


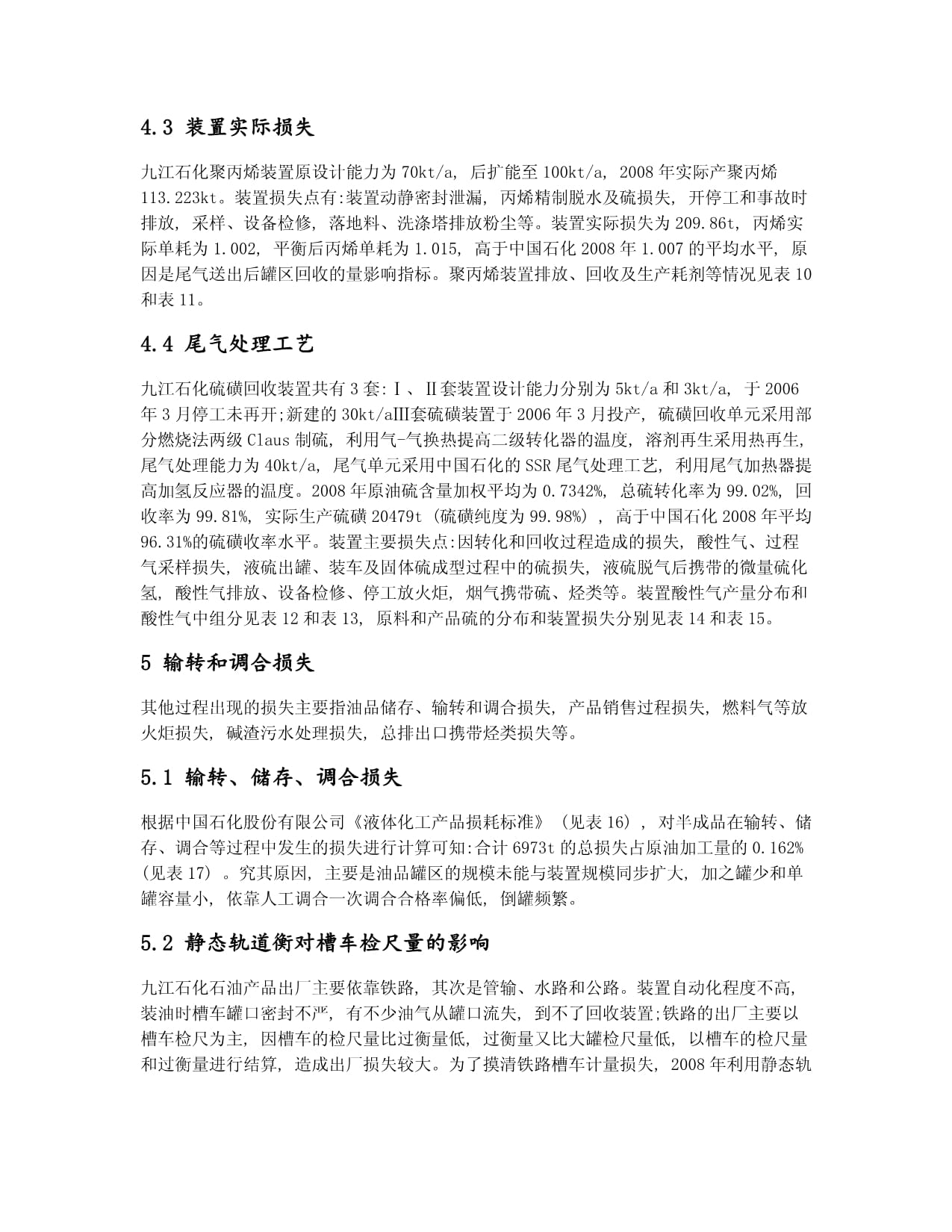

下载本文档
版权说明:本文档由用户提供并上传,收益归属内容提供方,若内容存在侵权,请进行举报或认领
文档简介
2008年江浙石化加工损失分析
1综合损失的现状原油综合损失是指油厂、储备厂、生产加工、成品存储、销售和安装过程中发生的全部损失。九江石化由于储存能力的制约,半成品和成品在同一罐中交替出现,因此,综合损失只能分为原(料)油途耗、储耗和加工损失两大块。加工损失除包括装置生产过程中出现的损失外,还包含产成品储存输转损失、出厂损失及新装置开工系统存油等。九江石化2008年加工损失达38388t,占原油加工量4312.1kt的0.89%,超出中国石化总部下达的0.8%的指标。2污水含盐量统计一次加工损失主要是指常减压蒸馏装置在生产过程中所发生的损失,其主要损失点有:电脱盐部分切水带油和含盐、三顶回流罐含硫污水带油和三顶气放火炬、电精制碱渣带油和沉积、静动密封点泄露以及设备检修、采样漏油等。因九江石化5.0Mt/aⅠ套常减压装置2008年初实施节能改造,至2008年3月中旬才开工,1.5Mt/aⅡ套常减压装置运行到2008年3月下旬就停运,2套装置采取接力式生产,所以分析损失时一并考虑。2008年原油脱盐前、后含水和含盐年平均值见表1,原油电脱盐工艺流程如图1所示。由表1、图1可知:因电脱盐和破乳剂的效果不理想(与原油品质也有关),电脱盐未达到脱后含盐量不大于3mg/L、切水含油量不大于150mg/L的控制指标,且切水含油还需经隔油罐沉降后才合格。2008年,在电脱盐注水量为324.12kt的情况下,有316.12kt水作为污水被切掉,电脱盐罐带出的油为113.329t,其中35.728t污油进入排水装置再回收,77.6t作为污油送罐区后进行回炼,回炼既增加加工消耗又增加输转损失。2008年“三顶”(初馏塔顶、常压塔顶、减压塔顶)污水含油标定分析数据见表2。九江石化2008年的实际原(料)油加工量为4312.1kt,有17132.8t水和20.67t盐带入后续工艺,有152.792t盐随含盐污水排放而损失掉。在17132.8t水中,平均有22.753t污油进入催化污水汽提原料罐进行隔油并定期(不小于半年)回收。三顶气相部分放火炬线已关,阀门也进行铅封,不凝气全部由轻烃压缩机送催化装置进行回收。装置加热炉自用燃料油和燃料气,在增加计量措施和加大管理力度后,生产量和自用量分别计量,物料的损失和能源的消耗不相混淆。按此实际情况统计,装置损失共计953.47t,是加工量的0.022%;平衡后,Ⅰ套常减压损失率为0.24%(含改造后装置系统藏油量)、Ⅱ套常减压损失率为0.19%,高于2008年中国石化0.13%的平均水平。3二次加工损失及分析二次加工损失主要是指催化裂化、延迟焦化、催化重整、芳烃抽提、汽柴油加氢、溶剂脱沥青等装置在生产过程中所发生的损失。3.1污水含硫、氮、污九江石化催化裂化装置由1.2Mt/a的蜡油加渣油催化裂化和1.0Mt/a的重油催化裂化组成,其主要损失点有:平衡催化剂带出的金属和碳,再生烟气中含的硫、氮,污水中含烃类、硫化物、氨氮,装置与低压瓦斯系统相连的安全阀、调节阀、放空阀、放火炬阀、机泵密封泄漏,开停工或事故状态下气压机入口放火炬等。根据分析数据和计量统计数据(见表3)可得出损失量(见表4)。Ⅰ、Ⅱ套催化裂化装置实际损失率分别为0.15%和0.13%,平衡后损失率分别为0.43%和0.49%,高于中国石化2008年0.35%的平均水平。3.2罐外排水损失九江石化1.0Mt/a延迟焦化装置主要损失点有:分馏塔、稳定塔顶回流罐外送的含硫污水携带油和硫,冷焦水罐和切焦水罐清罐焦损失,冷焦切焦排出的气体损失,飞溅的焦粉,放空沉降分离罐外排水携带油、设备泄漏和炉管烧焦等。由分析数据和计量统计数据(见表5)可得出损失量(见表6)。该装置实际损失率为0.11%,平衡后损失率为0.29%,好于中国石化2008年0.34%的平均水平。3.3装置实际运行损失九江石化催化重整、芳烃抽提、汽油加氢精制、汽柴油加氢精制等4套装置由一个生产车间进行管理。催化重整装置由原来1.5Mt/a扩能至目前的3.0Mt/a,但仍为固定床半再生式工艺,有4个反应器,重整催化剂按1∶1.5∶2.5∶5的比例装填,主要生产高辛烷值汽油和为芳烃抽提装置提供原料。预处理部分为全馏分加氢,采用氢气一次通过流程;重整部分采用二段混氢技术。2008年装置实际处理量为289.2kt。催化重整装置主要损失点有:预加氢催化剂和重整催化剂积炭1.8t,回流罐脱水含油、含硫、含氨共计3.14t,氢气压缩机入口分液罐脱液含油1.72t,与火炬线相连部位内漏(包括安全阀轻微内漏)和设备检修、泄漏损失共87t,脱氯剂和脱硫剂吸附损失共0.76t,因工艺原因排去低压瓦斯管网的443.8t中按20%计算未能回收的损失88.76t,热载体蒸发12.43t,生产波动放火炬56.98t,装置停工开工损失238t,装置总排水量81420t(携带油82mg/L)合6.68t。2008年共计损失497.27t,实际损失率为0.17%,平衡后损失率为0.62%,高于中国石化2008年0.48%的平均水平。芳烃装置为100kt/a的环丁砜抽提装置,产品为三苯两剂(苯、甲苯、混二甲苯、6号和120号溶剂油)。2008年实际处理量为109.063kt。其损失点主要有:精制混合芳烃的白土和溶剂油催化剂吸附造成的损失,回流罐脱水含油,精馏三塔回流罐排大气,设备检修、泄漏、采样等,装置开停工等。总损失实际为1172.4t,损失率为1.08%,平衡后损失率为1.99%,高于中国石化2008年0.66%的平均水平。汽油加氢装置由柴油加氢精制装置改造而来,2008年实际处理量为266.995kt;汽柴油加氢装置2008年实际处理量为1194.520kt。2套精制装置主要损失点有:原料、产品和回流罐脱水及外送含硫污水含油、含硫、含氨氮,汽油加氢回流罐因高压瓦斯系统压力高塔顶气体(190m3.4合成氨装置开工九江石化溶剂脱沥青装置是2005年从天津石化整体搬迁而来,设计负荷为500kt/a,2008年实际处理量为400.710kt,装置开工情况与合成氨装置生产有关。装置主要损失点有:容器切水含油、含硫,溶剂挥发和排低压瓦斯,直供化肥的脱油沥青和去调合沥青罐量的偏差,设备检修、介质泄漏、采样等。溶剂脱沥青装置损失实际为987t,损失率为0.25%,平衡后损失率为0.43%,高于中国石化2008年0.21%的平均水平。4三大公共故障分析三次加工损失主要是指气体分馏、MTBE、聚丙烯、硫磺回收等装置在生产过程中所发生的损失。4.1装置实际运行损失九江石化气体分馏装置共有2套,Ⅰ套气分由原120kt/a处理量扩能至150kt/a,2008年实际处理量为129.001kt;Ⅱ套气分由原160kt/a扩能至300kt/a,2008年实际处理量为260.502kt。两套装置主要损失点有:原料中携带的水,丙烯预精制脱水含油和硫,装置动静密封泄漏,正常条件下与低压瓦斯管网相连的各塔容器管线阀门泄漏或排放(见表8),装置开工充油及置换时损失,采样、设备检修等。根据计量和统计,装置损失实际分别为317.7和499.3t,损失率分别为0.25%和0.19%,平衡后损失率分别为1.38%和1.18%,高于中国石化2008年0.56%的平均水平。平衡后损失大于实际损失,原因主要是液化气、丙烷公路装车过程排放量较大造成的损失和出厂损失都回到了装置的加工损失中。从统计监督对比数据看,2008年1~3月,液化气对比损失每月在70t以上,丙烷损失每月在20t以上。通过实施改进措施和加强考核管理,以及重新设计操作流程、对放压线进行铅封、对装车条件进行调整、制定补装条件和要求等,至2008年底基本解决了装车损失问题。4.2装置停工及运行情况九江石化MTBE装置设计产能20kt/a,2008年实际生产量为17.745kt。装置的损失点主要有:装置动静密封泄漏,正常条件下与低压瓦斯管网相连的各塔容器管线阀门、机泵密封的泄漏或排放,更换催化剂,装置开工充油及置换、设备检修等,停工碳四排空与脱水携带甲醇,甲醇进装置量与实际量偏差(见表9)。MTBE装置实际损失为184.67t,损失率为0.20%,平衡后损失率为1.10%,高于中国石化2008年0.53%的平均水平。4.3装置实际损失九江石化聚丙烯装置原设计能力为70kt/a,后扩能至100kt/a,2008年实际产聚丙烯113.223kt。装置损失点有:装置动静密封泄漏,丙烯精制脱水及硫损失,开停工和事故时排放,采样、设备检修,落地料、洗涤塔排放粉尘等。装置实际损失为209.86t,丙烯实际单耗为1.002,平衡后丙烯单耗为1.015,高于中国石化2008年1.007的平均水平,原因是尾气送出后罐区回收的量影响指标。聚丙烯装置排放、回收及生产耗剂等情况见表10和表11。4.4尾气处理工艺九江石化硫磺回收装置共有3套:Ⅰ、Ⅱ套装置设计能力分别为5kt/a和3kt/a,于2006年3月停工未再开;新建的30kt/aⅢ套硫磺装置于2006年3月投产,硫磺回收单元采用部分燃烧法两级Claus制硫,利用气-气换热提高二级转化器的温度,溶剂再生采用热再生,尾气处理能力为40kt/a,尾气单元采用中国石化的SSR尾气处理工艺,利用尾气加热器提高加氢反应器的温度。2008年原油硫含量加权平均为0.7342%,总硫转化率为99.02%,回收率为99.81%,实际生产硫磺20479t(硫磺纯度为99.98%),高于中国石化2008年平均96.31%的硫磺收率水平。装置主要损失点:因转化和回收过程造成的损失,酸性气、过程气采样损失,液硫出罐、装车及固体硫成型过程中的硫损失,液硫脱气后携带的微量硫化氢,酸性气排放、设备检修、停工放火炬,烟气携带硫、烃类等。装置酸性气产量分布和酸性气中组分见表12和表13,原料和产品硫的分布和装置损失分别见表14和表15。5输转和调合损失其他过程出现的损失主要指油品储存、输转和调合损失,产品销售过程损失,燃料气等放火炬损失,碱渣污水处理损失,总排出口携带烃类损失等。5.1输转、储存、调合损失根据中国石化股份有限公司《液体化工产品损耗标准》(见表16),对半成品在输转、储存、调合等过程中发生的损失进行计算可知:合计6973t的总损失占原油加工量的0.162%(见表17)。究其原因,主要是油品罐区的规模未能与装置规模同步扩大,加之罐少和单罐容量小,依靠人工调合一次调合合格率偏低,倒罐频繁。5.2静态轨道衡对槽车检尺量的影响九江石化石油产品出厂主要依靠铁路,其次是管输、水路和公路。装置自动化程度不高,装油时槽车罐口密封不严,有不少油气从罐口流失,到不了回收装置;铁路的出厂主要以槽车检尺为主,因槽车的检尺量比过衡量低,过衡量又比大罐检尺量低,以槽车的检尺量和过衡量进行结算,造成出厂损失较大。为了摸清铁路槽车计量损失,2008年利用静态轨道衡对槽车计量情况进行了对比,发现槽车检尺量比铁路静态轨道衡偏低0.32%(见表18)。2008年铁路出厂量1525.8kt,铁路出厂实际损失为3552t。水路和管输实际出厂1480.76kt,装船和管输损失只有80t。目前公路液化气出厂采用地磅计量交接方式,2008年第二季度开始加强了对液化气装车出厂的监控和降损管理,月出厂损失由原来的100t左右下降至目前的5t左右,年损失量共计398t。2008年产品出厂总损失量为4030t,出厂损失率为0.13%。5.3座火炬的长明灯都消灭火炬点九江石化低压瓦斯系统设有1座5000m火炬:炼油配备2座、化肥1座,各有4根能自动点火的长明灯,正常情况下炼油2座火炬的长明灯都熄灭,化肥火炬点1个长明灯。由于气柜小,压缩机排量低,系统缓冲和回收能力不足,瓦斯受天气变化及装置操作波动等因素影响较大,阶段性不平衡,造成2008年火炬冲破水封累计时间为416h,化肥火炬持续点1个长明灯,年瓦斯损失估算为7620t,占原油加工量的0.18%,比瓦斯理论损失占原油加工量的0.04%大很多。5.4烃损失、烃损失九江石化2008年常线碱渣和混合碱渣合计硫、烃损失400t;炼油污水约3600kt,二级气浮出水COD约700mg/L,折合烃损失约735t,共计损失1135t。5.5减轻排水回收压力由于环保需要和企业效益要求,各装
温馨提示
- 1. 本站所有资源如无特殊说明,都需要本地电脑安装OFFICE2007和PDF阅读器。图纸软件为CAD,CAXA,PROE,UG,SolidWorks等.压缩文件请下载最新的WinRAR软件解压。
- 2. 本站的文档不包含任何第三方提供的附件图纸等,如果需要附件,请联系上传者。文件的所有权益归上传用户所有。
- 3. 本站RAR压缩包中若带图纸,网页内容里面会有图纸预览,若没有图纸预览就没有图纸。
- 4. 未经权益所有人同意不得将文件中的内容挪作商业或盈利用途。
- 5. 人人文库网仅提供信息存储空间,仅对用户上传内容的表现方式做保护处理,对用户上传分享的文档内容本身不做任何修改或编辑,并不能对任何下载内容负责。
- 6. 下载文件中如有侵权或不适当内容,请与我们联系,我们立即纠正。
- 7. 本站不保证下载资源的准确性、安全性和完整性, 同时也不承担用户因使用这些下载资源对自己和他人造成任何形式的伤害或损失。
最新文档
- 欠薪投诉活动方案
- 水上公园新年活动方案
- 沂蒙山女神节活动方案
- 毕业周年庆活动方案
- 毕业国风活动方案
- 江西军营联谊活动方案
- 水上救援大练兵活动方案
- 正月下单优惠活动方案
- 民俗村公关活动策划方案
- 气球开业活动方案
- 中国净菜行业市场深度研究及发展趋势预测报告
- 糖尿病饮食治疗讲课件
- 输液反应急救护理流程讲课件
- 钢结构仓库施工组织设计
- 变电站电气设备管理制度
- 中国农田水利行业发展前景及发展策略与投资风险研究报告2025-2028版
- 50篇短文搞定高考英语3500单词
- 物业消防检查培训课件
- 专题 完形填空 七年级英语下册期末复习考点培优专项北师大版(2024版)(含答案解析)
- 余料使用管理制度
- 2025至2030年中国彩涂铝材行业市场动态分析及发展趋向研判报告
评论
0/150
提交评论