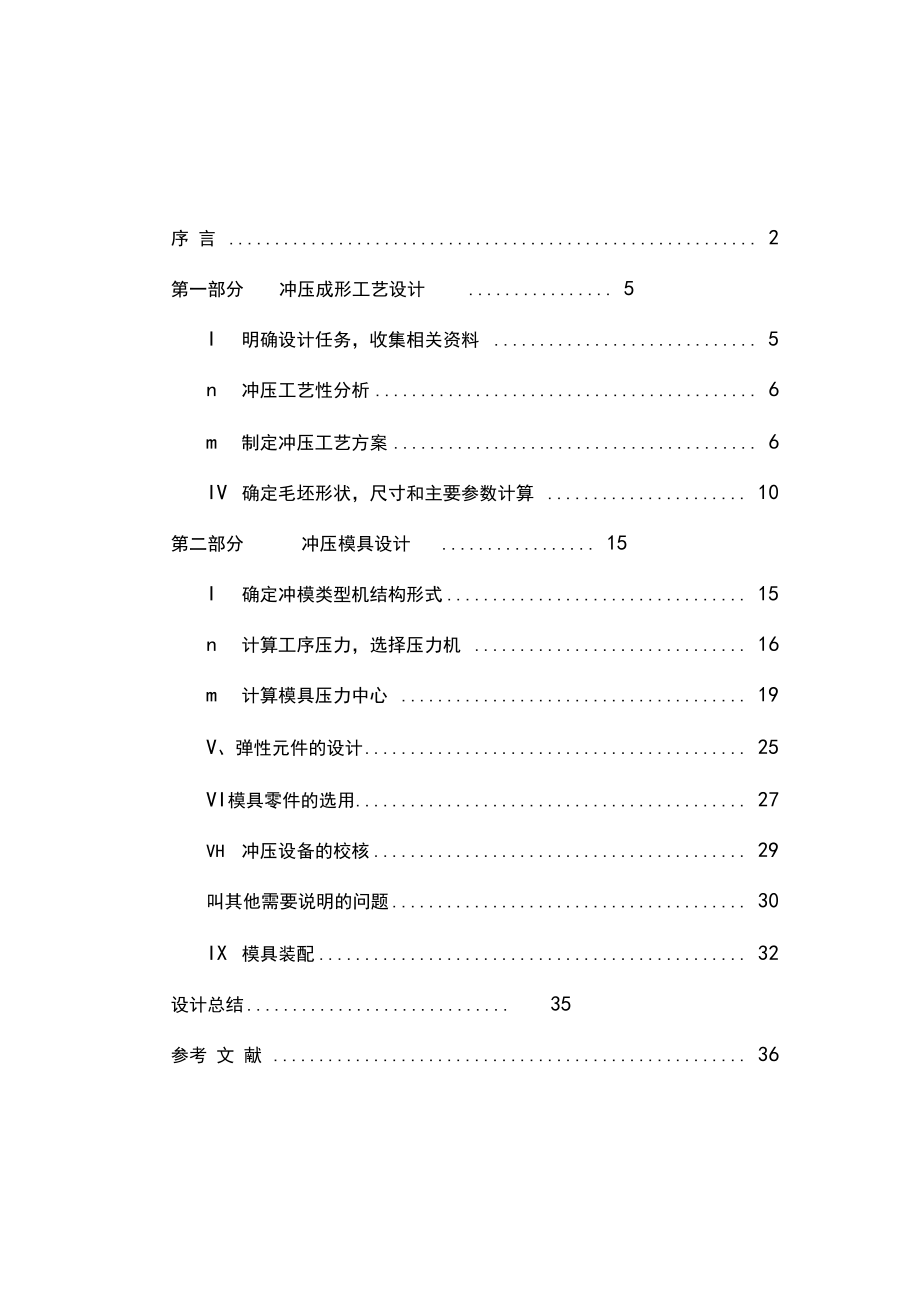
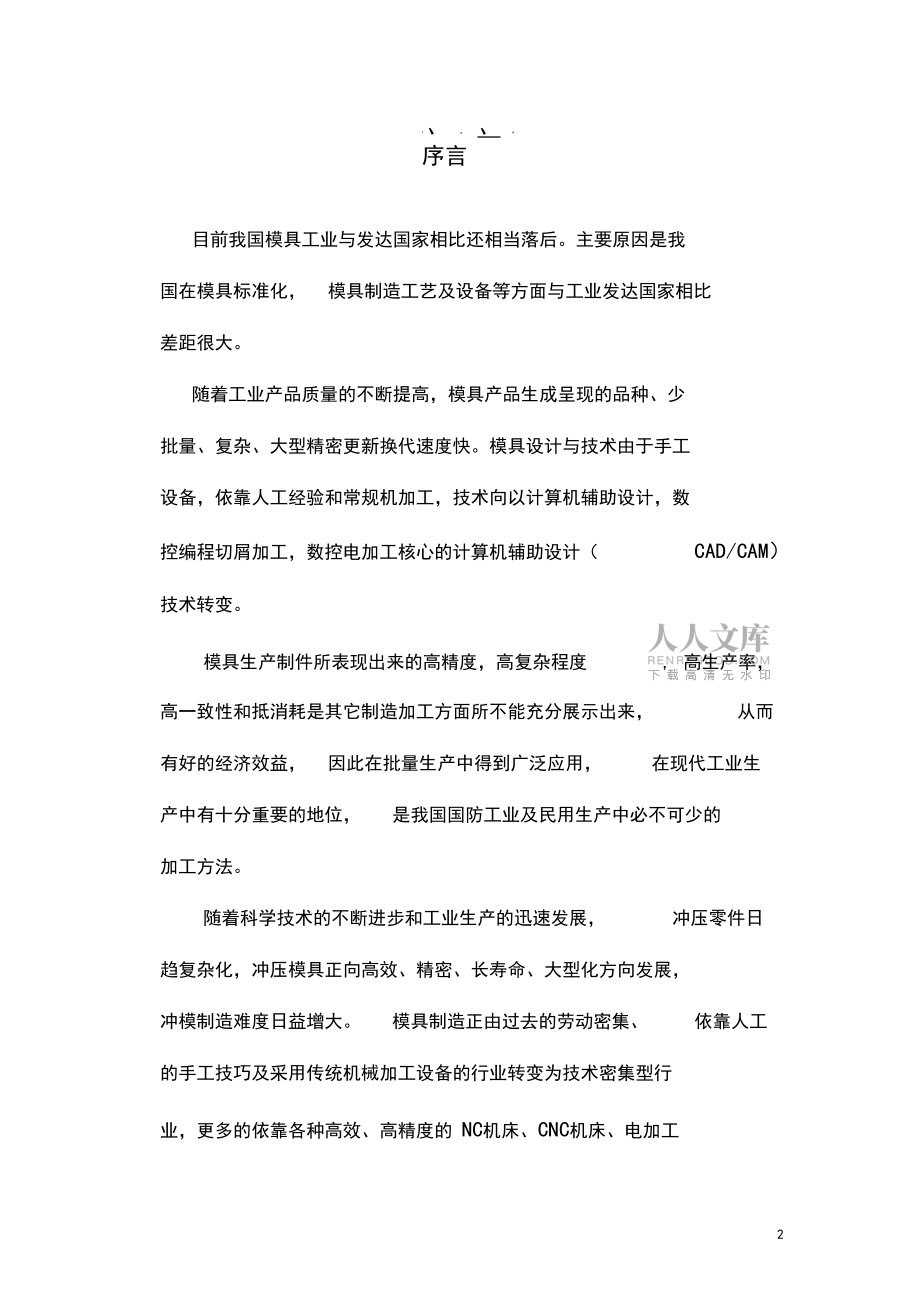



下载本文档
版权说明:本文档由用户提供并上传,收益归属内容提供方,若内容存在侵权,请进行举报或认领
文档简介
1、序 言 2第一部分冲压成形工艺设计 5I明确设计任务,收集相关资料 5n冲压工艺性分析 6m制定冲压工艺方案 6IV确定毛坯形状,尺寸和主要参数计算 10第二部分冲压模具设计 15I确定冲模类型机结构形式 15n计算工序压力,选择压力机 16m计算模具压力中心 19V、弹性元件的设计 25VI模具零件的选用 27VH冲压设备的校核 29叫其他需要说明的问题 30IX模具装配 32设计总结 35参考 文 献 361 、 a、 4序言目前我国模具工业与发达国家相比还相当落后。主要原因是我国在模具标准化,模具制造工艺及设备等方面与工业发达国家相比差距很大。随着工业产品质量的不断提高,模具产品生成呈现
2、的品种、少批量、复杂、大型精密更新换代速度快。模具设计与技术由于手工设备,依靠人工经验和常规机加工,技术向以计算机辅助设计,数控编程切屑加工,数控电加工核心的计算机辅助设计(CAD/CAM)技术转变。模具生产制件所表现出来的高精度,高复杂程度, 高生产率,高一致性和抵消耗是其它制造加工方面所不能充分展示出来,从而有好的经济效益,因此在批量生产中得到广泛应用,在现代工业生产中有十分重要的地位,是我国国防工业及民用生产中必不可少的加工方法。随着科学技术的不断进步和工业生产的迅速发展,冲压零件日趋复杂化,冲压模具正向高效、精密、长寿命、大型化方向发展,冲模制造难度日益增大。模具制造正由过去的劳动密集
3、、依靠人工的手工技巧及采用传统机械加工设备的行业转变为技术密集型行业,更多的依靠各种高效、高精度的 NC机床、CNC机床、电加工机床, 从过去的单一的机械加工时代转变成机械加工、电加工以及其他特种加工相结合的时代。模具制造技术,已经发展成为技术密集型的综合加工技术。本专业以培养学生从事模具设计与制造工作能力的核心,将模具成型加工原理、设备、工艺、模具设计与制造有机结合在一起,实现理论与实际相结合,突出实用性,综合性,先进性。正确掌握并运用冲压工艺参数和模具工作部分的几何形状和尺寸的综合应用,以提高我的模具设计与制造能力的综合应用。在以后的生产中,研究和推广新工艺,新技术。提高模具在生产生活中的
4、应用,并进一步提高模具设计水平。9陕西航空职业技术学院冲压工艺与模具设计机械工程系 飞机制造技术专业 学生姓名:郭峰亮 学号 0721432一 设计题目 筒形件落料,拉深,冲孔,复合模二设计内容要求材料:08厚度:t=2mm硬度:60 64HRCLoh3。一 0指导教师刘宝成2009 年10月第一部分冲压成形工艺设计明确设计任务,收集相关资料冲压工艺设计应在收集、调查、研究并掌握有关设计设计的原始资料的基础上的基础上进行,做到有的放矢,避免盲目性。工艺设计的原始资料主要包括如下内容:冲压件的产品图及技术要求零件图如设计任务书中所示的零件图。技术条件应明确合理。由此可对拉深件的结构,尺寸大小,精
5、度要求以及装配关系,实用性能等有全面了解,以便制定工艺方案,选择模具类型和确定模具精度。生产类型生产类型是企业生产产业程度的分类,一般分为大量生产、成批生产、 、小批量生产。根据生产纲领和产品零件的特征或工作的每月担负的工序数查文献表 1-3 生产类型和生产纲领的关系,确定该零件的生产类型为大批量生产。生产组织形式生产类型不相同,零件和产品的组织形式,采用的技术措施和达到的技术经济效果会不同。因为该零件是大批量生产,所以其生产类型查文献【1】表1-5 的各种生产类型的工艺性,特征其生产组织形式为零件的互换性,有修配法、钳工修配、缺乏互换性、毛坯的制造方法和加工余量、手工造型或自由锻造毛坯精度低
6、,加工余量大。工艺装备大批量的的采用专用夹具,标准附件,标准刀具和万能量具,靠划线和试切法达到精度要求。冲压工艺性分析1 材料 08 钢是优质碳素结构刚,易于拉伸成形,具有良好的冲压性能2 工件结构该工件为圆形带孔拉深件,拉伸高度不大,孔在底部并且不在拉深变形区3尺寸精度零件图上工件高度1600.18孔30+0.210。工件外轮廓4500.25 ,属IT14级。一般冲压均能满足精度要求。制定冲压工艺方案1 工序性质和数量( 1 ) 工序性质的确定在冲压加工中,工序性质是指冲压件所需的工序种类,剪裁,落料, 冲孔, 切边等使材料产生分离的工序。弯曲拉深局部成形等使材料产生变形的工序。冲压工序性质
7、的确定主要取决于冲压件的形状尺寸和精度要求。 同时还应考虑冲压变形规律及某些具体条件的限制。通常在确定工序性质时应当考虑以下几方面:1)从零件图上直观的确定工序性质,平板件冲压加工时常采用剪裁,落料,冲孔等冲裁工序。当平面度要求较高时采用较平的工序进行精压,当零件的断面质量尺寸精度要求较高时,需增加修整工序或采用精密冲裁工艺进行加工。2 )对零件图进行计算分析,比较后确定工序性质。3 )为改善冲压变形条件,方便工序定位,增加附加工序。预冲工序工艺切口达到改善冲压变形条件,提高成型质量母的。根据零件图分析冲压加工时须用落料,冲孔,拉深,翻边等工序。( 2 ) 工序数量的确定确定工序数量的基本原则
8、是:在保证工件质量,生产率和经济性要求的前提下,工序数量应尽可能地减少。该零件精度要求较高,故采用复合模。2 工序顺序和组合1 ) 工序顺序各工序的安排主要取决于冲压变形规律和零件质量要求。工序顺序的安排一般应注意以下几方面:1 )所有的孔只要其形状和尺寸不受后续工续的影响,都应在平板坯料上冲出。2 )所在位置会受到以后某工序变形的影响的孔,一般都应在有关的成型工序完成后再冲孔。3 ) 孔靠近或孔边缘较小时,如果模具强度够高,最好同时冲出。否则应先冲出大孔和一般精度孔,后冲出小孔和高精度孔或者先落料再冲孔,力求把可能产生的畸变限制在最小范围内。4 )如果在同一个零件的不同位置冲压时,变形区域互
9、相不发生作用,根据模具结构定位和操作的过程难易程度来确定。5 ) 多角弯曲件主要从材料变形核材料的运动两方面安排弯曲的顺序。一般是先弯外部角后弯内部角,弯角根据零件图先冲裁后落料,由固定挡料销定位。( 2 )工序组合方式选择冲压工序的组合是指将两个或两个以上的工序分析合并在一道工序内完成。减少工序及占用的模具设备和数量,提高效率和冲压件的精度,在确定工序组合时,首先应考虑组合的必要性和可行性,然后再决定是否组合。1 )工序组合的必要性主要取决于冲压件的生产批量。2 )工序的组合的可行性受到多种因素的限制,应保证能冲压出形状、尺寸和精度均符合要求的图样,实现其所需动作保证有足够的强度与现有的冲压
10、设备条件相适应。根据零件图的要求及批量采用落料,拉深,冲孔,切边复合模。3 冲压工艺方案(1 )工艺方案该工件包括落料,拉深,冲孔,切边四个基本工序,可以有以下三种工艺方案。方案一:先落料,再拉深,然后冲孔,最后切边。采用单工序模生产。方案二:落料拉深冲孔切边复合冲压。采用复合模生产。方案三:落料拉深冲孔切边连续冲压。采用连续模生产。( 2 )工艺方案分析方案一模具结构简单,但需四道工序,即需要落料模,拉深模,冲孔模,切边模四副模具,生产效率低,难以满足该零件的年产量要求。方安二只需一副模具,冲压件的形位精度和尺寸精度易保证,且生产效率也高。尽管模具结构较方案一复杂,但由于零件的几何形状简单对
11、称,模具制造并不困难。方案三也只需一副模具,生产效率也 很高,但零件的冲压精度稍差。欲保证冲压件的形位精度,需在模具 上设置导正销导正,故其模具制造,安装较复合模复杂。通过对上述 三种方案的分析比较,该件的冲压生产采用方案二为佳。IV 确定毛坯形状,尺寸和主要参数计算1毛坯尺寸计算该工件位无凸缘圆筒形件,根据等面积原则采用解析法求毛坯直径。如图1所示,将工件分为三个简单的几何体,如图i、ii、iii部分。按工件厚度中心层计算 h=15mm,d=43mm,r=5mm1) 确定是否加修边余量由于坯料的各向异性和模具间隙不均等因素的影响,拉深后 工件的边缘不整齐,甚至出现突耳,需在拉深后进行修边,所
12、有 在计算坯料直径时,要确定是否需要增加修边余量。由于其工作相对高度h/d=15/43 =0.35 <0.5查文献【1】P188表5 2可知不需加修边余量。2) 计算毛坯直径毛坯直径为:Dd24d/1.7200.56r2432 4 43 15 1.72 5 43 0.56 52=63.61故取D=63.63) 确定是否需要压边圈根据坯料相对厚度:t/D X 100=2/63.6 X 100=3.14 >2式中t坯料厚度,mmD毛坯直径,mm查文献【1】P185表5- 1可知不用压边圈,若怕该冲件在拉深过程中会发生起皱,保险起见,采用带弹性压边装置的模具也可。这里的压边圈实际上是作为
13、定位与顶件之用。2 确定拉深次数由于拉深件的高度与其直径的比值不同,有的拉深件科研用一次拉深制成,而有的高度大的拉深件,则需要多次拉深才能制成。所有根据工件的相对高度(h/d)和坯料的相对厚度(t/Dxl00)的大小确定拉深次数。查表可知,由于工件相对高度0.35 远远小于一次拉深时的相对高度0.700.57,则可一次拉深成形。也可根据相对厚度查表确定出筒形件(带压边圈)极限拉深系数m=0.530.55,而工件的拉深系数为 d/D=43/63.6弋0.68 >m则可一次拉成。3 排样及材料利用率1)排样方法冲裁件在板料,带料或条料上的布置方法称为排样。合理的排样是将低成本和保证冲件质量及
14、模具寿命的有效措施。应考虑以下原则:1 提高材料得利用率(不影响冲件的使用性能的前提下可适当改变冲件形状)122 合理排样可使操作方便,劳动强度低。3 模具结构简单寿命长。4 保证冲件质量和冲件对板料纤维方向的要求。A:根据零件图可选用少废料的利用率情况,排样有三种:a 有废料排样b少废料排样c无废料排样根据零件图可选用少废料排样。沿冲件部分外形切断或冲裁。 只有在冲件与冲件之间或冲件与条料侧边之间留有搭边。这种排 样利用率高,用于某些精度要求不是很高的冲裁件排样。B:排样的形式分为直排式,斜排式,直对排,斜对排,混合 排等。根据零件的形状和排样方法确定为直排排样。如图 2所示(2)搭边与料宽
15、1搭边排样中相邻两个零件之间的余量或零件与条料边缘件的余量称为搭边。其作用时补偿定位误差,保持条料有一定的刚度,以保证零件质量和送料方便。由排样图知搭边值a=a1=1.5式中a侧面搭边值ai冲件之间的搭边值搭边值的大小与下列因素有关:a 材料的力学性能b 材料的厚度c 零件的外形和尺寸d 排样方法e 送料及挡料方式2送料步距和条料宽度的确定a. 送料步距条料在模具上每次送进的距离称为送料步距(简称步距或进距)其大小应为条料上两个对应冲裁件的对应点之间的距离。b. 条料宽度条料宽度的确定原则:最小条料宽度要保证冲裁件零件周边有足够的搭边值。最大条料宽度要能在冲裁时顺利在导料板之间送行并与导料板之
16、间有一定的间隙。根据零件图要求,导料板之间无测压装置。送料进距:s=D+ a i=63.6+1.5mm=65.1mm条料宽度:b=D+2a=63.6+2 乂 1.5mm=66.6mm式中D 平行于送料方向冲裁件的宽度3裁板方法板料规格选用 2 mmx 1000 mnK 3000 mm每张钢板裁板条数nl:为了操作方便,采用横裁,即n1 =3000/66.6=45 条余 30mm每条裁板上的工件数n2n2=(B a1)/s=(1000-1.5)/65.1=15 个式中B-钢板宽度(每条裁板的长度)1000mm每张钢板上的工件总数:n >=n1 x n2=45X 15=675个(3)材料的利
17、用率衡量材料的经济利用率的指标是材料的利用率耳=(n 总X 兀 E2) /(4L XB) x 100%二(675X3.14 X63.62) /(4 x 3000X 1000) X 100%=71.4%第二部分冲压模具设计I确定冲模类型机结构形式在冲压工艺性分析后拟定冲压工艺方案时选择复合模,又因零件的几何形状简单对称,工件间无搭边值,复合模结构相对简单,操作方便, 又可直接利用压力机的打杆装置进行推件,卸件可靠、便于操作,所 以模具类型为少废料复合模。计算工序压力,选择压力机在冲裁模设计中,冲压力是指落料力,卸料力,拉深力,压边力,冲孔力,切边力和推件力的总称。它是冲裁时选择压力机,进行模具设
18、计校核强度和刚度的重要依据。1)落料力落料力38F= 1.3 兀 DS t= 1.3 X3.14 X63.6 X320X2N166153.782N 166.2KN式中材料抗剪强度查文献【1】 P63 表 3 18可知08专冈 S=260360MPa 取 S = 320Mpa)卸料力卸=K卸F落= 0.04 X166.2KN6.65KN查文献【1】 P60 表 3 16可知式中K卸=0.43 )拉深力F拉=K;t dt Sb= 0.45 X3.14 X43X 2X400N= 48607.2N弋 48.6KN查文献【1】 P197 表 5 7可知式中K修正系数,K= 0.45Sb材料强度极限,08
19、钢S b=342441MPa取Sb = 400MPa4 )压边力F压=兀 /4D2 (d+2rd) 2F= 3.14/463.62- (43+2X6) 2X 2.5N= 2001.6715N弋2KN式中rd凹模圆角半径,取rd=6mmP单位压边力,P= 2.5MPa5 冲孔力冲=1.3 兀 dt S= 1.3 X3.14 X30X 2X320N = 78374.4N弋 78.4KN式中d工件孔直径,d = 30mm5) 切边力F 切=1.3 兀 Dt S= 1.3 X3.14 X45X2X320N= 117561.6NQ 117.6KN式中D一一工件外轮廓直径,D= 45mm6) 推件力F 推
20、=nK推F冲= 3X0.05 X 78.4KN= 11.7KN式中n冲孔时卡在凹模内的废料数,n=3;K推推件力因素,K推=0.05。故总冲压力为:F总=F落+F卸+F拉+F压+F冲+F切+F推=166.2+6.65+48.6+2+78.4+117.6+11.76KN = 431.21KN从满足冲压力要求看,选用630KN®格的压力机具主要技术参数为:公称压力:630KN滑块行程:120mm最大封闭高度:360mm最大封闭调节量:90mm工作台尺寸:480mm x 710mm工作台垫板孔尺寸:180mm模柄孔尺寸: 50m诉 70 mm工作台厚度:90mm垫板厚度:80mm计算模具压
21、力中心模具的压力中心就是冲裁力合力的作用点。冲模压力中心应尽可能和模柄轴线以及压力机滑块中心线重合,以使冲模平稳地工作,减少导向件的磨损,从而提高模具的寿命。冲模压力中心的求法,采用求平行力系合力的作用点方法。由于绝大部分冲裁件沿冲裁轮廓线的断面厚度不变,轮廓部分的冲裁力与轮廓长度成正比,所以,求合力的作用点可转化为求轮廓线的中心。由图3可知,其压力中心就在圆心上即 Xo=0, Y=0。IV 计算模具零件主要工作部分的刃口尺寸模具的落料凹模24,落料拉深凸凹模5,拉深冲孔凸凹模20和冲孔凸模14工作部分的相互关系。如图4所示5小 己口1凸、凹模刃口尺寸的确定凸、凹模刃口尺寸的确定原则1)考虑落
22、料和冲孔的区别,落料件的尺寸取决于凹模。因此, 落料模应先决定凹模的尺寸,用减小凸模尺寸来保证合理的间 隙。冲孔件的尺寸取决于凸模,因此,冲孔模应先决定凸模尺 寸。用增大凹模尺寸来保证合理的间隙。2)考虑刃口的磨损对冲件尺寸的影响。刃口磨损后尺寸变大, 其刃口的基本尺寸应接近或等于冲件的最小极限尺寸;刃口磨 损后尺寸变小,应接近或等于冲件的最大极限尺寸。3)考虑冲件精度与模具精度之间的关系,选择模具制造公差 时,既要保证冲件的精度要求又要保证有合理的间隙值。一般 冲模精度较冲件精度高23级。2凸、凹模分别加工时的工作部分尺寸其公式见表:表一凸、凹模分别加工时的工作部分尺寸的计算公式工序性质冲件
23、尺寸凸模尺寸凹模尺寸落D0-ADP= " XADd= (T XA)料Zmin )- 3 p0+ 8 d冲孔D0+Adp= (d+XA)0- Spdd= (d+XA +Zmin)0+ 8 d表示:D, Dd分别为落料凸,凹模刃口尺寸d p, dd一分别为冲孔凸,凹模刃口尺寸D , d 一分别为落料件外径和冲孔件的基本尺寸心一分别为凸凹模的制造公差,凸模按IT6,凹模按 IT7.制件的制造公差Zmin 最小合理间隙X磨损系数,其值在0.51之间。零件精度IT10以上,X=1,工件精度IT14, X=0.5.为了保证 冲模的间隙小于最大合理间隙(ZmaX,凸模和凹模制造公差必 须P p +
24、" d W Zmax Z min3凸、凹模配合加工时的工作部分尺寸对于冲制复杂形状冲件的模具或单件生产的模具,其凸凹模常采用配合加工的方法。凸凹模工作部分尺寸计算:其落料件按凹模磨损后尺寸增大(A类尺寸),减小(B类尺寸)和不变(C类尺寸)的规律分 三种。冲件按凸模磨损后尺寸减小(B 类尺寸) ,增大( A 类尺寸)和不变(C类尺寸)的规律分三种。因为工件属冲孔,根据 设计要求确定凸模刃口尺寸并依次为基准配置凹模,按磨损后其尺寸变大,变小,不变。( 1) 落 料刃口尺寸计算对于落料部分按未注公差IT14 级计算,所以落料件尺寸为63.60o.imm根据查表得冲裁刃口双面间隙为 Zmi
25、n = 0.1mm, Zma40.14mm.063.6 00.1的制造公差查表得 8凹=0.04mm 8 凸=0.03mm8 凹+S 凸=0.04+0.03mm=0.07mmZmax-Zmin=0.14-0.1 mm =0.04 mm由于8凹+S T>Zmax-Zmin,故采用凸模与凹模配合加工法磨损系数为x=0.5. 则凹模刃口尺寸为D凹二(D-x ) +'凹 0二(63.6-0.5 X 1)+0.04 °=63.1+0.04凹模刃口尺寸d凹按凹模实际尺寸配制,其双面间隙为0.10.4mm为保证模具刃口有较长的使用寿命,即保证刃口磨损后还能冲出合格的制件来,制造是按最
26、小间隙Zmin=0.01mn®合间隙2)冲孔刃口尺寸计算对于30的孔尺寸为30+0.210,制造公差查表得8 凹=S 凸=0.02 mm由于 5 凹+S 凸=0.02+0.02mm=0.04mm即S凹+S = Zmax-Zmin凸故采用分开加工,则:d 凸=(d+x4) 0-8 凸=(30+0.5 X 0.21 ) +0.020 mm=30.105 +0.020 mmd 凹=(d+xA +Zmin) +'凹0=(30+0.5 X 0.21+0.1 ) +0.020 mm=30.205+0.020 mm(3) 拉深刃口尺寸计算对于拉深部分的工件高度450-0.25制造公差查表得
27、8 凹=S 凸=0.02 mm拉深凸模和凹模的单边间隙查表,按Z/2=1.1t,即Z=2X 1.1t则可求得拉深凸模和凹模的刃口尺寸为:D 凹二(D-0.75 A) +'凹0=(45-0.75 X 0.25 ) +0.020 mm=44.8125+0.020 mmQ 40.41 +0.02 0 mmV、弹性元件的设计为了得到较平整的工件。此模具采用弹压式卸料结构。弹簧和橡胶是模具中广泛应用的弹性元件。主要为弹性卸料,压料及出件装置供弹压力。弹压卸料装置是由卸料板、弹性元件( 弹簧或橡胶) ,卸料螺钉等零件组成。根据模具安装位置拟选4 个弹簧,每个弹簧的预压力为:Fo > Fx/n
28、式中:Fx为冲裁卸料力;n 为弹簧个数。所以FoAFx/n=2928 4=732N查冲压模具设计指导表8-40 ,初选弹簧规格为40mr 6mm x 80mm其 余 件 参 数 是D=40mm, d=6mm, h0 =80mm,t=9.9mm, hj =28mm,f=-3 79mm, Fj =1200N, n=7.4D弹簧中径;d材料直径;t 节距;Fj 工作极限负荷;ho自由高度;n有效圈数;hj工作极限负荷下 变形量。Ho 2hjFj732 c。28120017mm也可以直接在弹簧压缩特性曲线上根据查出H0,见图检查弹 簧最大允许压缩量,如满足下列条件,则弹簧选的合适。hjHo h工h修模
29、HHo hx h修模工=1.8mm h修模修磨为凸凹模修磨量,一般取41Omm h修模取=4mm所以,h j H o h工h修模=17+1.8+4mm =22.8mm由 28>22.8 ,即 hj> Ho所以,所选弹簧特性曲线为VI模具零件的选用1 .模架的选择冲模模架标准是1991年5月1日由国家技术监督局批 准频布实施的,该标准是在冷冲模国家标准的基础上修订 的新标准,其中模架产品标准:(GB/T2851.1, GB/T2851.3小7, GB/T2852.14)共10个。模架的选择一般根据凹模定位和 卸料装置的平面而定,选择模座的形状和尺寸,模座外形,尺 寸比凹模相应尺寸大4
30、070mm模座厚度一般取凹模厚度的1八 1.5倍。下模座外形尺寸至少超过压力机约50mm同时选择的模架与闭合后的模具设计的高度相适应。通常所说的模架由上模座,下模座,导柱,导套四部分组成,一般标准模架不包括模柄。模架是整副模具的骨架,它是连接冲模主要零件的载体,模具的全部零件都固定在它上面,并承受冲压过程的全部载荷。模具的上模座盒下模座分别与冲压设备的滑块和工作台固定。上下模间的精确位置由导柱导套来实现。模架的选择应从三方面入手:依据产品零件精度,模具工作零件配合精度、高低确定模架精度;根据产品零件精度要求,形状,板料送料方向选项二模架类型;根据凹模周界尺寸确定模架的大小规格。查文献【 1】
31、P117 表 2 49选择冲模滑动导向模架后侧导柱模架GB/T2851.3-1990。后侧导柱模架的特点是导向装置在后侧,横向和纵向送料都比较方便,但如果有偏心载荷,压力机导向又不精确,就会造成上模歪斜,导向装置和凸、凹模都容易磨损,从而影响模具寿命,此模架一般用于较小的冲裁模。选择模架规格:导套 d/mm< L/mm< D)/mmfe 25X95X38(mm)导柱 d/mnm< L/mnriK 为 25 x 180(mm)模座厚度H上模取35mm上模垫板厚度H垫7mm凸模固定板H固为14 mm,下模座厚度H下模取40mm那么该模具的闭合高度:H 闭 H 上模 H 垫 H 凹
32、 H 固 H 凸、凹 H 下模h2 式中H凹为凹模厚度H凹=24mmH凸、凹为凸凹模厚度H凸、凹=24mmh2为凸凹模冲裁后进入凹模的深度h2=0.4mm所以 H 闭=35+7+24+24+24+39-0.4=142.6mm2模柄的选择查文献【1】表237知选用旋入式模柄。通过螺纹与上模 座连接,为防止松动,常用防转螺钉紧固,优点是拆装方便, 缺点是模柄轴线与上模座的垂直度较差。3螺钉固定螺钉引入模体的深度勿太深,如拧入铸铁件深度是螺钉 直径的2-2.5倍,拧入一般钢件深度是螺钉直径的1.52倍。4定位销冲模中的定位销常选用圆柱销,其直径与螺钉直径接近, 不能太细,每个模具上只需两个销钉,长度
33、不能太长,使进入 模体长度直径的22.5倍。W 冲压设备的校核选用630KNB格的压力机具主要技术参数为:公称压力:630KN滑块行程:120mm最大封闭高度:360mm最大封闭调节量:90mm工作台尺寸:480mm乂 710mm工作台垫板孔尺寸:180mm模柄孔尺寸:50m诉70 mm工作台厚度:90mm垫板厚度:80mm皿其他需要说明的问题1、挡料钉在卸料板上设置一个挡料钉,4的挡料钉的结构如图,导正应在卸料板压紧板料之前完成导正, 考虑料厚和能准确挡料,确定卸料板上的挡料钉超出卸料板 O.4mm并考虑到挡料钉下部弹簧的长度h0 25mm,结合模座其它零件的尺寸,确定挡料钉的长度为 19m
34、m挡料钉和其孔的配合采用H/h6,其结构如图:Lcn2、定位钉定位钉用于单个坯料或工序件的定位,其定位方式有两种:外缘定位和内孔定位,如图所示:3、垫板的设计垫板的作用是直接承受凸模的压力,以降低模座所受的单位压力,防止模座被局部压陷,从而影响模具的正常工作,垫板上的螺钉 孔,销钉孔,推杆孔均根据凹模固定板进行配作,垫板厚度一般取 4-12mm此模具中的垫板厚度取7 mm垫板的长和宽尺寸和凸模固定 板相同。4、卸料板当卸料板仅起卸料作用时,凸模与卸料板的双边间隙取决于板料 厚度,有一般在0.2-0.5mm之间,板料薄时取小值;板料厚时取大值。 当固定卸料板兼起导板作用时,一般按 H7/ h6配
35、合制造,但应保证 导板与凸模之间间隙小于凸、凹模之间的冲裁件时,一般采用固定卸料装置。IX模具装配模具装配是按照规定的技术要求,将若干个零件结合成型零部件, 再将若干个零件和部件组合成模具的工艺过程,装配工作通常分为部件装配和总装配。1、冲裁间隙的调整对于冲裁模,即使模具零件的加工精度已经得到保证,但是在装配时, 如果不能保护冲裁间隙均匀会影响制件的质量和模具的使用寿命。2、模架的装配模柄的装配此模具采用的是凸缘模柄中的B 型,模柄与上模座的配合为H7 h6, 将模柄装上模座,用角尺检查模柄圆柱面与上模座上平面的垂直度,其误差不大于O. 05mn后用螺钉将其固定在上模座上,应在装模柄前先装入推板。导柱和导套的装配导柱导套与上下模座均采用压入式连接导套导柱与模座的配合分别为H7 r6 和 R7 r6 压入时要注意校正导柱对模座底面的垂直度,装配好的导柱的固定端面与下模座底面的距离不小于1-2mm3、凸模和凸凹模的
温馨提示
- 1. 本站所有资源如无特殊说明,都需要本地电脑安装OFFICE2007和PDF阅读器。图纸软件为CAD,CAXA,PROE,UG,SolidWorks等.压缩文件请下载最新的WinRAR软件解压。
- 2. 本站的文档不包含任何第三方提供的附件图纸等,如果需要附件,请联系上传者。文件的所有权益归上传用户所有。
- 3. 本站RAR压缩包中若带图纸,网页内容里面会有图纸预览,若没有图纸预览就没有图纸。
- 4. 未经权益所有人同意不得将文件中的内容挪作商业或盈利用途。
- 5. 人人文库网仅提供信息存储空间,仅对用户上传内容的表现方式做保护处理,对用户上传分享的文档内容本身不做任何修改或编辑,并不能对任何下载内容负责。
- 6. 下载文件中如有侵权或不适当内容,请与我们联系,我们立即纠正。
- 7. 本站不保证下载资源的准确性、安全性和完整性, 同时也不承担用户因使用这些下载资源对自己和他人造成任何形式的伤害或损失。
最新文档
- 浅论马克思主义关+于人的全面发展思想简析
- 介入个案护理比赛策划与实施要点
- 违法强制拆除协议书
- 输液致死纠纷协议书
- 饭店宴席预定协议书
- 养生馆店长合同协议书
- 转让私人墓地协议书
- 酒店蛋糕采购协议书
- 酒店预定服务协议书
- 买卖合同和居间协议书
- GB/T 22838.5-2024卷烟和滤棒物理性能的测定第5部分:卷烟吸阻和滤棒压降
- 2024年安徽中考英语词汇表
- 事业单位聘用工作人员登记表
- DL∕T 5783-2019 水电水利地下工程地质超前预报技术规程
- 人教九年级历史上册《七单元大单元设计》教学课件
- 成都市2022级(2025届)高中毕业班摸底测试(零诊)物理试卷(含答案)
- 2024年四川省广元市中考数学真题试卷(含答案)
- 无菌操作技术原理及实验课件
- 江苏省无锡市梁溪区2023-2024学年六年级下学期期末语文试卷
- 名侦探柯南与化学探秘智慧树知到期末考试答案章节答案2024年中南大学
- 医院培训课件:《失禁护理的新进展》
评论
0/150
提交评论