

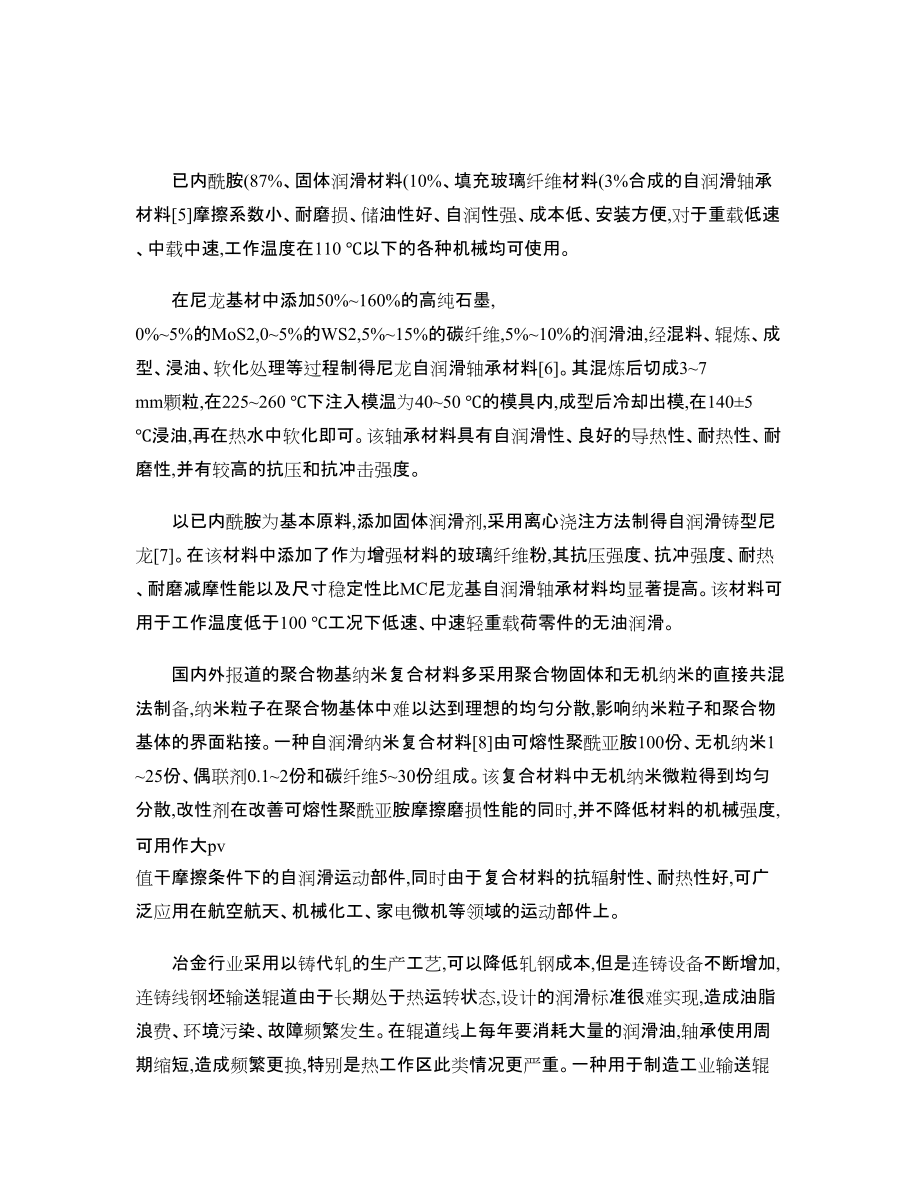


版权说明:本文档由用户提供并上传,收益归属内容提供方,若内容存在侵权,请进行举报或认领
文档简介
1、聚合物基自润滑轴承材料刘超锋1,杨振如2(1.郑州轻工业学院材料与化学工程学院,河南郑州 450002;2.郑州财贸学校,河南郑州 450066摘要:概述了热塑性塑料基和热固性塑料基自润滑轴承材料,重点介绍了以PTFE和聚酰胺为基础的热塑性塑料基自润滑轴承材料,总结了聚合物基自润滑轴承材料的研究热点。关键词:自润滑轴承;材料;聚合物基添加少许润滑剂或者完全没有润滑剂,使滑动轴承自身具有润滑性的轴承叫做自润滑轴承。自润滑轴承技术完全突破了一般依靠油脂润滑的局限性而实现了无油润滑,省去了润滑装置及润滑油、脂的密封装置,因而使轴承的设计大大简化,成本大幅度降低。由于经济、生态环境以及技术等方面的原因
2、,自润滑材料轴承技术是目前润滑技术的发展趋势,机械强度高和摩擦性能好的自润滑复合材料的开发成为摩擦学领域的重要热点1。聚合物基自润滑轴承材料以其重量轻、成型性好等优点也受到此领域的研发人员的关注。1 热塑性树脂基自润滑轴承材料1.1 PTFE“塑料王”聚四氟乙烯(PTFE常被选作非金属轴承材料,但纯PTFE其弯曲强度、压缩强度仅为10 MPa,弹性模量仅约400 MPa,且硬度低、蠕变较大、回弹性差、耐磨损性也很低。PTFE基复合材料轴承一般都是通过添加增强纤维或/和粉状功能填料进行改性,使其强度、刚度、抗蠕变性、耐磨损性等有明显提高之后制成的。但受成型工艺限制,纤维、填料的体积含量一般不超作
3、者简介:刘超锋(1969,男,河南郑州人,工学硕士,副教授,主要从事材料与化学工程技术的研究。过40%,氟塑料基复合材料滑动轴承的极限pv值一般约为1 MPam/s。氟塑料基复合材料作为耐磨减摩衬层与钢背复合在一起制造的复合结构滑动轴承,仍不能满足pv值较大的传动技术要求。又因该复合结构轴承的薄钢板制钢背结构,还制约其在腐蚀环境中的推广应用。耐高温的以氟塑料为基体树脂的自润滑轴承复合材料2,3中的功能改性剂包括占基体材料质量10%25%的微粒状功能填料和占基体材料质量010%的高分子改性剂,微粒状功能填料包括一种或一种以上的粒径100 nm的纳米粒子。该滑动轴承,由于纳米粒子增强、增韧改性,其
4、最高极限载荷在原来的基础上提高25%以上,最高失效温度提高40 以上,pv值提高30%以上,如无背衬聚四氟乙烯基纳米复合材料滑动轴承的pv值达1.46 MPam/s。1.2 聚酰胺对于在无润滑条件下工作的滑动轴承,可采用与聚酰胺和生产工艺不同的其它塑料为基础的复合材料加工,保证其尺寸稳定性好,摩擦偶的承载能力高。普通尼龙轴承的缺点是耐温、抗冲击以及耐磨性能差。一种自润滑浇铸油尼龙滑动轴承4采用高分子聚合工艺加工,在单体己内酰胺热熔化过程中加入油助剂NZ-HA型矿物油,在已内酰胺熔化的同时抽真空,然后加入催化剂NaOH、继续抽真空,至已内酰胺与油助剂全部熔融后停止真空聚合反应,继续加温至1401
5、45 时,加入助催化剂甲苯二异氰酸脂,然后迅速将反应后的液体倒入160170 的轴承模具中,保温15分钟,即得轴承毛坯,再经水处理和油处理,最后经精密车床加工而成。其优点是机械强度高,耐磨性能好,使用寿命长,成本低,便于安装,其加工工艺简单。已内酰胺(87%、固体润滑材料(10%、填充玻璃纤维材料(3%合成的自润滑轴承材料5摩擦系数小、耐磨损、储油性好、自润性强、成本低、安装方便,对于重载低速、中载中速,工作温度在110 以下的各种机械均可使用。在尼龙基材中添加50%160%的高纯石墨, 0%5%的MoS2,05%的WS2,5%15%的碳纤维,5%10%的润滑油,经混料、辊炼、成型、浸油、软化
6、处理等过程制得尼龙自润滑轴承材料6。其混炼后切成37 mm颗粒,在225260 下注入模温为4050 的模具内,成型后冷却出模,在1405 浸油,再在热水中软化即可。该轴承材料具有自润滑性、良好的导热性、耐热性、耐磨性,并有较高的抗压和抗冲击强度。以已内酰胺为基本原料,添加固体润滑剂,采用离心浇注方法制得自润滑铸型尼龙7。在该材料中添加了作为增强材料的玻璃纤维粉,其抗压强度、抗冲强度、耐热、耐磨减摩性能以及尺寸稳定性比MC尼龙基自润滑轴承材料均显著提高。该材料可用于工作温度低于100 工况下低速、中速轻重载荷零件的无油润滑。国内外报道的聚合物基纳米复合材料多采用聚合物固体和无机纳米的直接共混法
7、制备,纳米粒子在聚合物基体中难以达到理想的均匀分散,影响纳米粒子和聚合物基体的界面粘接。一种自润滑纳米复合材料8由可熔性聚酰亚胺100份、无机纳米125份、偶联剂0.12份和碳纤维530份组成。该复合材料中无机纳米微粒得到均匀分散,改性剂在改善可熔性聚酰亚胺摩擦磨损性能的同时,并不降低材料的机械强度,可用作大pv 值干摩擦条件下的自润滑运动部件,同时由于复合材料的抗辐射性、耐热性好,可广泛应用在航空航天、机械化工、家电微机等领域的运动部件上。冶金行业采用以铸代轧的生产工艺,可以降低轧钢成本,但是连铸设备不断增加,连铸线钢坯输送辊道由于长期处于热运转状态,设计的润滑标准很难实现,造成油脂浪费、环
8、境污染、故障频繁发生。在辊道线上每年要消耗大量的润滑油,轴承使用周期缩短,造成频繁更换,特别是热工作区此类情况更严重。一种用于制造工业输送辊道中的高分子高温无润滑轴承材料9由高温树脂、固体润滑剂、碳纤维复合成聚酰亚胺复合材料,合成聚酰亚胺有六组配方。其工艺为:首先按六组配方在乙醇溶液中反应合成聚酰胺酸液;开环加成,合成聚酰胺酸;加入固体润滑剂和碳纤维,混合均匀;环化脱水,干燥,研成粉末状聚酰亚胺复合粉。用它制造的耐高温无润滑轴承衬套可以取代各类粉末冶金含油轴承、金属滑动轴承和滚动轴承,其使用寿命可提高23倍。全芳香族聚酰胺的聚间苯二甲酸间苯二胺树脂(PMIA树脂和聚对苯二甲酸对苯二胺浆粕(PP
9、TA浆粕均具有机械强度高、耐温性好、耐溶剂性强等优异性能。此外,PPTA浆粕还有易于分散的特点。两种材料还有相似的化学组成及结构,也就是说树脂基体与纤维有良好的相容性。在聚间苯二甲酸间苯二胺中填加聚对苯二甲酸对苯二胺浆粕、石墨、MoS2等固体润滑剂及稀土氟化物等改性剂,通过湿法或干法混合将浆粕和原料混合均匀,在温度为300330 ,压力为60 120 MPa下热压制成复合材料10,此材料的摩擦系数0.25,磨损率1.8910-15m3/Nm。复合材料可在化工、纺织、汽车、机械等领域的轴承上使用。碳纤维和芳纶纤维具有强度高、耐高温等优点,但是芳纶浆粕纤维比碳纤维有更大的比表面积、更好的韧性和耐冲
10、击能力,和基体树脂结合力强,有很好的增强增韧效果;而碳纤维有高的模量,性质刚硬,石墨化的结构使它具有固体润滑剂功能,是一种优异的耐磨材料,碳纤维又具有导热、导电性能,热膨胀系数小,用它制成的复合材料尺寸稳定性好,将以上两种纤维充分均匀混合后,制成一种高性能复合材料,即耐磨、耐高温、传热、导电等性能优异的工程材料。金属粉末冶金轴承的比重大,重量比塑料重,且吸油性能、润滑性能、耐腐蚀性能不及塑料轴承;塑料轴承比粉末冶金轴承轻,摩擦系数小,磨耗小,但塑料轴承导热系数小,容易造成摩擦热积聚而使轴承温度升高,并且塑料的热变形温度低,尺寸稳定性差。一种轴承用混杂增强高性能复合材料11的组成为短切碳纤维、芳
11、纶浆粕纤维、填料和聚苯硫醚、聚醚酮,聚酰亚胺等在260 以上耐高温树脂;其中,短切碳纤维、芳纶浆粕纤维、填料和耐高温树脂的重量比分别为0% 40%、5%50%、0%55%、30%85%,当短切碳纤维重量比为0时,芳纶浆粕纤维、填料和耐高温树脂的重量比为5%50%、5%55%、30%85%。该材料可用于制造纺纱锭小轴承、高速电机轴承、石墨轴承、含油轴承等。玻璃纤维或石墨作为添加剂的尼龙含油树脂轴承往往采用重量比20%30%的玻璃纤维,尽管轴承的耐磨性得以提高,但随之产生的问题是摩擦系数相应增大,直接影响摩擦副的使用寿命。一种高分子含油轴承12的成分为:己内酰胺100,石墨02,炭黑311,高温油
12、39,氢氧化钠0.150.2,甲苯二异氰酸酯 0.3 0.5。由于以炭黑取代玻璃纤维,同时降低了石墨的重量比,使高分子含油轴承的强度提高约40%,耐磨性提高35倍,摩擦力降低2040%,抗拉强度提高到6274 MPa,而摩擦系数仅为0.10 0.18。2 热固性树脂基自润滑轴承材料以酚醛树脂为粘合剂,有机无机填料为填充材料,填加纤维及弹性材料进行增强增韧,混合后热压成形的轴承套13冲击强度可达12 kJ/m2,弯曲强度可达95 MPa。该轴承件还具有自润滑性,可进行车削加工,成功替代日本进口材料。3 结语聚合物基自润滑轴承材料领域研究较多的是聚酰胺基,从增强方式来看,纤维增强研究最为活跃。用来
13、增强的纤维材料有玻璃纤维、碳纤维和浆粕纤维,以碳纤维应用最多。填充增强的研究方面,还出现了采用纳米材料作为填料的技术。不管采用何种增强方式,在提高轴承材料力学性能的基础上,提高耐摩擦磨损性能及其它性能,仍是下一步发展聚合物基自润滑轴承材料需要解决的问题。参考文献1 阎家宾.自润滑滑动轴承J.世界橡胶工业,2005,32(4:3135.2 李学闵,贾衍才,苏衍良等.耐高温聚合物基复合材料滑动轴承P.中国专利:CN 1 431 406A,2003-07-23.3 李学闵,苏衍良,赵顺伟等.氟塑料基纳米复合材料滑动轴承P. 中国专利:CN 1 431 407A,2003-07-23.4 张静霞.自润
14、滑浇铸油尼龙轴承及其加工工艺P.中国专利:CN 1 226 477A,1999-08-25.5 芦新选.填充尼龙6基自润滑轴承材料P. 中国专利:CN 1 021 374A,1988-10-12.6 黄根宝.含油尼龙自润滑轴承材料P. 中国专利:CN1 043 776A,1990-07-11.(下转第31页我们的研究结果,因素是非常重要的,无论如何应该把能量高效地传递给压电材料。关于其它因素,材料特性不同,即使没有太大的问题,也要有良好的条件。因此重要的是能量能直接传播给材料,关于复合型减振材料的有机物相互间怎样的混合方式就会容易传播能量呢?图3 有机复合材料的构成成分和化学结构有机-有机混合
15、材料是在有机高分子中加入有机低分子,效果非常好。再在树脂中掺入像炭黑体系填料那样的导电物质的话,作为声学材料具有高性能。利用这一特性能制作出特殊性质的材料。我们作过的试验曾发现细圆柱形的结晶不但减振性能提高,而且声学特性也变好,见图3。4 用控制结晶形状作低频减振薄膜我们用热处理精确控制有机低分子的结晶形态能制作出低频吸声材料。把有机低分子加工成中间相的特殊构造,用它就能制作低频吸声材料。用特别薄的薄膜作低频吸声材料在当今还没有。我们用1 mm以下的薄膜材料应该能吸收低频的声音。现在抑制低频的效果是困难的状况,但发现了上述原理上是可行的。但是,吸收低频的压电PVDF 100 mm100 mm薄
16、膜高达3万日元,所以现在的应用只限于声学元件和超声波诊断等。聚合物的共混物比有机低分子的PVDF薄膜便宜,用聚合物的共混物能够容易制作成薄膜和涂料,可以认为是减振降噪的有效材料。不可思议的是,把有机混合材料的薄膜装配在音箱板上听音乐的话,发现变成了老音箱那样的舒适音响效果的现象。(译自安立美.工嶪材料,2006,54(4: 14.(上接28页7 华洪良.增强自润滑铸型尼龙P. 中国专利:CN 1032 345A,1989-04-12.8 阎逢元,蔡辉,刘维民等.自润滑纳米复合材料及其制备方法P. 中国专利:CN 1 414 037A,2003-04-30.9 徐福卿.高分子高温无润滑轴承材料P. 中国专利:CN 1 422 902A,2003-06-11.10刘旭军,李同生,田农等
温馨提示
- 1. 本站所有资源如无特殊说明,都需要本地电脑安装OFFICE2007和PDF阅读器。图纸软件为CAD,CAXA,PROE,UG,SolidWorks等.压缩文件请下载最新的WinRAR软件解压。
- 2. 本站的文档不包含任何第三方提供的附件图纸等,如果需要附件,请联系上传者。文件的所有权益归上传用户所有。
- 3. 本站RAR压缩包中若带图纸,网页内容里面会有图纸预览,若没有图纸预览就没有图纸。
- 4. 未经权益所有人同意不得将文件中的内容挪作商业或盈利用途。
- 5. 人人文库网仅提供信息存储空间,仅对用户上传内容的表现方式做保护处理,对用户上传分享的文档内容本身不做任何修改或编辑,并不能对任何下载内容负责。
- 6. 下载文件中如有侵权或不适当内容,请与我们联系,我们立即纠正。
- 7. 本站不保证下载资源的准确性、安全性和完整性, 同时也不承担用户因使用这些下载资源对自己和他人造成任何形式的伤害或损失。
最新文档
- 努力不止 2024年公务员试题及答案
- 2025股权转让合同模板2
- 市民大厅租房合同范本
- 船舶沙石运输合同范本
- 私人厂房转让合同范本
- 揭阳农村建房合同范本
- 化工配方出售合同范本
- 武汉科技职业学院《计算结构力学》2023-2024学年第二学期期末试卷
- 大连大学《园林设计(一)》2023-2024学年第二学期期末试卷
- 燕山大学里仁学院《中外文学经典作品赏析》2023-2024学年第二学期期末试卷
- 2024年电子商务师真题试题及答案
- 园艺植物遗传育种 课件全套 第1-10章 绪论-新品种的审定与推广繁育+实训
- 2025-2030中国免洗护发素行业市场发展趋势与前景展望战略研究报告
- 《智能优化算法解析》 课件 第6章-基于群智能的智能优化算法
- 《红岩》中考试题(截至2024年)
- 华为IAD132E(T)开局指导书
- (2025)二十大知识竞赛题库(含答案)
- 2025年华北电力大学辅导员及其他岗位招考聘用54人高频重点提升(共500题)附带答案详解
- 2022《信访工作条例》学习课件
- 2025年高考政治一轮复习知识清单选择性必修一《当代国际政治与经济》重难点知识
- 儿童青少年肥胖食养指南(2024年版)
评论
0/150
提交评论