

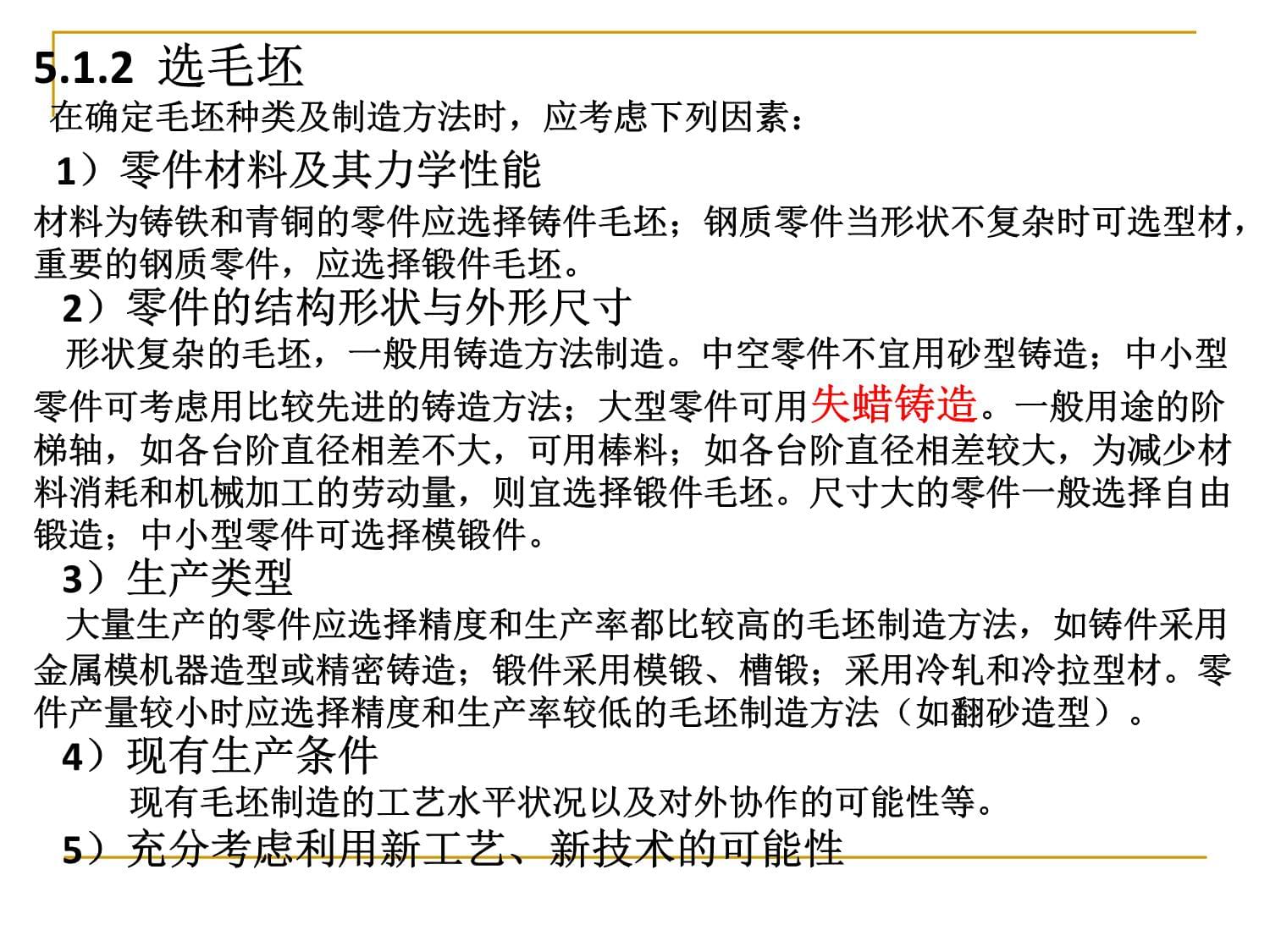


版权说明:本文档由用户提供并上传,收益归属内容提供方,若内容存在侵权,请进行举报或认领
文档简介
第三章数控车床的编程与加工
第五章数控车床的编程与加工
数控车床主要用于加工轴类、套类和盘类等回转体零件。本章主要介绍在数控车床上加工此类零件的工艺处理及程序的编制。5.1车削零件的工艺分析与加工要领
5.1.1分析零件图样零件图样分析主要考虑以下几方面:
1.构成零件轮廓的几何条件由于设计原因.可能在零件图样上出现描绘零件加工轮廓的数据不充分、尺寸模糊不清等缺陷,这会增加编程的难度。具体是:1)零件图上漏掉某尺寸,影响到零件轮廓的构成。
2)零件图上的图线位置模糊或尺寸标注不清(例如某些切点)。
3)零件图上给定的几何条件不合理,造成数学处理困难。2.尺寸精度要求
分析零件图尺寸精度的要求,以判断能否利用车削工艺达到目标。在利用数控车床车削零件时,常常对零件要求的尺寸取最大和最小极限尺寸的平均值(公差带均值)作为编程的尺寸依据。3.形状和位置精度要求零件图上给定的形状和位置公差是保证零件精度的重要依据。加工时可以根据机床的特殊需要进行一些技术性处理。如保证同轴度应一刀车削出来。
4.表面租糙度要求表面租糙度是保证零件表面微观精度的重要要求,也是合理选择机床、刀具及确定切削用量的依据。
5.材料与热处理要求零件图样上给定的材料与热处理要求是选择刀具、机床型号、确定切削用量的依据。(能否切动)5.1.2选毛坯在确定毛坯种类及制造方法时,应考虑下列因素:
1)零件材料及其力学性能材料为铸铁和青铜的零件应选择铸件毛坯;钢质零件当形状不复杂时可选型材,重要的钢质零件,应选择锻件毛坯。
2)零件的结构形状与外形尺寸形状复杂的毛坯,一般用铸造方法制造。中空零件不宜用砂型铸造;中小型零件可考虑用比较先进的铸造方法;大型零件可用失蜡铸造。一般用途的阶梯轴,如各台阶直径相差不大,可用棒料;如各台阶直径相差较大,为减少材料消耗和机械加工的劳动量,则宜选择锻件毛坯。尺寸大的零件一般选择自由锻造;中小型零件可选择模锻件。
3)生产类型大量生产的零件应选择精度和生产率都比较高的毛坯制造方法,如铸件采用金属模机器造型或精密铸造;锻件采用模锻、槽锻;采用冷轧和冷拉型材。零件产量较小时应选择精度和生产率较低的毛坯制造方法(如翻砂造型)。
4)现有生产条件现有毛坯制造的工艺水平状况以及对外协作的可能性等。
5)充分考虑利用新工艺、新技术的可能性5.1.3确定装夹方法和对刀点
(1)零件的装夹在数控车床加工中,除了采用三爪自定心卡盘和四爪单动卡盘外(可调偏心),数控车床中还有许多相应的夹具,它们主要分为两大类,即用于轴类零件的夹具和用于盘类零件的夹具。
1)用于轴类零件的夹具数控车床加工轴类零件时,为保证同轴度,毛坯装在主轴顶尖和尾座顶尖之间,由主轴上的拨动卡盘或拨齿顶尖带动旋转并传递足够大的转矩,以适应主轴高速旋转车削的需要。
2)用于盘类零件的夹具这类夹具适用于无尾锥的卡盘式数控车床上。用于盘类零件的夹具主要有可调卡爪卡盘和快速可调卡盘。2.确定对刀点和换刀点
(A)对刀(主要用来确定工件坐标系的原点)对刀是操作数控车床的重要内容,对刀的好坏将直接影响到车削零件的尺寸精度。
(1)刀位点:刀位点是指在加工程序编制中,用以表示刀具特征的点,也是对刀和加工的基准点。各类车刀的刀位点如上图所示。
(2)对刀:对刀是指加工前调整刀具的刀位点,使其尽量重合于某一理想基准点,以求得此时刀位点在机床坐标系的坐标和确定工件坐标系的过程。理想基准点可设定在基准刀的刀尖上,也可设定在光学对刀镜内的十字刻线交点上。对刀一般分为手动对刀和自动对刀两种。目前,大多数的数控车床是采用手动对刀,其基本方法有:
1)定位对刀法:对刀时只要将基准刀的刀位点调整至与理想基准点重合即可。此方法简便。但其对刀精度受到操作者技术熟练程度的影响,故精度不太高,还需在加工中或试切中进行修正。
2)光学对刀法:它的定位基准通常由光学显微镜(或投影放大镜)上的十字基准刻线交点来体现。此方法比定位对刀法的对刀精度高,并且不会损坏刀尖。3)ATC对刀法:
ATC对刀法是通过一套将光学对刀镜与CNC组合在一起,从而具有自动刀位计算功能的对刀装置,也称为半自动对刀法。采用此方法对刀时,需要将由显微镜十字刻线交点体现的对刀基准点调整到机床的固定原点位置上,以便于CNC进行计算和处理。4)试切对刀法:在以上三种手动对刀方法中,均因可能受到手动和目测等多种误差的影响,其对刀精度十分有限,往往需要通过试切来修正已经设定的工件坐标系数据,以得到更加准确的结果。(B).确定对刀点1)尽量与零件的设计基难或工艺基准一致。2)便于用常规量具在车床上进行找正。3)该点的对刀误差应较小(可视性较好),或可能引起的加工误差为最小。4)尽量使加工程序中的引入或返回路线变短,并便于换刀。下图是数控车床对刀点的实际例子:
(C).确定换刀点换刀点是指在加工过程中自动换刀装置的换刀位置。换刀点的位置应保证刀具转位时不碰撞被加工零件或夹具,还应注意切削的连续,一般可设置在对刀点。较好的点5.1.4、确定加工方案
1)
制定工艺路线在数控车床加工过程中,由于加工对象复杂多样.特别是轮廓曲线的形状及位置千变万化,应该考虑以下原则:(1)先粗后精:
粗加工完成后,接着进行半精加工和精加工。其中,安排半精加工的目的是:当粗加工后所留余量的均匀性满足不了精加工要求时,则可安排半精加工作为过渡性工序,以便使精加工余量小而均匀。精加工时,零件的轮廓应由最后一刀连续加工而成。这时,加工刀具的进、退刀位置要考虑妥当,尽量沿轮廓的切线方向切入和切出,以免因切削力突然变化而造成刀具弹性变形,致使光滑连接轮廓上产生表面划伤、形状突变或滞留刀痕等疵病。粗加工轮廓
(2).先近后远这里所说的远与近,是按加工部位相对于对刀点的距离大小而言的。通常在粗加工时,离对刀点近的部位先加工,离对刀点远的部位后加工,以便缩短刀具移动距离。对于车削加工.先近后远还有利于保持坯件或半成品件的刚性,改善其切削条件。(3)先内后外
对有内表面(内型、腔)的零件,在制定其加工方案时,通常应安排先加工内型和内腔,后加工外形表面。这是因为控制内表面的尺寸和形状较困难,刀具刚性相应较差。
(4)刀具集中:即用一把刀加工完相应各部位以后再换另一把刀,以减少换刀时间。2.确定走刀路线确定走刀路线的重点在于确定精加工及空行程的走刀路线。走刀路线包括切削加工的路径及刀具引入、切出等非切削空行程。(1)刀具引入、切出在数控车床上进行精加工时,要安排好刀具尽量沿轮廓的切线方向引入和切出。尤其是车螺纹时,必须设置引入段L1和退刀段L2、这样可避免因车刀升降速而影响螺距.(2)确定最短的空行程路线确定最短的走刀路线,除了依靠大量的实践经验外,还应善于分析与计算。基本思路介绍如下:
3.2切削用量的选择及要领5.2.1车刀的类型及选用数控车削用的车刀一般分为三类:即尖形车刀、圆弧形车刀和成形车刀。1.尖型车刀以直线形切削刃为特征的车刀一般称为尖形车刀。这类车刀的刀尖(同时也为其刀位点)由直线形的主、副切削刃构成,如内、外园车刀,左、右端面车刀,切槽(断)车刀等2.圆弧形车刀圆弧形车刀是较为特殊的数控加工用车刀。其特征是:构成主切削刃的刀刃形状为一圆弧;该圆弧刃每一点都是圆弧形车刀的刀尖,因此,刀位点在圆弧的圆心上。
3.成形车刀成形车刀俗称样板车刀.其加工零件的轮廓形状完全由刀刃的形状和尺寸决定。数控车削加工中,常见的成形车刀有小半径圆弧车刀、非矩形车槽刀和螺纹车刀等。在数控加工中,应尽量少用或不用成形车刀。(没有必要)在数控车削加工中常用尖形车刀,但在加工圆弧面时,若要求较高的光洁度和精度,则应选择圆弧车刀:5.2.3、确定切削用量数控机床加工中的切削用量包括背吃刀量、主轴转速和进给速度。在加工程序的编制工作中,选择好切削用量,使背吃刀量、主轴转速和进给速度三者间能互相适应,以形成最佳切削状态。1.切削深度(背吃刀量aP)的确定
在车床主轴一夹具一刀具一零件这一系统刚性允许的条件下,尽可能选取较大的切削深度,以减少走刀次数。当零件的精度要求较高时,则应考虑适当留出精车余量,其所留精车余量一般比普通车削时所留余量小,常取0.1-0.5mm。
2.主轴转速(切削速度)的确定主轴转速的确定方法,除螺纹加工外,其他与普通车削加工时一样,应根据零件上被加工部位的直径,并按零件和刀具的材料及加工性质等条件所允许的切削速度来确定。在实际生产中,主轴转速可用下式计算:
n=1000v/(πd)式中:n是主轴转速(r/min);v是允许切削速度(m/min),d是零件待加工表面的直径(mm)。在确定主轴转速时,需要首先确定其切削速度,而切削速度又与背吃刀量和进给量有关。3.进给量的确定
进结量是指工件每转一周车刀沿进给方向移动的距离(mm),它与背吃刀量有着较密切的关系。粗车时一般取为0.3一0.8mm/r,精车时常取0.1一0.3mm,切断时宜取0.05一0.2mm/r,具体选择时可参考表3—1进行。5.3数控车床的编程5.3.1数控车床的编程特点
1)数控车床上工件的毛坯大多为圆棒料,加工余量较大,一个表面往往需要进行多次反复的加工。如果对每个加工循环都编写若干个程序段,就会增加编程的工作量。为了简化加工程序,一般情况下,数控车床的数控系统中都有车外圆、车端面和车螺纹等不同形式的循环功能。
2)数控车床的数控系统中都有刀具补偿功能。刀具补偿功能为编程提供方便,编程人员可以按工件的实际轮廓编写加工程序。在加工过程中,对于刀具位置的变化、刀具几何形状的变化及刀尖的圆弧半径的变化,都无需更改加工程序,只要将变化的尺寸或圆弧半径输入到存储器中,刀具便能自动进行补偿。
3)数控车床的编程有直径、半径两种方法。所谓直径编程是指X轴上的有关尺寸为直径值,半径编程是指x轴上的有关尺寸为半径值。常见的车床如CK0630数控车床中的编程均采用直径编程。
4)为了提高机床径向尺寸的加工精度,数控系统在x方向的脉冲当量应取Z方向的脉冲当量的一半。例如,经济型数控车床中,Z轴的脉冲当量为0.01mm/P,X轴的脉冲当量取0.005mm/P。5.3.2数控车床基本编程方法
1.数控车床编程坐标系(工件坐标系)的建立编程坐标系如下图所示:Z轴与机械坐标系的Z轴重合,正方向是远离卡盘的方向;X轴与Z轴相垂直,正方向亦为刀架远离主轴轴线的方向。
车床坐标系与车削加工工件坐标系确定工件坐标系原点位于“O”的两种方法(1)G50X400Z400指定工件坐标系的原点在“O”点
(2a)用OFFSET面板命令将G54的偏差寄存器的值设为X=400;Z=400
(2b)在工件的加工程序里用G54指定工件坐标系的原点在“O”点2.回程序原点指令(
G28X–Z--G29X--Z--)程序的起点就称为程序原点(程序启动刀具初始位置)(有时还称为起刀点),G28命令刀具(具体指刀位点)快速移动,经X与Z指定的中间点到程序原点R点(经中间点绕行的目的是避开可能的障碍)G29命令刀具快速经G28指定的中间点到达G29X—Z—指定的终点G28路线:A-----B-------RG29路线:R---B------C问:G28及G29的作用?3、快速点位定位指令G00G00指令是模态代码,它命令刀具以点定位控制方式从刀具所在点快速运动到下一个目标位置。它只是快速定位,而无运动轨迹要求。其指令书写格式是:G00X(U)——Z(w)——;刀具整个运动轨迹一般不是直线,而是两条线段的组合。例如下图所示:从起点A快速运动到目标点B。走这一条路
4、直线插补指令G01
直线插补指令是直线运动指令。它命令刀具在两坐标间以插补联动方式按F指定的进给速度作直线运动。G01指令是模态(续效)指令。指令格式:G01X(U)——Z(w)—(有时为G1)编程方法:绝对值及相对值编程:(如图4—18所示)选右端面O点为编程原点)6.M功能:M功能也称为辅助功能,它指令机床一些装置的开与关,例如:(1)M00命令程序暂停运转(此期间可以测量工件尺寸是否已合格),重新按程序启动按钮后程序又开始运转。(2)M02程序结束。(不返回程序起点)--整批零件全部加工完毕常用(3)M30程序结束,并且程序指针返回程序起点。--一批零件中的加工一个完毕再准备下一个常用(4)M03/M04/M05命令主轴正转/反转/停转(5)M08/M09命令切削液泵开启/停转7、锥的切削(用G01实现)
(1)车锥原理:在车床上车外圆锥时可以分为车正锥(左大右小)和车倒锥两种情况,而每一种情况又有两种加工路线(3刀成型)。图3-29所示为车正锥的两种加工路线,按图a的加工路线车正锥时,需要计算终刀距S。假设圆锥大径为D,小径为d,锥长为L,背吃刀量为aP
,则由相似三角形可得:当按图b的走刀路线车正锥时,则不需要计算终刀距S,只要确定了背吃刀量aP即可车出圆锥轮廓。但在每次切削中,背吃刀量是变化的。图3-30为车倒锥(右大左小)的两种加工路线,车锥原理与正锥相同。记住:车正锥与车倒锥采用的刀具不同(用右偏车刀车倒锥)(2)车锥编程实例已知毛坯为Φ30mm的棒料,3号刀为外园刀,试车削成如图3-31所示的正锥。解:确定分三次走刀,前两次背吃刀量αp=2mm,最后一次背吃刀量αp=1mm。按第一种车锥路线进行加工,终刀距具体程序如下:8、圆弧插补指令G02/G03圆弧插补指令命令刀具在指定平面内按给定的F进给速度作圆弧运动,并切削出轮廓。圆弧插补指令分为顺时针圆弧插补指令G02和逆时针圆弧插补指令G03。
数控车床是两坐标的机床,只有X轴和Z袖,观察者让Y轴的正向指向天空,站在这样的位置上就可正确判断X--Z平面上圆弧的顺逆了。G02/G03指令的格式:在车床上加工圆弧时,不仅要用G02/G03指出圆弧的顺逆时针方向,用X(U),Z(w)指定圆弧的终点坐标,而且还要指定圆弧的中心位置。常用指定圆心位置的方式有两种,因而G02/G03的指令格式有两种:
1)用I、K指定圆心位置:I、K是圆弧中心与圆弧起点的X方向差值与Z方向的差值R是整个圆弧的半径值,比较精确
9、固定循环固定循环是预先给定一系列操作,用来控制机床位移或主轴运转,从而完成各项加工。对独刀完成的轮廓表面加工,即加工余量较大的表面,采用循环编程可以缩短程序的长度。固定循环一般分为单一形状固定循环和复合形状固定循环。各类数控系统固定循环的形式和使用方法(主要是编程方法)相差甚大。这里主要介绍常用的FANAC系统的固定循环。(1)单—表面的固定循环(简单固定循环)G77G79该循环主要用于圆柱面和圆锥面的循环切制。1)外园柱/外圆锥切削循环(可能要多刀成型)指令格式:G77X(U)一Z(w)一—F—G77X(U)一Z(w)一I—F—
刀具从循环起点开始按矩形循环,最后又回到循环起点。图中虚线表示按R快速运动,实线表示按F指定的工作进给速度运动。x、Z为圆柱面切削终点坐标值;U、W为圆柱面切削终点相对循环起点的增量值,其加工顺序按1、2、3、4进行。2)编程举例:如图:如下图所示,I为锥体大小端的半径差。在编程时应注意I的符号.确定的方法是:锥面起点坐标大于终点坐标时为正(一般是倒锥),反之为负(一般是正锥)。
2)编程举例:加工如下图所示的工件,其有关程序如下:O3)端面固定循环G79G79X(U)Z(W)F
它适用于圆柱棒料毛坯端面方向粗车,刀具从循环起点开始按矩形循环,最后又回到循环起点。图中虚线表示按R快速运动,实线表示按F指定的工作进给速度运动。x、Z为端面切削终点坐标值;U、W为端面切削终点相对循环起点的增量值,其加工顺序按1、2、3、4进行。N1G79U100.W50.F0.3注意:动作3的执行距离较短,大概是小于5mm,故该指令仅适用于车端面(一刀成型)问:G77与G79的区别何在?(2)轮廓切削固定循环G71、G72、G73、G70(复杂固定循环)程序格式:G71P(ns)Q(nf)U(Δu)W(ΔW)D(Δd)F(f)S(s)T(t)式中:ns——循环程序中第一个程序段(句)的顺序号;nf——循环程序中最后一个程序段(句)的顺序号;
Δu——径向(x轴方向)的精车余量(直径值);
Δw——轴向(z轴方向)的精车余量;
Δd——每次吃刀深度(沿垂直轴线方向)例如加工下图零件的程序:主轴正转应用举例:图3-39为采用G7l园粗车循环与G70精车循环的例子。毛坯为Φ140mm的棒材,刀具从P0的开始后走到C点,进行粗车循环,每次粗车循环的背吃刀量为7mm,径向与横向加工余量为2mmN01
温馨提示
- 1. 本站所有资源如无特殊说明,都需要本地电脑安装OFFICE2007和PDF阅读器。图纸软件为CAD,CAXA,PROE,UG,SolidWorks等.压缩文件请下载最新的WinRAR软件解压。
- 2. 本站的文档不包含任何第三方提供的附件图纸等,如果需要附件,请联系上传者。文件的所有权益归上传用户所有。
- 3. 本站RAR压缩包中若带图纸,网页内容里面会有图纸预览,若没有图纸预览就没有图纸。
- 4. 未经权益所有人同意不得将文件中的内容挪作商业或盈利用途。
- 5. 人人文库网仅提供信息存储空间,仅对用户上传内容的表现方式做保护处理,对用户上传分享的文档内容本身不做任何修改或编辑,并不能对任何下载内容负责。
- 6. 下载文件中如有侵权或不适当内容,请与我们联系,我们立即纠正。
- 7. 本站不保证下载资源的准确性、安全性和完整性, 同时也不承担用户因使用这些下载资源对自己和他人造成任何形式的伤害或损失。
最新文档
- 2025年度租赁合同解除条件补充协议范文
- 二零二五年度电工安全检查与整改合同
- 2025年全球及中国微流控免疫测试分析仪行业头部企业市场占有率及排名调研报告
- 施工日志填写样本施工过程中的问题与解决方案
- 科技发展与学科教育的互促关系研究
- 科技教育编程教育的普及与推广
- DB4453T 30-2025广藿香组培苗生产技术规程
- DB35T 2232-2024海峡两岸共通 火龙果生产技术规程
- 东莞企业劳动合同范本
- 个人贷款房屋抵押合同模板大全
- 音乐教学集训课程设计
- 山东省潍坊市2024-2025学年高三上学期期末 地理试题(含答案)
- 肺切除手术的术前评估课件
- 招聘专职人员报名表
- 《大学生创新与创业》课件
- 护士的护理职业生涯规划
- 2024年高考语文复习:古诗文阅读强化练习题汇编(含答案解析)
- 不良反应事件及严重不良事件处理的标准操作规程药物临床试验机构GCP SOP
- 劳动合同(模版)4篇
- 义务教育数学课程标准(2022年版)重点
- 2021上海春考作文题解析及范文(怎样做与成为什么样人)
评论
0/150
提交评论