



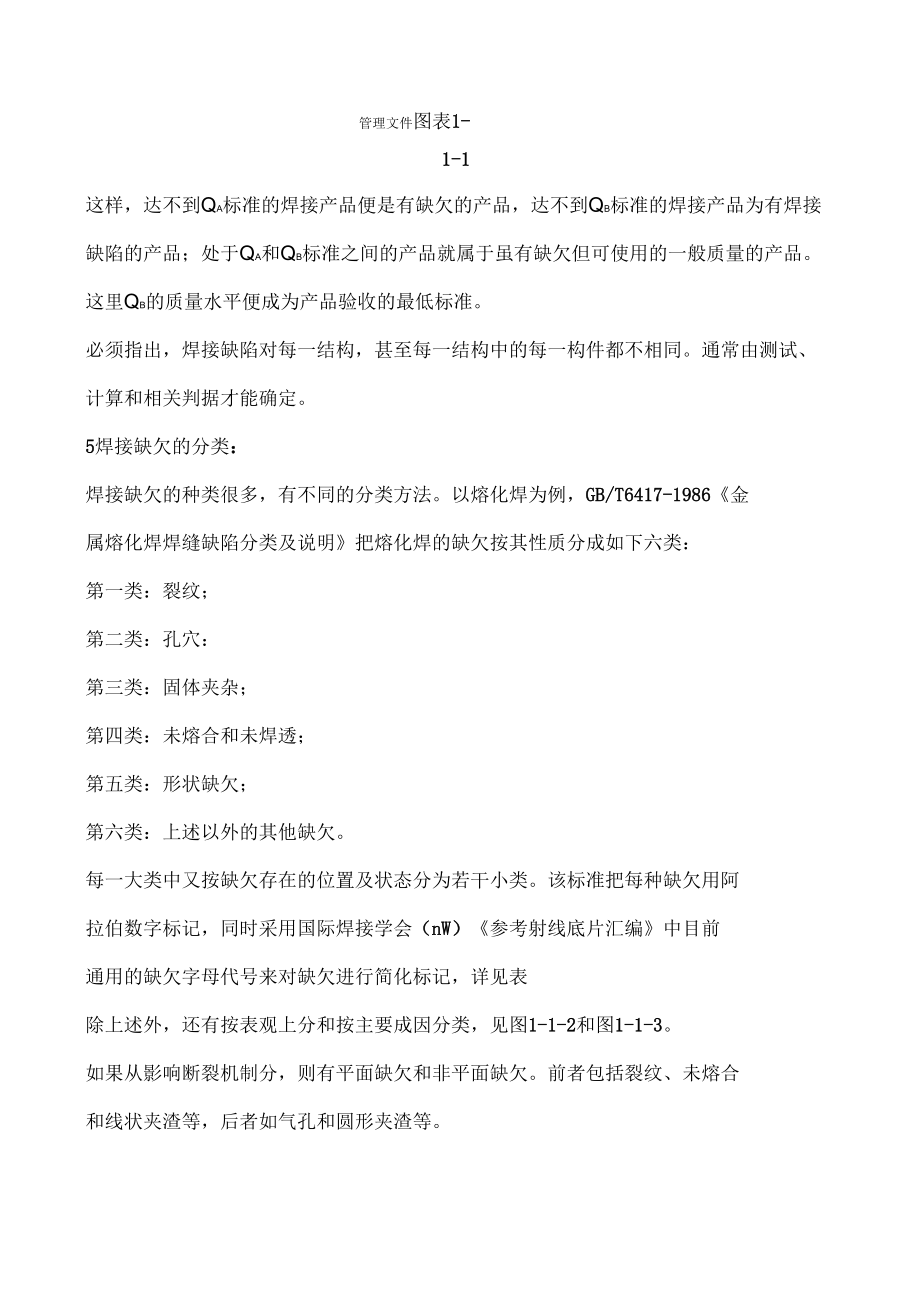
版权说明:本文档由用户提供并上传,收益归属内容提供方,若内容存在侵权,请进行举报或认领
文档简介
1、管理文件1范围本规程规定公司焊接件的质量检验的类别、检验项目、检验方法、检验抽样规定及质量的评定与对检验员的工作要求,是焊接检验人员进行质量检验的指导性文件。本规程适应于公司的所有焊接零件。2产品检验的依据在检验工作中,确定产品制造过程的检验内容、方式和方法时必须有依据;当检测结果出来后,评定该制造环节是否符合质量要求时,或者制订验收标准时,也需要有依据。这些依据是:(1)产品的施工图样图样规定了产品加工制造后必须达到的材质特性、几何特性(如形状、尺寸等)以及加工精度(如公差等)的要求。(2)技术标准包括国家的、行业的或企业的有关标准和技术法规。在这些标准或法规中规定了产品的质量要求和质量评定
2、的方法。(3)产品制造的工艺文件如工艺规程等,在这些文件中根据工艺特点提出必须满足的工艺要求。(4)订货合同在订货合同中有时对产品提出附加要求,作为图样和技术文件的补充规定,同样是制造和验收的依据。管理文件3焊接检验方法分类:类别特点内容破坏性检验检验过程中必须破坏被检的对象结构力学性能检验包括:拉伸、驾曲、冲击、硬度、疲劳、韧度等试验化学分析与试验化学成份分析;晶间腐蚀试验;铁素体含量测定金相与断口的分析试验宏观组织分析;微观组织分析;断口检验与分析非破坏性检验检验过程中不破坏被检对象的结构和材料外观检验包括:母材、焊材、破口、焊缝等表面质量检验,成品或半成品的外观几何形状和尺寸的检验强度试
3、验水压强度试验、气缸强度试验致密性试验气密性试验、吹气试验、载水试验、水冲试验、沉水试验、煤油试验、渗透试验、氮检试验无损检测试验射线探伤;超声波探伤;磁粉探伤;渗透探伤;涡流探伤工艺性检验在产品制造过程中为了保证工艺的正确性而进行的检验材料焊接性试验:焊接工艺评定试验;焊接电源检查;工艺装备检验;辅机及工具检验;结构的装配质量检验;焊接工艺参数检验;预热、后热及焊后热处理检验4焊接缺欠及其分类:焊接结构在制作过程中受各种因素影响,生产出每一件产品都不可能完美无缺。不可避免地产生焊接缺欠,它的存在不同程度上影响到产品的质量和安全使用。焊接检验目的之一就是运用上述各种检验方法把焊件上产生的各种缺
4、欠检查出来,并按有关标准对它进行评定,以决定对缺欠的处理。1.焊接缺欠与焊接缺陷焊接检监规范管理文件缺欠与缺陷本无原则区别,均表征产品不完整或有缺损。但对于焊接结构而言,基于合于使用准则,有必要对缺欠和缺陷赋予不同的涵义。在焊接接头中的不连续性、不均匀性以及其他不健全等的欠缺,统称焊接缺欠。不符合焊接产品使用性能要求的焊接缺欠,称焊接缺陷。也就是说,焊接缺陷是属于焊接缺欠中不可接受的那一种缺欠,该缺欠必须经过修补产品才能使用,否则就是废品。判别焊接缺陷的标准是焊接缺欠的容限。国际焊接学会(nW第V委员会从质量管理角度提出了两个质量标准Qa和Qb',见图1-1-1。Qa是用于正常质量管理
5、的质量水平,它是生产厂家努力目标,必须按Qa进行管理生产。Qa也是用户的期望标准;Qb是根据合于使用准则确定出反映缺欠容限的最低的质量水平,只要产品质量不低于Qb水平,该产品即使有缺欠,也能满足使用要求,不必返修就可投入使用。如果达不到Qb的质量水平,则该产品所存在的缺欠只能经修补处理后才能使用,否则报废。质量一般,不必修补管理文件图表1-1-1这样,达不到Qa标准的焊接产品便是有缺欠的产品,达不到Qb标准的焊接产品为有焊接缺陷的产品;处于Qa和Qb标准之间的产品就属于虽有缺欠但可使用的一般质量的产品。这里Qb的质量水平便成为产品验收的最低标准。必须指出,焊接缺陷对每一结构,甚至每一结构中的每
6、一构件都不相同。通常由测试、计算和相关判据才能确定。5焊接缺欠的分类:焊接缺欠的种类很多,有不同的分类方法。以熔化焊为例,GB/T6417-1986金属熔化焊焊缝缺陷分类及说明把熔化焊的缺欠按其性质分成如下六类:第一类:裂纹;第二类:孔穴:第三类:固体夹杂;第四类:未熔合和未焊透;第五类:形状缺欠;第六类:上述以外的其他缺欠。每一大类中又按缺欠存在的位置及状态分为若干小类。该标准把每种缺欠用阿拉伯数字标记,同时采用国际焊接学会(nW)参考射线底片汇编中目前通用的缺欠字母代号来对缺欠进行简化标记,详见表除上述外,还有按表观上分和按主要成因分类,见图1-1-2和图1-1-3。如果从影响断裂机制分,
7、则有平面缺欠和非平面缺欠。前者包括裂纹、未熔合和线状夹渣等,后者如气孔和圆形夹渣等。6产生焊接缺欠的原因分析:构造缺欠冶金缺欠构造不连续缺口效焊缝布置不良引起的应力与变形焊脚尺寸不合适裂纹气孔夹杂物性能恶化图表1-1-3按表观上的缺欠分类管理文件7焊接检验类别a)焊前检验;b)焊接过程检验;c)焊后成品检验。7.1 焊接检验的项目、检测内容与检测方法项目检验内容检验方法焊条外观质量用目测药皮是否牢固,紧贴在焊芯上并有f强度。药皮应无裂纹、气孔肿涨和未调匀的药团。外观检查后核实焊条型号、规格。焊丝焊丝直径、外观质量用目测焊丝应无氧化皮、锈、油污。用卡尺检查焊丝直径施焊焊件a待焊件焊接部位不许有锈
8、、油漆、氧化物、毛刺和影响焊接的镀层;b焊接坡口处边缘应均匀一致,坡口开头和尺寸应符合图样要求;c暂焊点分布合理,不能分布在应力集中处;d暂焊点不允许有烧穿、裂纹、未焊透和气孔等缺陷,如发现这些缺陷应在焊接前排除a目测b对坡口尺寸、形状按图样要求用标准样板或焊接检验尺测量。c目测d目测管理文件7.2 焊接过程检验焊件的首件应进行首检,在焊接过程中还应对焊接设备运行情况、焊接规范进行检验。焊接多层焊时,每焊完一道焊缝要进行质量检查和精渣检验。同时对已焊的零件进行抽检,及时发现问题,及时解决。项目检验内容检验方法外观检查1.焊缝尺寸是否符合图样要求,焊缝表面后元裂纹等/、允许的缺陷;2外观质量1.
9、1 .万能量规,检测焊缝尺寸;低倍放大镜检验外观缺陷;2.2 .目测7.3焊后成品检验项目检验内容检验方法外观检查外观质量目测内部质量(必要时)检查焊缝内部是否启裂纹、未熔合、气孔、夹渣等缺陷;试压热熔釜、油箱、储罐等对焊缝进行致密性检验煤油试验、气压试验、载水试验、吹起试验煤油试验煤油试验使用于敞开的容器和储存液体的储器以及同类其他产品的密封性检验。试验时在便于观察和焊补的一面,涂以白垩粉,待干,然后在焊缝另一面以煤油,试验过程中涂23次。持续15min3h。涂油后立即开始观察白垩粉一侧,如在规定时间内,焊缝表面未出现油斑和油带,即定合格。碳钢和低合金钢做煤油试验所需时间推存值见表:管理文件
10、碳钢和低合金钢做煤油试验所需时间推存值板厚/mm时间/min备注<520当煤油透漏至其他位置时,煤油作用时间可适当增加51035101545>1560载水试验使用于不受压的容器或敞门焊接储器的密封性试验。试验时,仔细清理容器焊缝表面,并用压缩空气吹净、吹干。在气温不低于0c的条件下,在容器内灌入温度不低于5c的净水,然后观察焊缝,期待时间不的少于1h,在试验时间内,焊缝不出现水流、水滴状渗出,焊缝及热影响区表面无“出汗”现象,即为合格。吹起试验用压缩空气流吹焊缝,压缩空气压气压力不小于0.4Mpa,喷嘴与焊缝距离不大于30mm,且垂直对准焊缝,在焊缝另一面涂以100g/L的水肥皂液
11、一侧是否出现肥皂泡来发现缺陷。气压试验气压试验一般用于低压容器和管道的检验,气压试验比水压试验更为灵敏和迅速。由于试验后产品不用排水处理,因此气压试验特别适用于排水困难的容器和管道。气压试验的危险性比水压试验大。气压试验方法及要求试验方法试验要求结果分析与判定气压试验.气压试验用于低压容器和管道的检验.试验要在隔离场所进行。.在输气管道上要设置一个储气罐,储气罐的气体出入口均装肩气阀,以保证进气稳定。在产品入口端管道上需要安装安全阀、工作压力计和监控压力计.所用气体应是于干燥、洁净的空气、氨气或其他惰性气体,气漏不低于15C.当试验压力达到规定值(一般为产品工作压力的1.251.5倍)时,关闭气阀门,停止加压。.施压卜的产品不得敲击,振动和修补焊缺陷.低温下试验时,要采取防冰冻的措施停止加压后,用涂肥皂水检漏或检验工作压力表数值变化,如没有发现漏气或压力表数值稳定,则为合格。7.4焊缝的抽检规定类别检验内容抽检数量小型结构件的一般焊缝外观检查每批100%焊缝的尺寸检查每批20%60%但不少于5件车架、箱体、油箱、热熔釜外观检查每批100%焊缝尺寸检查全检焊接结构尺寸检查全检变形检查全检油箱
温馨提示
- 1. 本站所有资源如无特殊说明,都需要本地电脑安装OFFICE2007和PDF阅读器。图纸软件为CAD,CAXA,PROE,UG,SolidWorks等.压缩文件请下载最新的WinRAR软件解压。
- 2. 本站的文档不包含任何第三方提供的附件图纸等,如果需要附件,请联系上传者。文件的所有权益归上传用户所有。
- 3. 本站RAR压缩包中若带图纸,网页内容里面会有图纸预览,若没有图纸预览就没有图纸。
- 4. 未经权益所有人同意不得将文件中的内容挪作商业或盈利用途。
- 5. 人人文库网仅提供信息存储空间,仅对用户上传内容的表现方式做保护处理,对用户上传分享的文档内容本身不做任何修改或编辑,并不能对任何下载内容负责。
- 6. 下载文件中如有侵权或不适当内容,请与我们联系,我们立即纠正。
- 7. 本站不保证下载资源的准确性、安全性和完整性, 同时也不承担用户因使用这些下载资源对自己和他人造成任何形式的伤害或损失。
最新文档
- 摩托车的骑跃技巧与体验活动考核试卷
- 厨房电器生产环境与职业健康安全考核试卷
- 木材加工过程中的物料管理优化考核试卷
- 皮革制品修补行业国际标准与认证考核试卷
- 模拟音响电路设计考核试卷
- 纱线疵点分析与防治考核试卷
- 水果种植茬口农业产业国际合作考核试卷
- 纺织品在智能家居环境监测的应用考核试卷
- 洗浴行业服务个性化发展模式探索与应用考核试卷
- 中国心力衰竭诊断与治疗指南(2024版)解读 4
- IATA空运危险货品-IATA《危险品规则》
- 酒店业股权收购居间合同
- 引水隧洞回填固结灌浆施工方案
- 《安全人机工程学》试题及答案
- 【七年级下册地理人教版】七下地理期中测试卷01
- 2025年华侨港澳台生联招考试高考化学试卷试题(含答案解析)
- 2025年度人工智能教育培训合同(AI应用培训版)2篇
- 水电安装合同范本6篇
- 2025年山西焦煤集团公司招聘笔试参考题库含答案解析
- 新媒体营销(第三版) 课件全套 林海 项目1-6 新媒体营销认知-新媒体营销数据分析
- 广州市房产买卖合同范本
评论
0/150
提交评论