
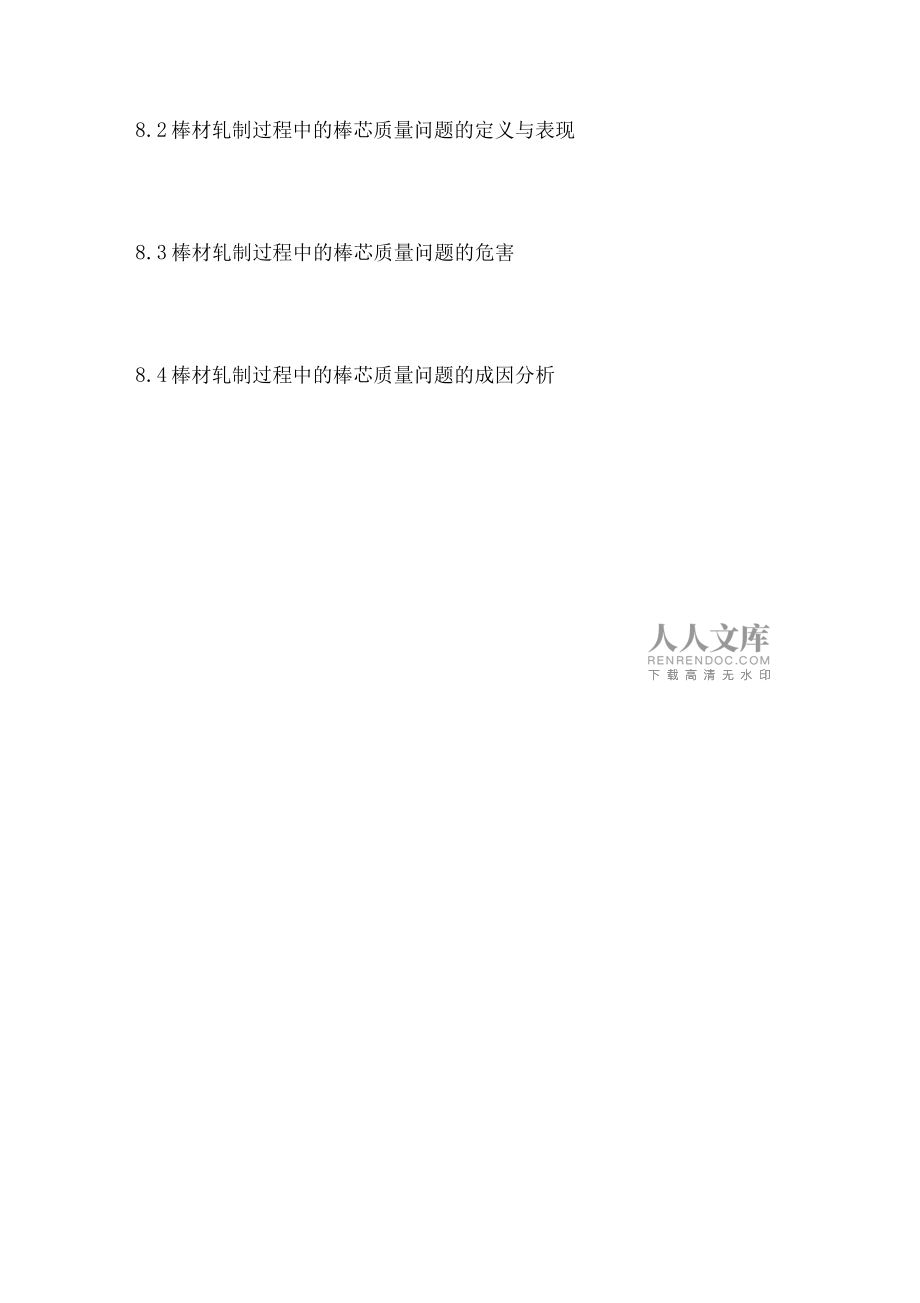



下载本文档
版权说明:本文档由用户提供并上传,收益归属内容提供方,若内容存在侵权,请进行举报或认领
文档简介
1、8 棒材轧制过程中的棒芯质量问题与控制技术8.1 概述棒材在国民经济发展中起着重要的作用, 它广泛地应用于建筑、 冶金、 机械、电力、 煤炭等行业, 其中以机械行业居多。 棒材轧制属于高温大变形塑性成形过程, 存在温度一变形一微观组织演变强耦合效应。 制定合理的轧制规程需要进行轧件金属变形机理和产品质量控制研究。生产实践表明棒材芯部孔隙性缺陷是影响大棒材轧制质量的主要原因之一,对此许多专家学者开展了大量的研究工作, 研究人员针对浇铸工艺、 钢坯成分及质量、 轧制孔型等做了大量有价值的研究。 另有专家学者采用有限元仿真技术对轧制过程进行动态仿真,准确地计算、分析、校核了轧件的应力场、温度场和轧制
2、力、 轧制力矩等重要参数的分布值以此对轧辊强度、 孔型尺寸及相关的轧制工艺参数进行分析、校核、修正和改进,取得了很有参考价值的结果。本文针对棒材轧制过程中芯部存在孔隙性缺陷问题, 建立三维有限元数值模型,分析棒材轧制过程中的工艺参数(压下量、摩擦系数、温度、轧制速度等)对棒材芯部质量的影响, 利用模拟结果可以获得优化的轧制工艺参数。 本文阐述了棒芯质量问题的危害, 分析了影响棒芯质量的成因, 建立了改进棒芯质量的实验模型, 并初步提出了控制棒芯质量的加工工艺路线, 为提高棒材芯部质量及棒材的工艺改进提供依据。8.2 棒材轧制过程中的棒芯质量问题的定义与表现8.3 棒材轧制过程中的棒芯质量问题的
3、危害8.4 棒材轧制过程中的棒芯质量问题的成因分析为分析轧制工艺各因素对棒材芯部质量的影响,本文采用三维造型软件/E建立几何模型,再导入DEFORM3D的前处理器中建立三维轧制有限元模型Pro8.4.1 材料的选用本研究采用石钢常用钢种42CrMO,对应DEFORM3D材料库中钢号为AISI-4140。42CrMO的化学成分如表4-1所示。表4-1 42CrMO的化学成分钢种CSiMnPSCrMo42CrMO0.420.280.610.0160.0111.110.28.4.2 有限元模型建立(1)轧辗模型:定义为刚性主动辗,直径为 700 mm的平辗。(2)轧件:棒材轧制过程中,轧件处于高温状
4、态,道次变形量大,弹性变 形相对很小可忽略,因此,在建模时可以认为轧件服从多孔可压缩刚塑性材料模 型,棒材轧制属于对称轧制,取轧件 1/4建立几何模型。为单独分析每个因素对棒材芯部质量影响,设轧件各物理量仅沿Y方向变化,沿X方向认为各量一致,侧边自由。(a)正视图(b)三维视图棒材轧制三维轧制模型如图4-1所示。(c)三维轧制视图图4-1三维有限元轧制模型8.4.3 模拟结果分析(1)压下量对芯部质量的影响压下量(绝对、相对压下量)是轧制工艺中最常用的调节措施,其对棒材芯 部质量影响可以通过有限元法模拟给出,利用模拟得到的棒材中心到表面相对密 度变化情况,可以分析不同工艺对棒材芯部的压实效果,
5、 从而为提高棒材芯部质 量,改进工艺提供指导。为研究总压下量、道次压下量对棒材芯部压实作用的效果, 分别模拟了总压 下量一定,道次压下量不同(轧制总道次不同)和单道次轧制,不同道次压下量 对芯部质量的影响,具体压下量分配如表 4-2。表4-2压下量分配顺序号道次数相对压卜量(相对原始坯料尺寸)1110%2120%3130%4140%545%5%5%25%645%5%25%5%745%25%5%5%8425%5%5%5%9410%10%10%10%1)单道次轧制,不同道次压下量为分析压下量对棒材芯部孔隙性缺陷压合的影响,采用一道次轧制,压下量为 36 mm (10%) , 72 mm (20%)
6、 , 108 mm (30%) , 144 mm (40%)时, 分别对轧制过程进行模拟。棒材中心到表面沿压下方向和宽展方向(图 1中-y 和z方向)的模拟结果如图4-2、图4-3所示。(a)压下方向y轴(b)宽展方向x轴*VM 堡图4-2同压下量时,棒材横断面相对密度分布图4-2中结果为y, z轴处的相对密度结果,0, 10% , 20%, 30% , 40%分别代表压下量的百分比。为比较不同厚度坯料内部的压实效果,图 4-2中横坐标 为棒材中心到表面的相对距离。9590A立M事营甲由缶本雄0.85 r1J0 to 203040图4-3棒材中心相对密度随压下量变化由图4-2、图4-3可以看出
7、,单道次轧制,压下量不同时,压下量越大,芯 部密度提高越多,孔隙性缺陷的压合效果越好。棒材中心相对密度随压下量(10%40%)呈线性增加,但即使压下量达到40%,棒材中心相对密度也仅从初始的0.85提高到0.93,没能达到1.00。尽管压下量不同,压下方向(y轴方向)、宽展方向(z轴方向)相对密度 在棒材内部分布曲线类似,都分为比较明显的4个部分(见图4-2) o棒材中心到表面相对长度 00.2范围,压下量一定时,相对密度从棒材 中心到表面方向提升平缓,压下方向芯部相对密度略低,宽展方向芯部相对密度 略高;随压下量增加相对密度提升量增加。从棒材中心到表面相对长度0.200.45范围(初始相对密
8、度变化分界面左 右),相对密度从棒材中心到表面方向提升较快;相对密度提升随压下量增大而 增大;但是当棒材中心到表面相对长度约为0.45时,相对密度趋于一致(约为棒材初始表层相对密度),压下方向该处的相对密度仅随压下量增加略有增加, 宽展方向该处的相对密度基本不变。这是因为该处初始相对密度较大,提升空间 小,且轧制作用对此处相对密度改善效果也较小。从棒材中心到表面相对长度 0.45 mm-0.80 mm范围,在宽展方向,相对密 度基本不变;在压下方向,相对密度从初始表层密度增加到1。从棒材中心到表面相对长度0.81.0范围,在宽展方向,相对密度基本不 变;在压下方向,相对密度为1,即使压下量较小
9、(10%)时,棒材表面附近孔 隙性缺陷也能基本压合,说明轧制变形对轧制表面附近压合效果很好。值得一提白是,图2 (b)中,小压下量(10%)对应的轧制工艺,宽展方向 棒材芯部相对密度在相对长度为 0.20.4时,略低于轧制前棒材坯料的相对密度。这是因为小压下量轧制,金属变形主要集中在材料表面,棒材芯部金属变形 很小,对芯部相对密度影响很小,而宽展方向棒材几何尺寸有所增加, 且两侧的 棒材表层部分金属厚度变化很小,棒材芯部相对密度较低部分所占比例在横断面 内增加,高密度与低密度交界区向表层方向移动造成的,而不是该区域处材料相对密度降低,出现更多的孔隙性缺陷。2)总压下量和总道次一定,不同道次压下
10、量总压下量为144 cm (总的相对压下量为40%),采用四道次轧制工艺进行 轧制,具体压下量分配见表4-2,模拟中不考虑坯料温度的变化,设坯料温度为 1050C,棒材芯部损伤及密度情况见图 4-4。(a)总压下量一定时,压下方向四遒次轧制末道次密度对比41 BUhct(b)总压下量一定时,宽展方向四道次轧制末道次密度对比图4-4四道次轧制模拟结果由图4-3和图4-4可以看出:5-5-5-25工艺(各道次压下量分别为相对原始 尺寸的5%、5%、5%、25%)对芯部改善最大。其次是5-25-5-5和25-5-5-5的, 并且这两种工艺和5-5-5-25相差并不是太大,而10-10-10-10(简
11、记为10 M)的芯部 损伤最大,密度最小;但实际轧制工艺中的第一道次咬入条件的限制,25-5-5-5工艺不可取,因此5-5-5-25或5-25-5-5工艺对芯部质量改善相对较好。结合单道此轧制结果,单从压下量考虑,加大道次压下量并将大压下量放存 末道次或前儿道次(第一道次除外)产品芯部质量的改善是较为理想的,因此在 制定轧制规程时,建议增大第二道次或末道次的压下量。3)单纯压下和轧制对芯部质量的影响对比为了分析轧制条件下辗子的前后滑动对棒材芯部质量的影响,假设温度、坯料等条件不变,对坯料分别进行压下和轧制模拟, 具体模拟结果如图8。图中ny 表示相对压下量为n%时单纯的锻压;nz表示相对压下量
12、为n%时的轧制,其中 n=10,,40。由图8可以看出,压下量相同时,锻压比轧制对芯部的压实效果好, 并且损 伤小;随着压下量的增加,两种工艺的差值也随之变大,因此可见轧制时金属的 前后滑动对提高棒材芯部的质量是不利的。4道次轧制未道次对比小)相时况离(a) 4道次轧制压下方向末道次损伤对比相时跑离(b) 4道次轧制压下方向末道次密度对比图4-5 4道次轧制在总压下量一定时末道模拟结果对比多道次轧制,总压下量一定时,棒材心部孔隙性缺陷的压合效果不仅与道次相对压下量的最大值有关,而且还与相对压下量的最大值所在道次出现的次序有 关,通过分析棒材芯部压合效果与压下量之间的关系,可以看出:相对压下量的
13、最大值越大,棒材心部压合效果越好。当相对压下量的最大值相差不大时,相对压下量的最大值所在道次出现的 次序对棒材芯部压合效果有明显的影响,相对压下量的最大值所在道次出现的次 序越靠前,压合效果越好。这是由于小压下量轧制时,高密度表层金属变薄,影 响后继道次对芯部的压合效果,比较明显的是上述四道次5-5-25 -5工艺。小压下量轧制不利于棒材芯部压合。(2)摩擦对棒材芯部质量的影响在钢塑性有限元中,如何正确的确定接触表面上的摩擦, 将直接影响到各计 算结果的准确性。模拟采用剪切摩擦形式,为确定合理的摩擦系数,在恒温度(1050C),相对压下量为30%时,轧辗转速恒定的条件下,通过改变摩擦系 数进行
14、模拟研究。具体的仿真结果见图 4-6所示。 4。6(a)宽展方向不同摩擦系数时损伤对比-4k (teQ 9(L2a* o.e(b)宽展方向不同摩擦系数时密度对比(c)压下方向不同摩擦系数时损伤对比0,瓯 ''*00.2。40$IdlRturr(d)压下方向不同摩擦系数时密度对比图4-6摩擦对棒材质量影响由仿真结果可以看出,棒材芯部宽展和压下方向上棒材芯部相对密度随摩擦 系数的增加而增大,其中当摩擦系数为 0.9时,密度最大,因此粗轧道次应加大 摩擦系数来改善芯部质量,建议采用增加摩擦系数。(3)轧制温度对芯部质量的影响棒材原始温度1100C,控制棒材表面温度,使棒材表面温度分别
15、为 1050、 1000、950C ,采用72 mm的压下量对其进行轧制模拟。模拟结果见图 4-7、图 4-8。由于棒材芯部孔性缺陷呈弥散分布,具体位置、形状具有一定的随机性。所以才用相对密度来表征芯部质量的好坏,相对密度越高芯部质量越好。I O + 、 o o O据零x«0.04口,950匕1000 匕 - 1OS0T0 1 0 2 03 0.4 0.5 0.6 0.7 0.8 0 9 1.0相对距离一 = - O 00H90M LO.O.O.期曲版弹图4-7压下量为72 mm时不同温度下的密度对比010.40.6 Q8 1.0相时距离图4-8压下量为72 mm时不同温度下压下方向
16、上的损伤对比由图4-7和图4-8的仿真结果可以看出,在棒材轧制初始阶段。其他条件不 变,改变棒材表面温度棒材芯部和外层的相对密度、损伤都会发生相应的变化。1)棒材芯部(从棒材中心到表面相对长度 00.4范围)相对密度随表面温 度的降低而增大;芯部损伤随表面温度的降低而减小。芯部相对密度大、损伤小代表棒材芯部孔隙性缺陷压合比较好,棒材的质量比较好。2)棒材外层(从棒材中心到表面相对长度 0.41范围)棒材的相对密度随 表面温度的增大而增大。棒材损伤程度随棒材表面温度的增大而减小。随轧制温 度升高金属变形阻力减小。当轧件表面温度高于芯部温度时,轧件表面的金属变 形量最大,芯部变形很小。因此降低棒材
17、表面温度有利于轧制力向芯部渗透,有利于棒材芯部孔隙性缺陷的压合,减少棒材芯部损伤。提高棒材质量。(4)轧制速度对芯部质量的影响轧制速度对棒材轧制的咬人、芯部压实效果等影响很大。为分析轧制速度对棒材芯部质量的影响,现设压下量相同,轧制温度相同。分别采用不同的轧制速 度来模拟轧制速度的影响,具体模拟结果见图4-9和图4-10。模拟结果:当轧辗角速度为04 0.45、0.5 rad/s时,棒材芯部密度是最大, 且芯部相对密度相差不大,并以角速度为 0.5 rad/s左右时为最大值;从损伤角 度看,轧辗角速度为0.7 rad/s时,芯部损伤最小,其次是0.4-0.5 rad/s,并且 此范闱内损伤相差
18、不大。因此综合考虑棒材芯部损伤和相对密度,当轧辗角速度在0.5 rad/s左右时,棒材芯部质量改善最为理想。00.2014dlAtmce0.85图4-9不同轧制I速度时压下方向上损伤对比disuncc图4-10不同轧制速度时压下方向上密度对比棒材质量的优劣主要参考芯部相对密度的大小,芯部相对密度越大表征棒材 的质量越好。所以在棒材轧制工艺中,在保证轧制设备、主电机功率和轧制成品 终轧温度允许的情况下应降低棒材表面温度,即采用降温轧制工艺。棒材芯部表面温度梯度越大,越有利于轧制力向芯部渗透,越有利于芯部缺陷的改善.同时 降温轧制可以降低轧制工艺的能源消耗,有利于钢铁工业的节能环保。理论计算 在生
19、产设备、产品终轧温度允许范围内将棒材的加热温度从1000c降到950C,可使整个轧制工生产线节省6.58%的能源消耗。8.5棒材轧制过程中的棒芯质量问题的控制技术在石钢连轧工序粗轧段采用的实际工艺基础上进行相应调整,实验性模拟模 型来分析调节措施的可行性。对于具体的棒材产品,其总压下量是一定的,因此要通过优化其他工艺参数 来提高棒材的芯部质量,而工艺参数的优化包括:1)加工条件参数的优化:在加工的过程中降低棒材表面温度,尽量保持轧辗角速度在0.40.5 rad/s范围内。2)加工过程中参数的优化:通过重新分配道次压下量来改善芯部孔隙性缺 陷的压合效果。而第2种优化方式是最理想而且是最有效的方式
20、。根据前面的分 析:当孔型一定时,随道次压下量的增大,轧件中应力趋于稳定,即大压下量对 芯部质量改善比较明显,因此在总压下量基本不变的情况下。采用调整道次压下 量的方法,通过使个别道次相对压下量提高来改善棒材芯部质量。根据生产实践,棒材芯部压实作用主要是在粗轧段完成的,所以应围绕增加粗轧断道次压下量来 进行工艺调整。经过分析,可通过通过表 4-3所示两种改进工艺对原设计工艺进 行优化。表4-3轧制工艺工艺序号孔型代码设计(n150)改进1 (150)改进 2 ( X150)1101V9089.589.52102H6059593103V6057574104H2015.616.65105V1513.515可以看出,各工艺采用的轧辗孔型一样,而区别就在于辗缝的大小,也就是各道次压下量不同。工艺道次绝对压下量见表 4-4。表4-4 3种工艺下粗轧各道次绝对压下量对比工艺序号12345n15069.2874.262.260.437.4x15069.8875.263.465.834.415069.887
温馨提示
- 1. 本站所有资源如无特殊说明,都需要本地电脑安装OFFICE2007和PDF阅读器。图纸软件为CAD,CAXA,PROE,UG,SolidWorks等.压缩文件请下载最新的WinRAR软件解压。
- 2. 本站的文档不包含任何第三方提供的附件图纸等,如果需要附件,请联系上传者。文件的所有权益归上传用户所有。
- 3. 本站RAR压缩包中若带图纸,网页内容里面会有图纸预览,若没有图纸预览就没有图纸。
- 4. 未经权益所有人同意不得将文件中的内容挪作商业或盈利用途。
- 5. 人人文库网仅提供信息存储空间,仅对用户上传内容的表现方式做保护处理,对用户上传分享的文档内容本身不做任何修改或编辑,并不能对任何下载内容负责。
- 6. 下载文件中如有侵权或不适当内容,请与我们联系,我们立即纠正。
- 7. 本站不保证下载资源的准确性、安全性和完整性, 同时也不承担用户因使用这些下载资源对自己和他人造成任何形式的伤害或损失。
最新文档
- 商业银行金融科技人才普惠金融能力培养策略报告2025
- 2025年公众参与视角下环境影响评价公众满意度调查报告
- 电梯委托监督检验协议书
- 江苏国际货运代理协议书
- 珠宝厂出租转让合同范本
- 电梯井道施工安全协议书
- 防火隔热服采购合同范本
- 混凝土合同三方协议模板
- 领取小区大门钥匙协议书
- 私人仓库房屋租赁协议书
- 人教版(2024)第三单元-汉语拼音《yw》教学课件
- 初中语文九级上册第三单元大单元整体教学设计 人教版
- 2024年便携式储能行业分析报告
- 2023年全国职业院校技能大赛-中药传统技能赛项规程
- 滦州事业单位笔试真题及答案2024
- 了解DSA-200型受电弓结构及作用讲解
- 煤矿开掘技术操作规程
- 《光伏组件功率衰减检验技术规范(征求意见稿)》
- 威图电柜空调SK3304500使用说书
- 客运驾驶员汛期安全培训
- 2023年湖北宜昌高新区社区专职工作人员(网格员)招聘考试真题及答案
评论
0/150
提交评论