
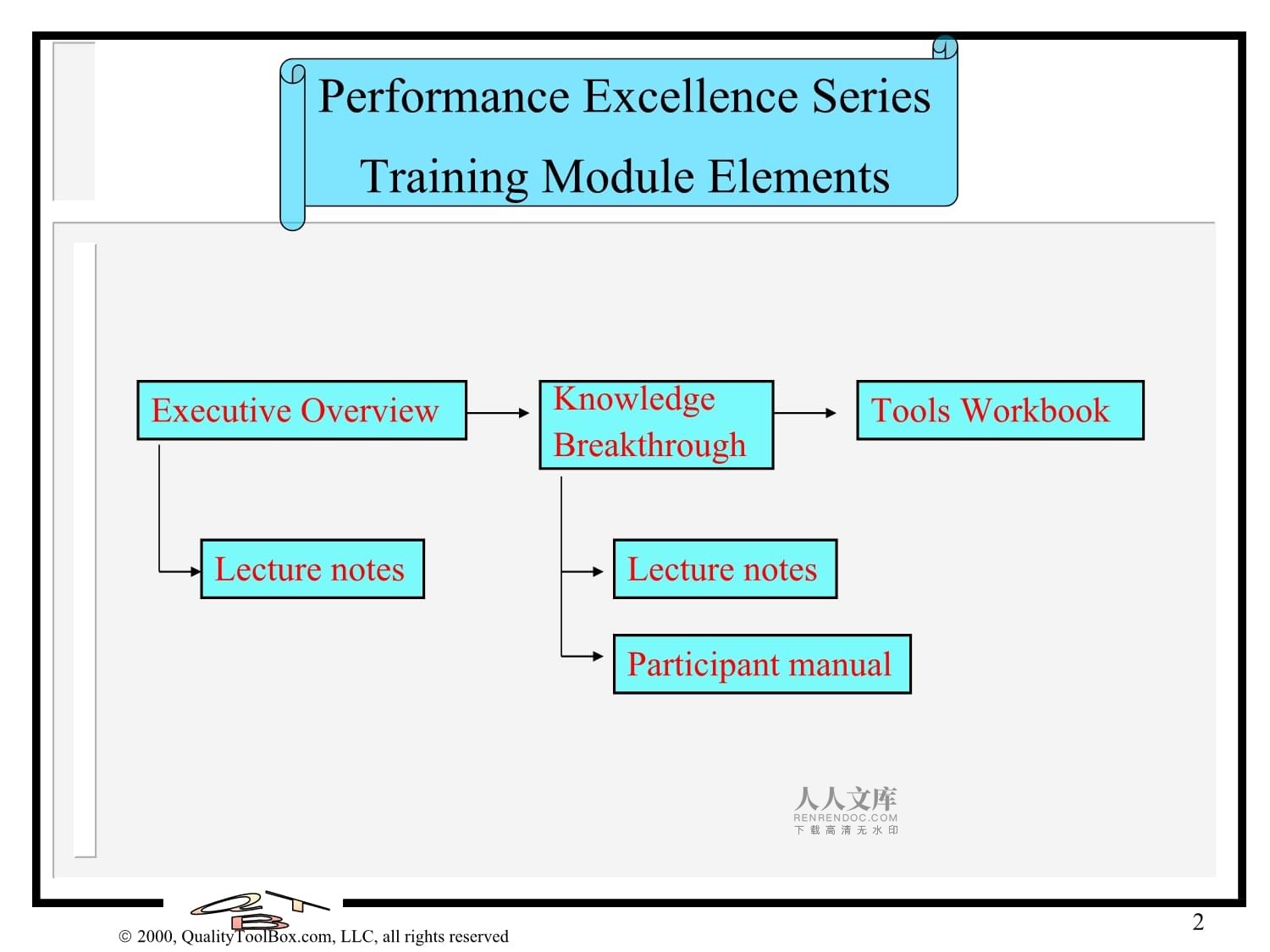



版权说明:本文档由用户提供并上传,收益归属内容提供方,若内容存在侵权,请进行举报或认领
文档简介
1、A Strategy for Performance ExcellenceMistake Proofing & Poka-yoke1Executive OverviewParticipant manualTools WorkbookKnowledge BreakthroughLecture notesLecture notesPerformance Excellence SeriesTraining Module Elements2Table of ContentsPoka-Yoke ( Mistake Proofing)Session 1.0Introduction. 3Session 2.
2、0Zero Defects & Costs. 7Session 3.0Waste Management . 12Session 4.0Zero Defect Quality(ZDQ). 19Session 5.0Understanding Process Errors. 27Session 6.0Four Elements of ZDQ. 35Session 7.0Seven Steps to Poka-Yoke. 42Session 8.0Poka-Yoke Methods. 44Session 9.0Summary. 673IntroductionDefects & CostsWaste
3、ManagementZero Defect Quality ( ZDQ)Understanding Process ErrorsFour Elements of ZDQSeven Steps To Poka-Yoke AttainmentPoka-Yoke MethodsSummaryPoka-Yoke Concepts4Why is “Zero Defects” an Important Concept?Key Element in our capability to implement Kaizen- Lean Manufacturing Systems.No need for “just
4、 in case” inventoriesAllows company to make only what the customer needs. 5Why KaizenTimeCPI ProjectTimeCPITimeSavingsSavingsSavingsProcess Improvement Project ImplementedMaintenance of Process PerformanceKaizen6 Sigma Data Driven Methodology to Magnify Impact of Process Improvement Apply Control Te
5、chniques to Eliminate Erosion of Improvements Proceduralize/Standardize Improvements for Improved Maintenance of Critical Process ParametersKaizen Use Small Teams to Optimize Process Performance by Implementing Incremental Change Apply Intellectual Capital of Team Members Intimate with Process CPI P
6、rojects Emphasize Control and Long Term MaintenanceKaizen Projects Emphasize Incremental Improvements6MajorCPITools(6s) Kaizen LeanDescriptionCp/Cpk 4Process capability assessmentDOE 4Design of experimentsSPC 4Process control based on statistics and data analysisFMEA 4Risk assessment toolRegression
7、4Correlate effect one variable has on anotherProcess Map 4 4 4Map process steps to communicate and identify opportunities5 whys /2 hows 4 4 4 Determination methods for root cause discoveryPareto 4 4 4Column chart ranking items highest to lowestFishbone 4 4 4Cause / Effect Diagram5S 4 4Elimination wa
8、steVisual Mgmt 4 4 4Emphasis on visual techniques to manage processPoka-Yoke 4 4Error proofing techniquesSpaghetti Chart 4 4Kanban 4 4Material storage technique used to control processTakt Time 4 4Determine pace or beat of a processStd Work 4 4Evaluate tasks done during a processSMED 4 4Single minut
9、e exchange of dies - Quick machine set upTPM 4 4Integrate maintenance strategy with processCellular Flow 4 4Reduce inventory & cycle time through process layout and pull production techniquesExpand Process Improvement Program to Utilize Kaizen Tool Kit Tool Kit Comparison7IntroductionDefects & Costs
10、Waste ManagementZero Defect Quality ( ZDQ)Understanding Process ErrorsFour Elements of ZDQSeven Steps to Poka-Yoke AttainmentPoka-Yoke MethodsSummaryPoka-Yoke Concepts8Why is “Zero Defects” an Important Concept?Maintain Customer Satisfaction & LoyaltyHappy Customers mean more sales!9Why is “Zero Def
11、ects” an Important Concept?COSTThere is always a cost associated with manufacturing defects!10Costs of Defects ?Does it cost more to make processes better ? NOMaking processes better leads to reducedReworkScrapWarranty costsInspection costs111-10-100 RuleThe 1-10-100 rule states that as a product or
12、 service moves through the production system, the cost of correcting An error multiplies by 10.ActivityCost Order entered correctly$ 1Error detected in billing$ 10Error detected by customer$ 100Dissatisfied customer shares the experience with others the costs is $100012IntroductionDefects & CostsWas
13、te ManagementZero Defect Quality ( ZDQ)Understanding Process ErrorsFour Elements of ZDQSeven Steps to Poka-Yoke AttainmentPoka-Yoke MethodsSummaryPoka-Yoke Concepts13Why is “Zero Defects” an Important Concept?Key Element in our capability to eliminate waste.DefectsMisused resourcesInventoriesUntappe
14、d ResourcesMotionsDelaysProcesses14What is Waste? Everything we do that costs something without adding value to the productOur objective Value added = MaximumNon-Value Added = Minimum15The nine types of wasteOverproductionDelays (waiting time)TransportationProcessInventoriesMotionsDefective products
15、Untapped resourcesMisused resources 9 Wastes16Continuous ImprovementIs the continuous elimination of waste17Elimination of WasteThe MethodCheck and measure resultsIdentify wasteSearch for causesImplement continuous improvement18Elimination of Wastes and Continuous ImprovementElimination of wastesKAI
16、ZENContinuous ImprovementOne piece flowSMEDVisual ControlsWorkplace OrganizationKanbanStandard WorkProcess ControlTotal Productive MaintenancePoka-YokeLeadtimeCostsQuality the First TimeThe ApproachThe MeansThe Strategy19IntroductionDefects & CostsWaste ManagementZero Defect Quality ( ZDQ)Understand
17、ing Process ErrorsFour Elements of ZDQSeven Steps to Poka-Yoke AttainmentPoka-Yoke MethodsSummaryPoka-Yoke Concepts20What is a Zero Defect Quality System (ZDQ)?A quality concept to manufacture ZERO defects & elimination of waste associated with defects!“ZERO” is the goal! 21What is a Zero Defect Qua
18、lity System (ZDQ)?Based on a discipline that defects are prevented.Control the process so that defects are impossible!22What is a Zero Defect Quality System (ZDQ)?No Finger Pointing. Operators and Machines will sometimes make mistakes.Find ways to keep errors from becoming defects!23What is a Zero D
19、efect Quality System (ZDQ)?A Method for Mistake-Proofing (Poka-yoke) a process.ZDQ assures that defects are not shipped!24How ZDQ Makes Work EasierMistake-Proof or Poka-yoke the process!Recognize that it is natural for people to make mistakes.25How ZDQ Makes Work EasierMistake-Proof or Poka-yoke the
20、 process!Not noticing that an error is made or a machine is not functioning does not make a person stupid or foolish.26How Do We Achieve ZDQ ?Mistake-Proof or Poka-yoke the process!Errors never become defects!No finger pointing after the fact. No mandate to do better next time.27IntroductionDefects
21、& CostsWaste ManagementZero Defect Quality ( ZDQ)Understanding Process ErrorsFour Elements of ZDQSeven Steps to Poka-Yoke AttainmentPoka-Yoke MethodsSummaryPoka-Yoke Concepts28Poka-Yoke results in Quality of Processes Dedicated linesOne piece flowTransformation = Quality production the 1st time Insp
22、ection.eliminated ?TransportStorageDelay/waitLeadtimeQuality the 1st time Cost29Relationship between processes and quality defects.Almost any business activity can be considered a process.Production processes involve the flow of material. Machining, assembly, and packaging are typical production pro
23、cesses.Business processes involve the flow of information. Financial planning, purchasing & order entry are typical business processes.All processes have the potential for defects. Hence, all processes offer a opportunity for the elimination of defects and the resultant quality improvement.30In orde
24、r to reduce quality defects and stop throwing away money, we must Understand the process an its relationship to other business processes.Identify the inputs and outputs of the process.Know who are the suppliers to and customers of the process.=Reduce the variation of the processAnd31What Causes Defe
25、cts?Process Variation From1. Poor procedures or standards.2. Machines.3. Non-conforming material.4. Worn tooling.5. Human Mistakes.Except for human mistakes these conditions can be predicted and corrective action can be implemented to eliminate the cause of defects32What Causes Defects?Human Mistake
26、sSimple errors-the most common cause of defects-occur unpredictably.The goal of ZDQ is zero! Make certain that the required conditions are in place and controlled to make acceptable product 100% of the time.33Ten Types of Human MistakesForgetfulnessMisunderstandingWrong identificationLack of experie
27、nceWillful (ignoring rules or procedure)Inadvertent or sloppinessSlowlinessLack of standardizationSurprise (unexpected machine operation, etc.)Intentional (sabotage)3435IntroductionDefects & CostsWaste ManagementZero Defect Quality ( ZDQ)Understanding Process ErrorsFour Elements of ZDQSeven Steps to
28、 Poka-Yoke AttainmentPoka-Yoke MethodsSummaryPoka-Yoke Concepts36The 4 Components of ZDQZDQ functions by combining four elementary components:1. Point of Origin Inspection2. 100 % Audit Checks3. Immediate Feedback4. Poka-Yoke37InspectionThe 3 basic approaches to inspection of processed product are:J
29、udgement/Standard InspectionInformative InspectionPoint of Origin InspectionThe first two approaches are widely used and considered traditional.Only Point of Origin Inspection actually eliminates defects.38Point of Origin InspectionFocus on prevention, not detection.One of the 4 basic elements of ZD
30、Q.Differs from Judgement and Informative:Catches errorsGives feedback before processingNo risk of making more defective productDetect ErrorFeedback/Corrective ActionProcess with Zero DefectsBy combining Check and Do in the ZDQ approach; the Doing is controlled so it cannot be wrong 100% of the time!
31、May include: Switches that detect miss-fed parts Pins that prevent miss-feeding Warning lights Sound signals39ZDQ/Check and Do/Point of Origin InspectionPoint of Origin InspectionCheck for optimum process conditions before processing is done and errors can be made.Instant feedback.Corrections made b
32、efore defects occur.40100% Audit ChecksPoint of Origin Inspection on every piece.The second of the 4 basic elements of ZDQ.Differs from SQC inspection:Does not rely on samplingPrevents defectsDoes not assume defects will statistically occur100% Audit checks everything on the line!Zero Defects41Quick
33、 FeedbackError correction as soon as possibleThe third of the 4 basic elements of ZDQ.Differs from traditional inspection approaches that:Correct problems after the processAddress the problem when errors are already defectsIn some cases never identify an error has occurredZDQ sends the operator a si
34、gnal and alarms the person that an error has happened!ZDQ Inspections = Immediate Feedback42IntroductionDefects & CostsWaste ManagementZero Defect Quality ( ZDQ)Understanding Process ErrorsFour Elements of ZDQSeven Steps to Poka-Yoke AttainmentPoka-Yoke MethodsSummaryPoka-Yoke Concepts43The Seven Gu
35、idelines to Poka- Yoke Attainment1.) Quality Processes - Design “Robust” quality processes to achieve zero defects.2.) Utilize a Team Environment- leverage the teams knowledge,experience to enhance the improvement efforts.3.) Elimination of Errors -Utilize a robust problem solving methodology to dri
36、ve defects towards zero.4.) Eliminate the “Root Cause” of The Errors-Use the 5 Whys and 2 Hs approach 5.) Do It Right The First Time- Utilizing resources to perform functions correctly the “first” time. 6.) Eliminate Non-Value Added Decisions- Dont make excuses-just do it !7.) Implement an Increment
37、al Continual Improvement Approach-implement improvement actions immediately and focus on incremental improvements; efforts do not have to result in a 100% improvement immediately.44IntroductionDefects & CostsWaste ManagementZero Defect Quality ( ZDQ)Understanding Process ErrorsFour Elements of ZDQSe
38、ven Steps to Poka-Yoke AttainmentPoka-Yoke MethodsSummaryPoka-Yoke Concepts45Poka-yokeMistake-proofing systemsThe fourth of the 4 basic elements of ZDQ.Does not rely on operators catching mistakesInexpensive Point of Origin inspectionQuick feedback 100% of the time“The machine shut down. We must hav
39、e made an error!”BEEP!BEEP!BEEP!Most Poka-yoke devices are sensor or jig devices that assure 100% compliance all the time!46Poka-yokeWhat is Poke-yoke?A method that uses sensor or other devices for catching errors that may pass by operators or assemblers.Poka-yoke effects two key elements of ZDQ:Ide
40、ntifying the defect immediately ( Point of Origin Inspection)Quick Feedback for Corrective ActionHow effective the system is depends on where it is used: Point of Origin or Informative Inspection. Poka-yoke detects an error, gives a warning, and can shuts down the process.47Poka-yokePoke-yoke and Po
41、int of Origin Inspections( Proactive Approach):A fully implemented ZDQ system requires Poka-yoke usage at or before the inspection points during the process. Poka-yoke will catch the errors before a defective part is manufactured 100% of the time.48Poka-yokePoka-yoke and Informative Inspection( Reac
42、tive Approach):Check occurs immediately after the process.Can be an operator check at the process or successive check at the next process.Not 100% effective, will not eliminate all defects.Effective in preventing defects from being passed to next process.Although not as effective as the Source inspe
43、ction approach, this methodology is more effective than statistical sampling and does provide feedback in reducing defects.49Poka-yoke Systems Govern the ProcessTwo Poka-Yoke System approaches are utilized in manufacturing which lead to successful ZDQ:1. Control ApproachShuts down the process when a
44、n error occurs.Keeps the “suspect” part in place when an operation is incomplete.2. Warning ApproachSignals the operator to stop the process and correct the problem.50Control SystemTakes human element out of the equation;does not depend on an operator or assembler.Has a high capability of achieving
45、zero defects.Machine stops when an irregularity is detected.“There must have been an error detected; the machine shut down by itself!”51Warning SystemSometimes an automatic shut off system is not an option.A warning or alarm system can be used to get an operators attention.Below left is an example o
46、f an alarm system using dials, lights and sounds to bring attention to the problem.Color coding is also an effective non automatic option.BEEP!BEEP!BEEP!“Im glad the alarm went off, now Im not making defects!”52Methods for Using Poka-yokePoka-yoke systems consist of three primary methods:1. Contact2
47、. Counting3. Motion-SequenceEach method can be used in a control system or a warning system.Each method uses a different process prevention approach for dealing with irregularities.53Contact MethodA contact method functions by detecting whether a sensing device makes contact with a part or object wi
48、thin the process.Missing cylinder;piston fully extended alarm soundsContact Method using limit switches identifies missing cylinder.An example of a physical contact method is limit switches that are pressed when cylinders are driven into a piston. The switches are connected to pistons that hold the
49、part in place. In this example, a cylinder is missing and the part is not released to the next process.Cannot proceed to next step.Cylinder present54Physical Contact DevicesLimit SwitchesToggle Switches55Energy Contact DevicesPhotoelectric switches can be used with objects that are translucent or tr
50、ansparent depending upon the need.Transmission method: two units, one to transmit light, the other to receive.Reflecting method:PE sensor responds to light reflected from object to detect presence.LightTransmitterReceiverObjectIf object breaks the transmission, the machine is signaled to shut down.5
51、6Contact DeviceAn example of a contact device using a limit switch. In this case the switch makes contact with a metal barb sensing its presence. If no contact is made the process will shut down.57Contact MethodsDo not have to be high tech!Passive devices are sometimes the best method. These can be
52、as simple as guide pins or blocks that do not allow parts to be seated in the wrong position prior to processingTake advantage of parts designed with an uneven shape!A work piece with a hole a bump or an uneven end is a perfect candidate for a passive jig. This method signals to the operator right a
53、way that the part is not in proper position.58Counting MethodUsed when a fixed number of operations are required within a process, or when a product has a fixed number of parts that are attached to it. A sensor counts the number of times a part is used or a process is completed and releases the part
54、 only when the right count is reached.In the example to the right a limit switch is used to detect and count when the required amount of holes are drilled. The buzzer sounds alerting the operator that the appropriate amount of steps have been taken in the process.59Counting MethodAnother approach is
55、 to count the number of parts or components required to complete an operation in advance. If operators finds parts leftover using this method, they will know that something has been omitted from the process.“I have an extra part. I must have omitted a step!”60Motion-Sequence MethodThe third poka-yok
56、e method uses sensors to determine if a motion or a step in a process has occurred. If the step has not occurred or has occurred out of sequence, the the sensor signals a timer or other device to stop the machine and signal the operator.This method uses sensors and photo-electric devices connected t
57、o a timer. If movement does not occur when required, the switch signals to stop the process or warn the operator. 61Motion-Sequence MethodIn order to help operators select the right parts for the right step in a process the “sequencing” aspect of the motion-step method is used. This is especially he
58、lpful when using multiple parts that are similar in size and shape.In this example, each step of the machine cycle is wired to an indicator board and a timer. If each cycle of the machine is not performed within the required “time” and “sequence”, the indicator light for that step will be turned on
59、and the machine will stop.Indicator BoardMachine62Types of Sensing DevicesSensing devices that are traditionally used in poka-yoke systems can be divided into three categories:1. Physical contact devices2. Energy sensing devices3. Warning Sensors Each category of sensors includes a broad range of devices that can be used depending on the process.63Physical Contact SensorsThese devices work by physically touch
温馨提示
- 1. 本站所有资源如无特殊说明,都需要本地电脑安装OFFICE2007和PDF阅读器。图纸软件为CAD,CAXA,PROE,UG,SolidWorks等.压缩文件请下载最新的WinRAR软件解压。
- 2. 本站的文档不包含任何第三方提供的附件图纸等,如果需要附件,请联系上传者。文件的所有权益归上传用户所有。
- 3. 本站RAR压缩包中若带图纸,网页内容里面会有图纸预览,若没有图纸预览就没有图纸。
- 4. 未经权益所有人同意不得将文件中的内容挪作商业或盈利用途。
- 5. 人人文库网仅提供信息存储空间,仅对用户上传内容的表现方式做保护处理,对用户上传分享的文档内容本身不做任何修改或编辑,并不能对任何下载内容负责。
- 6. 下载文件中如有侵权或不适当内容,请与我们联系,我们立即纠正。
- 7. 本站不保证下载资源的准确性、安全性和完整性, 同时也不承担用户因使用这些下载资源对自己和他人造成任何形式的伤害或损失。
最新文档
- 2024昌吉职业技术学院辅导员招聘笔试真题
- 2025年衢州龙游县机关事业单位招聘考试试题【答案】
- 2025年血液灌流吸附器合作协议书
- 2025年河北石家庄学院选聘事业单位工作人员考试试题【答案】
- 2025年梧州岑溪市选聘市区学校专任教师考试试题【答案】
- 2025年内江市隆昌市教育和体育局选拔教师考试笔试试题【答案】
- 工商联会员代表大会工作报告
- 2025年DH(DHP)离心压缩机项目合作计划书
- 2025年高纯超细石英粉项目建议书
- 2025年应用软件设计服务项目合作计划书
- 职业教育学试题及答案
- GB/T 17619-1998机动车电子电器组件的电磁辐射抗扰性限值和测量方法
- GB/T 10560-2017矿用焊接圆环链用钢
- FZ/T 52025-2012再生有色涤纶短纤维
- 2023年山东铁路投资控股集团有限公司校园招聘笔试题库及答案解析
- 音标版中考必考英语1600单词
- 机械制造企业隐患排查清单(公司级、车间级、岗位级)
- 夏季高温施工安全生产培训
- 纯净水及矿泉水厂可行性研究报告
- 援绝神丹_集成良方三百种_方剂加减变化汇总
- 中药饮片GMP认证检查指导原则
评论
0/150
提交评论