5月11日确认内容未配备30棒配合振捣确认方法现场调查确认过程
20、查阅2009年03月12日混凝土施工技术交底,明确钢筋较密处采用30棒配合50棒振持捣密实。现场检查已施工的柱基混凝土,表面质量较好,无蜂窝、漏筋、漏振等缺陷。确认标准混凝土振捣密实确认结果混凝土振捣密实,表面无漏振等缺陷。确认结论非要因确认时间2009.5.8确认人郑瑞恒、吴根顺1模板龙骨尺寸不准07 要因确认122模板散拼受力不均3模板拼缝不严要因确认结论08 制定对策1对策评价选择序号要因项目对 策方 案 评 价综合得分方案选择操作性可靠性有效性经济性1模板龙骨尺寸不准模板进场按规格厚度分规格使用,木龙骨进场二次加工989935是采购规格尺寸标准的模板和木方499527否2模板散拼受力不
21、均配制成组合式模板或配成大块模板使用,减少拼拆次数。998935是招聘或培训高水平的技术工人,加大检查验收力度。477523否3模板拼缝不严采取企口连接或粘海绵条方式处理模板拼缝。988833是提高模板制作精度,提高模板支撑加固的刚度,加大培训和检查验收力度。688426否制表:刘新立 审核:李贵良 日期:2009年5月11日表8-108 制定对策2对策表1序号要因对策目 标措 施地点完成时间负责人1模板龙骨尺寸不准模板进场按规格厚度分规格使用,木龙骨进场二次加工1.多层板相邻板块厚度偏差不大于1mm。2.多层板模板加工长度偏差控制在0-5mm 。3.模板龙骨截面加工误差不大于1mm。4.钢管
22、主次龙骨的直线度不大于3mm。 1.多层板进场后按规格进行质量验收,分规格存放使用。2.同一柱的同一侧板面采用板厚偏差在1mm以内的板块。3.模板龙骨进场后全部过压刨,保证龙骨尺寸标准。4.加固用主次龙骨使用前挑选,必要时进行调直。5.由土建技术负责人编制技术交底,并经总工批准列入作业指导书,加强自检和项目验收。施工现场2009-6-15王志义刘新立曹鹏飞霍 峰表8-2制表:刘新立 审核:李贵良 日期:2009年5月17日08 制定对策3对策表2序号要因对策目 标措 施地点完成时间负责人2模板散拼受力不均配制成组合式模板或配成大块模板使用,减少拼拆次数。1.模板缝隙高低差小于1mm 。 1.双
23、肢柱的立面用多层板做成四片组合式模板,整支整拆,减少过程中拼拆次数。2.双肢柱芯孔模采用钢框覆塑多层板组合安装。3.双肢柱外侧用双架管长螺栓加固。施工现场2009-7-20李贵良赵立如梁福辉郑瑞恒表8-3制表:刘新立 审核:李贵良 日期:2009年5月16日08 制定对策4对策表3序号要因对策目 标措 施地点完成时间负责人3模板拼缝不严采取企口连接或粘海绵条方式处理模板拼缝。1.模板拼接严密,不漏浆。 1. 外侧模加工时连角处设25mm的企口连接。2.所有模板缝隙均粘贴厚2mm宽10mm的海绵条。3.双肢柱外侧柱箍加固采用双架管18穿墙(孔)长螺栓加固。施工现场2009-7-20林 刚杨振新郝
24、春霞表8-4制表:刘新立 审核:李贵良 日期:2009年5月15日09 对策实施1实施1序号措施项目负责人地点完成时间1细化模板龙骨加工方案,列入作业指导书。总工批准,王志义霍 峰施工现场2009-05-292组织现场加工技术交底刘新立曹鹏飞2009-05-213模板龙骨加工现场交底,现场示范。王志义霍 峰2009-05-214自检及专项检查验收刘新立曹鹏飞2009-05-23至2009-06-15表9-1制表:刘新立 审核:李贵良 2009年5月18日模板龙骨尺寸不准对策实施计划多层板进场后,由项目材料部门负责,供货方、质检、班组相关人员配合,对板材按板厚重新分类堆放,并明显标识。板材规格为
25、18mm,分类标准为:16.5-17.5mm,17.5-18.5mm,18.5-19.5mm。木加工后台指定专人操作,组织专项交底,明确模板和龙骨加工质量标准,并按规格分类堆放,明显标识。经现场实测,钢管龙骨壁厚实际为32mm。项目土建负责人根据方案明确的主、次龙骨间距、最小规格板材和龙骨的实际规格尺寸进行刚度验算,满足使用要求。项目土建技术、质检对加工质量进行了专项检查,确认合格与否,并悬挂合格状态标识。09 对策实施2序号检查项目目标检查点数合格点数合格率偏差整改检查人1板块厚度偏差0 1mm216216100%/王志义2多层板模板加工长度偏差0-5mm21620494%已整改刘新立3木龙
26、骨加工尺寸误差0 1mm26025598%已整改曹鹏飞4钢管主次龙骨的直线度0 3mm1029593%已整改霍 峰表9-2对策实施效果检查 2009年5月23日至2009年6月15日,项目部专人负责对模板龙骨加工情况进行了专项检查,检查结果如下:实施效果模板龙骨加工尺寸按对策及措施方案实施完毕,达到偏差允许值的合格率平均值为96%,基本达到预定目标。模板龙骨加工尺寸精确,满足了模板支设高质量目标的要求。模板龙骨加工方法已列入项目模板作业指导书,作为项目过程控制精细化管理提出了可操作性的依据。制表:刘新立 审核:李贵良 2009年6月30日09 对策实施3序号措施项目负责人地点完成时间1细化双肢
27、柱模板组合安装方案,编制模板工程施工方案,总工批准。李贵良赵立如施工现场2009-05-252组织现场加工技术交底梁福辉郑瑞恒2009-05-273模板龙骨加工现场交底,现场示范。李贵良赵立如2009-05-304自检及专项检查验收梁福辉郑瑞恒2009-05-31至2009-07-20表9-3制表:刘新立 审核:李贵良 2009年5月18日模板散拼受力不均对策实施计划2009年5月18日至2009年5月25日,QC小组成员经过充分讨论论证,经总工批准,确定了双肢柱柱面模板拼装支设方案、芯孔模板支设方案,并明确了质量标准。为保证芯孔内模八字角尺寸准确,八字角处采用内外钢框,钢框厚25mm,用拉杆
28、固定。考虑混凝土浇筑侧压力,经讨论决定,芯模加工安装后,几何尺寸比设计混凝土构件几何尺寸大1mm;柱外模加工几何尺寸比设计混凝土构件几何尺寸小1mm;实施2双肢柱的四个立面用多层板做成四片组合式模板,整支整拆。模板采用18mm厚多层板,背楞采用50X100mm方木。双肢柱外侧柱箍加固采用双架管18穿墙(孔)长螺栓加固。双肢柱芯孔内模采用钢框18mm 覆塑多层板组合安装。沿双肢柱纵轴外侧搭设四排钢管脚手架,做为柱模支撑体系,同时用于模板体系的垂直定位和轴线定位。09 对策实施4柱模单片组合模板偏差统计表序号检查项目允许偏差实测点合格点合格率最大值1表面平整度2mm6262100%2mm2板缝高低
29、差2mm6262100%2mm3板片加工尺寸2mm12412298%3mm表9-4制表:刘新立 审核:李贵良 2009年6月18日双肢柱模板安装偏差统计表序号检查项目允许偏差实测点合格点合格率最大值1轴线位移3mm17617197%3mm2模内尺寸+3mm35534998%-4mm3层高垂直度3mm35535399%-4mm4预留孔洞中心线位移3mm928997%4mm5预留孔洞尺寸0+5mm928896%-1mm表9-509 对策实施5 2009年5月31日至2009年7月20日,项目部对双肢柱模板支设质量进行检查,部分项目检查结果汇总如下表:制表:刘新立 审核:李贵良 2009年7月28日
30、 实施效果模板安装偏差达到允许值的合格率平均值为97%,基本达到预定目标。采用钢木组合拼装方案,整支整拆,模板安装质量提高,减少拼装数量。模板施工工艺已进行技术总结,编写了工法。09 对策实施6实施3模板拼缝不严序号要因地点完成时间负责人1编制技术交底,经总工批准列入作业指导书。施工现场2009-5-25吴根顺林 刚2现场指导安装并检查验收2009-7-20林 刚 吴根顺郝春霞采用企口连接解决了八字角连角处板材斜接不易接槎的问题。缝隙满粘海绵条解决了模板拼接缝隙漏浆的问题。实际检查混凝土表面,模板拼缝处无漏浆现象。表9-6对策实施计划表制表:刘新立 审核:李贵良 2009年5月15日 实施效果
31、09 对策实施709 对策实施810 效果检查1 2009年6月25日到7月31日,项目对双肢柱混凝土施工的截面尺寸偏差进行了现场检查统计,如下表。序号项目名称项目内容1检查部位每个双肢柱自下而上的每个施工段,含柱外缘尺寸和芯孔、牛腿尺寸。2检查标准北京市结构长城杯标准,截面尺寸允许偏差值+3mm3检查数量5124合格点数4975合格率97%混凝土施工截面尺寸偏差调查表表10-1制表:刘新立 审核:李贵良 2009年7月31日 10 效果检查20活动前目标值89%达到合格百分率%阶段名称100%50%95%97%现状值制表:刘新立 审核:李贵良 2009年7月31日 结 论对策实施后,完成了本QC小组课题关于截面尺寸合格率提高到95%的目标,活动开展有效10 效果检查30模板支设质量差预埋件留设偏差大67%0频数(次)N93其它钢筋安装偏差大100%累计百分比(%)75%50%25%78%89%1110模板支设质量差预埋件留设偏差大573%1
温馨提示
- 1. 本站所有资源如无特殊说明,都需要本地电脑安装OFFICE2007和PDF阅读器。图纸软件为CAD,CAXA,PROE,UG,SolidWorks等.压缩文件请下载最新的WinRAR软件解压。
- 2. 本站的文档不包含任何第三方提供的附件图纸等,如果需要附件,请联系上传者。文件的所有权益归上传用户所有。
- 3. 本站RAR压缩包中若带图纸,网页内容里面会有图纸预览,若没有图纸预览就没有图纸。
- 4. 未经权益所有人同意不得将文件中的内容挪作商业或盈利用途。
- 5. 人人文库网仅提供信息存储空间,仅对用户上传内容的表现方式做保护处理,对用户上传分享的文档内容本身不做任何修改或编辑,并不能对任何下载内容负责。
- 6. 下载文件中如有侵权或不适当内容,请与我们联系,我们立即纠正。
- 7. 本站不保证下载资源的准确性、安全性和完整性, 同时也不承担用户因使用这些下载资源对自己和他人造成任何形式的伤害或损失。
最新文档
- 农村土房子收购合同范例
- 农村自建别墅合同样本
- 二居合同标准文本
- 乡镇楼盘收购合同范例
- 上海市家装合同标准文本
- 动态美术教学模型的研究与应用计划
- 2013劳动合同标准文本
- 2025《合同协议样本》
- 养虾雇人合同标准文本
- 买卖茶具合同标准文本
- 导游人员管理法律制度课件
- 2022年江苏安东控股集团有限公司招聘笔试题库及答案解析
- 美国地图高清中文版
- 金属监督监理实施细则
- 不锈钢304焊接工艺评定报告PQR(全氩弧)
- 正确认识汽车太阳膜课件
- 工程建筑给排水外文文献翻译1
- 曲线上梁的平分中矢坐标计算方法解读
- DB4201∕T 646-2021 轨道交通工程运营期结构监测技术规程
- 200句话搞定上海中考单词(精华版)
- 船舶辅锅炉的自动控制系统分析
评论
0/150
提交评论