

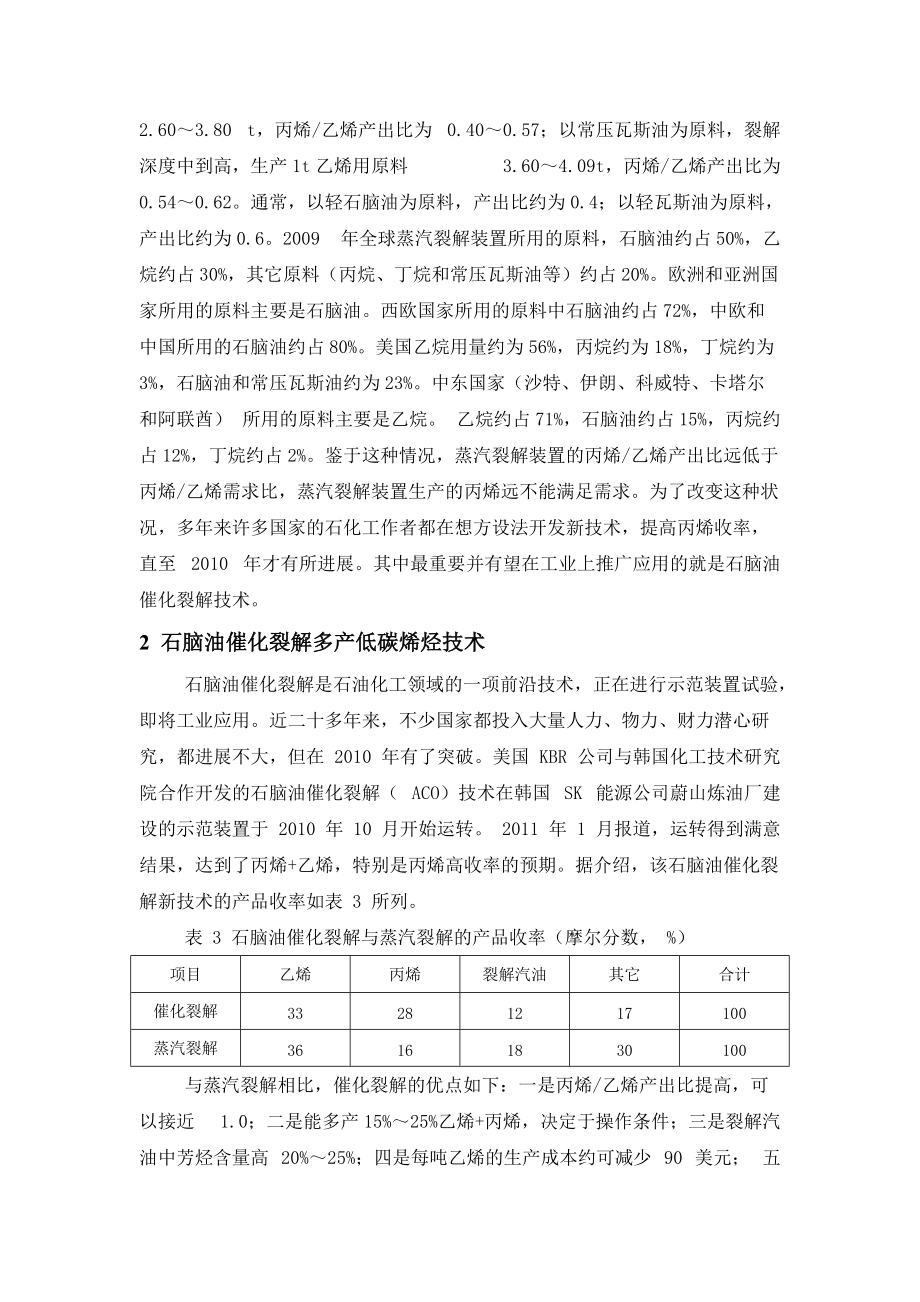


版权说明:本文档由用户提供并上传,收益归属内容提供方,若内容存在侵权,请进行举报或认领
文档简介
1、催化裂解生产低碳烯烃技术乙烯和丙烯是最重要的石油化工原料之一。蒸汽裂解技术问世60多年来一直是生产乙烯和联产丙烯的主要技术。可是,近 20 多年来随着乙烯和丙烯的需求逐年增加,丙烯/乙烯需求比呈上升趋势,丙烯/乙烯产出比呈下降趋势。近 10 年来的情况如表 1 所列。2010 年乙烯的需求约为 1.15 亿吨,丙烯的需求约为7000万吨,丙烯/乙烯需求比上升到0.61,而丙烯/乙烯产出比下降到0.34。预计2011年丙烯的需求将增长5%,达到7350万吨,丙烯/乙烯的产出比还会下降。表 1 全球丙烯/乙烯的需求比和蒸汽裂解装置的丙烯/乙烯产出比项 目2000年2002年2004年2006年20
2、08年2010年丙烯/乙烯需求比0.560.570.570.570.580.61丙烯/乙烯产出比0.390.380.370.360.350.34预计今后若干年全球丙烯需求的增速在5%以上,高于乙烯需求的增速,裂解原料的比例不会有大的变化,因此蒸汽裂解生产的丙烯不能满足需求的现状还将持续下去。多年来,市场需求不足的丙烯主要由炼油厂常规催化裂化和高苛刻度催化裂化(石油化工厂称催化裂解,以下称催化裂解)副产的丙烯提供。虽然近 20 多年来,出现了多种多产丙烯的专用技术,而且有一些已经工业应用,但由于种种原因,这些专用技术生产的数量有限,丙烯供应的紧张状况并未得到根本缓解。据统计,2003 年全球丙烯
3、的需求约为 5630 万吨,其中67%来自蒸汽裂解装置,30%来自炼油厂的催化裂化装置,2%来自丙烷脱氢装置,1%来自其它装置。据统计,2010年全球丙烯的需求约为7000万吨,其中54%来自蒸汽裂解装置,37%来自炼油厂的催化裂化和催化裂解装置,9.5%来自烯烃易位、丙烷脱氢和C4C8 烯烃裂解,0.5%来自其它装置。预计今后20 年间石油和天然气仍然是人类需求最主要的能源,石油和天然气液仍将是石化原料的主要来源。由于原料资源、价格、水资源、技术、投资和生产成本等多种因素的影响,预计丙烷脱氢、甲醇制烯烃等专用技术生产低碳烯烃会有一些增加,但不会增加很多,能够增加较多的仍然是石脑油蒸汽裂解/催
4、化裂解和减压瓦斯油 /常压渣油催化裂化/催化裂解。本文主要介绍石脑油催化裂解和炼油厂减压瓦斯油 /常压渣油催化裂解技术工业应用的进展。1 蒸汽裂解生产低碳烯烃技术工业应用的现状据统计,到 2009 年底全球有 58 个国家的 216座石油化工厂建有蒸汽裂解装置,乙烯生产能力为13297.4 万吨/年。蒸汽裂解的原料和产品收率如表 2 所列。表 2 蒸汽裂解的原料和典型产品收率(一次通过,质量分数, %)产 品原 料乙烷丙烷丁烷石脑油常压瓦斯油(轻柴油)H2+CO4.061.701.23 1.030.71CH43.6723.3721.75 15.3510.69C2H20.500.670.500.
5、690.34C2H452.4539.6531.7431.0224.85C2H634.764.573.673.422.75C3H6+C3H41.1513.2819.8516.2114.28C3H6/C386.758.399.098.396.7C3H80.127.420.680.380.31C42.244.0312.90 9.549.61裂解汽油0.874.276.4119.3320.6裂解燃料油0.161.111.263.0115.78稀释蒸汽/原料0.300.350.400.500.80单位能耗/kJkg1(乙烯)16000200002300027000100 万吨/年乙烯大型裂解装置的能耗。
6、蒸汽裂解的产品收率因原料和裂解深度而异。裂解深度低(较低的温度和压力),丙烯和所有副产品的收率都提高。以乙烷为原料,裂解深度高,生产1t 乙烯用原料1.24 t,丙烯/乙烯产出比为 0.024;以丙烷为原料,裂解深度中到高,生产1t乙烯用原料 2.182.67 t,丙烯/乙烯产出比为 0.370.45;以丁烷为原料,裂解深度高,生产1t 乙烯用原料2.65 t,丙烯/乙烯产出比为 0.41;以石脑油为原料,裂解深度中到高,生产1t 乙烯用原料 2.603.80 t,丙烯/乙烯产出比为 0.400.57;以常压瓦斯油为原料,裂解深度中到高,生产1t乙烯用原料 3.604.09t,丙烯/乙烯产出比
7、为 0.540.62。通常,以轻石脑油为原料,产出比约为0.4;以轻瓦斯油为原料,产出比约为0.6。2009 年全球蒸汽裂解装置所用的原料,石脑油约占50%,乙烷约占30%,其它原料(丙烷、丁烷和常压瓦斯油等)约占20%。欧洲和亚洲国家所用的原料主要是石脑油。西欧国家所用的原料中石脑油约占72%,中欧和中国所用的石脑油约占80%。美国乙烷用量约为56%,丙烷约为18%,丁烷约为3%,石脑油和常压瓦斯油约为23%。中东国家(沙特、伊朗、科威特、卡塔尔和阿联酋) 所用的原料主要是乙烷。 乙烷约占71%,石脑油约占15%,丙烷约占12%,丁烷约占2%。鉴于这种情况,蒸汽裂解装置的丙烯/乙烯产出比远低
8、于丙烯/乙烯需求比,蒸汽裂解装置生产的丙烯远不能满足需求。为了改变这种状况,多年来许多国家的石化工作者都在想方设法开发新技术,提高丙烯收率,直至 2010 年才有所进展。其中最重要并有望在工业上推广应用的就是石脑油催化裂解技术。2 石脑油催化裂解多产低碳烯烃技术石脑油催化裂解是石油化工领域的一项前沿技术,正在进行示范装置试验,即将工业应用。近二十多年来,不少国家都投入大量人力、物力、财力潜心研究,都进展不大,但在 2010 年有了突破。美国 KBR 公司与韩国化工技术研究院合作开发的石脑油催化裂解( ACO)技术在韩国 SK 能源公司蔚山炼油厂建设的示范装置于 2010 年 10 月开始运转。
9、 2011 年 1 月报道,运转得到满意结果,达到了丙烯+乙烯,特别是丙烯高收率的预期。据介绍,该石脑油催化裂解新技术的产品收率如表 3 所列。表 3 石脑油催化裂解与蒸汽裂解的产品收率(摩尔分数, %)项目乙烯丙烯裂解汽油其它合计催化裂解33281217100蒸汽裂解36161830100与蒸汽裂解相比,催化裂解的优点如下:一是丙烯/乙烯产出比提高,可以接近 1.0;二是能多产15%25%乙烯+丙烯,决定于操作条件;三是裂解汽油中芳烃含量高 20%25%;四是每吨乙烯的生产成本约可减少 90 美元; 五是规模经济性好, 催化裂解单反应器乙烯+丙烯生产能力可达 150 万吨/年,而目前成熟的蒸
10、汽裂解炉单炉乙烯最大生产能力约为 20 万吨/年,乙烯+丙烯生产能力约为 30 万吨/年。催化裂解技术采用 KBR 公司开发的正流型催化裂化反应系统和韩国化工技术研究院开发的专用催化剂,将石脑油选择性催化转化为丙烯和乙烯。反应系统的结构是正流型,有提升管、紧固式旋风分离器和第三级分离器以及专用的催化剂再生系统, 在许多方面非常类似于炼油厂的催化裂化装置。但也有一些不同的特点:一是骤冷换热器,反应器顶部流出物冷却与裂解炉类似,产生高压蒸汽,因此工艺能效提高,而这种换热器在催化裂化装置上是没有和不能使用的,因为催化裂化反应流出物中有大量油浆会发生严重的结垢;二是热平衡,催化裂解是吸热反应,因为原料
11、油轻,催化剂上的生焦量不足以满足反应需要的热量,为保持热平衡,必须向反应系统提供热量, KBR 公司专门设计的催化剂与燃料连续燃烧系统已通过示范试验; 三是催化剂/反应产物分离,虽然旋风分离器非常有效,但总会有一些催化剂细粉被反应产物带入反应器, KBR 公司专门设计的催化剂细粉脱除系统已通过示范试验。催化裂解技术的关键是专用催化剂。韩国化工技术研究院专门开发的催化剂机械性能、水热稳定性和生产低碳烯烃的选择性都比较好。 KBR公司称,根据其 Superflex 技术在南非 Seeunda 合成油厂工业装置的应用情况, 预计石脑油催化裂解的中试结果能够在示范装置/工业装置上重复。催化裂解工艺的回
12、收系统采用前脱丙烷流程,生产聚合级乙烯和丙烯。流程的大部分都类似于蒸汽裂解装置典型的回收系统,但也有一些不同的特点, 如在反应流出物中有一些微量杂质如氮氧化物、氧和其它杂质,都必须脱除。这些技术问题在催化裂解的工艺流程中都已经解决。KBR 公司称,因为催化裂解的乙烯+丙烯收率比传统的蒸汽裂解高 15%25%,而且提高的部分主要是丙烯。鉴于市场需求丙烯的增速高于乙烯,所以催化裂解的产品收率与分布更适合于今后若干年市场的需求。催化裂解技术可以用于替代计划新建的蒸汽裂解装置,也可用于原有蒸汽裂解装置的扩能改造。 KBR 公司称,示范装置运行稳定和成功以后,希望与中国、中东或南美的生产厂家合作建设工业
13、装置。KBR公司称,已与潜在用户洽谈技术转让方案,预计2011年可以达成工业规模催化裂解项目协议。3 炼油厂减压瓦斯油 /常压渣油催化裂解多产低碳烯烃技术此项技术已经成熟,有望进一步扩大工业应用。炼油厂催化裂化装置的主产品是汽油,丙烯是副产品。催化裂化装置多产丙烯有两种方法:一种是采用择形沸石ZSM-5助剂的常规催化裂化;另一种是采用特殊配方专用催化剂的催化裂解。两种方法的产品收率如表 4 所列。表 4 催化裂化多产丙烯两种方法的产品收率(摩尔分数, %)项目常规催化裂化用助剂的常规催化裂化催化裂解丙烯4820乙烯<124混合丁烯101417汽油585033表 5 催化轻汽油中的烯烃选择
14、性裂化的产品收率(摩尔分数, %)原料中的烯烃产 品乙烯丙烯丁烯戊烯丙烯/丁烯C5 烯烃31.738.3C6 烯烃7.583.47.90.710.6C7 烯烃0.947.347.70.91.0C8 烯烃微量27.544.1280.6采用择形沸石 ZSM-5 助剂多产丙烯的常规催化裂化主要是将用主催化剂生成的催化裂化轻汽油中的烯烃选择性裂化为 C3/C4 烯烃。这种择形沸石助剂选择性裂化的产品收率如表 5 所列。美国炼油厂于 20 世纪 80 年代中期首先使用ZSM-5 助剂提高催化裂化汽油的辛烷值。当时ZSM-5 助剂的添加量只占装置催化剂藏量的 2%,因为用 ZSM-5 助剂可使催化轻汽油中
15、的烯烃转化为丙烯和丁烯。到了 90 年代美国炼油厂使用 ZSM-5助剂的催化裂化装置越来越多,大多数装置都添加2%5%的 ZSM-5 助剂,使丙烯收率提高 2%3%而达到 6%7%。由于长期以来,美国丙烯的市场价格大约是汽油的 1.9 倍,炼厂为提高经济效益, ZSM-5 助剂的用量进一步增加,丙烯收率也进一步提高。与此同时, ZSM-5 助剂的品种也由低活性和中活性发展到高活性和超高活性。国际市场供应ZSM-5 助剂的生产商很多,但选择形裂化效果最好、 工业应用最多的是 Grace Davison 公司的高活性助剂 OlefinsMax 和超高活性助剂 OlefinSultra。 前者200
16、1 年问世,含 25%用磷改性的 ZSM-5 小晶粒;后者 2003 年问世,含 40%用磷改性的 ZSM-5 小晶粒。高活性和超高活性助剂的问世,使催化裂化多产丙烯的收率进一步提高。但是,多产丙烯就少产汽油,也使汽油中的芳烃含量增加、密度变大。由于催化裂化汽油是炼油厂成品汽油的主要组分,为确保生产合格的清洁汽油产品,美国和西欧炼油厂的催化裂化装置用 ZSM-5 助剂多产丙烯,一般都控制丙烯收率在 10%左右。其主要原因有三:一是多用 ZSM-5 助剂会使催化裂化主催化剂稀释,转化率下降,从而使主催化剂添加量增加,成本上升;二是要得到合格的清洁汽油产品,催化裂化汽油组分的芳烃不能过多, 密度不
17、能过大;三是不能突破催化裂化装置反应器/主分馏塔、湿气处理或处理多产的 C3 和 C4 烯烃(回收丙烯或烷基化)能力的极限14。这项技术主要用在美国和西欧。减压瓦斯油 /常压渣油催化裂解技术是在用ZSM-5 助剂多产丙烯的常规催化裂化技术基础上发展起来的生产更多丙烯( >15%)的新技术。与常规催化裂化技术的主要区别是,采用更高的提升管反应温度( 530600 )、更高的剂油比( 1220)和更低的烃分压,并采用特殊配方的专用催化剂,使一次裂化和择形裂化结合,使催化汽油中的多碳烯烃更多地转化为乙烯、丙烯和丁烯,还可以与ZSM-5 助剂一起使用提高生产低碳烯烃的灵活性。 目前工业应用最多的
18、两种催化剂是 Grace Davison 公司的 AP-PMC-900 和 Albemarle 公司的 AFX。 这项技术目前主要应用在中国、印度、泰国、越南和一些中东国家。最近几年全球催化裂化副产丙烯的情况如表 6所列。可以看出,常规催化裂化用 ZSM-5 助剂多产丙烯占绝大多数,催化裂解用专用催化剂多产丙烯仍然不多,但呈逐年增加之势,前景看好。表 6 催化裂化副产丙烯的工业应用情况(摩尔分数, %)项目2005年2006年2007年2008 年2009年常规催化裂化副产丙烯99.598.398.496.693.9催化裂解副产丙烯0.51.71.63.46.1合计100.0100.0100.
19、0100.0100.0目前工业应用的减压瓦斯油 /常压渣油催化裂解技术有以下 6 种。(1) PIPP/SW 公司的 DCC 技术 这是一项由中国石化石油化工科学研究院开发、 SW 公司在国外转让的深度催化裂化( DCC)技术,采用含改性五硅环沸石的专用催化剂, 1990 年首次工业应用。目前已建的工业装置有 10 套, 其中最大的一套加工能力是 92000 桶/日(约460 万吨/年),建在沙特的PetroRabigh 炼化一体化联合企业,以加氢处理的减压瓦斯油为原料,生产 90 万吨/年丙烯和 5.9 万桶/日汽油,2009年投产。建在泰国 TPC 的一套加工能力是 18000 桶/日(约
20、 90 万吨/年),原料油是经过加氢处理的减压瓦斯油( 82.5%)、脱沥青油( 6.5%)和润滑油脱蜡副产的蜡油( 11%),得到5.3%乙烯、18.5%丙烯、13.3%丁烯、35.7% C5 以上汽油和 27.2%其它副产品,1997年投产。(2) UOP公司的 PetroFCC 技术 这项技术采用把一部分待生催化剂返回提升管反应系统的新设计 RxCat 和择形沸石含量高的专用催化剂,以减压瓦斯油为原料,可以得到 6%乙烯、 22%丙烯、14%丁烯和 18%BTX,是一种用重原料油专门生产石化原料的催化裂解新技术。目前采用这项技术的工业装置有 4 套,另有 5 套在建设中,还有 4 套正在
21、设计。建在亚洲的一套大型装置 2009 年投产。(3) IOC/Lummus 公司的 Indmax 技术这是一项印度石油公司开发、 Lummus 公司负责工程设计并在其它国家转让的催化裂解技术。采用提升管反应系统和特殊配方的专用催化剂。建在印度阿萨姆邦 Guwahati 炼油厂的第一套工业装置加工能力为 10 万吨/年, 2003 年投产,以常压渣油和焦化重瓦斯油为原料,得到 17.2%丙烯。正在建设的装置有两套, 其中一套设计加工能力是 85000 桶/日( 425万吨/年),建在印度奥里萨邦 Paradip 炼化一体化联合企业(加工能力 30 万桶/日),用经过加氢处理的减压瓦斯油为原料生
22、产丙烯和乙烯, 预计 2012 年投产。(4) Axens/Shaw 公司的 PetroRiser 技术 这是在 Shaw 公司 R2R 常规渣油催化裂化( RFCC)技术的基础上,由 Axens/Shaw/Total/IFP 合作开发的双提升管渣油催化裂解多产丙烯的新技术。以常压渣油为原料, 丙烯收率可由 R2R 的 5%提高到 12%。主要特点是,第一根提升管在 550 和剂油比 8 1的条件下操作,第二根提升管在 590 和剂油比121 的条件下操作,把第一根提升管生产的催化轻汽油择形裂化生产丙烯, 每根提升管都独立操作,既能多产丙烯又能减少再生剂上的焦炭含量。如果不需要多产丙烯,可以返
23、回到常规汽油方案操作。经济效益是加工每桶渣油的收益可以提高 1.2美元。2008 年 7 月转让技术建设第一套工业装置。 目前建在越南榕桔( Dung Quat)炼油厂(加工能力 14 万桶/日)的第一套装置已经投产,正在建设中的装置有 4 套:建在阿联酋阿布扎比炼制公司( Takreer)加工能力为 41.7 万桶/日( 2085 万吨/年)的 Ruwais炼化一体化联合企业, 装置的加工能力是 12.7 万桶/日( 635 万吨/年),计划 2013 年投产;建在卡塔尔加工能力 25 万桶/日( 1250 万吨/年)的 Al-Shaheen炼油厂,装置加工能力为 6 万桶/日( 300 万
24、吨/年),计划 2012 年投产; 建在巴西里约热内卢加工能力为16.5 万桶/日( 825 万吨/年)的炼化一体化联合企业( Comperj), 计划 2013 年投产; 建在越南黎山( NghiSon)加工能力为 20 万桶/日( 1000 万吨/年)的炼油厂,计划 2013 年投产。(5) CNPC 的 TMP 技术 中国石油石油化工研究院开发的这项双提升管催化裂解多产丙烯兼顾生产汽柴油的技术, 采用特殊配方的专用催化剂,以大庆常压渣油为原料,丙烯收率为 20.31%,干气 和 焦 炭 产 率 为 14.28% , 液 体 产 品 收 率 为82.66%,汽油研究法辛烷值为 96。一套
25、12 万吨/年的工业装置已累计安全平稳运行 600 天以上。这项技术 2009 年 2 月 17 日通过中国石油鉴定委员会的鉴定。(6) RIPP/SW 公司的 CPP 技术 中国石化石油化工科学研究院开发的这项催化热裂解( CPP)技术,采用特殊配方的专用催化剂,在提升管中试装置上以掺减压渣油的减压瓦斯油为原料,在反应温度 640、反应压力 0.07MPa、注水量 54.3%的条件下, 得到 22.82%乙烯、 15.96%丙烯、 液体产品( C5以上汽油、柴油、重油) 24%、焦炭 8.51%,其它27.8%,损失 0.91%。第一套工业装置建在沈阳的中国蓝星沈阳化工集团, 加工能力为 5
26、0 万吨/年, 2009年 8 月投产。4 思考与启示(1)Murphy 石油公司 2010 年发表的报告预测, 2030 年全球的能源需求结构是:石油占 32%,煤炭占 28%, 天然气占 23%, 水能和可再生能源占 11%,核能占 6%。 BP 公司 2011 年初发表的报告预测, 2030 年全球的能源需求结构是:石油占 27%,天然气占 27%,煤炭占 27%,核能、太阳能、风能、生物质能、地热能合计占 19%。业内专家一致认为,今后 20 年间石油和天然气仍将在全球能源需求结构中居主导地位,运输燃料仍主要是来自炼油厂,石油化工原料仍主要是石油和天然气液(乙烷、丙烷、丁烷)。这种状况
27、不会改变,当然,我国也不会例外。(2)目前我国炼油厂的原油加工能力和石油化工厂蒸汽裂解装置的乙烯生产能力均居世界第二位。据预测, 2015 年我国炼油厂的原油加工能力将由 2010 年的 1010 万桶/日( 5.05 亿吨/年)增加到1390 万桶/日( 6.95 亿吨/年),增加 38%。 2010 年我国原油净进口量首次突破 2 亿吨,对外依存度超过 55%,预计 2015 年可能超过 60%。 2015 年我国石油化工厂的乙烯生产能力将由 2010 年的 1450 万吨/年增加到 21002300 万吨/年,我国乙烯的当量消费自给率将由 50%提高到 60%65%。我国丙烯的当量消费自
28、给率也大体相当。(3)我国的国情是相对“富煤缺油少气”。发展我国石化原料特别是低碳烯烃生产,既要认真贯彻“大型化、基地化、园区化”方针,更要认真贯彻“轻质化、多元化、炼化一体化”方针。要用新思维开拓新途径开发新技术,贯彻落实“轻质化、多元化、炼化一体化”方针。轻质化就是要尽可能多用石脑油、凝析油、液化气作原料生产乙烯和联产丙烯,要尽可能少用或不用轻柴油(常压瓦斯油) 和加氢裂化尾油作原料。因为我国柴油短缺,并且加氢裂化尾油有更好的用途和经济效益。石脑油(凝析油)催化裂解比蒸汽裂解可以多产乙烯和丙烯特别是多产丙烯,有更好的经济效益。这项技术在国外已进行示范装置试验,即将工业应用。我国有关单位早在
29、十多年前就开展过这项研究工作,现在应该加大支持力度、加强研发力量、加快研发进程。多元化就是除了用石脑油、凝析油、丙烷、丁烷等作原料生产低碳烯烃外,还可以用我国丰富的煤炭作原料生产低碳烯烃。我国神华集团在内蒙古包头市的 60 万吨/年煤制乙烯/丙烯( MTO)示范项目已于 2011 年 1月 1 日开始商业化运行, 神华宁煤在宁夏林乌市和大唐国电在内蒙古锡林诺尔市的50 万吨/年煤制丙烯( MTP)示范项目也将在今年投产。这样做可以减少对进口石油的依赖,但是也应该考虑以下因素。一是用煤制甲醇生产低碳烯烃,要有廉价丰富的煤炭资源。用煤制甲醇生产 1t 低碳烯烃大约用煤 5t。生产 1000万吨低碳
30、烯烃,一年就要用煤 5000万吨, 生产30年就要用煤 15亿吨。媒体报道, 我国到 2020 年将投资 370 亿美元(2500亿元人民币),使煤制低碳烯烃的能力达到 1000万吨/年。据此计算,建设 100万吨/年煤制低碳烯烃能力需要投资 250 亿元人民币,可能还要更多一些。因此,没有远低于市场价格的原料煤供应,发展煤制低碳烯烃生产是难以为继的。二是煤制烯烃耗水量很大。煤制甲醇的吨耗水量约为 15t,高于煤间接液化制油的耗水量。甲醇制烯烃( MTP)也生产水,可是 1.8 t 甲醇才生产 1t 水。因此,水资源匮乏煤资源丰富的地区发展煤制低碳烯烃生产也是难以为继的。三是煤制烯烃是高污染、高安全要求的行业,要实现绿色、环保、低碳、节能,技术要求高,难度很大。目前我国已拥有自主知识产权的甲醇制烯烃技术,但大型化的煤制合成气技术和合成气制甲醇技术还需要引进。因此,落实国家的方针政策,建设几个示范项目是必要的,不具备煤资源、水资源、环境容
温馨提示
- 1. 本站所有资源如无特殊说明,都需要本地电脑安装OFFICE2007和PDF阅读器。图纸软件为CAD,CAXA,PROE,UG,SolidWorks等.压缩文件请下载最新的WinRAR软件解压。
- 2. 本站的文档不包含任何第三方提供的附件图纸等,如果需要附件,请联系上传者。文件的所有权益归上传用户所有。
- 3. 本站RAR压缩包中若带图纸,网页内容里面会有图纸预览,若没有图纸预览就没有图纸。
- 4. 未经权益所有人同意不得将文件中的内容挪作商业或盈利用途。
- 5. 人人文库网仅提供信息存储空间,仅对用户上传内容的表现方式做保护处理,对用户上传分享的文档内容本身不做任何修改或编辑,并不能对任何下载内容负责。
- 6. 下载文件中如有侵权或不适当内容,请与我们联系,我们立即纠正。
- 7. 本站不保证下载资源的准确性、安全性和完整性, 同时也不承担用户因使用这些下载资源对自己和他人造成任何形式的伤害或损失。
最新文档
- 行政管理与组织优化策略试题及答案
- 2024年项目管理资格的考试技巧与策略试题及答案
- 证券从业资格证考试考试经验总结试题及答案
- 2025年国际金融理财师资格考试的准备计划和策略试题及答案
- 充分准备2025年证券从业资格证考试试题及答案
- 2024年项目管理流程分析试题及答案
- 2025年注会考试的法律知识重要性及试题及答案
- 2024园艺师考试模拟测试试题及答案
- 注册会计师的职业发展方向试题及答案
- 2024年项目管理专业人士资格认证试题及答案概述
- 2024-2025学年统编版语文二年级下册 期中测试题(含答案)
- 2025年高级工程测量员(三级)技能认定理论考试题库(含答案)
- JJF(闽)1097-2020总溶解固体(TDS)测定仪校准规范-(现行有效)
- 推拉门定制安装合同协议书范本
- 麦迪床边重症系统操作指南
- 急诊腹痛医学课件
- 机械完整性专题知识讲座
- 《生态环境规划》课程教学大纲
- DB43∕T 1817-2020 公路货运车辆不停车超限超载检测系统建设与使用技术规范
- 人际交往与沟通概述课件
- 丛枝菌根真菌的功能多样性分析
评论
0/150
提交评论