
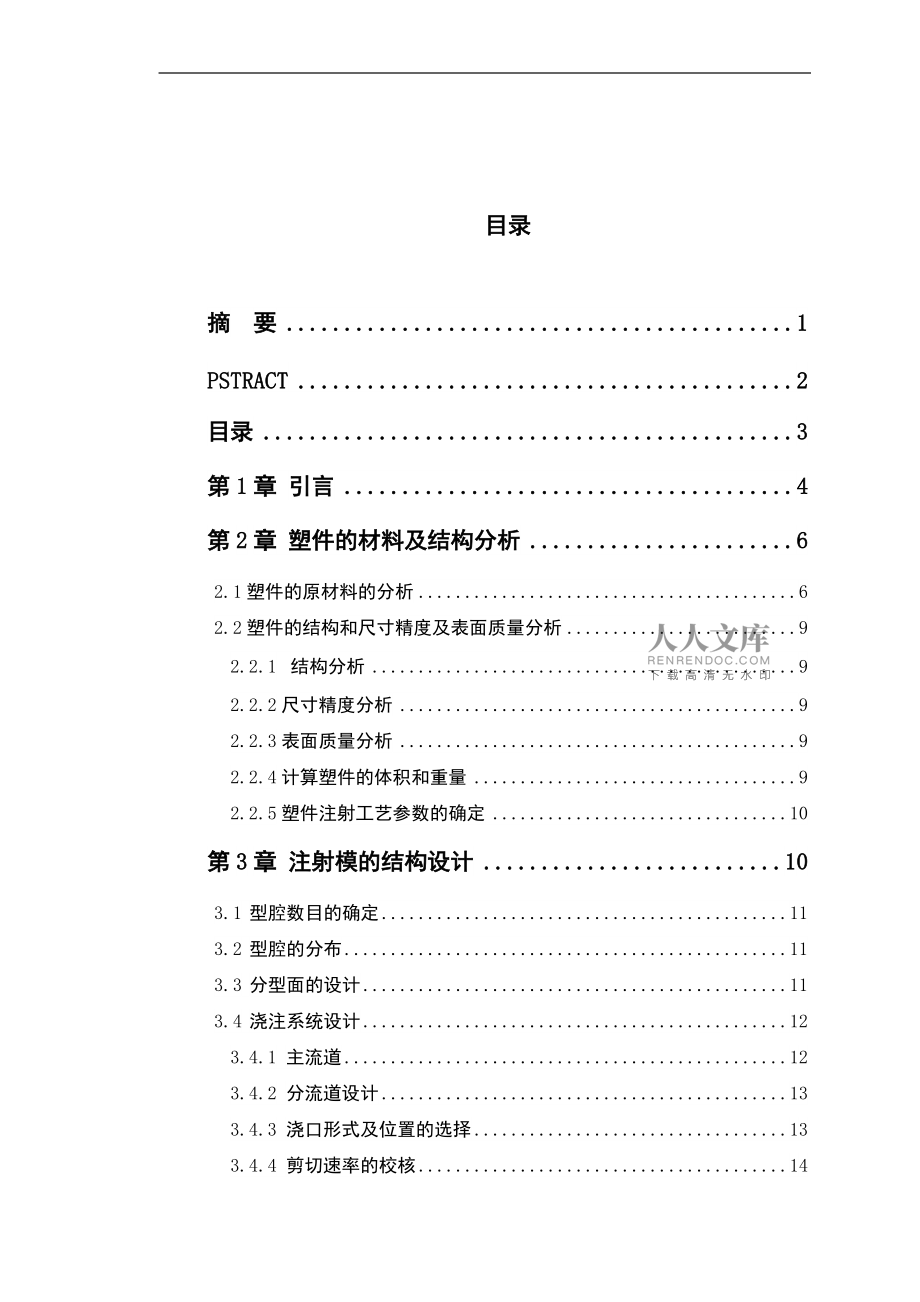



版权说明:本文档由用户提供并上传,收益归属内容提供方,若内容存在侵权,请进行举报或认领
文档简介
1、摘摘 要要本次课程设计是为了让我们能综合运用模具设计的基本理论,并结合生产实习中学到的实践知识,独立的分析和解决工艺问题,具备设计一个简单程度零件的能力和注塑模设计的基本原理和放法,完成结构设计的能力,也能熟悉和运用有关手册、图表等技术资料及编写技术文件等基本技能的一次实践。该课题从产品结构工艺性,具体模具结构出发,对模具的浇注系统、模具成型部分的结构、顶出系统、冷却系统、注塑机的选择及有关参数的校核、都有详细的设计。通过整个设计过程表明该模具能够达到此塑件所要求的加工工艺。也就是设计一副注塑模具来生产塑件产品,以实现自动化提高产量。针对塑件的具体结构,该模具是侧浇口的单分型面注射模具。通过模
2、具设计表明该模具能达到的质量和加工工艺要求。关键词:关键词:模具,注塑模,塑料模具 目录目录摘摘 要要 .1 1PSTRACTPSTRACT .2 2目录目录 .3 3第第 1 1 章章 引言引言 .4 4第第 2 2 章章 塑件的材料及结构分析塑件的材料及结构分析 .6 62.1 塑件的原材料的分析 .62.2 塑件的结构和尺寸精度及表面质量分析 .92.2.1 结构分析 .92.2.2 尺寸精度分析 .92.2.3 表面质量分析 .92.2.4 计算塑件的体积和重量 .92.2.5 塑件注射工艺参数的确定 .10第第 3 3 章章 注射模的结构设计注射模的结构设计 .1 10 03.1 型
3、腔数目的确定.113.2 型腔的分布.113.3 分型面的设计.113.4 浇注系统设计.123.4.1 主流道.123.4.2 分流道设计.133.4.3 浇口形式及位置的选择.133.4.4 剪切速率的校核.143.4.5 主流道剪切速率校核.153.4.6 浇口剪切速率的校核.153.5 成型零件结构设计.153.5.1 定模的结构设计.153.5.2 动模的结构设计.16第第 4 4 章章 模具设计的有关计算模具设计的有关计算 .1 16 64.1 型腔和型芯工作尺寸计算 .164.2 型腔侧壁厚度计算.174.3 模具加热和冷却系统的计算.184.3.1 塑料熔体释放的热量.194.
4、3.2 高温喷嘴向模具的接触传热.194.3.3 注射模通过自然冷却传导走的热量.194.44.4 模具闭合高度的确定模具闭合高度的确定.21214.4.1 由锁模力选定注射机.214.4.2 最大注塑量的校核.224.4.3 锁模力的校核.224.4.4 塑化能力的校核.22 第 5 章 绘制模具总装图 .23第第 6 6 章章 抽芯系统设计抽芯系统设计 .2 24 46.1 侧向分型与抽芯机构的分类.246.2 侧向分型与抽芯机构的设计.25第第 7 7 章章 装配运动过程装配运动过程 .2 27 7总结与展望总结与展望 .2 27 7致谢致谢 .2 28 8参考文献参考文献 .2 29
5、9第第 1 1 章章 引言引言随着中国国民经济的高速发展,各相关行业对于塑料模具需求越来越多,要求也日益提高。预计到 2005 年底,仅汽车行业就将需要各种塑料制品 36 万吨;电冰箱、洗衣机和空调的年产量均超过 1000 万台。到 2010 年,在建筑与建材行业方面,塑料门窗的普及率为 30%,塑料管的普及率将达到 50%,这些都会大大增加对模具的需求量。虽然目前中国塑料模具工业的技术水平已取得了很大的进步,但总体上与发达工业国家相比仍有较大的差距。专家认为,制造理念陈旧是其发展滞后的直接原因。加快技术进步,调 整产品结构,增加高档模具的比重,减少对进口模具的依赖,是塑料模具工业发展的方向。
6、且在未来的模具市场中,塑料模具在模具总量中的比例将逐步提高,且发展速度将高于其他模具。 未来模具设计行业的主要发展方向 近年来,全球制造业正以垂直整合的模式向中国及亚太地区转移,中国正成为世界制造业的重要基地。制造业模式的变化,必将产生对新技术的需求,也必将导致 CAD/CAM 技术的发展。从我国国情出发,认真面对模具工业发展的现状,加快模具 CAD/CAM 技术的推广,建立起一套软件开发、使用评价维护体系,形成区域规模优势,相互交流与协作,组成行业集团,尽快与国际接轨,参与国际竞争。我们有理由相信,随着中国经济的不断发展,模具行业将逐渐与国际 CAD/CAM 行业接轨,适应国 CAD/CAM
7、 的要求,创造出具有中国特色的模具设计制造模式。 目前我国塑料模具存在的问题我国塑料模具存在六大问题:塑料模具行业与其发展需要和国外先进水平相比,主要存在六个方面的问题。 (1)发展不平衡,产品总体水平较低。 (2)工艺装备落后,组织协调能力差。 (3)多数企业开发能力弱。一方面是技术人员比例低、水平不够高,另一方面是科研开发投入少,更重要的是观念落后,对开发不够重视。 (4)管理落后。 (5)供需矛盾一时还难以解决。 (6)体制和人才问题的解决尚待时日。 塑料模具分类及常见类型塑料模具分类 塑料最常见的成型方法一般分为熔体成型和固相成型两大类。 熔体成型的模具主要有注射成型、压塑成型、挤出成
8、型等。固相成型的模具主要有真空成型、压缩空气成型和吹塑成型等。 按照上述成型方法的不同,可以划分出对应不同工艺要求的塑料加工模具类型,主要有注射成型模具、挤出成型模具、压塑成型模具、吹塑成型模具、吸塑成型模具、高发泡聚苯乙烯成型模具等。 塑料注射模具:它主要是热塑性塑料件产品生产中应用最为普遍的一种成型模具塑料注射成型模具对应的加工设备是塑料注射成型机,塑料首先在注射机底加热料筒内受热熔融,然后在注射机的螺杆或柱塞推动下经注射机喷嘴和模具的浇注系统进入模具型腔塑料冷却硬化成型脱模得到制品。它是塑料制品生产中应用最广的一种加工方法。塑料挤出模具:是用来成型生产连续形状的塑料产品的一类模具。塑料压
9、缩模具:压缩成型方法是根据塑料特性将模具加热至成型温度后将计量好的压塑粉放入模具型腔和加料室闭合模具塑料在高热、高压作用下呈软粘流经一定时间后固化定型,成为所需制品形状。塑料吹塑模具:是用来成型塑料容器类中空制品的一种模具。塑料吸塑模具:是以塑料板、片材为原料成型某些较简单塑料制品的一种模具。 高发泡聚苯乙烯成型模具:是应用可发性聚苯乙烯原料来成型各种所需形状的泡沫塑料包装材料的一种模具。 塑料模的常用类型注塑模具种类很多,常见的有:注射模、压塑模、挤出模等。但以注射模最为常用。 注射模是安装在注射机上,完成注射成形工艺所使用的模具。第第 2 2 章章 塑件的材料及结构分析塑件的材料及结构分析
10、2.1 塑件的原材料的分析塑件的原材料的分析聚苯乙烯是指由苯乙烯单体经自由基加聚反应合成的聚合物,英文 聚苯乙烯名称为 Polystyrene,日文名称为,简称 PS。玻璃化温度8090,非晶态密度 1.041.06 克/立方厘米,晶体密度 1.111.12 克/立方厘米,熔融温度 240,电阻率为 10201022 欧厘米。导热系数 30时0.116 瓦/(米开)。通常的聚苯乙烯为非晶态无规聚合物,具有优良的绝热、绝缘和透明性,长期使用温度 070,但脆,低温易开裂。此外还有全同和间同立构聚苯乙烯。全同聚合物有高度结晶性。 聚苯乙烯(PS)包括普通聚苯乙烯,发泡聚苯乙烯(EPS),高抗冲聚苯
11、乙烯(HIPS)及间规聚苯乙烯(SPS) 。普通聚苯乙烯树脂为无毒,无臭,无色的透明颗粒,似玻璃状脆性材料,其制品具有极高的透明度,透光率可达 90%以上,电绝缘性能好,易着色,加工流动性好,刚性好及耐化学腐蚀性好等。普通聚苯乙烯的不足之处在于性脆,冲击强度低,易出现应力开裂,耐热性差及不耐沸水等。 普通聚苯乙烯树脂属无定形高分子聚合物,聚苯乙烯大分子链的侧基为苯环,大体积侧基为苯环的无规排列决定了聚苯乙烯的物理化学性质,如透明度高.刚度大.玻璃化温度高,性脆等。可发性聚苯乙烯为在普通聚苯乙烯中浸渍低沸点的物理发泡剂制成,加工过程中受热发泡,专用于制作泡沫塑料产品。高抗冲聚苯乙烯为苯乙烯和丁二
12、烯的共聚物,丁二烯为分散相,提高了材料的冲击强度,但产品不透明。间规聚苯乙烯为间同结构,采用茂金属催化剂生产,是近年来发展的聚苯乙烯新品种,性能好,属于工程塑料。 特点PS 一般为头尾结构,主链为饱和碳链,侧基为共轭苯环,使分子结构不规整,增 聚苯乙烯材料性能大了分子的刚性,使 PS 成为非结晶性的线型聚合物。由于苯环存在,PS 具有较高的 Tg(80105) ,所以在室温下是透明而坚硬的,由于分子链的刚性,易引起应力开裂。 聚苯乙烯无色透明,能自由着色,相对密度也仅次于PP、PE,具有优异的电性能,特别是高频特性好,次于 F-4、PPO。另外,在光稳定性方面仅次于甲基丙烯酸树脂,但抗放射线能
13、力是所有塑料中最强的。聚苯乙烯最重要的特点是熔融时的热稳定性和流动性非常好,所以易成型加工,特别是注射成型容易,适合大量生产。成型收缩率小,成型品尺寸稳定性也好。 热性能:最高工作温度为 6080。当加热至 Tg 以上,PS 转变为高弹态,且保持这种状态在较宽的范围内,这就使其热成型提供方便。PS 的热变形温度为 7080,脆化温度为-30,PS 在高真空和 330380下剧烈降解。机械性能PS 的分子量过高,加工困难,所以通常聚苯乙烯的分子量为 520 万。PS的机械性能,随温度升高,刚性(弹性模量、抗拉强度、冲击强度等下降,而断裂伸长率较大。PS 的透明性好,透光率达 8892%,仅次于丙
14、烯酸类聚合物,折射率为 1.591.60。故可用作光学零件,但它受阳光作用后,易出现发黄和混浊。PS 有主要缺点是性脆和耐热性低。对 PS 进行改性,如橡胶改性的高抗冲PS(HIPS) ;MMA-丁二烯-苯乙烯(MBS) ;A(丙烯腈)B(丁二烯)S ,在工业上应用最广泛的是 ABS 塑料。 优异、持久的隔热保温性:挤塑板,导热系数为0.028w/mk,具有高热阻、低线性膨胀率的特性。其导热系数远远低于其它 的保温材料如:EPS 板、发泡聚氨酯、保温砂浆、水泥珍珠岩等。同时由于本材料具有稳定的化学结构和物理结构,确保本材料保温性能的持久和稳定。优越的抗水、防潮性挤塑板具有紧密的闭孔结构。聚苯乙
15、烯分子结构本身不吸水,板材的正反面又都没有缝隙,因此,吸水率极低,防潮和防渗透性能极佳。 高强度抗压性:挤塑板由于发泡结构紧密相连且壁间无缝隙,所以其抗压强度极高,即使长时间水泡仍维持不变。因此用作泊车平台、机场跑道、高速公路等领域能受到良好的抗冲击性。 防腐蚀、经久耐用性:一般的硬质发泡保温材料使用几年后易产生老化,随之导致吸水造成性能下降。而挤塑板因具有优异的防腐蚀、防老化性、保温性,在高水蒸汽压力下,仍能保持其优异性能,使用寿命可达到 30-40 年。轻质、高硬度挤塑板完全的闭孔发泡结构形成轻质,而均匀的蜂窝结构造成高硬质,但又不像聚氨酯发泡、酚醛发泡那样发脆,因此不易破损,不仅搬运、安
16、装轻便,切割容易,用作屋顶保温时不会影响结构的承受能力。 高品质环保型:挤塑板不会发生分解和霉变,不会有有害物质挥发,化学性质稳定。同时在生产过程中,利用环保型原料,不产生有害气体,没有废水产生,所形成的固体下脚料,可回收处理再利用,是高品质环保型产品。成型性能无定形料,吸湿小,不须充分干燥,不易分解,但热膨胀系数大,易产生内应力。流动性较好,可用螺杆或柱塞式注射机成型。宜用高料温,高模温,低注射压力,延长注射时间有利于降低内应力,防止缩孔、变形.。 可用各种形式浇口,浇口与塑件圆弧连接,以免去处浇口时损坏塑件。脱模斜度大,顶出均匀。塑件壁厚均匀,最好不带镶件,如有镶件应预热。编辑本段聚苯乙烯
17、化学性能特点塑料检测是将塑料原料或塑料制品通过多种分离技术,利用高科技分析仪器进行检测,而后将塑料检测的结果通过经过技术人员的逆向推导,最终对完成对样品未知成分进行定性、定量判断的过程。在这个过程中技术人员除了依靠先进设备支持外,同时还必须具有丰富的行业知识和理论知识。 聚苯乙烯(PS)是一种热塑性树脂,由于其价格低廉且易加工成型,因此得以广泛应用。聚苯乙烯有均聚物(透明粒料)或增韧接枝共聚物或与弹性体的共混体(抗冲击聚苯乙烯 IPS)形式。聚苯乙烯共聚物在物理性能和热性能上比均聚物有所提高。这几类聚苯乙烯有多种品级,如标准 IPS 和标准透明品级、抗环境应力开裂品级(ESCR) 、耐紫外线级
18、。阻燃级、耐磨级、制轻质制件的高挠性品级、可发泡品级、超初级以及低残余挥发分品级等。聚苯乙烯树脂用于制造日常生活中的一次性餐具、汽车部件、包装材料、玩具、建筑材料、电器和家庭用品等。 化学和塑料检测性能: 透明 PS 粒料它是通过苯乙烯单体的加成聚合反应得到的无定形聚合物。无色、透明,光学性能极好,并有高刚性。性脆易裂、经过双轴拉伸后才较柔软和有韧性,透明 PS 的代表性能如下: 密度 105 g/cm3 拉伸强度 483MPa 弯曲强度 827MPa 典型收缩率 00045 in/in 热膨胀系数 58 X 10-5in/(inc) 伸长率 23% 维卡软化点 225F 聚苯乙烯本身耐 y
19、射线,因此 y 线照射灭菌对制品性能没有影响。聚苯乙烯溶于芳香族溶剂和某些酮类,能溶解于甲基乙基酮。透明 PS 颗粒的熔体指数范围是 125 g/10 min 或高于 25 g/10 min。它有耐热高的品级(维卡软化点达 223F) ,也有残余单体含量低的品级。2.2 塑件的结构和尺寸精度及表面质量分析塑件的结构和尺寸精度及表面质量分析2.2.12.2.1 结构分析结构分析见零件图,该零件总体形状为圆形。尺寸如图;上表面有一个圆滑曲面。就此看来,模具设计时无须设置复杂机构,该零件属于中等复杂程度。2.2.22.2.2 尺寸精度分析尺寸精度分析技术要求中提出该塑件的尺寸公差 IT3(SJ137
20、2-78) 。由以上分析可见,该零件的尺寸精度中等偏上,对应的模具相关零件的尺寸加工可以保证。2.2.32.2.3 表面质量分析表面质量分析该零件的表面要求没有缺陷、毛刺、无飞边及要有一定的光泽,没有特别高的表面质量要求,所以比较容易实现。综上分析可以看出,注射时在工艺参数控制得好的情况下,零件的成型要求可以得到保证。2.2.42.2.4 计算塑件的体积和重量计算塑件的体积和重量计算塑件重量是为了选用注射机及确定模具型腔数。根据设计手册可查得 PS 的密度为 =1.05g/cm成型收缩率成:0.30.8% 成型温度:180200。计算塑件的体积:V=9.262cm(通过三维软件计算得到)计算塑
21、件重量:W=V9.262cm1.05g/cm=9.7g考虑到塑件结构不太复杂,需求量中等固采用一模 2 件的模具结构,考虑其外形尺寸、注射时所需压力和工厂现有的设备等情况,初步选用注射机为 SZ-200/60。2.2.52.2.5 塑件注射工艺参数的确定塑件注射工艺参数的确定查找塑料模设计手册和参考工厂的实际应用的情况,PS 的成型工艺参数可作如下选择。试模时,可根据实际的情况作适当的调整。注塑机类型螺杆式 螺杆转速/(r/min)400喷嘴形式/温度 直通式170180料筒温度/78前段180200中段 165180后段150170模具温度/5080注射压力/mpa 60100保压力/mpa
22、3050注射时间/s2090高压时间/s 05冷却时间/s20120成型周期/s50200第第 3 3 章章 注射模的结构设计注射模的结构设计注射模结构设计主要包括:分型面选择、模具型腔数目的确定及型腔的排列方式和冷却水道布局以及浇口位置设置、模具工作零件的结构设计、侧向分型与抽芯机构的设计、推出机构的设计等内容。3.1 型腔数目的确定型腔数目的确定该塑件精度要求不高,但需求量中等,固应选多腔模更为合适。它可以提高生产效率,降低塑件的整体成本。生产经验表明,每增加一个型腔,塑件的尺寸精度将降低 4%。按注射机的最大注射量计算型腔数目 型腔数目 nn(Kmp-m1)/m式中 K:注射机最大注射量
23、的利用系数,取 0.8mp:注射机最大注射量,gm1:浇注系统凝料量,gm:单个塑件的质量,g经过估算得 n 取 2,采用一模 2 件的形式。3.2 型腔的分布型腔的分布由于型腔的排布与浇注系统密切相关的,所以在模具设计时应综合加以考虑。型腔的排布应使每个型腔都能通过浇注系统从总压力中均等地分得所需的足够压力,以保证塑料熔体能同时均匀地充填每个型腔,从而使各个型腔的塑件内在质量均一稳定。3.3 分型面的设计分型面的设计模具设计中,分型面的选择很关键,它决定了模具的结构。分型面与模具的整体结构、浇注系统的设计、塑件的脱模和模具的制造工艺等有关,因此分型面的选择是注射模设计中的一个关键步骤。应根据
24、分型面选择原则和塑件的成型要求来选择分型面。该塑件表面质量无特殊要求,结构也比较简单,固选平直分型面。如图 3 如何确定分型面,需要考虑的因素比较复杂。由于分型面受到塑件在模具中的成型位置、浇注系统设计、塑件的结构工艺性及精度、嵌件位置形状以及推出方法、模具的制造、排气、操作工艺等多种因素的影响,因此在选择分型面时应综合分析比较,从几种方案中优选出较为合理的方案。选择分型面时一般应遵循以下几项原则:(1)分型面应选在塑件外形最大轮廓处。(2)便于塑件顺利脱模,尽量使塑件开模时留在动模一边。(3)保证塑件的精度要求。(4)满足塑件的外观质量要求。(5)便于模具加工制造。(6)对排气效果的影响。3
25、.4 浇注系统设计浇注系统设计浇注系统是指模具中由注射机喷嘴到型腔之间的进料通道。普通浇注系统一般由主流道、分流道、浇口和冷料穴等四个部分组成。浇注系统的设计是模具设计的一个重要环节,设计合理与否对塑件的性能、尺寸、内外部质量及模具结构、塑料的利用率等有较大的影响。对浇注系统进行设计时,一般应遵循如下基本原则。(1).了解塑件的成型性能(2).尽量避免或减少产生熔接痕(3).有利于型腔中气体的排出(4).防止型芯的变形和嵌件的位移(5).尽量采用较短的流程充满型腔(6).流动距离比和流动面积比的校核3.4.13.4.1 主流道主流道主流道是指浇注系统中从注射机喷嘴与模具接触处开始到分流道为止的
26、塑料熔体的流动通道,是熔体最先流经模具的部分,它的形状与尺寸对塑料熔体的流动速度和充模时间有较大的影响,因此必须使熔体的温度降和压力损失最小。根据设计手册查得注射机喷嘴的有关尺寸:喷嘴前端孔径:;mmd40喷嘴前端球面半径:;mmR120根据模具主流道与喷嘴的关系R=mmR10mmdd5 . 00取主流道球面半径 R=13mm;取主流道的小端直径 d=4.5mm.为了便于将凝料从主流道中拔出,将主流道设计成圆锥形,其锥度为,02经换算得大端直径 D=8.5mm。为了使熔料顺利进入分流道,可在主流道出料端设计半径 r=3mm 的圆弧过渡。3.4.23.4.2 分流道设计分流道设计分流道是指主流道
27、末端与浇口之间的一段塑料熔体的流动通道。分流道的作用是改变熔体流向,使其以平稳的流态均衡地分配到各个型腔。设计时应注意尽量减少流动过程中的热量损失与压力损失。分流道的形状及尺寸,应根据塑件的体积、壁厚、形状的复杂程度、注射速率、分流道长度等因素来确定。本塑件的形状不算太复杂,熔料填充型腔比较容易。根据型腔的放置方式可知分流道的长度不长,为了便于加工起见,选用形状为圆形分流道,查塑料模设计手册得 R=3mm。塑料迅速冷却,只有内布的熔体流动比较理想,因此分流道表面粗糙度一般取1.6mmaR3.4.33.4.3 浇口形式及位置的选择浇口形式及位置的选择浇口亦称进料口,是连接分流道与型腔的熔体通道。
28、浇口的设计与位置的选择恰当与否,直接关系到塑件能否完好、高质量地注射成型。浇口可分成限制性浇口和非限制性浇口两大类。按浇口的结构形式和特点,常用的浇口可分为以下几种形式。(1).直接浇口(2).中心浇口(3).侧浇口(4).环形浇口(5).轮辐式浇口(6).爪形浇口(7).侧浇口(8).侧浇口按此零件对外表面的要求:该零件的表面要求没有明显的缺陷、毛刺、无飞边及要有一定的光泽。模具设计时,浇口的位置及尺寸要求比较严格,初步试模后还需进一步修改浇口尺寸,无论采用何种浇口,其开设位置对塑件成型及质量影响很大,因此合理选择浇口的开设位置是提高质量的重要环节,同时浇口位置的不同还影响模具结构。总之要使
29、塑件具有良好的性能与外表,一定要认真考虑浇口位置的选择,通常要考虑以下几项原则:(1)浇口应开设在塑件壁厚最大处。(2)必须尽量减少熔接痕。(3)应有利于型腔中气体排出。(4)考虑分子定向影响。(5)避免产生喷射和蠕动。(6)浇口处避免弯曲和受冲击载荷。(7)尽量缩短流动距离。综合以上分析,浇口选择侧浇口位置见图 4。图 4 浇口的位置3.4.43.4.4 剪切速率的校核剪切速率的校核生产实践表明,当注射模主流道和分流道的剪切速率 R=、浇口的剪切速率 R=时,所成型的塑件质量最132105108 . 5S5410101S好。对一般热塑性塑料,将以上推荐的剪切速率值作为计算依据,可用以下经验公
30、式表示: 33 . 3RqRv式中 q 体积流量(CM /S) ;R 浇注系统断面当量半径v33n(CM) 。3.4.53.4.5 主流道剪切速率校核主流道剪切速率校核Q=0.8Q/T =338.21.5=225.5 (CM /S)主v公3 T 注射时间:T=2.5(S) ; R 主流道的平均当量截面半径:R =0.538(CM) nn421dd d 主流道小端直径 , d =0.63 (CM) ; d主流道大端直径,112d=1.2(CM)2R= 3.1158.9/(3.140.2783)=1.4710 S主33 . 3nvRq31510 1.4710 510 (满足条件)2333.4.63
31、.4.6 浇口剪切速率的校核浇口剪切速率的校核R= =3.67152/(3.140.423)=1.45103 S浇33 . 3nvRq1其中:浇口面积 S=/4(D22-D12),当量面积 S=R 所以 R=7mm。 2当n当n单从计算上看,交口剪切速率偏小。但由于模具比较特殊,为一模 2 腔,无分流道,压力损失少,进料速度快,成型比较容易, ,传递压力好,所以浇口的剪切速率是合适的。从以上的计算结果看,流道与浇口剪切速率的值都落在合理的范围内,证明流道与浇口的尺寸取值是合理的。3.5 成型零件结构设计成型零件结构设计3.5.13.5.1 定模的结构设计定模的结构设计根据模具的结构形式,考虑加
32、工的难易程度和材料的价值利用等因素,定模的结构很简单,加工没有特别的困难,所以定模芯采取整体式结构,其结构见总装图。3.5.23.5.2 动模的结构设计动模的结构设计成型塑件内表面的零件称凸模或型芯,主要有主型芯、小型芯、螺纹型芯和螺纹型环等。对于结构简单的容器、壳、罩、盖之类的塑件,成型其主体部分内表面的零件称主型芯或凸模,而将成型其他小孔的型芯称为小型芯或成型杆。主型芯的结构设计按结构主型芯可分为整体式和组合式两种组合式结构:为了便于加工,形状复杂型芯往往采用镶嵌组合式结构。这种构是将型芯单独加工后,再镶入模板中。所以我们采取动模型芯采取组合式结构,将型芯割开以便加工。其凸模型芯凹模的结构
33、形式另见模具总装图。第第 4 4 章章 模具设计的有关计算模具设计的有关计算本成型零件工作尺寸计算时均采用平均尺寸、平均收缩率、平均制造公差和平均磨损量来进行计算。查表得 PS 收缩率为 Q=0.30.8%,故平均收缩率为Qcp=(0.3+0.8)%/2=0.55%,考虑到工厂模具制造的现有条件,模具制造公差取 z=/3。4.1 型腔和型芯工作尺寸计算型腔和型芯工作尺寸计算(1)型腔径向尺寸 已知在规定条件下的平均收缩率 S,塑件的基本尺寸 Ls 是最大的尺寸,其公差为负偏差。塑件基本尺寸,查表得mmLs361,即故:09. 0103. 01zzcpssMSLLL431 =03. 009. 0
34、430055. 03636 =03. 00134.36(2)型芯的径向尺寸 塑件基本尺寸,查表得mmLs10203. 0,09. 0z2故 zcpssmSLLL432 =03. 0343.10 4.2 型腔侧壁厚度计算型腔侧壁厚度计算 (1)凹模型腔侧壁厚度计算凹模型腔为组合式型腔,按强度条件计算公式SR-r=r(/-2p)1/2-1 进行计算。式中各参数分别为:p=50Mpa(选定值);=0.05mm;=160MPar=28mmSR-r=r(/-2p)1/2-1=28(160/160-250)1/2-116.8mm一般在加工时为了加工方便,我们通常会取整数,所以凹模型腔侧壁厚度为 17。(2
35、)凹模底板厚度计算按强度条件计算,型腔地板厚为:p=50 Mpar=28mm=160MPah1.22pr2/1/21.2250282/1601/217.3mm一般在加工时为了加工方便,我们通常会取整数,所以凹模型腔侧壁厚度为 18mm。4.3 模具加热和冷却系统的计算模具加热和冷却系统的计算本塑件在注射成型时不要求有太高的模温因而在模具上可不设加热系统,是否需要冷却系统可作如下设计计算。设定模具平均工作温度为 60C,用常温 20C 的水作为模具冷却介质,其出口温度为 25C,产量为(初算每 1min1 套)1.05kg/h。塑料树脂传给模具的热量与自然对流散发到空气中的模具热量、辐射散发到空
36、气中的模具热量及模具传给注射机热量的差值,即为用冷却水扩散的模具热量。假如塑料树脂在模内释放的热量全部由冷却水传导的话,即忽略其他传热因素,那么模具所需的冷却水体积流量则可用下式计算。根据体积流量的公式得:qv=Mq/60c(1-2)=(1.252.5)/604.451(25C-20C)=0.35m3/minQv:冷却水体积流量,m3/minM:单位时间注射入模具内的树脂质量,kg/hQ:单位时间内树脂在模具内释放的热量,J/kgC:冷却水的比热容,J/(kg.k):冷却水的密度,kg/m31:冷却水出口处温度,C2:冷却水入口处温度,C由体积流量 qv 查设计手册可知所需的冷却水管直径为 6
37、mm。4.3.14.3.1 塑料熔体释放的热量塑料熔体释放的热量Q =nG C (t t )1S10=60236.2101.65(22060)3=3365.02KJ/h式中:n每小时注射次数, n=60 (次) ;G每次的注射量(KG), G=217.610;3C 塑料的比热容(KJ/KG),C =1.9;SSt 熔融塑料进入型腔的温度,t =220;11t 塑件脱模温度,t =60。004.3.24.3.2 高温喷嘴向模具的接触传热高温喷嘴向模具的接触传热Q =3.6A(t t )2Z12=3.6415310130(22050)6=325.12 KJ/h式中:A 注塑机的喷嘴头与模具的接触面
38、积(m ) ,Z2A =406910m (A =4R =43.1418 =406910m ,R=18mm 注塑机Z62Z2262喷嘴球半径, ) ;金属传热系数 =140(W/ m);2t 模具平均温度 t =50 ;22t 熔融塑料进入型腔的温度 t =220。114.3.34.3.3 注射模通过自然冷却传导走的热量注射模通过自然冷却传导走的热量Q=hA ( t t )对1m2343=5.760.12(5020)43=104KJ/h 式中:h 传热系数(KJ/ m h ) ,h =4.15(h =4.27(0.25+1211)= 4.27(0.25+)= 6.15) ;2360300t 36
39、050300A 两个分型面和四个侧面的面积 m2,A =0.203【A =(A)+ (A)mmm1m2mnk = 0.075+0.350.78=0.41,A=2BL=225023010=0.081m ; A1m62=4BH =422025010=0.22m ) ;2m62t 模具平均温度,t =50;22t 室温,t =20。33Q=20.8 A() () 辐2m2273100t43273100t4=20.80.220.8() () 273501004273201004=128.7 KJ/h式中: 辐射率,一般表面=0.80.9;A=0.22; 2mQ=hA( t t )h台2接232= 51
40、20.0274(5030)=453.94 KJ/h式中:传热系数h =502KJ/(mh );22 A 模具与工作台的接触面积 m ,A=0.0484;接2接从计算的结果看,工作台散发的热量比塑料熔体释放的热量还多,这显然是不正确的,说明了 Q的计算结果错误。这是因为有关 Q的计算参考资料很台台少,计算中有很多地方不规范。简单的计算以塑料熔体释放出的热量 Q 为总热1量,这些热量全部由冷却介质带走,这些热量应分别由凹模和型芯的冷却系统带走,实验表明,约 1/3 的热量被凹模带走,其余由型芯带走。模具应由冷却系统带走的热量:Q=(Q + Q )(Q+ Q+ Q)冷12对辐台由于现在无法得到 Q的
41、正确值,所以计算以简单计算原则,取 Q= Q 。台总14.44.4 模具闭合高度的确定模具闭合高度的确定图 8 总装图因而模具的闭合高度:H=H1+H2+H3+H4+H5+H6+H7331mm4.4.14.4.1 由锁模力选定注射机由锁模力选定注射机F锁F胀=A分P型 =P型24D=1/43286.22 (KN)式中 F锁:注射机的锁模力(N) ; A分:塑件和浇注系统在分型面上的投影面积之和;P型:型腔压力,取P型=25MP ; D取的是塑件的最大直径。a结合上面两项的计算,初步确定注塑机为国产注射机SZ-200/60,其主要技术参数如下表所示。表 2-1 注射机参
42、数型号SZ-200/60螺杆直径(mm)35注射容量(cm3或 g)200注射压力(N/cm3)150锁模力 (KN)600最大注射面积(cm2)14.05模具厚度(mm)170300模板行程(mm)300喷嘴球半径(mm)10喷嘴孔直径(mm)4喷嘴伸出量(mm)20顶出行程(mm)80外形尺寸(m * m * m)3.9 X 1.3 X 1.84.4.24.4.2 最大注塑量的校核最大注塑量的校核为确保塑件质量,注塑模一次成型的塑件质量(包括流道凝料质量)应在公称注塑量的 35%75%范围内,最大可达 80%,最小不小于 10%。为了保证塑件质量,充分发挥设备的能力,选择范围通常在 50%
43、80%。 满足要求。4.4.34.4.3 锁模力的校核锁模力的校核 在确定了型腔压力和分型面面积之后,可以按下式校核注塑机的额定锁模力: FK AP分型 1.351/43288.22KN因此锁模力满足要求。式中 :F 注塑机额定锁模力:1600KN; K 安全系数,取 K=1.2; 4.4.44.4.4 塑化能力的校核塑化能力的校核由初定的成型周期为 60 秒计算,实际要求的塑化能力=成型周期每次实际注射量即:226.3/60=7.5(g/s) ,远小于注塑机的塑化能力 22.2(g/s) ,说明注射机能完全满足塑化要求。 第第 5 5 章章 绘制模具总装图绘制模具总
44、装图本模具的总装图如图所示,其工作原理:模具安装在注射机上,定模部分固定在注射机的定模板上,动模部分固定在注射机的动模板上。合模后,注射机通过喷嘴将熔料经流通注入型腔,经保压,冷却后塑件成型。开模时动模部分随动板一起运动渐渐将分型面打开,当分型面打开完毕后,凝料从上模中脱出,在注塑机顶杆的作用下,顶杆通过推件板将塑件和凝料系统顶出,与此同时由于采用的是侧浇口,在顶出的瞬间,塑件和凝料分开。此时塑件自动脱落,实现全自动脱模。合模时,随着分型面的闭合复位杆将顶杆复位,模具闭合,等待下一次的动作。图 9 总装图第第 6 6 章章 抽芯系统设计抽芯系统设计侧向分型与抽芯机构用来成形制品侧壁的内外侧孔和
45、凹槽,该类机构活动零件多,动作复杂,为保证该机构能可靠,灵活和高效地工作,它们应具有以下基本功能:a.在保证不引起塑件变形的情况下准确的抽芯和分型;b.运动灵活,动作可靠;c.具有必要的强度和刚度;d.配合间隙和拼缝线不溢料;这样既保证塑件必要的尺寸精度,又可以保证模具具有较长的工作寿命。此外,侧向分型和抽芯机构结构比较复杂,设计时应充分考虑制造和装配的难易程度。6.1 侧向分型与抽芯机构的分类侧向分型与抽芯机构的分类侧向分型与抽芯机构类型很多,按动力来源可分为三种:a.机动侧抽芯借助注塑机的开模力或顶出力进行模具的侧向分型与抽芯,该机构经济性好,实用性强,效率高,动作可靠,故应用最广泛。机动
46、抽芯按结构形式可分为下列几种:(1)斜导柱分型抽芯分型抽芯;(2)弹簧分型抽芯;(3)斜滑块分型抽芯;(4)弯销分型抽芯;(5)齿轮齿条分型抽芯;(6)其他形式抽芯机构;其中尤以斜导柱分型抽芯机构最为常用。b.液压侧抽芯借助液压装置进行模具的侧向分型与抽芯及其复位,特点是抽拔距离长,但动作灵活,常在大型注塑模具中使用。c.手动侧抽芯采用手动侧抽芯的模具结构简单,其效率低,劳动强度大,抽拔力有限,只在特殊情况下使用。6.2 侧向分型与抽芯机构的设计侧向分型与抽芯机构的设计本设计采用斜导柱分型斜导柱抽芯机构由斜导柱,滑块,侧型芯,压紧块及滑块定位装置等组成,其特点是结构紧凑,制造方便,动作安全可靠
47、。故其应用较广,特别是在抽芯距离较短和抽拔力不太大的情况下更为适用。斜导柱抽芯机构主要由开模力通过斜导柱作用于滑块上的分力驱动其朝一定的方向运动。a.斜导柱设计:计算抽拔力:(5-1)09.8QuChP式中 Q抽拔力(N) ;u塑料对金属的摩擦系数,u=0.3;C型芯成型部分断面的平均周长() ;h型芯被塑料包紧部分的长度() ;P0塑料对型芯单位面积的包紧力(/2) ;一般取 P0=80120/2。代入数据得:Q=698(N)计算抽芯距:S=S1+23式中 S抽芯距()S1取出塑件的最小尺寸()代入数据得 S=16.5+2=18.5斜导柱倾角:斜导柱的倾角越小,斜导柱受力状况越好,由于抽芯距
48、大,因此取倾斜角 a=20。斜导柱直径:根据抽拔力 Q 和倾斜角 a 由表查得斜导柱直径 d=16。斜导柱长度: costan(10 15)11822sinDdSLTanahaamma (5-2)斜导柱其固定的模板之间采用过渡配合 H7/m6。斜导柱与滑块上斜道孔之间可以采用较松的间隙配合 H11/b11。b.导滑槽设计斜导柱驱动滑块是沿着导滑槽移动的,故对导滑槽提出如下要求:1)滑块在导滑槽内运动要平稳,无上下窜动和卡紧现象;2)滑块与导滑槽间应上,下与左,右各有一对平面呈过度配合,配合精度可选 H7/e6,其余各面均应留有间隙;3)导滑槽应有足够的硬度(HRC52HRC56)c.楔紧块设计
49、:楔紧块的作用:1)注射时,型腔里的塑料熔体以很高的压力作用在侧型芯上,特别是当侧型芯的面积较大时,将产生一个很大的侧推力。这个力通过滑块传给斜导柱,会使斜导柱产生弯曲变形。因为计算斜导柱直径时只考虑了抽拔力的影响并未将这个侧推力的影响估计在内,因此必须另加闭锁装置即压紧块来承受这个侧推力。2)由于斜导柱与滑块的配合间隙较大,故合模后靠斜导柱不能保证滑块的精确位置。侧型芯的准确位置要靠精确加工的压紧块来保证。设计要点:压紧块的斜角应略大于斜导柱的倾斜角,一般 a 大于斜导柱倾斜角 2030.d.滑块设计滑块分为整体式和组合式,本设计采用的是整体式,即在滑块上直接制出側向型芯,整体式结构简单,配
50、合精度高.第第 7 7 章章 装配运动过程装配运动过程模具安装在注射机上,定模部分固定在注射机的定模板上,动模部分固定在注射机的动模板上。合模后,注射机通过喷嘴将熔料经流通注入型腔,经保压,冷却后塑件成型。开模时动模部分随动板一起运动渐渐将分型面打开,同时斜导柱带动滑块侧向运动,当分型面打开完毕后,凝料从上模中脱出,在注塑机顶杆的作用下,通过推板将塑件和凝料系统顶出,与此同时由于采用的是侧浇口,在开模的瞬间,塑件和凝料分开。此时塑件自动脱落,实现全自动脱模。合模时,随着分型面的闭合复位杆将顶杆复位,模具闭合,等待下一次的动作。 总结与展望总结与展望当今制造业正向着数字化、全球化、网络化的方向发展,产品的生命周期越来越短,新产品的上市速度越来越快。模具是制造业的基本工艺设备,模具设计及制造效率对产品的开发效率有着决定性的影响
温馨提示
- 1. 本站所有资源如无特殊说明,都需要本地电脑安装OFFICE2007和PDF阅读器。图纸软件为CAD,CAXA,PROE,UG,SolidWorks等.压缩文件请下载最新的WinRAR软件解压。
- 2. 本站的文档不包含任何第三方提供的附件图纸等,如果需要附件,请联系上传者。文件的所有权益归上传用户所有。
- 3. 本站RAR压缩包中若带图纸,网页内容里面会有图纸预览,若没有图纸预览就没有图纸。
- 4. 未经权益所有人同意不得将文件中的内容挪作商业或盈利用途。
- 5. 人人文库网仅提供信息存储空间,仅对用户上传内容的表现方式做保护处理,对用户上传分享的文档内容本身不做任何修改或编辑,并不能对任何下载内容负责。
- 6. 下载文件中如有侵权或不适当内容,请与我们联系,我们立即纠正。
- 7. 本站不保证下载资源的准确性、安全性和完整性, 同时也不承担用户因使用这些下载资源对自己和他人造成任何形式的伤害或损失。
最新文档
- 低压电器 课件 单元二 项目二 任务一 刀开关、组合开关的使用
- 内蒙古满洲里市重点中学2024-2025学年初三下学期4月模拟物理试题含解析
- 四川省宜宾市翠屏区中学2024-2025学年中考英语试题:考前冲刺打靶卷含答案
- 邵阳市大祥区2025年三下数学期末学业水平测试试题含解析
- 华中师范大学《药理学》2023-2024学年第一学期期末试卷
- 私立华联学院《人机交互的软件工程方法》2023-2024学年第二学期期末试卷
- 上海市市西中2025年高考物理试题查漏补缺试题含解析
- 汕尾职业技术学院《现代审计学双语》2023-2024学年第二学期期末试卷
- 内蒙古鄂托克旗乌兰镇中学2025届初三生物试题期末试题含解析
- 云南交通职业技术学院《桥梁工程(二)》2023-2024学年第二学期期末试卷
- 教务处教学教案作业检查记录表
- 电梯设备故障记录表
- 血透室传染病登记本
- DB50∕T 341-2009 城乡社区消防安全管理规范
- 干粉灭火器点检记录表(样表)
- 伍光和自然地理学4版知识点总结课后答案
- 手压式手电筒设计(棘轮机构及电路设计)
- 滇10J6-1住宅厨房、卫生间烟气道及管道井构造图集
- 华中科技大学版五年级信息技术教案
- 600MW超临界锅炉给水控制系统分析
- 固定收益研究报告透过x系统看银行间交易未来发展
评论
0/150
提交评论