



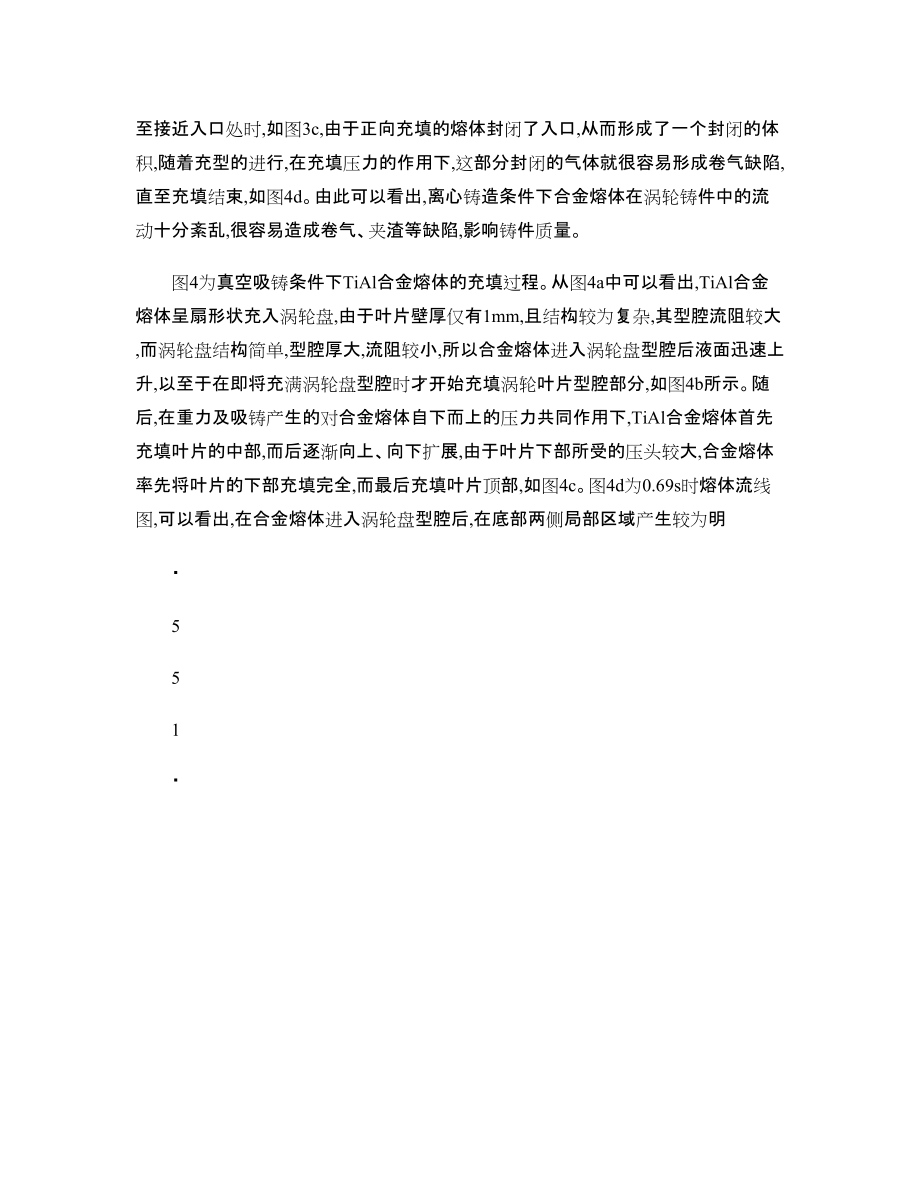
版权说明:本文档由用户提供并上传,收益归属内容提供方,若内容存在侵权,请进行举报或认领
文档简介
1、收稿日期:2009202218;修订日期:2009206220基金项目:国家重点基础研究发展计划(编号:2007CB613802NationalBasic Research Program of China 作者简介:王建国(19682,陕西武功人,工程师.研究方向:舰船动力质量技术.Em ail :bopie TiAl 合金铸造工艺数值模拟及分析王建国1,周中波2,王一川2,商国强2,李金山2(1.山西大同一号信箱81分箱海军代表室,山西大同037036;2.西北工业大学凝固技术国家重点实验室,陕西西安710072摘要:利用数值模拟方法对比研究了重力铸造、离心铸造和真空吸铸等工艺铸造TiAl
2、 合金涡轮铸件的工艺过程,分析了TiAl 合金熔体在型腔中的充填规律及凝固特性。结果表明,传统的重力铸造及离心铸造容易产生浇不足、缩松、缩孔等缺陷,真空吸铸技术能大幅提高钛合金熔体的充填能力,且充填过程十分平稳,凝固过程中易于补缩,是小型TiAl 合金铸件理想的成型方法。关键词:TiAl 合金;真空吸铸;离心铸造;数值模拟中图分类号:T G249;TP391文献标识码:A 文章编号:100028365(20090821054204Nu me ri c al Si m ula ti o n a n d A nal ys is o n Ca s ti n g Pr oc e s s of TiAl
3、 All o yWANG Jian 2guo 1,ZH OU Zhong 2bo 2,WANG Yi 2chuan 2,SHANG G uo 2qiang 2,L I Jin 2shan 2(1.Dep artm ent of N aval Deputies ,Postbox 1(81,DaT ong 037036,China ;2.State K ey Laboratory of Solidification Processing ,Northw estern Polytechnical U niversity ,Xi an 710072,ChinaAbs t rac t :The cast
4、ing proce ss of TiAl turbocharger with gravity casting ,centrifugal casting andvacuum suction casting were comparatively studied by numerical simulation.Laws of cavity 2filling and the solidification characteristics of molten TiAl in the turbocharger mold were analyzed.The re sults show that grivity
5、 casting and centrifugal casting are prone to produce defects such as misrun ,shrinkage poro sity ,shrinkage cavity.The filling ability of TiAl molten can be improved by the vacuum suction casting proce ss and its stationary filling proce ss can be well feed ,which is a ideal forming method for smal
6、l TiAl casting.Ke y w ords :TiAl alloy ;Vacuum suction casting ;Centrifugal casting ;Numerical simulationTiAl 合金以其耐高温、抗腐蚀、高的比强度和比模量等特性而成为一种极具潜力的航空航天高温结构材料14,国内外关于TiAl 合金做了大量的研究59,但由于TiAl 在室温下塑性较低10,采用机械加工、锻造、焊接等加工方法加工比较困难,导致TiAl 构件的成本十分高昂,因此,发展先进的铸造成形技术成为TiAl 合金的一个重要研究方向。在2003年德国钛会上,英国的X Wu 等人利用真空吸铸
7、技术成功浇注出了高质量的TiAl 合金排气阀11。由于真空吸铸能显著提高材料的利用率,大幅度降低生产成本,在随后的几年中该技术得到很多国家和学者的重视,至2007年初,日本采用该项技术已经生产了5万件TiAl 合金涡轮铸件12,并已成功应用到了汽油发动机上。目前,国内还没有关于TiAl 及钛合金真空吸铸技术的报道。本文采用数值模拟技术对比研究重力铸造、离心铸造和真空吸铸工艺TiAl 合金熔体的铸造性能,分析了TiAl 合金熔体在各工艺过程中的充填及凝固规律,为钛合金真空吸铸技术在国内的推广应用提供借鉴。1铸造过程有限元模型1.1充型及流动过程数值模拟数学模型假设TiAl 合金熔体为粘性不可压缩
8、流体,熔体充型过程数值模拟的基本控制方程为描述牛顿流体流动过程的N 2S 方程、连续性方程和自由表面控制方程。考虑充型过程中的传热,在控制方程中加入对流扩散传热方程。1.2几何模型及材料参数采用TiAl 涡轮铸件作为研究对象,其三维实体形状如图1a 所示,高度为155mm ,底盘直径为190mm ,叶片为楔形,最薄处厚度为1mm 。重力铸造及真空铸造技术08/2009王建国等:TiAl合金铸造工艺数值模拟及分析吸铸时TiAl合金熔体直接从涡轮杆浇入,离心铸造浇注系统如图1b所示,其直浇道尺寸为150mm×250 mm,横浇道与涡轮杆直接相连。所有三维实体模型采用四面体有限元网格进行网
9、格剖分,网格尺寸均为7mm。图1三维实体模型Fig.1Three2dimensional solid model重力铸造、离心铸造、真空吸铸时浇注温度均为1600,铸型材料为ZrO,浇注时预热到700。其中,重力铸造时浇注速度为0.65m/s;离心铸造转速为600r/min,顺时针旋转;采用真空吸铸工艺时,压差变化速率为3.5kPa/s,保压压力35kPa。2结果及分析2.1TiAl合金熔体流动形态分析图2为重力铸造TiAl合金熔体充填过程的模拟结果。可以看出,浇注时TiAl合金熔体直接到达涡轮盘底部,如图2a,此时TiAl熔体强烈冲击涡轮盘底部,其反向压力致使TiAl熔体向四周扩展,自由液面
10、呈现出中间低四周高的特点。开始充填涡轮下部的叶片,如图2b所示。当TiAl合金熔体将要充满涡轮盘型腔时,处于涡轮盘边缘的合金熔体向中心流动,与从浇口处流入的熔体相汇流,如图2c所示,这种流动形态一直持续到充型结束,如图2d。以上分析可以看出,重力铸造条件下TiAl合金熔体在充型初期对铸型的冲击力较大,容易导致粘砂,影响铸件的表面质量,而在充型中后期,自由液面十分紊乱,容易造成卷气和夹渣等缺陷,铸件质量得不到很好的保证。图2重力铸造条件下TiAl合金熔体充填过程Fig.2Flow morphology of TiAl molten during gravity casting process图3
11、为离心铸造条件下TiAl合金熔体充填流动过程。可以看出,TiAl合金熔体进入横浇道后,在离心力作用下沿铸型的迎流面向远端流动,并开始充填涡轮上部的薄壁叶片,如图3a所示。另外,TiAl合金熔体流股呈倾斜状充入涡轮型腔,这是由于随着在离心力作用下熔体向前流动的速度不断加大,其产生的柯氏力及柯氏力加速度也不断加大,在柯氏力加速度大于重力加速度时,由重力控制截面方向转变为由柯氏力控制熔体截面的方向,即熔体的流股由水平方向变为倾斜。随着充型过程的进行,TiAl熔体抵达涡轮顶部后,在压力的作用下一部分垂直于纸面向两边扩展,一部分背离迎流面向前流动进行反向充填,充填正向尚未填满的部分,如图3b所示。当熔体
12、反向充填至接近入口处时,如图3c,由于正向充填的熔体封闭了入口,从而形成了一个封闭的体积,随着充型的进行,在充填压力的作用下,这部分封闭的气体就很容易形成卷气缺陷,直至充填结束,如图4d。由此可以看出,离心铸造条件下合金熔体在涡轮铸件中的流动十分紊乱,很容易造成卷气、夹渣等缺陷,影响铸件质量。图4为真空吸铸条件下TiAl合金熔体的充填过程。从图4a中可以看出,TiAl合金熔体呈扇形状充入涡轮盘,由于叶片壁厚仅有1mm,且结构较为复杂,其型腔流阻较大,而涡轮盘结构简单,型腔厚大,流阻较小,所以合金熔体进入涡轮盘型腔后液面迅速上升,以至于在即将充满涡轮盘型腔时才开始充填涡轮叶片型腔部分,如图4b所
13、示。随后,在重力及吸铸产生的对合金熔体自下而上的压力共同作用下,TiAl合金熔体首先充填叶片的中部,而后逐渐向上、向下扩展,由于叶片下部所受的压头较大,合金熔体率先将叶片的下部充填完全,而最后充填叶片顶部,如图4c。图4d为0.69s时熔体流线图,可以看出,在合金熔体进入涡轮盘型腔后,在底部两侧局部区域产生较为明551 图3离心铸造条件下TiAl 熔体充填过程Fig.3Flow morphology of TiAl molten during centrif ugal casting process 图4真空吸铸条件下TiAl 合金熔体充填过程Fig.4Flow morphology of T
14、iAl molten during vacuum suction casting process显的涡流区,从而容易产生夹渣类缺陷。总体上看,采用真空吸铸工艺,涡轮铸件型腔中TiAl 合金熔体在宏观上呈自下而上的顺序充填特征,有利于形成自上而下的温度分布及补缩条件,获得高质量的TiAl 铸件。2.2涡轮叶片温度场分布及缺陷分析图5为各浇注条件下TiAl 涡轮铸件800s 时温度场分布。由图5a 可知,重力铸造条件下涡轮叶片上的温度梯度较大,而涡轮盘上的温度梯度较小,温度分布较为均匀。这是由于涡轮叶片壁厚很薄,散热较快,而涡轮盘十分厚大,其热容量大,造成叶片上的温度梯度很大,且TiAl 合金熔体
15、在涡轮铸件型腔中的流动十分紊乱,导致涡轮盘型腔中先进入的低温熔体与后进入的高温熔体充分混合,从而使得涡轮盘中的温度分布较为均匀,趋于同时凝固。在离心铸造条件下,由于合金熔体在铸件型腔中的流动十分紊乱,铸件上的温度场分布与重力铸造相似,从而使合金熔体趋于同时凝固,不利于补缩,如图5b 所示。由图4可知,在真空吸铸工艺条件下,TiAl 合金熔体在涡轮型腔中的流动十分平稳,总体上呈自下而上的顺序充填,从而在涡轮铸件上形成了如图5c 所示的自上而下温度逐渐升高的温度场分布,有利于合金熔体对铸件的补缩,减少铸件缺陷。图6为各浇注条件下TiAl 涡轮铸件缩松分布图,图中云图颜色深浅代表缩松的严重程度。可以
16、看出,重力铸造及离心铸造条件下涡轮铸件上的缩松十分严重,而采用真空吸铸工艺后,涡轮铸件上除叶片上分布有少数缩松外,其他区域均没有发现缩松,这就进一步说明,真空吸铸是TiAl 合金涡轮类零件的一种较为理想的铸造成形方法。 图5涡轮铸件800s 时温度场分布Fig.5Temperature field distribution of TiAl turbocharger at t =800s3结论重力铸造、离心铸造工艺条件下TiAl 合金熔体在涡轮型腔中的流动过程十分紊乱,不易形成有利于顺序凝固的温度分布,容易形成较多的卷气、夹渣、缩松等铸造缺陷。而真空吸铸可以实现TiAl 合金熔体在型腔中自下而上
17、的顺序充填,从而形成自上而下逐渐铸造技术08/2009王建国等:TiAl 合金铸造工艺数值模拟及分析 图6TiAl 涡轮铸件缩松分布图Fig.6Shrinkage distribution of TiAl turbocharger升高的温度场分布,有利于铸件的补缩,提高了铸件质量,可作为TiAl 合金涡轮类铸件较理想的成形工艺。参考文献1E Hamzaha ,M Kanniah ,M Harun.Effect of chromiumaddition on microstructure and creep strength of as 2cast Ti 248Al alloyJ .Materia
18、ls Science and Engineering A ,2008,4832484:5552559.2Zh G Jiang ,B Chen ,K Liu ,etc.Effects of boro n o nphase transformation of high Nb containing TiAl 2based alloyJ .Intermetallics ,2007,15:7382743.3H Clemens ,A Bartels ,S Bystrzanow ski ,etc.Grainrefinement in 2TiAl 2based alloys by solid state phase transformationsJ .Intermetallics ,2006,14:138021385.4梁作俭,许庆彦,李俊涛.2TiA
温馨提示
- 1. 本站所有资源如无特殊说明,都需要本地电脑安装OFFICE2007和PDF阅读器。图纸软件为CAD,CAXA,PROE,UG,SolidWorks等.压缩文件请下载最新的WinRAR软件解压。
- 2. 本站的文档不包含任何第三方提供的附件图纸等,如果需要附件,请联系上传者。文件的所有权益归上传用户所有。
- 3. 本站RAR压缩包中若带图纸,网页内容里面会有图纸预览,若没有图纸预览就没有图纸。
- 4. 未经权益所有人同意不得将文件中的内容挪作商业或盈利用途。
- 5. 人人文库网仅提供信息存储空间,仅对用户上传内容的表现方式做保护处理,对用户上传分享的文档内容本身不做任何修改或编辑,并不能对任何下载内容负责。
- 6. 下载文件中如有侵权或不适当内容,请与我们联系,我们立即纠正。
- 7. 本站不保证下载资源的准确性、安全性和完整性, 同时也不承担用户因使用这些下载资源对自己和他人造成任何形式的伤害或损失。
最新文档
- 2025年商务公司股权变更协议
- 2025年商场内部装修工程安全管理协议
- 2025年饭庄股东权益保护协议
- 2025年仓储设施租赁协议策划终止标准
- 2025年劳务合作策划管理协议
- 统筹推进教师教育能力提升的现状及总体形势
- 储备物资的高效配送与仓储创新
- 文化创新与社会需求的契合路径
- 高升专数学(文)一元一次方程应用题模拟试卷(2025年)
- 播音员主持人资格考试2025年模拟试题集(涵盖新媒体传播技巧)
- 2025年宣城郎溪开创控股集团有限公司下属子公司招聘12人笔试参考题库附带答案详解
- 酒类考试题及答案大全
- 职高历史考试题及答案
- 订制衣柜付款合同协议
- 风冷模块培训课件
- 2025年中国振弦式应变计市场调查研究报告
- 上海市闵行区六校联考2023-2024学年高一下学期期末考试数学试题(解析版)
- GB/T 6516-2025电解镍
- 职业技术学院2024级工业互联网技术专业人才培养方案
- 罗森加盟合同协议
- 榆林市煤炭资源整合实施方案
评论
0/150
提交评论