
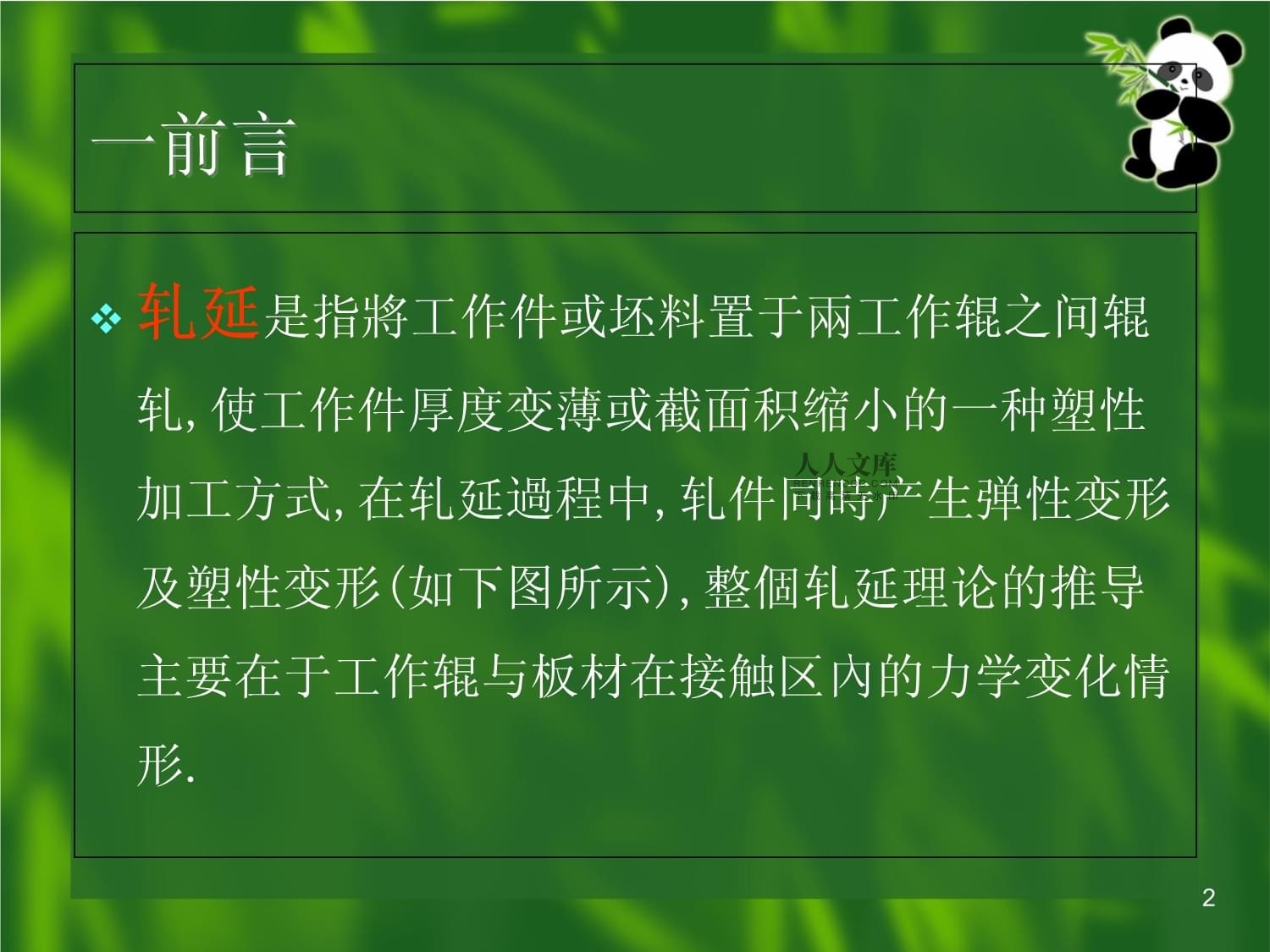



版权说明:本文档由用户提供并上传,收益归属内容提供方,若内容存在侵权,请进行举报或认领
文档简介
轧延理论基本介绍轧延理论基本介绍1一前言轧延是指將工作件或坯料置于兩工作辊之间辊轧,使工作件厚度变薄或截面积缩小的一种塑性加工方式,在轧延過程中,轧件同時产生弹性变形及塑性变形(如下图所示),整個轧延理论的推导主要在于工作辊与板材在接触区內的力学变化情形.一前言轧延是指將工作件或坯料置于兩工作辊之间辊轧,使工作件厚2二.基本概述板材在兩辊间轧延示意图
D/2v1h1出口弹性变形區接触弧長
入口弹性变形區
塑性变形區
咬入角v0h2中性点二.基本概述板材在兩辊间轧延示意图D/2v1h1出口弹性3
压下率指轧延加工量之厚度压下率,其定义為:
r=△h/h2=((h2-h1)/h2)*100%。 r称为压下率
。△h称为压下量
。压下率指轧延加工量之厚度压下率,其定义為:4咬入角和接触弧长
咬入角:板材与工作辊接触的塑性变形区域內,入料端以及出料端与工作出料端所涵盖的角度
咬入角Ø=2*(h2-h1)/D如何才能实现正常咬入?接触弧長:工作辊与板材所接触的圆弧長度接触弧長L=Ø*(D/2)咬入角和接触弧长
咬入角:板材与工作辊接触的塑性变5中性點
在塑性变形區內,板材因厚度減少导致長度增加,會造成材料在軋延方向速度的增加,所以在軋延中,入口速度v0會小於v1,而在轧辊与板材接触区域內,存在有一個板材与轧辊转速相等的點,称之为中立点前滑值:
S=[(V1-Vr)/Vr]*100%后滑值中性點
在塑性变形區內,板材因厚度減少导致長度增加6
影响前滑的因素
宽展1)摩擦系数u越大,其前滑值越大2)前张力增加时,则使金属的向前流动的阻力减少,从而增加前滑区,使前滑增加,反之后张力增加时,则后滑区增加.3)轧件厚度H减小,前滑增加,反之减小.轧制过程中,沿横向移动的体积引起的轧件宽度上的的变化叫宽展.
影响前滑的因素
宽展1)摩擦系数u7轧制力
轧制力:轧机將板材由一截面积,经辊轧后減至另一較小的截面积時,對板材所施加之力,主要是包括轧辊与板材間磨擦力与板材塑性变形之抵抗力
主要因素:材料的变形抵抗力压下率張力作用轧机的刚性
工作辊辊径磨擦阻力轧制力
轧制力:轧机將板材由一截面积,经辊轧后減至另8轧延压力分布图
材料塑性变形阻力分布图摩擦力分布图摩擦力峰值中立点轧延压力分布图材料塑性变形阻力分布图摩擦力分布图摩擦力峰值9
根据A.J.Zelikow所推导出之轧延力公式可清楚了解影响轧延力与各项因素之間的关系
P=(△h*B*σ/2μ)*(exp(2*L/△h)-1)
△h:压下量
B:板宽σ
:变形应力μ
:磨擦系数L:接触弧長
根据A.J.Zelikow所推导出之轧延力公式可清楚了解影10
1)材料塑性之变形阻力(应力-应变图)应力ρ
降伏點Yp
伸長率(%)
1)材料塑性之变形阻力(应力-应变图)应力ρ降伏點Yp11
2)轧下率
BR1R2R3
OL1L2L3轧辊压力P
接触弧長
D
C
A
其中:R压下率2)轧下率
BO123)工辊辊径
图2-7不同辊径對轧延负荷之影响
D1D2D3其中D为工辊辊径轧辊负荷P
轧下率%3)工辊辊径图2-7不同辊径對轧延负荷之影响D1134)
摩擦阻力接触弧長
轧辊压力P
中立点移动轨跡
μ3
μ2
μ1
軋延压力分布受磨擦系数影响其中:μ3>μ2>μ1
4)摩擦阻力接触弧長轧辊压力P中立点移动轨跡μ3μ145)张力作用轧延负荷P后张前张张力增加接触弧长ABCDEN3N1N2KJIHGONMLO1O2O35)张力作用轧延负荷P后张前张张力增加接触弧长156)軋机的剛性影響:
轧延荷重P轧辊间隙变化量剛性大
剛性小
图2-12轧机的刚性大小与轧辊间隙变化量关系轧机的刚性定义如下:
轧机刚性=施加于轧机的力/轧机的变形量
刚性的大小会影响轧辊间隙的变化量6)軋机的剛性影響:
轧延荷重P轧辊间隙变化量剛性大16OperatorsideDrivesideOperatorsideDriveside边波OS边波中波边波Figure34边波DS中波¼波三板形控制
OperatorsideDrivesideOperato17钢板在宽度方向不同伸長量示意图
L+△L
L钢板在宽度方向不同伸長量示意图L+△LL18
弯曲力
弯曲力19
中间辊移动板材
有效平面
板
宽
中间辊移动板材20四AGC(AUTOGAUGECONTROL)控制系統簡介:
轧延板材厚度改变的原理有以下的关系式:板厚=轧机的弹性变形+轧辊设定位置所以板厚的改变有两种方式:
1.改变轧辊的设定位置(screwdown下压量)2.改变轧延荷重(tensioncontrol)改变轧延荷重的主要方法是改变張力值,其中以后張力的影响较大,其厚度的变化量与轧延荷重的关系式为:△h1=△P/K四AGC(AUTOGAUGECONTROL)控制系21X-RAY测厚仪简介
X-RAY测厚计量测原理主要是,当钢板置于放射源与侦测器之间时,放射源穿透钢板后,其强度會衰減,而侦测器则依所侦测之不同强度转换为相对不同的钢板厚度,其转换的关系式如下: T=(1/μ)㏑(I0/I) T:钢板厚度。
μ:线性吸收系數。
I0:放射源強度(T=0時)。
I:放射源穿透钢板后,由侦测器所测得之强度。X-RAY测厚仪简介X-RAY测厚计量测原理主要是22如图所示DetectorVoltage钢板厚度T
Source X-RAY测厚原理示意图如图所示DetectorVoltage钢板厚度TS231150带钢常见事故处理办法飞剪带铁头
轧机之间起套堆钢来料弯大,阴阳面造成跑偏堆钢
甩尾拉丝
AGC伺服故障
钻出口刮水板、轧线标高调整不当,造成翘、叩头
压下实际值与设定值不符、二级头部设定超厚
中间坯头部超宽主传动跳闸,轧机停车工作辊有大块掉肉,造成轧制力增加
下表面划伤工作辊表面有裂纹侧导板与活套耐磨板螺丝脱落轧机辊缝未调平,跑偏堆钢粗轧轧机辊缝偏差太大侧导板自动回缩粗轧来料未进精轧精轧工作辊断辊支撑辊断辊
1150带钢常见事故处理办法飞剪带铁头24一、飞剪带铁头事故原因带头,带尾不能侧底切断,而带入到立辊或进出口导卫内,下块带钢在进钢时,将其带入轧机进行轧制,造成废钢及断辊等重大事故。由于飞剪未切头,导致无法进钢,产生中间废。热检(HMD)检测不准,飞剪提前动作。处理办法操作员,发现这种情况后,并联系上道工序停轧。联系相关岗位,进行确认。准备好钩子将铁头吊出。电气,调整查出故障进行处理。对飞剪上下剪刃进行检查,确保剪刃无裂纹,无缺口。观察中间坯来料板形,头尾弯度是否超出剪刀宽度,如有立即对中间坯板形进行调整。预防措施提高飞剪的命中率,保证能切到头部。带钢跟踪系统正常维护。定期对飞剪进行检查,制定飞剪更换制度。定期对中间坯进行测量,保证来料板形正常。在轧制过程中,操作人员应注意,每块带钢的剪切情况,发现带铁头的现象应立既停车。一、飞剪带铁头25事故原因轧机之间秒流量不等造成堆钢。轧制时活套故障,造成轧机之间起套。测压头故障。侧导板开口度设定不到位,造成废钢。带钢叩、翘头引起堆钢。操作调整不当,引起一侧跑偏。处理办法操作人员应在手动干预无效时,立即按急停。将急停复位,并将冷却水停掉。第一时间,现场观察堆钢及轧辊情况。如有条件,台下人员马上指挥,台上操作人员,将立辊反转,飞剪辊道及所有输送辊道反转。采用下将F1工作辊平衡,靠工作辊辍重压住钢板然后手动点动轧机拉出,如有必要时将上支撑辊下将处理完事故必须进行零调。如钢板拉不出时,要在轧机上进行切割,必须通知台上确认好,自己位置插上安全销。将不规则处,头部和拱起部分切割掉,用行车将其吊走,然后与台上联系,将剩余的废钢倒出。预防措施操作人员应精心操作,对活套要注意观察,发现有异常情况,应及时干预。加强轧制前的确认。准确观察钢板在轧机内的状态,及时参与调整。修正数据,确保微张力运行正常,正确修定参数。二、轧机之间起套堆钢二、轧机之间起套堆钢26三、来料弯大,阴阳面造成跑偏堆钢事故原因停轧时间过长,开轧后来料,阴阳面大,精轧穿带单边浪大,跑偏严重,拍急停。来料弯大,带钢头部跑偏撞护板。由于粗轧来料,头部偏,而精轧未做相应调整,就进行轧制,造成精轧前段机架卡钢。处理办法1、同轧机之间起套堆钢一样。预防措施停轧时间过长,要对带钢穿带时的跑偏预见性。精心操作,时刻观察料型变化情况,提高调整判断能力。精轧必须保证板形平直,轧制厚度均匀。三、来料弯大,阴阳面造成跑偏堆钢事故原因27四、甩尾事故原因:轧辊未调平。尾部温度过低。轧件宽度方向,温度分布不均。精轧侧导板,对中不良。抛钢速度不当。来料质量不良。处理办法1、用工具或天车将废钢取出。预防措施精心操作不断提高。保证设备精度。保证精轧来料温度。四、甩尾事故原因:28五、拉丝故障原因:钢带边部与侧导板磨擦造成拉丝压入钢带下表面与辊道、活套辊造成划痕细丝压入前后机架侧导板不对中造成边部刮侧导板磨损严重的侧导板未及时更换处理方法:对侧导板磨损严重的及时更换保证设备运转正常预防措施:操作工精心操作轧钢工勤检查,勤更换侧导板。保证设备精度。五、拉丝故障原因:29六、AGC伺服故障事故原因1、伺服故障,造成误动作,由于活套调节范围,超限造成堆钢处理办法操作人员,应在手动干预无效时,立即按急停。将急停复位,并将冷却水停掉。待伺服阀处理好后,将B(A)阀切换A(B)阀锁定复位。辊缝能够打开方可处理卡钢,以下同轧机之间起套堆钢处理方法是一样的。预防措施更换伺服阀,由工作阀导向备用阀。六、AGC伺服故障事故原因30七、钻出口刮水板、轧线标高调整不当,造成翘、叩头故障原因在穿带过程中带钢头部叩头顶在出口下切水板与护板的交接处,造成带钢堆在下切水板里,将下切水板挤坏。由于下工作辊上表面与轧制线的高度调整不当,造成翘、叩头。挡水板与辊之间间隙大。处理方法同“轧机之间起套堆钢”处理方法。机械处理气缸和下护板。预防措施精心操作轧辊车间应在更换支撑辊的时,根据支撑辊辊径和将要使用的工作辊辊径范围确定合适的垫板厚度。超出轧制线标高的工作辊不要下送。导卫工常更换磨损严重的挡水板。七、钻出口刮水板、轧线标高调整不当,造成翘、叩头故障原因31八、压下实际值与设定值不符、二级头部设定超厚事故原因AGC压下造成某机架轧制力大,电流急剧增加,速度也急剧下降,造成机架之间堆钢。主要原因是人工设定辊缝不合理,形成速降,造成堆钢。压下位置没有到设定的位置,会造成机架内堆钢或拉断。处理方法发现有这种情况应将块钢倒出重新设定。当带钢咬入后出现这种情况后压下和速度操作工应及时手动干预使此块带钢能顺利轧制过去。操作人员应在手动干预无效时立即按急停。同“轧机之间起落套堆钢”处理方法一样。通知设备电气人员进行处理。预防措施操作人员在每次进钢前,必须确认画面上设定值和实际值,另外对设备重点跟踪,查找故障原因。计算机二级设定要正常。八、压下实际值与设定值不符、二级头部设定超厚32九、中间坯头部超宽事故原因中间坯头部超宽处理方法咬入的钢,操作人员应在手动干预无效时立即按急停。同“轧机之间起套堆钢”外理方法预防措施粗轧因根据测宽仪上显示的宽度对立辊进行调整。对于轧制极限规格必须严格执行工艺纪律,要将温度控制范围缩小为±20°C。九、中间坯头部超宽事故原因33十、主传动跳闸,轧机停车事故原因由于电气的原因而造成主传动跳闸。由于主传动的负荷过大而造成跳闸停车。处理方法机架间如果有钢,可利用立辊反转将钢板拉出。如果对工作辊没有影响的,则在处理完了废钢以后通知电气合主传动,然后精轧操作人员在画面上复位,合主传动;对工作辊有影响的话,精轧需要在处理完废钢后,换辊。预防措施保证精轧的轧制温度,不轧低温钢。加强点检。加强设备的维护,防止主传动运行故障。十、主传动跳闸,轧机停车事故原因34十一、工作辊有大块掉肉,造成轧制力增加故障原因在轧制过程中,轧辊掉肉后,使轧制力增加,使速度下降,从而造成轧机间堆钢。轧辊材质有缺陷。水嘴局部堵塞、冷却水不均。卡钢时含钢使轧辊内部有裂纹。处理方法同“轧机间起套堆钢”处理方法一样。更换工作辊。预防措施卡钢后必须抽辊检查,确认轧辊状态。轧辊上机前要做好超声波探伤。轧辊冷却水必须均匀。十一、工作辊有大块掉肉,造成轧制力增加故障原因35十二、下表面划伤故障原因对中辊道和除磷辊道有死辊。辊道护板高于辊面。活套辊不转。输出辊道上有死辊。处理方法首先操作人员必须按标准化作业。开机前必须认真检查中间辊道、活套辊和输出辊道的运转情况,发现有不转的和护板高于辊面的现象立即请设备人员处理。预防措施杜绝死辊。辊道、表面、护板高度严格的执行有关技术规程。十二、下表面划伤故障原因36十三、带钢表面铬印故障原因穿带时头部轧破、轧制时中间轧破、抛钢时甩尾,造成辊面铬伤。板坯结疤,异物,造成精轧铬印。处理方法发生轧破时,质检开卷,确认带钢质量。如计划不允许,必须停机。甩尾后机架内的碎片必须清除。轧线发现铬印要立刻停轧,检查轧辊质量,轻微的可用角磨机进行打磨,如严重的必须换辊,确保产品质量。预防措施加强设备维护和电气系统修正。轧制计划严格按规程编制。发现甩尾后及时检查处理。操作工不断提高操作水平。轧制时观察带钢表面及走势。上料时要处理原料缺陷。十三、带钢表面铬印故障原因37十四、工作辊表面有裂纹故障原因轧辊的本身材质原因引起。轧辊冷却水控制不好,在急停拍下时未停水。处理方法更换工作辊预防措施轧辊出现卡钢换辊后要填好轧辊使用清单,下机后严格检查。严格按规定探伤、磨削,把好新辊的质量关。操作人员加强轧辊上机检查。十四、工作辊表面有裂纹故障原因38
十五、侧导板与活套耐磨板螺丝脱落故障原因侧导板活套耐磨板螺丝没锁紧。过钢中由于抖动较大,螺丝松动,螺头冒出。处理方法同机架间堆钢处理方法一样。通知机械,导卫人员到现场更换螺丝。预防措施轧钢工要勤检查。发现问题停机处理。十五、侧导板与活套耐磨板螺丝脱落故障原因39十六、轧机辊缝未调平,跑偏堆钢故障原因零调后辊缝未调平。调整工穿铝板时,辊缝未进行修正。严格按照换辊操作规程进行换辊。处理方法同轧机机架堆钢处理办法一样。预防措施严格按照换辊操作规程进行各项操作。穿铝板时,使用千分尺读数要准确,依据实际来料厚薄差进行辊缝修正。操作工要精心操作,做到眼疾手快,反应灵敏,相互配合。十六、轧机辊缝未调平,跑偏堆钢故障原因40十七、粗轧轧机辊缝偏差太大故障原因粗轧压下自动位移。液压平衡压力过大或失效。万向接首夹紧缸没有打开。零调标定数据与实际数据不准确。发现此问题立既停轧。处理方法如有钢在输送辊道上,立既通知精轧,启动紧急改规格程序。及时通知机电进行检查。预防措施操作工精心操作,发现问题及时通知二级,电气,机械人员。二级对此类事故进行监控,对磁尺的位移等现象要及时发现,迅速处理。操作工要勤检查,交接班时要严格执行交接班制度,要对电脑数据进行核对,对轧辊实际辊缝进行测量。十七、粗轧轧机辊缝偏差太大故障原因41十八、侧导板自动回缩故障原因设定侧导板开口度与实际开口度有偏差。侧导板自动回缩。处理方法发现有此类现象,立既停止过钢,及时与电工,液压工、二级人员进行联系。轧钢工与操作工重新做侧导板标定。做好标定后通知液压人员关闭球阀。预防措施保证设备精度操作工勤检查十八、侧导板自动回缩故障原因42十九、粗轧来料未进精轧故障原因粗轧来料五道翘头过大,切头后未进立辊。粗轧来料镰刀弯过大,顶在立辊前导卫护板。大剪辊道和粗轧辊道不转。精轧立辊不转。处理方法大剪操作工,加大切头长度,尽量将翘头部分多切。如切完后还进不了,迅速将来料倒出进行第二次切头。粗轧操作工要时刻关注,来料的板形状况,根据实际情况进行辊缝较正。大剪操作工要精心操作,发现辊道不转要立既打电话通知机械,电气进行处理。操作工要精心操作,杜绝立辊未启动的现象。预防措施操作工精心操作。发现问题及时通知相关人员进行处理。加强巡检制度。十九、粗轧来料未进精轧故障原因43二十、精轧工作辊断辊故障原因轧黑印钢、由于本块钢的温度变化大造成工作辊断;多层进钢造成工作辊断;工作辊本身的材质有问题,在轧制过程中断辊。负荷分配不合理造成工作辊断辊;板坯有结疤造成工作辊断没有轧辊冷却水处理方法上工作辊断辊。按正常换辊方法将下工作辊点动抽出并使销头对正,将上工作辊平衡落下,用下辊将上辊带出机架,然后将上工作辊断辊拉出、吊走。清理机架间杂物,抽支撑检查辊面,必要时更
温馨提示
- 1. 本站所有资源如无特殊说明,都需要本地电脑安装OFFICE2007和PDF阅读器。图纸软件为CAD,CAXA,PROE,UG,SolidWorks等.压缩文件请下载最新的WinRAR软件解压。
- 2. 本站的文档不包含任何第三方提供的附件图纸等,如果需要附件,请联系上传者。文件的所有权益归上传用户所有。
- 3. 本站RAR压缩包中若带图纸,网页内容里面会有图纸预览,若没有图纸预览就没有图纸。
- 4. 未经权益所有人同意不得将文件中的内容挪作商业或盈利用途。
- 5. 人人文库网仅提供信息存储空间,仅对用户上传内容的表现方式做保护处理,对用户上传分享的文档内容本身不做任何修改或编辑,并不能对任何下载内容负责。
- 6. 下载文件中如有侵权或不适当内容,请与我们联系,我们立即纠正。
- 7. 本站不保证下载资源的准确性、安全性和完整性, 同时也不承担用户因使用这些下载资源对自己和他人造成任何形式的伤害或损失。
最新文档
- 2024年秋新教科版八年级上册物理教学课件 第4章 光的世界 3 平面镜成像
- 2024年秋新冀少版生物七年级上册课件 第一章 细胞 1.1.1 显微镜的使用
- 述职报告部队士官炊事员(14篇)
- 万威客食品有限公司-如何提高员工执行力
- 物流信息管理第七章 不同行业物流信息系统分析
- 部编版一年级语文上册分类检测卷课文内容填空(全优考卷新编)
- 2023年RS跑车项目需求分析报告
- 2023年水利设施开发管理服务项目评估分析报告
- 美团七夕节营销策略全案
- 技术开发合同的范本
- 常见古英语单词对照
- 初中数学思想方法篇——数形结合
- 蚕病防治专题11湖南课件
- 四年级语文上册分层作业设计
- 全书配套课件:C语言程序设计案例教程 王明福
- 第二十届上海青少年科技创新大赛优秀科技论文和创造发明获奖一
- 无人值守变电站及监控中心技术导则
- 人教版九年级物理全册教案
- 医院MDT建设方案设计
- 2020年《地舒单抗在骨质疏松症中临床合理用药中国专家建议》解读(全文)
- 一年级10以内加减法口算题(100道题_可直接打印)
评论
0/150
提交评论