

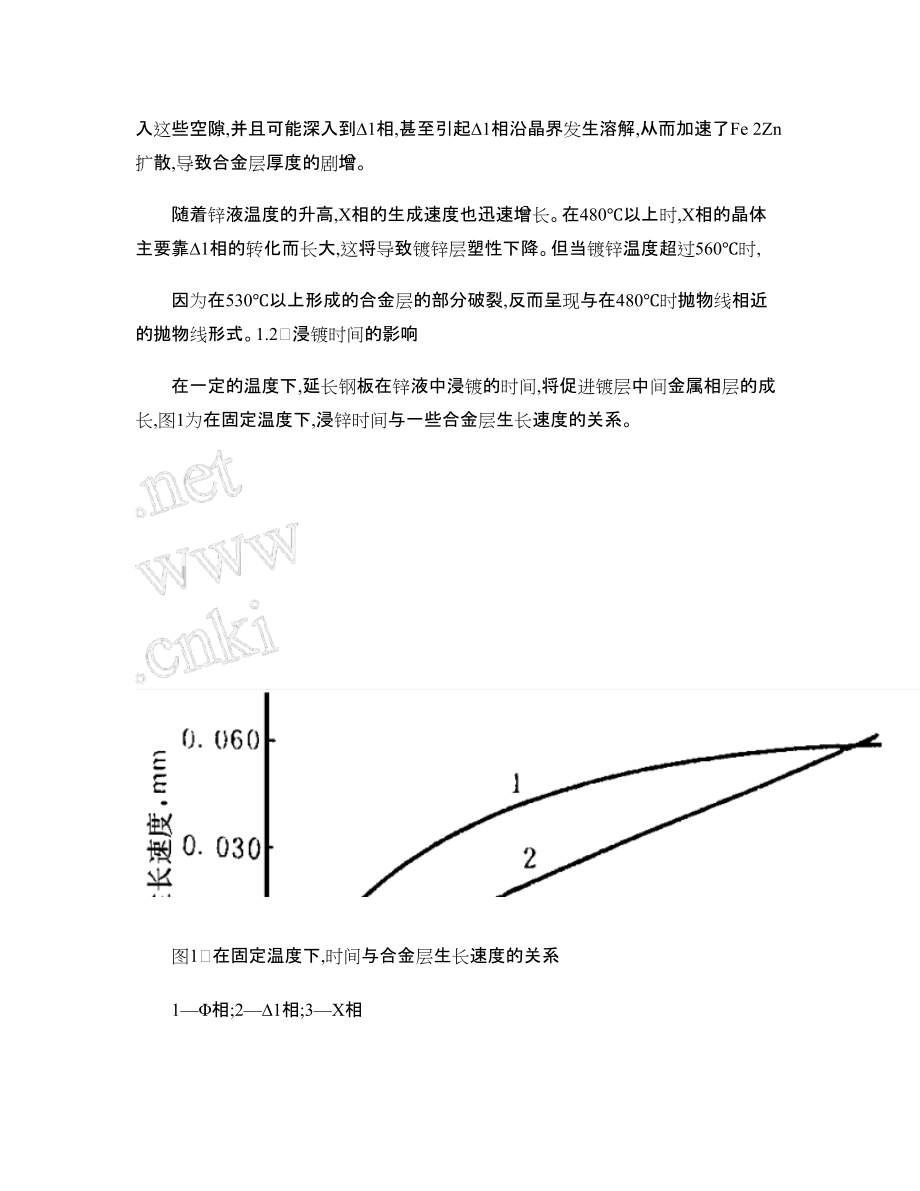


版权说明:本文档由用户提供并上传,收益归属内容提供方,若内容存在侵权,请进行举报或认领
文档简介
1、技术讲座热镀锌钢板生产概述第三讲影响镀层结构的因素 朱立(鞍钢技术中心摘要钢铁的热浸镀锌是一个物理化学反应过程,热浸镀锌产品质量与钢板的原始状态及锌液中的化学成分有着密切的关系。系统地介绍了镀锌温度、浸镀时间、钢中的化学成分及锌液中的其它微量元素对镀层结构的影响。关键词镀锌层结构B rief In troducti on of the P roducti on of Ho t Galvan ized Steel SheetL ectu re 3Facto rs A ffecting on P lated Coat Con structi onZhu L i(A ISC T echno logy
2、 Cen ter Abstract Ho t di p galvan ized of steel is a physical and Chem ical reacti on p rocess .T he quality of ho t di p galvan ized p roducts is in clo se relati on sh i p w ith the p ri m ary statu s of sheet and the chem ical con stituen t in zinc ligu id .T he temperatu re of galvan izing ,the
3、 ti m e of di p ,the chem ical con stituen t of steel and o ther m icro 2elem en t in zinc liqn id affect 2ing on the p lated coat con structi on are in troduced system atically .Key W ords zinc coating con structi on1锌液温度及浸镀时间对镀层结构的影响1.1锌液温度的影响用溶剂法进行钢板镀锌时,在钢板进入朱立高级工程师鞍钢技术中心钢研所邮编114001锌液处,锌是被冷却的,其温度
4、多在430460左右,这时铁损按照低抛物线规律随镀锌时间而变化,其关系可用下式表示:G =A t 12式中:G 铁损;A 常数;t 时间。当镀锌温度接近480时,Fe 2Zn 之间的扩散速度加快(合金层增厚加快,主要是增加了塑性较差的相的厚度,从而镀层的塑性变差。当镀锌温度超过480500时,铁损可以用直线关系来表示:G =B t ,B 亦为常数。铁在锌中的溶解量增长较快,这是因为,当镀锌温度超过480时,相的晶体形成速度很慢,只能形成为数极少的且带有较大空隙的晶核,这样液态的锌就会侵入这些空隙,并且可能深入到1相,甚至引起1相沿晶界发生溶解,从而加速了Fe 2Zn 扩散,导致合金层厚度的剧增
5、。随着锌液温度的升高,相的生成速度也迅速增长。在480以上时,相的晶体主要靠1相的转化而长大,这将导致镀锌层塑性下降。但当镀锌温度超过560时,因为在530以上形成的合金层的部分破裂,反而呈现与在480时抛物线相近的抛物线形式。1.2浸镀时间的影响在一定的温度下,延长钢板在锌液中浸镀的时间,将促进镀层中间金属相层的成长,图1为在固定温度下,浸锌时间与一些合金层生长速度的关系。 图1在固定温度下,时间与合金层生长速度的关系1相;21相;3相由图可见,在浸锌温度为450,钢的成分为C 0.08%,M n 0.40%,Si 0.006%,P 0.021%和Cu 0.02%条件下,相的厚度达到正常的0
6、.004mm 时,需要不到1m in 的时间。对于工业纯铁,需要3045s 。相起初生长得很快,超过了1相。在大约90m in 后,1相的生长速度就接近了相,这表明了Fe 通过和1相的扩散比通过相的扩散来得快。所以当相长大以后,锌必须经过更长的路径,于是的生长就落后于1相的生长,因此在正常镀锌时(浸镀620s 相最厚。这一点对镀层的塑性极其重要,因为相是脆性的单斜晶系结构,相越厚,镀层的塑性越差。所以在热镀锌时,尽量缩短浸锌时间,可以减少相的厚度,从而使镀层的塑性得到改善。2钢基结构与成分的影响2.1钢铁结构与碳的影响钢铁中碳的存在形式不同,对Fe 2Zn 反应的影响也不同。钢中的碳以粒状珠光
7、体和层状珠光体存在时,铁的溶解速度很快。实验证明,在同样条件下,含0.8%C 的粒状珠光体钢比工业纯铁的铁损大十倍。如果碳以索氏体或屈氏体组织存在时,则铁在锌中的溶解就比较慢。碳不仅影响铁的溶解,还会影响镀锌层外观。例如,由于退火温度高而形成的晶间渗碳体,提高了钢板的表面张力,影响了锌液对钢板的浸润能力,影响了锌的流动性,容易使表面出现锌瘤缺陷。除了组织结构的影响之外,碳含量本身就强烈地影响Fe 2Zn 反应。一般来说,碳含量越高,Fe 2Zn 反应就越剧烈,铁损就越高。Fe 2Zn 合金层也就变得越厚,从而使整个镀锌层性能变坏,影响了镀锌板的机械加工性能,因此,应尽量选择含碳量为0.05%0
8、.15%之间的低碳钢板来生产镀锌钢板。2.2钢铁中其它成分的影响钢铁中除了含碳之外,一般都含有M n、S、P、Si、Cu、T i等元素。它们对钢铁热镀锌有着不同的影响。(1钢中锰和硫的影响钢铁中锰和硫的含量极少,实践证明,钢基中的锰和硫对镀锌层的结构影响很小。(2钢中磷的影响钢中如含有杂质磷,能使钢材产生冷脆现象。所以生产过程中往往把磷含量控制得很低,一般在0.05%以下,这种成分的钢板在镀锌时,不会造成大的影响,即使磷含量为0.06%0.12%的高磷薄板,在热镀锌时也无明显的异常。但是当钢中的含磷量达到了0.15%时,镀锌层组织会生成特别厚而且容易开裂的Fe2Zn合金层,相变薄而相和1相则生
9、长得较快。这表明铁原子扩散得快,从而使镀锌板表面变得灰暗而失去花纹,形成斑点,同时镀层的粘附性也变差。(3钢铁中的硅对镀锌的影响钢中的硅对钢板热浸镀锌有明显的影响,经验证明,钢基中的硅含量高会引起镀锌层中Fe2Zn合金层相的剧烈增长,这使镀层变厚并形成灰色镀层,同时使镀层附着性能变坏。但是,这种镀层厚度随着钢基中硅含量增加而变厚的关系存在一种波浪式变化的现象,这种现象被叫做圣德林(Sandelin效应。这种现象一般在浸锌3m in之后发生。这在现代镀锌生产中,由于浸锌时间短而不会出现。硅对镀锌的影响有以下几点:硅使铁在锌液中的浸蚀加快,试验证明,在460时,硅含量为0.2%的钢比碳含量为0.2
10、%的钢在锌液中的铁损大了1倍。含硅钢在锌液温度为520下具有最大的重量损失。硅对镀层厚度有明显的影响,硅含量低的钢在镀锌后可以获得致密的Fe2Zn合金层,而含硅量达到0.3%时,1层被破坏,使结晶变成粗大而自由生长的晶体,这种反应产物是疏松的。含硅量还会影响镀层外观。有的研究发现,当硅含量为0.06%0.07%时,镀层灰暗色斑点最多,由于1相迅速长大,相晶粒被迫向表面推移,致使表面锌层很薄甚至不存在。关于硅对镀层产生影响的原理,有着不同的见解,有观点认为是硅加速了Fe2Zn合金层的生长,并形成了薄的纯锌层,而又有观点认为是由于钢中Si氧化而生成的Si O2在起作用。(4钢中含铜和钛对热镀锌的影
11、响钢中含铜量一般是很低的,由于废钢中含铜量较多,可使钢中含有一定量的铜。铜的存在对镀锌时的铁锌反应并没有大的影响,但是由于铜在热轧后冷却时集聚在铁素体的晶界处,并且铜与铁相比,耐氧化能力强,因而在钢板表面出现铜的富集。这在轧制时,由于铜的强度与铁的差别,而形成网状裂纹,并且能保留到冷轧之后,这样的表面在热镀锌之后容易形成类似划伤或条状的疤痕状的缺陷。钢中的钛大多是为了获得高强度而加入的。它以固溶体的方式存在于2Fe的晶格中,它的存在对镀锌钢板基板性能的影响较大,但对钢在锌中的浸蚀速度影响则不大。不过钛对镀锌层组织的影响有它的独特之处。这就是它使合金层发展最厚的不是1而是相。另外含钛钢镀锌后表面
12、较好,因为钛的存在在钢中形成了氢的陷井,这使钢在酸洗或保护气氛还原时,进入钢中的氢气的逸出减少,从而防止了氢气在镀锌时逸出对纯锌层的影响。(5钢中镍和铬对热镀锌的影响钢中镍的含量为5%,在460温度下镀锌,锌液对钢浸蚀速度降低了30%,当钢中含镍达8%时,镀锌层会减薄,这说明镍控制了相的增长。钢中的铬对钢在锌中的浸蚀速度有很大影响,当钢中铬含量为0.6%时,锌液对钢的浸蚀速度增加了1倍,当钢中含铬为4% 9%时,锌液对钢的浸蚀速度会有所降低。但是,当钢中的铬含量上升到13%18%时,则会使合金层相快速发展,镀层会变得疏松而大量漂移,所以不锈钢并不一定比碳钢更耐锌液浸蚀。(6钢中铝对热镀锌的影响
13、铝作为一种对钢铁热镀锌起重要作用的元素,它对Fe2Zn反应有着极大的影响,并引起了镀锌层生成机理的变化。但是,当铝作为钢铁中的成分时,它对Fe2Zn反应几乎没有影响。而作为脱氧剂用来生产镇静钢时,则会对镀锌层产生不良的影响。铝含量较高(如浇注时加入0.7%以上会导致表面缺陷。这是因为,脱氧时生成的三氧化二铝会在钢中形成很细的偏析,这在热镀锌时容易引起漏镀而产生花斑。3锌液中不同元素对热镀锌的影响(1锌液中铁的影响铁作为锌锭的杂质而被带入锌液,其量是很小的,最多不超过0.03%(4号锌锭。在450时,铁在锌中的溶解度为0.03%,若锌液中铁的含量超过0.03%,铁将与锌生成铁锌化合物FeZn7,
14、由于其比重大于锌而沉入锅底,即成为底渣。当锌液中含铝时,也有可能和铝反应,生成Fe2A l5,其比重较锌轻而浮起,形成浮渣。两种渣的生成都消耗了大量的锌和铝。锌液中铁的存在,将使锌液的粘度和表面张力增加,从而使锌液的流动性变差,同时恶化了锌液对钢板的润湿条件。如相应地延长镀锌时间则会使镀层变厚,而且主要是使相变厚。锌液中铁的存在还会提高镀层的硬度,并阻碍再结晶过程。以上的影响都已为实验结果所证实。总之铁的过量存在是有害的,它使镀层变脆,表面变灰暗,增加锌渣的生成,增加了锌和铝的消耗量。(2锌液中的铅对钢铁热镀锌的影响锌液中的铅不仅仅是因为自然界中锌铅总是伴生成矿而作为杂质由锌锭带入,而有时在镀
15、锌时是作为原料加入的,铅在温度为450的锌液中的溶解度为1.5%,过量的铅会沉到锌锅底部。以往的研究结果表明,铅是以珠状弥散于纯锌层中的,它对热锌镀时的Fe2Zn反应和镀层的其它合金层没有影响。由于铅的存在,使锌液的粘度和表面张力降低,增强了锌液对钢板的浸润能力,从而减少了带钢的浸锌时间,同时铅的存在还能使锌液的熔点降低。这延长了锌液的凝固时间,促进了锌花的成长,可以获得较大的锌花。在使用铁制锌锅时,在锌锅内加入铅,使之形成1030c m厚的铅层(湿法镀锌时更多,这一方面是为了以铅作为Fe2Zn之间的传热介质,减少了铁与锌的接触面积,从而减少了锌对铁锅的侵蚀。另一方面,锌渣可以浮在铅液上面,便
16、于捞取。在锌液中加入铅也带来一些问题。例如:铅的加入会使镀层颜色发暗;当铅在锌液中的含量超过1%时,会引起镀层的晶间腐蚀,降低镀层的耐腐蚀性能;铅的蒸发将污染环境,危害操作人员的健康。(3锌液中金属锑对热镀锌的影响金属锑的加入主要是代替铅以利于形成较大的锌花。锑的加入不会象铅那样引起镀层的晶间腐蚀。但是,锑的加入也带来一些不利的影响。例如:锑会引起纯锌层的脆性,降低其挠性;另外它还会使合金层增厚;增加铁在锌中的溶解度。从而增加铁损,也使锌的损耗增加,还会使镀层变得灰暗;在使用钢制锌锅时,一旦出现局部过热现象时锑使钢的浸蚀增加。另外实验证明,在酸性介质中,锑使镀层的腐蚀溶解速度增加。锌液中含有0
17、.01%0.02%的作为杂质存在的锑时,锑的不良影响并不明显,当含量达到0.05%时即产生不利影响。(4锌液中的锡对热镀锌的影响锡作为锌锭中的杂质元素,含量不应大于0.002%,当含量大于0.002%时,会使锌液的粘度增加,并使镀层的粘附性能变坏。影响镀锌层的挠性。当含量达到5%时,合金层的平均厚度会增加38%,曾有实验证明1%的锡含量可以抵消0.05%的铝所起的作用。但是当锡含量超过1%时,又可以使Fe2Zn 合金层减薄,如锡含量超过5%时,可使合金层的厚度降到原来的6%,锡的加入主要是使镀层得到较大的锌花,或改进表面光泽使板面白亮。锡的增加不仅增加锌液的粘度,引起镀锌层厚度的变化,而且还会
18、引起镀层的耐腐蚀性能变化,当含锡量较高,超过0.3%时,锡会聚集在锌的晶粒表面而形成Zn2Sn 共析,增加了镀层的腐蚀速度,并且在腐蚀后出现坑点。锡与锑一样,它的存在降低了镀层在酸性介质中的耐腐蚀性能。(5锌液中的镉对热镀锌的影响作为锌中的杂质,镉的含量不超过0.001%0.07%,在此范围内,镉对镀锌层的组织和铁在锌中的溶解度都有影响,在锌液温度较低时,影响尚不显著,当温度升高时,对铁的浸蚀有加速作用,浸蚀速度可提高1倍以上。这对使用铁锅进行镀锌生产是一个值得重视的问题。镉有使锌结晶粗化的作用,可以在表面获得较大的锌花。锌液中镉的存在会使镀层中的铁合金层变厚,铁损增加,并降低镀层的挠性。当镉含量达到2.5%2.8%时,铁损量达到最高值。另外镉的蒸汽对人体有害,当镉含量较高时,可以通过加铝来降低其危害。(6锌液中镁对热镀锌的影响镀锌层中镁的存在可明显地提高镀层的耐腐蚀性能。还可以消除锌液中铅对耐蚀性的不良影响,当镁含量在0.024%0.084%时,耐蚀性最好。但是当
温馨提示
- 1. 本站所有资源如无特殊说明,都需要本地电脑安装OFFICE2007和PDF阅读器。图纸软件为CAD,CAXA,PROE,UG,SolidWorks等.压缩文件请下载最新的WinRAR软件解压。
- 2. 本站的文档不包含任何第三方提供的附件图纸等,如果需要附件,请联系上传者。文件的所有权益归上传用户所有。
- 3. 本站RAR压缩包中若带图纸,网页内容里面会有图纸预览,若没有图纸预览就没有图纸。
- 4. 未经权益所有人同意不得将文件中的内容挪作商业或盈利用途。
- 5. 人人文库网仅提供信息存储空间,仅对用户上传内容的表现方式做保护处理,对用户上传分享的文档内容本身不做任何修改或编辑,并不能对任何下载内容负责。
- 6. 下载文件中如有侵权或不适当内容,请与我们联系,我们立即纠正。
- 7. 本站不保证下载资源的准确性、安全性和完整性, 同时也不承担用户因使用这些下载资源对自己和他人造成任何形式的伤害或损失。
最新文档
- 五声教育计划
- 验货专员年终总结
- 面对考试的CFA试题及答案心态调整
- 第一章 5 弹性碰撞和非弹性碰撞-2025版高二物理选择性必修一
- 第六章 作业14 生活中的圆周运动-2025版高一物理必修二
- 河南省南阳市邓州市春雨国文学校2024-2025学年高一上学期入学摸底考试语文试题
- 教导主任个人工作总结7
- 基于电子书包的小学英语理解性教学实验研究
- 高中定语从句知识点讲解
- 支教工作个人总结2
- 2025年浙江宁波奉化区农商发展集团有限公司招聘笔试参考题库附带答案详解
- 2025年高考物理一轮总复习:牛顿运动定律(原卷版)
- 2025年领导胜任力测试题及答案
- 2025年医院基建科面试题及答案
- 中职高考数学一轮复习讲练测专题一 集合与充要条件(测)原卷版
- 水利项目申报专项债、中央预算内资金、超长国债
- 企业财务会计(第四版)教案27:合同成本
- 2025年春季安全教育主题班会教育记录
- 工厂安全事故案例100例
- 人工湿地施工合同
- 公司安全事故隐患内部举报、报告奖励制度
评论
0/150
提交评论