


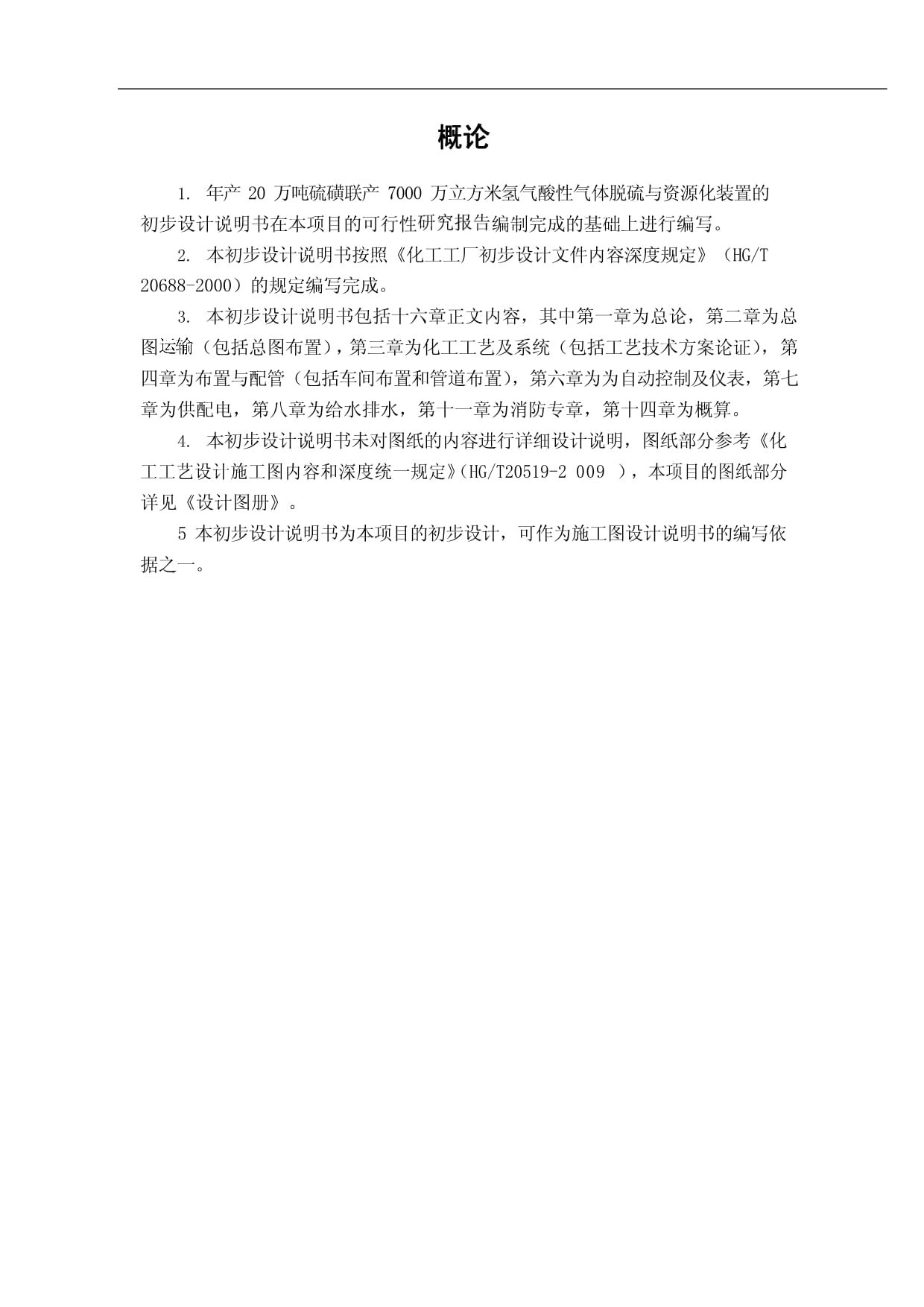

下载本文档
版权说明:本文档由用户提供并上传,收益归属内容提供方,若内容存在侵权,请进行举报或认领
文档简介
概 第一章总 设计说明 图 第二章总图设计概 设计依 厂址概 总平面布 设 第三章化工工艺及系 工艺路线选 工艺技术选 工艺方案简 流程模拟及优 换热网络与热集 第四章车间布置与配 设计依 车间布 管道布 第五章设 总 反应器设 换热器设 泵选型设 储罐选型设 第六章自动控制及仪 概 自动控制系统设计依 自动控制系统所用仪表及选 控制系统选 具体控制方 第七章供配 设计依 设计原 负荷分 供电电 区划分和设备选 配电线 动力和照 防雷和接 第八章给水排 设计依 设计原 给水工 排水系 节水及安全环保措 第九章土 地理情 设计依 建筑设 结构设 第十章环境保 设计依 主要污染源与主要污染 环保治理措 第十一章消 设计依 工艺物料分 事故发生可能性及性分 消防安全措 消防系 第十二章维 设计依 设计原 设备...........................................................................................................................设备维 检修举 维修管 第十三章能耗及节能措 设计说 能耗指标及分 节能措 第十四章概 编制依 工程概 来源及投资方式 总成本费用估 财务净现金流 第十五章重大及安全措 重大物质分 15.2、有害因素的辨识结 有害因素分 自然因素分 重大辨识分 化学品重大分 与可操作性分析 厂区及模拟分 安全对策措施与建 第十六章特殊说 概,工工艺设计施工图内容和深度统一规定(HG/T20519-2009第一章设计说明书概项目名称项目性质项目建设性质及规模项目简介本项目是为化工设计一套酸性气脱化硫发生斯反应2H2S+SO2→3/xSx+2H2O反应生成产品液体硫磺,同时和氢气,并利用斯工艺回收的大量热量。H2S+H2SO4→2H2O+SO2+SI2+SO2+2H2O→H2SO4+2HI2HI→H2+I2 的尾气 发展规划,2020年前公司将新建260万吨/年渣油加氢、280方面都有极其重要的意义。设计依据与《产业结构调整指 化联产发[2012]115号)及有关专业;相关的国家法律、设计指导设计范建设规模及产品建设规模1.1元,所得税后静态投资回收期为8.5年,动态投资回收期15.9年。为了保证项目操作时间按每年8000小时计。产品方案1.1本项目产品方案及规序产规格产备120万吨/27000万立方米/格和质量符合GB/T2449.2-2015一等品技术指标,见表3.3。表3.3液体硫磺产品规格及质量指标表(GB/T2449.2-技术指标硫(S)的质量分数/%水分的质量分数/%灰分的质量分数/%酸度的质量分数[以硫酸(H2SO4)计有机物的质量分数/%砷(As)的质量分数/%铁(Fe)的质量分数/%硫化氢和多硫化氢的质量分数(以H2S计≤以质量符合GB-T3634.1-2006合格品技术指标,见表1.3。以表1.3氢气产品规格及质量指标表(GB-T3634.1-技术指标氢气的体积分数2氧的体积分数/10-≤氮加氩的体积分数/10-≤≤---游离水/(mL/40L瓶-主要原材料1.4主要原材料、辅助材料来源表
(硫化氢
36万吨/
0.6吨/3吨/碘23吨/液化 1万立方米/ 化 生产方法及全厂总终尾气处理选用成还原加氢工艺厂址概本项目位于化工内部,位于市滨海新区大港区,东临渤海油田,南靠大港油田,占地面积13.24平方公里,与市区公用工
1.4 环境保护及综合劳动安全1.51.5性物质特物二氧化硫硫化氢硫物质 沸闪自燃极火灾物质 沸闪自燃极火灾称度上下险类别氢2----硫化氢--<-甲---消工程、水文地质条件和存在的问题及解决的本项目总体技术可行性效益可行性目资源化利用废气中H2S生产的硫磺产品存在巨大的供需缺口,销路广阔,虽价格用脱硫资源回收产生的氢气,将为企业每年节省大量成本,利用原厂PSA工艺提存在问题结图工艺总流1.5物料平衡1.6第二章采用的和标准、规范及理采用的和标50016-50160-50187- 50489-《总图制作标准 GB/T50103-《化工装置设备布置设计规定 HG20546—《石油化工企业厂区总平面布置设计规范 SH/T3053-《压缩机厂房建筑设计规定 HG/T20673-《化工装置管道布置设计规定 HG/T20549-《厂矿道路设计规范 GBJ22-采用理由设计基础温为-4℃550~68080%。本项目位于化工内部,位于市滨海新区大港区,东临渤海油田,南靠大港油田,占地面积13.24平方公里,与市区2.2总平面布置总平面布置装置布置选址结保持原厂布置不变,在此基础上合理加入本套装置。选址结果如图2.3所示,装置周边绿
2.3本项目平面布置规范评
2.2火灾性分险性进行分类,可以得到装置的火灾性类别,得到主要装置的结果。表2.3装置的火灾分类及耐火等级11级 装置间设计距离表2.4设施间距表本项目设施相邻设施设计距离规范要求规范条文号符合----------------------------项目与周边环境设计距离表2.5建设项目与装置周边环境间距一览序周边单位名称本项目设施名称设距规要规范文符性方名1东2南3西4北设设计本装置设本项目是在原厂的基础上进行建设,因此保证原厂不变,本套装置运输设计规则与原厂其他部分设计规则保持一致,运用原厂现有的道路、铁路等线路,装置四周设置一条主干道,三条次干道,而内部上,人流第三章化工工艺及系工艺路线选择概体(氧气,空气,通过高温反应促使硫化氢直接氧化生成单质硫,流程的(常见的是铁离子和EDTA配合体,H2S和配位体发生氧化还原反应生成单硫化氢脱除和硫磺回收的工艺路线干法脱硫中的斯工艺。1883年英国化学家斯(CarlFriedrichClaus)提出原始的斯法制硫工艺。原始斯法分为两个阶段,专门用于回收Leblanc法生产碳酸钠时所第1阶段是把CO2导入由水和硫化钙(CaS)组成的淤浆中,按以下反应CaS+H2O+CO2→CaCO3+ (3-第2阶段是把H2S和空气混合后导入一个装有催化剂的容器,催化剂床层预先以某种方式预热至所需温Claus工艺的主要化学反应可以如下反应式表示: (3-H2S+2O2→xSx+ 有1/3体积的H2S在燃烧炉内被氧化为SO2,并释放出大量反应热;第2阶段为催化反应阶段,即剩余的2/3体积H2S在催化剂上与生成的SO2继续反应而生成元素硫。由于在燃烧炉后设置了废热锅炉,炉内反应所释放的热量约有80%可现代改良斯法硫磺回收工艺的基础。图3.1典型的斯流程示意式已经不能满足环保要求,因此斯进行了多次改良。富氧斯工富氧斯工艺是指以氧气或富氧空气代替空气来增加装置处理能力的一分解。但该工艺并不能解决出口尾气SO2浓度可能的问题。超级斯工由于原始工艺当中斯尾气当中不免存在未反应完的H2S,SO2气体,超级克劳斯技术(SuperClaus)的主要创新在于将过程气中残余的H2S在选择性氧化催化剂的作用下直接氧化成元素硫,反应按式3-1发生。超级斯工艺要求尾气中H2S稍过量,否则无法处理SO2含量的问题。亚工亚(SubDewPoint,SDP)工艺指在硫温度以下进行低温斯反MCRC、Clinsulf点法工艺,将斯工艺的总硫回收率提高到了约99.2%的水平。反应,H2S60%~75%。此需要一个吸附—再生的过程,这种条件下产生了Sulfreen、Clauspol、回斯工艺,这种工艺的代表是SCOT、RAR和国内研发的SSR等工艺,常与克以SCOT工艺为例。该工艺本质上是将斯工段产生的废气,混合氢气进入装有用铝矾土负载钴钼催化剂的固定床反应器,当气体经过床层时,元素硫、SCOT3.1SCOT工艺改进说超级联合再生串级吸收H2S/SO2超级气气 H2分析仪低温采用配方型选吸脱硫溶剂以改善H2S低硫湿法脱硫物理吸收法是利用H2SCO2、COS等酸性组分在特定溶剂中溶解度的差异而脱除溶剂还应满足以下要求:吸收容量大、蒸汽压低、粘度小、不易挥发、不与气体成分反应、不易腐蚀设备等。目前常用的物理吸收法有:低温甲醇洗法法、磷酸三丁酯法(Estasolvan法)等。H2SCO2等酸性组分的目的。目前开发的物理化学吸收法有砜胺法、常温甲醇法(Amisol法、CFID法、Selefining法、Optisol法等。化学吸收法是利用碱液或强碱弱酸盐溶液与H2SH2S,生成硫化物或氢硫化物,在催化剂2020价铁还原回二价铁进行循环利用。主要的成功运用工艺是LO-CAT,自循环LO-CAT(LO-CATII,Sulferox2LO-CATH2SHSHS-H+Fe3+HS-发后铁催化剂用空气氧化,将Fe2+氧化为Fe3+,使催化剂恢性后循环使用,反23.3LO-CATH2SH2SH2S的循环溶液经溶液循环泵加压后,大部分送预吸收器再去吸收气相中LO-CAT工艺采用由碳酸盐、络合铁、添加剂(表面活性剂、消泡剂和杀菌剂等)Sulferox工艺,其工艺流程与LO-CAT法相似,但未使络合系统,抑制降解Fe2+4%,是LO-CAT法的20倍。与此同时,从LO-CAT整个工艺流程出发,改良吸收氧化塔,接触,产生了LO-CATII。砷基工艺于20世纪50年代由Koppers公司工业化。常用的砷基工艺下,H2S与硫酸盐反应生成硫代硫酸盐,硫代硫酸盐再被砷酸盐氧为硫代砷是比较昂贵,逐渐被LO-CAT工艺所替代。湿气制酸(WSA)工艺湿气制酸(WetgasSulfuricAcid,WSA)工艺不属于硫磺回收工艺,该工H2SCS2H2SSO2SO2 硫化氢深度资源化利用制氢气的工艺路线资源化再生。传统硫回收工艺可以简单的理解为如下过程:先将H2S不完全燃烧生成SO2,再使生成的SO2与H2S反应生成硫磺和水。这些过程虽然能够回收硫磺或 (3-H2S+2O2→H2O+x放出的热量。1H2S→H2+x (3-自发反应。但是1分子H2SO2反应可10H2S分子的热分解提供足够3-4硫化氢直接分解制氢的工艺开发进展H2SH2S研究表明1000℃时,H2S的转化率仅为20%;而1200℃时转化率为38%;只有在高于1375℃的条件下,H2S转化率才能达到50%以上。如果加入惰性气体,控制H2S分压5.05kPa,1200℃下转化率可达65.8%。催化分解法常用到的催化剂包括Al、Fe、Mo、Co、V等过渡金属元素的氧化物和硫 剂,因此该工艺产能受到限制,且氢气产出不稳定,硫化氢转化率也达不到环保超绝热分解法是指不加催化剂,也无外加热源供能,直接利用H2S在多孔介质中部分氧化产生热量,从而实现硫化氢自发热分解的方法。多孔介质为H2S分解提供了富燃条件,H2S中间循环剂与H2S进行氧化还原反应产生硫磺,经微孔过滤,被还原的中间循环剂H2S+2Fe3+→2Fe2++2H++S (3-2Fe2+→2Fe3++(3-2H++2e−→H2(3-2Fe2+2H+→H2↑(3-85%H2S,Fe2+Fe3+100%。间接分解硫化氢工艺路线的提出源(能、风能、生物能等)和核能。1Fe3O4→3FeO+2 (3-3FeO+H2O→Fe3O4+ (3-ZnO→Zn
(3-2Zn+H2O→ZnO+ (3-率理论最高可达82%。 CaBr2+H2O→CaO+ (3-
CaO+Br2→CaBr2+2
(3- Fe3O4+9HBr→3FeBr2+4H2O+ (3- 3FeBr2+4H2O→Fe3O4+6HBr+ (3-虑废热发电该体系热效率为45~50%。Cycle SO2+I2+2H2O→2HI+ (3-1
H2SO4→H2O+SO2+2 (3- 2HI→I2+ (3-70~80年代进行了论证和试验。下面分别介绍这三个反应。按照GA公司名原则,反应3-10a在SectionI中进行,该反应称为BunsenBunsen,3.5Bunsen(1+x)I2+SO2+(2+m+n)H2O↔[H2SO4+mH2O]+[2HI+xI2+ (3-3.2Bunsen反应操作条件总参反应温度330-x84-11-m45n6-反应3-10c在SectionIII中进行,发生碘化氢的热分解反应产生氢气。该步反应可以在气相或液相里发生反应。研究表明体系中碘和水含量过高会对HIHIHI度。因为HI和水形成最高共沸物,所以把HI从Bunsen反应产物中提取出来存GA公司最早用磷酸作为萃取剂,在HI分解反应前通过萃取精馏提浓。该过程电渗析(Eetr–lctoilyis,ED)装置主要包含阳极、阴极和质子交换膜:阴极侧I2得到电子从而被还原成I-;阳极侧,I-失去电子从而被氧化为I2;质子交换膜避免了阴阳两级溶液混合,并允许阳极的H+传输至阴极,从而提高HIEED3.7EED性和HI转化率。并能证明工业放大不存在问题,EED技术或许会成为最佳选择。同时在反应精馏装置内进行。从Bunsen反应分层后的HIx相出来的I2-HI-H2O混合溶液进入反应精馏装置,催化剂存在于填料之间。HIx相精馏出来的气体可直接因为大部分文献中碘化氢分解转化率难以突破40%,而且Bunsen反应a.法国原子能(Commissariatàl’énergieatomique,CEA)在20003.8CEABunsenb.启动了核能系统研究与发展计划(NuclearEnergyInitiativeNERI旨在2017年底前证明使用核能进行制氢的可行性。美术主要在GA公司开展。GA径,并进行了大量的原始研究。GA公司改进的流程图如下:3.9GA反应模块;GASNL3.10规模整合试验(IntegratedLaboratory-Scale,ILS)3.12GA3.13SNLc.原子能开发机构(JapanAtomicEnergyAgency,JAEA)20年展了硫碘循环制氢的研究,在2004年JAEA开发的装置实现了175小时的稳定运行,每小时产氢31NL。续运试。8小时的连续生产测试中,氢气产出为每小时10L,初步的连续生100L/hBunsenSO2能完全d.
根据2006-2020年国家科技发展规划部署核能与新能源技术(InstituteofNuclearandNewEnergyTechnology,INET)2005了硫碘循环制氢的研究。依托一台10MW高温气冷实验反应堆(HTR-10),大循环制氢技术开发研究的启动和前期工作(2005-2007;2009(10L/h2014HTR-10(2015-2020续生产实验,氢气产出量是每小时10NL。性得到了确认。产氢的速率是60NL/h。INET验,评估各种材料和工艺,建立一个符合真作条件的中试装置。 Bunsen反应 SO2+I2+2H2O→2HI+ (3-1
H2SO4→H2O+SO2+2 (3-碘化氢分解 2HI→I2+ (3-有、俄罗斯、韩国、、南非等。总结来看,目前在SectionI也就是Bunsen反应单元的研究结果表明:剂H2S+H2SO4→2H2O+SO2+ (3-I2+SO2+2H2O→H2SO4+ (3-2HI→H2+ (3-于硫化氢脱除与资源化利要验证该反应第一步即3-12a是否满足生产要求,3-12反反 ΔS/kJ H2SOH2SO4=H2SO4g=SO3g+SO3g=SO2g+3I2+SO2+2H2O=+2I−+---2H++2I−=2HI+2HIg=H2g+--- H2SO4ia=H2S+H2SO4l=Sl+SO2g+---3I2+SO2+2H2O=2H+a+2I−+---2H++2I−=2HI+2HIg=H2g+--- 3 3 3 3 3 2H2S+O2→2S+ΔH=-(3-H2S→S+(3-其中,式3-13是斯工艺的总反应式,式3-14是硫碘循环分解硫化氢的xH2S+yO2=(2x−y)H2O+2xS+(x− (3-a (Taη Q+
(3-其中 释放的热量,298.15K下值为286kJ/mol。Q是制氢过程输入的热量,W是输入的电效率(一般小于40%)需要乘以一个系数。可再生;硫碘循环分解水制氢效率大于50%。类似地,用式3-16评估硫碘循环分解硫化氢(式3-12)的热效率,结果为41%。但是考虑硫化氢氧化输入的能量,效率实际上能提高很多,达到66%,已经接在和斯工艺结合后,式3-12描述的的工艺路线理论上可以不消耗任何CO2、SO2H2S,是一个完全绿色的过程。虽然考虑热研究表明硫化氢能在浓硫酸(浓度>90wt%)的作用下按照式3-12a发生化学计H2SO4H2S反应,不能自发进行。具体参考图3.20。136℃是H2SH2SO4分子反应的产物临界温度点,136℃以上时H2SH2SO4136±5℃90%wt低。本项目模拟结果表明,进入该工段的的气体中烯烃含量很少(摩尔分数<0.001至此,上述提到的四个问题都能够得到解决,证明了反应式3-12a描述的工艺依靠斯工段供能,能耗低工艺技术选比前各方法代表工艺方案比较总结于表3.3。各工艺流程图见图3.21~3.27。本项目可以利用原厂已有的加氢还原装置,也可新建一套还原-吸收选择低温斯反应器方案控制SO2的排放,未达标气体由原厂还原 斯处理工艺,详细说明见4工艺路线。3.22SCOT3.23SSR源(蒸汽、电等源(蒸汽、电等3.3H2S艺比亚 Simont 该工艺与同SCOT该工艺为国内公司工艺成熟、运转可工艺相比,主要区消化吸收SCOT工靠、操作弹性大、别是没有 炉,艺后 抗干扰能力强,总加氢反应器热源由术,近年来市场占硫回收率高,排放反应器进出口物流有率逐步提高。利指标能满足环保标换热或其他外部热用装置自身热源准。但该工艺装 投资高,尤其是加提供。由于没有在氢反应器所需热源线炉,使得过程气供氢作氢源,利用由加热炉提供总量较SCOT工艺高温掺合阀和换热和氢源需外供,造减少10%,从而具器而取消了传统的成操作复杂,操作有设备规模小、尾 费用增加,并且占气排放量相对较少具有设备规模小地面积较大 尾气排放量相对个 催化剂采用以TiO2该工艺为国内公司为主体的直接氧化消化吸收冷吸附床催化剂,主要特征(CBA)后是把H2S直接氧化具有自主知识成元素硫,并且具的技术,特点和有COS加氢活性。Clinsulf相似,在能装置流程简单,但量利用率、硫回收硫回收率不高。按率等方面有所提传统Claus工艺配 H2S:SO22:H2S含量略过量。VKSO2转化成SO3之前含硫工艺 较 较 较较 较一 较低高高技术成熟、处理能技术成熟、处理能自主知识,投力大、效果好。但力大、效果好。投 投资是几个工艺资高,占地面积 资相对SCOT和中最高的,适合超大,适合超大规模RAR大规模炼化企业 炼化企业 型炼化企业需要精确控制H2S需要精确控制H2S和SO2的比例,相和SO2的比例,二较其他亚工艺氧化硫排放量有超在能耗、硫回收率标风险;流程短投上有一定优势,但资低,处理量可大是也继承了缺点;可小,适合一般炼自主知识,实化企业和天然气净际运用的企业较 H2S浓度较高的酸工艺方案简介4.2Mpa2H2S+O2→2S+(3-2H2S+3O2→2SO2+(3-H2S+CO2→COS+(3-2H2S+CO2→CS2+(3-1000350℃以下后进入通过液硫泵泵入硫封罐,而后打入液硫池。在斯反应器中催化剂为CT6-4B活性Al2O3,动力学数据参考Abdel-Fattah等人的研究结果,发生的主要反应为:2H2S+SO2→3S+ (3-330℃,通过蒸汽发生器取热,随后MDEAH2S,吸收后气体经由尾气炉后放空。再生得到的H2S气体和酸性气一并打入斯燃烧炉循环处理。ProcessEconomicsProgramReport216AcidGasTreatmentandSulfurRecovery中关于反应器条件的部分内容。图中上半部分为硫碘循环制氢单元,该单元各装置分别发生式3-10三个反应Wang等人的研究结果。反应产生的液硫分相后经液硫泵打入液硫池,反应后气体主要是SO2,进入Bunsen反应器,在60℃常压下发生Bunsen反应3-10b。本森反应器是一个短停和硫化氢氧化塔产生稀硫酸去硫酸提浓装置在0.02Mpa(>90%wt下层HIx相进入碘化氢反应精馏塔发生HI分解反应3-10c按照理论研究,Bunsen反应中原料H2O和I2需要过量,即式3-9的参数x、m、n需要根据流程Lee等人的数据,H2OI2实验证明,理论上SO2会反应完全,但不能排除部分操作条件波动时反应不完全的可能,Bunsen反应产生的气相中主要含硫化氢氧化塔未完全反应产生的H2S、无反应活性的烃类、CO2SO2,一并打入斯工段Bunsen反应器的设计参考了SNL的报告,动力学数据来自Zhu等人的研碘化氢反应精馏塔是一个筛板塔,精馏段5块塔板,提馏段3块塔板HI分解成H2和I2反应可能同时在气相和液相中发动力学数据参考因为塔内存在过量的水,塔顶塔釜温度接近,根据Murphy的建议,可以通过需求,另设计了一套以1,2-丙二醇为工质的热泵系统,该系统在0.08Mpa~0.2Mpa之间操作,流量比以水为工质时要大。反应后产生的H2被经过冷凝的塔底液体洗涤后经过残余碘回收工序,输出到未反应的碘化氢,二者主要以I3-离子形式存在,连同过量的水,去Bunsen反应器作为Bunsen反应原料,完成第二个循环。酸性气,酸性气来源根据原厂调研取得的数据如表3.3所示:表3.4酸性气体组成和性质温 组质量分数注:应原厂生产据要求对酸性气组数据做了部调整,流根本项目实际情况合,所有数接近原厂调数据原厂酸性气主要来源是180万吨/年加氢裂化、130万吨/年蜡油加氢、40万吨/年焦化汽柴油加氢、120320津发展规划,2020年前将新建260万吨/年渣油加氢、280万吨/年重油催化裂化120万吨/年催化汽油吸附脱硫等5个装置2020油部产能翻倍,1613IMTP400.19Mpa流程模拟及优化流程模吸收-再生单元需要两套斯装置,即需要吸收再生A,B两个系列。硫碘循环制氢单
同时硫化氢和硫磺。本项目提出如下硫碘循环分解硫化氢路线:
3.31化氢反应精馏塔发生HI分解反应。流程模拟如下图所示: 而在流程中单独设置Heater模块代替,流程模拟如下图所示:硫磺回收单
理选用成亚工艺。预热,剩余蒸汽并入公用工程。流程模拟过程如下:3.34酸性气与空气在预热之后,在斯燃烧炉燃烧生成SO2,继而SO2与H2S发生斯反应生成硫磺蒸汽此时硫化氢转化率70%左右同时副反应产生COS、CS2等,炉内温度达到1100℃以上,继而在废热锅炉中冷却到350℃左右,产生2MPa蒸汽,接着进入一级硫冷凝器,降温到170℃左右,回收液硫,之后换热升温至240℃,准备进入斯反应器中进行反应值得注意的是,AspenS2,S8图3.34斯燃烧炉单元模拟示意二段斯反应器单在一级斯反应器中继续发生低温下的斯反应,同时COS和CS2在催化H2SCO2,之后继续进行二段转化,液硫回收。MDEAH2S,吸收后气体经由尾气炉后放2ASPEN模拟结果显示,尾气SO含量100mg/m3的排放标准,远低于2015年环保标准的最严要求。吸收塔富液去再生塔再生,再生得到的H2S气体和酸性气一并打入斯燃烧炉循环处理。2塔的参数对整个流程中各个的塔设备进行参数优化Aspen模拟里面的灵敏度分析软件,再生塔时候,整个吸收再生循环富集硫化氢的效果提高。当回流比从2逐渐提升至5的过程中,富集硫化氢效果逐渐提高直至稳定。在2-3.4之间,出口硫化氢含量变化较大,说明提高回流比对于整个吸收再生流程有较大的提高。考虑到R的继续增资,因此我们选定再生塔回流比为4.6比较合理。857
8558528508478458428408372 2 2 2 2 3 3 3 3 3 4 4 4 4 4 5VARY1C102COL-SPECMOLE-们选择塔板数为13。
SensitivityResults VARY1C102PARAM效果,进料位置定在5板比较合理。
SensitivityResults VARY1C1021-4尾气吸收塔SensitivityResults0 反应精馏塔择闭式热泵进行热量集成,在塔的灵敏度分析结束之后,荷是绝对值,因而冷量对比时需要加负号)在进料位置在3-9板的位置时,对塔顶2012012012002002002002002002002002002007
186186186186186186186186186186186186186186186185
TOPC3003253503754004254504755005255505756006256506757007257507758008258508759VARY1B12S23150275
274
274274274115274
3003253503754004254504755005255505756006256506757007257507758008258508759VARY1B12S23800
SensitivityResults
600060065070075080085090095100105110 1351401451501551601651701751801851901952VARY1B12COL-SPECMOLE-收率。因而回流比选择在0.75-0.9是合理的。
45040030025020015010050060065070075080085090095100105110 1351401451501551601651701751801851901952VARY1B12COL-SPECMOLE-用软件进行三维作图,得到一张三维网格图如下所示,负荷的倒数kmolW𝐖 𝑸𝑯+其中:𝑭𝑯𝟐𝑸𝑯——塔釜再沸器热负荷,单位𝑸𝑪——塔顶冷凝器冷负荷,单位1(分母变再沸器负荷37552KW,并根据这个优化结果设计热泵。反应器的参数1.加氢反应器加氢反应器主要作用是将尾气当中含有的SO2全部还原成H2S,由于该反应动力学限制Aspen模拟结果可在管径大3m,管长大于1m的情况下,可Bunsen反应器作为硫碘循环的关键设备,特殊的气液反应使得工艺上放大的案例很少,同时更为难的是,其动力学十分复杂,很难做到规划到符合Aspen输入标准的数据,因此我们使用软件,将文献中实验数据进行拟合,根3.44Bunsen动态控概的内容,该动态控制方案为生产设计及PID图的绘制提供指导与技术支持,稳态模拟向动态模拟转入AspenPlusDynamics30%——来罐、塔釜的设计。假设标准回流罐长径比假设为2:1,得到下表。塔顶回流 塔釜回流3.5再生塔塔釜塔塔顶回流 塔釜回流长度H 直径长度H 在确定没有严重错适用于AspenDynamics的模拟文件如下图。并且以这个稳态模拟文件进入Dynamics运行界面整个流程共存在5个控制变量,分别是吸收液塔压P,吸收液流量V、再生塔塔顶冷凝器热负荷QC再生塔塔釜再沸器热负荷QH再生塔回流量(回流比R。结合着几个变量进行流程控制。3.463.47根据ASPEN模拟结果,再生塔的灵敏板的位置在第二块板,因此对再生塔的温
3.48可持续性,做出如下改动:增益改为20,周期改为12min,以更符合吸收再生塔的LC0101,LC0102,LC0103TC0101之前加入死时间元件,为了更好地符合实际情况,这个改动需于TC0101加入死时间控制元件,因此仅要对改控制器进行整定,正定过程如设置死时间元件并初始化。将在将没有加上死时间元件的TC0101,InitalizeValue之后,得到控制的稳定值,之后AspenPlusAspenDynamicTestsettingsTestsettings5%设定完之后点击菜单栏中的RUN按钮,然后点击控制面板中的Tune面板按下Starttest按钮,则控制器开始进行整定测试,经过大致4-6个周期,最后点击TuneFinishtest按钮完成对控制器的整定。图3.50继电-反馈显点击整定面板中的Tuningparpmeters页面选择Tyreus-Luyben整定方法,点击Calculate按钮,就会计算得到控制器的比例增益和积分时间。完成对整定PID参数进行计最后点Updatecontroller将控制器PID结果上传到控制器中,从而完成两个温度控制器的PID参数的整定。因而温度控制器的参数最后整定如下:增益4.29,周期6.6min。控制系统的评估研究进气量波动20%的情况下系统是否可以快速进入稳定状态。由于控制阀FC0101的存在,在动态过程稳定1h之后,分别加入进料量的干在系统稳1h1h之后加入干扰0.01h计数1-5h为了方便比较进料上下变化的波动,将Dynamics的数据导入里面,使可以看出,扰动在一小时后加入,系统在2.5小时左右稳定,响应时间1.5小换热网络与热集成概加热等过程,所使用的热公用工程为0.5MPa、150℃的低压蒸汽、1.0MPa、180℃的低压蒸汽、3.5MPa、242℃的高压蒸汽。度的节能。热泵精馏以工质的来源可分为两大类:一类是直接式热泵精馏,以塔中的物质为工质;另一类是间接式热泵精馏,以额外的循环物质(如制冷剂、水成使用。热泵精馏的流程选择要密切结合具体条件(如当地的价格,所利用换热流股和公用工程3.6过程流股物流信息进口温度出口温度热负荷31-13_To_31-31-16_To_31-22-24_To_22-22-13_To_22-30-7_To_30-31-10_To_31-STR-1_To_STR-22-33_To_22-20-1_To_20-30-9_To_30-9-31-18_To_31-18-10-3_To_10-10-6_To_10-21-8_To_21-进口温度出口温度热负荷T0102-T0102-T0202-T0202-3.8公用工程物流信息进口温度出口温度-0确定能量将上述工艺流股信息输入到AspenEnergyyzerV8.8,在能量分析器3.53ΔTmin传热温差增大可以减少公用工程的耗费,而且经验来说10℃以上比较符合真实情况,因此此处选取最小传热温差为11.5℃比较合理。3.543.55需要达到的最低温度为20℃,由于的冷公用工程最低温度32℃,换热网络的设计与3.5669.09MW297.20MW,热公240.03MW57.6%,71.2%,114.3MW。所使用的冷公用工程为:冷却水(32℃、冷冻盐水(-5);所使用的热公用工程为:高压蒸汽(3.5MPa、中压蒸汽(1.0MPa、低压蒸汽3.57热泵精馏节能分析3.58器(5)、冷凝器(6)、膨胀阀(762压缩后,把它升高到一个较高的压力4中该工质再次冷凝,把它的热量传递给蒸发的塔76进行再循环,从中可以看到,间接式热泵,以水蒸气作为工质进行循环,使用ASPEN模拟热泵精馏过程如下图所若不使用热泵精馏,其塔顶冷却能耗为76365.5kW表所示,总能耗节约了46.67%。整个热泵精馏的热量计算比较详见附录。总结与分本项目使用了热集成节能技术,运用了AspenEnergyyzer软件,实型节能技术,节约了大量能量。76365.5kW,塔底加热能耗为37552.0kW;使用热泵精馏时,压缩机电耗为的能量形式,电热转换系数约为3.29,因此热泵精馏加热能耗为16821.3kW。反应精馏塔能耗能耗节约了46.67%。经过优化后,共需要冷公用工程126.00MW,热公用工程69.09MW。不含297.20MW,240.03MW。冷量节省57.6%,71.2%,总回收能量114.3MW,总能量回收率42.53%。第四章间布置与4.1GB50016-GB50160-HG20559-HG20519-HG/T20546-HG/T20549-HG/T20646-SH3034-SH3011-SH3010-4.24.2.1体原车间布置平面布置I(长方形、LTΠ型等。长方形厂房是比较常用的形式,一般适应地形的要求或者生产的需要,也有采用L型或T型的,这些形式适用于较复杂的车间,此时应充分考虑采光、通风、交通和立面等各方面的因素。至于Π柱网布置和跨度节约设计和施工力量,加速基建进度:一般单层、多层厂房宜采用6x6m柱网的布厂房的宽度厂房垂直布置5m,6m,4.5m,每及害性气体的厂,要适当加高建筑物的层高。有的车间宜采用区与非防爆区(生活、辅助及控制室等)间应设分隔。如两个区域需要互通时,中间应设双门斗,即设两道弹簧门隔开。上下层应设在同一轴线设备布置生产工艺对设备布置的要求2)运转设备应考虑其备用设备的位置。考虑 尽可能缩短设备间的管线。车间内要留有原料、、产品设备安装对设备布置的要求大设备宽0.5m。不经常检修的设备,可在墙上设置安装孔。考虑设备检修、拆卸等的起设备。的一端。厂房长度超过36m时,则吊装孔应设在厂央。控制在2.7m以内。厂房建筑对设备布置的要求笨重设备或运转时会产生很大振动的设备如压缩机、真空泵、机等,应600mm。容器布置原则廊立柱的净距可保持1.5m。校核取出搅拌器的最小。座基础中心线对齐或按封头切线对齐。卧式容器之间的可按0.7m考虑。在方需设通道时,容器底部配管与地面不应小于2.2m;不同直径的卧式容器高应比顶部管嘴法兰面低150mm。当液面计上部接口高度距地面或操作平台超过3m泵的布置泵与泵的间距视泵的大小而定,一般不宜小于0.7m,双排泵电机端与电机置的泵,其配管与阀门应排成一条直线,管道避免泵和电动机。压缩机的布置较好。大型压缩机多采层厂房,分上、下两层布置,压缩机基础为框架高基换热器的布置换热器外壳和配管对于不保温外壳最小为50mm,对保温外壳最小为反应器的布置催化剂可以由反应器的顶部加入或用真空抽入,装料口离操作台800mm左台,底部离地面最小距离不得小于500mm。塔设备的布置径的3-4倍。车间划分及净安全距离1不少于2至少3不小于456至少7至少8不小于9不小于不小于不小于不小于不小于不小于不小于不小于 不小于45 不小于60 不小于 不小于表4.2通道的宽度与高项 宽度 走道、楼梯操作台下的工作场所、管架 高 走道、楼梯操作台下的工作场所、管架 高 平台到水平人 次要道 平台到水平人 次要道 管束抽出的距离(室外 硫磺回收单元装置其他装置布
4.5操作与维修,泵与泵之间中心线的间隔设为1m。管道布置管道应或地上敷设;如确有需要,可埋地或敷设在管沟内。宜集中管道布置设计表4.3管道与建筑物及最小管道水平间最小水平间距12345表4.4管道与建筑物 最小管道垂直间最小垂直距离1234管径计udu其中,Vdu,m/s。4.5速选 液 气 流速<85%的临界速度,真空不超过气 流速<85%的临界速度,真空不超过最经济管径的MEE——每年消耗与克服管路阻力的能量费用(生产费用MMM为纵坐管壁厚度及管道管壁厚度管道材料 极限工作温度435℃。管道编根据《管道仪表流程图设计规定》(HG20559-1993)的相关规定,管道号由5部分组成,每个部分之间用一短横线隔开:第一部分:物料代
4.6流程图上的物料代号和缩写词》(HG20559.5-1993。工程上需要但在规定中没第二部分:工程的工序(主项)编号和管道顺序号置内给配给每一个工序(主项)01、10外,管道号的其他各部分、各单元都完全相同。系列号采用一位大写英文印刷体字母表示,通常不用O和1。表示在管道仪表的流程图首页上。第四部分:管道等级用于ANSI标准压力等级代号(其中I、J不用,L~Z用于国内标准压力等级代号(其中O、X不用。常用的国内标准压力等级代号:4.6常用国内标准压力等级代号LMNP4.7常用管道材质与代号对应表ABH4.第五部分:隔热、保温、防火和隔声代号母表示,其代号字母按《管道仪表流程图隔热、保温、防火和隔声代号》1993管道绝热绝热的功能绝热结构安全措 管道段的总压降,不得超过安全阀定压值3%;有导电的跨线,管道每隔80m接地一次。典型管道泵的管道布置抽空,若不能避免时,需在“气袋”顶添加DN15~20放气阀;若在水平管段上变径,蒸汽往复泵、计量泵、非金属泵的吸须设过滤器,避免杂物进入换热器的管道布置器的两端和法兰周围的安装与维修空间,在这个空间内不能有任何物;塔的管道布置管廊的管道布置其他管道布置间歇生产反应进行时,如果漏进某种介质有可能引起、着火或严硫回收装置管道布置示意图图 第五章总设备的型式、材质、基本设计参数、管口、维修安装要求、支承要求及其他要过程设备的基本过程设备设计的品或手册中查到其规格及型号,直接从设备生产厂家;另一类是非标设过程设备设计与选型的这些设备包括换热器系列、容器系列、搪玻璃设备系列以及圆泡罩、F1型浮阀(如防爆口、人孔、手孔、卸料口、液面计接口等反应器设计设计目反应器介式式管 气相;液
填料 气液反板式 气液反
催化 流化床化)相;特别是催化输送容易,但磨耗大;床内返混大,对高转化率不利
5.2填料塔与板式塔的优先适用情况填料填料 板式
反应精馏塔设计反应器选型5.3几种主要塔板的性能塔盘类塔盘类 优 缺 适用场泡罩
浮动喷射 表5.4几种主要塔板性能的量化比较
塔5393反应动力学碘化氢分解反 2HI↔𝐻2+𝑑[𝐻2]=𝑘[𝐻𝐼]2− [𝐻][𝐼 𝑑[𝐻2]= −1𝑟=k[HI]2− [𝐻][𝐼2 𝑘=𝐴exp(−exp(−𝑘−1=
文献<DevelopmentofEfficientFlowsheetandTransientModelingforNuclearHeatCoupledSulfurIodineCycleforHydrogenProduction>给出5.5力学正反应指前因子正反应指前因子 正反应活化能 逆反应指前因子 1.596×107逆反应指前因子 1.596×107进料摩尔组成𝑥𝐹,𝐻𝐼=0.1𝑥𝐹,𝐻2𝑂=0.51𝑥𝐹,𝐼2=塔顶组成𝑥𝐷,𝐻2=0.038𝑥𝐷,𝐻2𝑂=0.886𝑥𝐷,𝐼2=塔釜组成𝑥𝐵,𝐼2=0.475𝑥𝐵,𝐻2𝑂=表 流股数据TemperaturePressureVapor10010MoleFlowMassFlowVolumeFlow -----MoleFlow反应操作条件line(SCLs
𝑅𝑛+1 𝑅𝑛+1
𝑆𝑚 𝑆𝑚+1 𝑆𝑚+1𝑥𝑠,𝑚,𝑖=𝑦𝑠,𝑚,𝑖=式中,𝑅𝑛=[(𝑅1𝜅𝐷+1)𝜅𝑟𝑦−1]𝜅𝑟𝑥= 𝑆𝑚=(𝑆1𝜅𝑠𝑦+1)𝜅𝑠𝑥−1=𝑅1—塔顶回流比𝑆1 𝜈−1由于𝜐𝑇𝑂𝑇=0,则𝜅𝑠𝑦
=
𝑇𝑂𝑇5.1反应2HI=𝐻2𝐼2F=B+D−F𝑥𝐹𝑖=B𝑥𝐵𝑖+D𝑥𝐷𝑖−式中计量系数𝜐𝑇𝑂𝑇=解得反应深度𝜉𝑇𝑂𝑇=413.5𝑘𝑚𝑜𝑙/ℎB=41499.7kmol/h0.8𝜉𝑇𝑂𝑇≤𝜉𝑟+𝜉𝑠+𝜉𝑓≤碘化氢反应动力学方程式r=k[HI]2𝑘=1011exp
108=1.596×107exp(− 精馏段两板间浓度变化取𝑐3−𝑐3= (提馏段两板间浓度变化取𝑐3−𝑐3= (𝜉𝑟=𝑁𝑟×𝑟×𝐻𝑟=4×4.98×106∫𝑐2𝑑𝑐×𝐻𝑟=4×4.98×106×3.54×10−3÷=𝜉𝑠=(𝑁𝑠−=3×4.98×106∫𝑐2𝑑𝑐×𝐻𝑠=3×4.98×106×2.41×10−3÷=𝜉𝑓=𝑟×𝐻𝑠=4.98×106 𝑐2𝑑𝑐×𝐻𝑠=4.98×106×2.41×10−3÷3×𝐻𝑠=则有330.8≤300.8𝐻𝑠+293.8𝐻𝑟≤可取𝐻𝑟=0.06𝑚3𝐻𝑠=反应精馏塔的塔径𝑀𝐷𝑉=𝑀𝐹𝑉=𝑀𝐵𝑉=
=𝑀𝐷𝑉+𝑀𝐹𝑉==𝑀𝐵𝑉+𝑀𝐹𝑉=𝑀𝐷𝐿=𝑀𝐹𝐿=𝑀𝐵𝐿==𝑀𝐷𝐿+𝑀𝐹𝐿==𝑀𝐵𝐿+𝑀𝐹𝐿= =𝑝𝑀𝑟𝑣= =𝑝𝑀𝑠𝑣=
𝜌𝐷=𝜌𝐹=𝜌𝐵==𝜌𝐷+𝜌𝐹=2188.2𝑘𝑔/𝑚3=𝜌𝐵+𝜌𝐹=3248.5𝑘𝑔/𝑚3𝜎𝐷=𝜎𝐹=𝜎𝐵==𝜎𝐷+𝜎𝐹=
+78/2
=𝑉1𝑀𝑟𝑣==𝐿1𝑀𝑟𝐿= 取塔板间距𝐻𝑇= 板上液层高度ℎ𝐿= 𝐻𝑇−ℎ𝐿=
X=𝐿𝑟ℎ√𝜌𝑟𝐿= 𝐶20=𝜎𝑟𝐿C=𝐶20(20 =最大允许气速 =𝐶𝜌𝑟𝐿−𝜌𝑟𝑉= u=0.7𝑢𝑚=塔径D=√ =1.83m圆整至同上𝑉𝑠ℎ= 𝐿𝑠ℎ=取塔板间距𝐻𝑇= 板上液层高度ℎ𝐿= 𝐻𝑇−ℎ𝐿=
X=𝐿𝑠ℎ√𝜌𝑠𝐿= 𝐶20=𝜎𝑠𝐿C=𝐶20(20 =最大允许气速 =𝐶𝜌𝑠𝐿−𝜌𝑠𝑉= u=0.7𝑢𝑚=塔径D=√ =1.59m圆整至5.反应精馏塔的塔高及反应停留时塔板间距𝐻𝑇=0.50m塔顶空间高度𝐻𝐷=2𝐻𝑇=进料板高度取𝐻𝐹=塔底空间高度𝐻𝐵=ℎ1ℎ=460𝜌𝐵𝑉封头 =塔底页面至最下层塔板间距取ℎ2=则𝐻𝐵=0.551.5=H=(N−1−1)𝐻𝑇+𝐻𝐷+𝐻𝐹+𝐻𝐵=(8−1−1)×0.50+1.0+1.2+=精馏段气体流量
=𝑉1𝑀𝑟𝑣=
液体流量
=𝐿1𝑀𝑟𝐿= 𝜏𝑟𝑣
4
𝐻𝑇−𝐻𝑟)= ×0.5−
=
=3600𝑁𝑟𝐻𝑟=3600×4×0.06= 提馏段气相体积流量𝑉𝑠ℎ=液相体积流量𝐿𝑠ℎ= 𝜏𝑠𝑣
4
𝐻𝑇−𝐻𝑠)= ×0.5−
=6.溢流装
=3600𝑁𝑠𝐻𝑟=3600×4×0.08= 以下几种形式:U型流、单溢流、双溢流、多溢流。D=2.0m对于堰长lDlw= 以保证液体在降液管中有较长的停留时间。精馏段可取lw=0.6Dlw=D因此可查得精馏段𝐴𝑓0.055,𝑊𝑑0.1;提馏段𝐴𝑓0.09,𝑊𝑑0.15
2
𝐴𝑇=4𝐷
=
精馏段𝐴𝑓=0.055𝐴𝑇=0.17𝑚2,提馏段𝐴𝑓=0.09𝐴𝑇=精馏段𝑊𝑑=0.1𝐷=0.2𝑚,提馏段𝑊𝑑=0.15𝐷=出,一般要求 不应小于3~5s,而对于高压下操作的塔以及易起泡的物系,精馏段AfHTAf τ=3600𝐴𝑓𝐻𝑇=3600×0.17×0.5=6.65𝑠≥ τ= = =6.88𝑠≥ 由于停留时间3s,故降液管尺寸精馏段𝑙𝑤=0.6D=0.6×2.0=提馏段𝑙𝑤=0.7D=0.7×2.0=精馏段
ℎ
=
𝐸( 2
×1×
2提馏段 = 𝐿ℎ 73.30)3=
𝐸(
×1× 精馏段ℎ𝑤=ℎ𝐿−ℎ𝑜𝑤=0.06−0.032=0.028𝑚提馏段ℎ𝑤=ℎ𝐿−ℎ𝑜𝑤=0.08−0.040=0.040𝑚取降液管低隙处液体流速𝑢𝑜𝐿=0.25𝑚/𝑠精馏段ℎ= =46.04/3600= 提馏段ℎ= =73.3/3600= 6反应精馏塔板流体力学验算ℎ𝑓=ℎ𝑑+ℎ𝑙+由于筛孔气速𝑢0=0.68𝑚/𝑠,通过查干板流量系数图可知𝐶0=𝑢
=0 0 𝑢0 6.34ℎ𝑑0.051𝜌𝐶)=0.051 )=0.0169𝑚液 0.4h𝑙=𝛽(ℎ𝑤𝑜𝑤)=0.4×(0.0320.028)=0.024𝑚液柱ℎ𝑓=ℎ𝑑+ℎ𝑙=0.01690.036=0.0529𝑚∆P=ℎ𝑓𝜌𝐿𝑔=0.0529×2188.2×9.81=为防止降液管液泛现象发生,需控制降液管内液层高度𝐻𝑑<𝜑(𝐻𝑇𝑤),ℎ=
𝐿𝑠)2=
)2= 𝐻𝑑=ℎ𝑤+ℎ𝑜𝑤+ℎ𝑓+ℎ𝜋=0.028+0.032+0.0529+0.00958
取降液管 层相对密度为0.5,则有
𝐻′=𝜑(𝐻𝑇+ℎ𝑊)=(0.5+0.028)=dHdd
τ= = =6.65𝑠≥
1.36𝐿𝑍+𝑉
𝑆F
𝑠𝜌𝑙−𝜌𝑣𝐹𝐾𝐶𝐹√ √
3600+=
3600 2188.2−10.96=其中有𝑍𝐿=𝐷−𝑊𝑑=2.0−0.2= 𝐴𝑏=𝐴𝑇−2𝐴𝑓=3.14−AA2A3.801-20.456 5.4应控制泛点率不超过80%,故可知雾沫夹带能够满足要求。 =0 0动能因数:𝐹0=𝑢0√𝜌𝑣=6.34×√10.9621>5𝑢𝑜𝑤=4.4𝐶0√0.0056+0.13ℎ𝐿−ℎ𝜎𝜌𝑙/𝜌𝑣=4.4×0.78√0.0056+0.13×0.014−=塔,取泛点率F1=0.8,则:Vs
1.36LsKCF
1.36×1.8×𝐿+𝑉 0.8 𝑠2188.2−整理变形,得:𝑉𝑆=4.232ℎ𝑂𝑊
𝐸
2
=(0.00284×1)3600=取3s作为液体在降液管中停留时间的下限,则(𝐿) =𝐻𝑇𝐴𝑓=0.5×0.17= Hdhwhowhfh公式求得液泛线方程。𝐻𝑑=𝜑(𝐻𝑇+ℎ𝑤)=0.5×(0.5+0.028)=2 𝐿ℎ ℎ𝑂𝑊=1000𝐸(𝑙)=ℎ𝑓=ℎ𝑑+2h𝑙=𝛽(ℎ𝑤+ℎ𝑜𝑤)=0.0128+ 𝑢0 ℎ𝑑=0.051(𝜌)(𝐶)= ℎ=
𝐿𝑠)2=
= 2联立上式可得:𝑉𝑆2=42.1111047𝐿𝑆2−反应精馏塔机械工程设计塔径在2.5m以下,边缘宽度取溢流堰前安定区宽度WS取 堰后安定区宽度WS'取根据之前计算可知,降液管宽度为Wd=0.2m和则t=0.015m;n计算公式n=1.155𝐴𝑎=1.155×2.8=式中,开孔区面积𝐴𝑎=(9)开孔率φ=0.907(
2=0.907×(
2=)塔设备附件
525mm,4.4930𝑚2=d=
=实际流速u
==d=
=实际流速u= =0.30𝑚/𝑠。=d=
=实际流速u
=1.87𝑚/𝑠=d=
=实际流速u
=焊接长度:l=2𝛿𝑛=裙座筒体上端面至塔釜椭圆封头切线距离D=2000,壁厚𝛿𝑛10𝑚𝑚时,h=80mm选用圆筒形群座,裙座高度H=21.5𝐷=24894mm径管规格400mm。20M3016Mn18mm。校核结果见表5.7。板1881111度径1120312345812345000B7度值3℃182管内径(或宽度整0有取用厚度许用内压881段圆88名义厚度取用厚度88操作质量m0m01m02m03m04m05ma最小质量m0m010.2m02m03m04ma32风弯矩MIIPl/2 (l /2) (l /2) n横风向弯矩Mca(IMII2T2Ym(hhh kn横风向弯矩Mca(IIMII2T)2Ym(hhh T kk顺风向弯矩 顺风向弯矩 组合风弯矩 max(MII,(MII)2(MII)2 n弯矩MIIF(hh注:计及高振型时,此项按B.24 k偏心弯矩Meme max(MIIM,MII0.25MIIM 需横风向计算时 max(MIIM,MII0.25MIIM nFmhF00/mh(i1,2,..,n ii k垂直 k0000011PcDi/ (mIIgFII)/D i 4MII/ i (mIIgFII)/D i31PTDi/ mIIg/D i 4(0.3MIIM)/ iBA1123(内压23(外压A223(内压123(外压A312A42(pT9.81Hw)(Diei)/1:ij中i和ji=1j=1设计压力或试验压力下引起的轴向应力(拉i=2检修工况j=2重力及垂 j=3弯矩引起的轴向应力(拉或压注2: 注3:单位如下质量:kg力:N弯矩:Nmm应力(D4D4Zb (D2D2Ab b2,MC l2 x y M00/Z(mgF00)/b max0 0.3M0M)/Z g/ 应力M00Mmg w BME0.25MwMem0g 地脚螺栓需要的螺纹小径d 4BAb 0 nl 1G 3Fl 213 盖板最大应 4(l2d3)c(l4d2)盖板校核结果itit4MJ mJJgFJmax D Dit it-80m0m01m02m03m04m05mamminm010.2m02m03m04ma直立容器的最大mmaxm01m02m03m04mamw空塔重心至基础环板底截面距直立容器自振周s风载对直立容器总的横推力N载荷对直立容器总的横推力N操作工况下容器顶部最大挠横风向塔顶振幅0容器偏心质量计入直立容器的操作质量、最小质量、最大质量上封头校核计硫离团计算所依据的标椭圆计算压力设计温度内径曲面深度S30403(板材设计温度许用力试验温度许用力负偏差腐蚀裕量焊接接头系数压力试验时应力压力试验压力pT=1.25p[]=1.5426(或由用户输入[压力试验允许通应力pT.(KDi0.5eh 2eh 1 D2622i i Kpc=2[]t0.5pcheh=nh-C1-2[]t[pw]=KDi0.5eh计算压力设计温度内径曲面深度力力负偏差腐蚀裕量焊接接头系数][应力pT.(KDi0.5eh 2eh 1 D2622i i Kpc=2[]t0.5pcheh=nh-C1-2[]t[pw]=KDi0.5eh计算压力设计温度内径负偏差腐蚀裕量焊接接头系数=2[]tPce=n-C1-pT=1.25p[]=1.5426(或由用户输入[的应力水平T=pT.(Die)2e2e[]t[pw]=(Die)pc(Die 接管计算压力0℃头系数壳体内直径度8壳体厚度负偏差壳体腐蚀裕量1010接管厚度负偏差1补强圈厚度负偏差补强圈许用应力1壳体计算厚度接管计算厚度数frr0开孔补强计算直径补强区有效宽度接管有效内伸长度强面积A壳体多余金属面积补强区内的焊缝面积 补强圈面积A-换热器设计换热器概备之一。换热器行业涉及暖通、压力容器、中水处理设备,化工,石油等近30多数据显示2010年中国换热器产业市场规模在500亿元左右,主要集中于石油、量的专业换热器,这些市场约有130亿元的规模。换热器分类和压力降得范围;对、维修的要求;材料价格;使用等。0.6MPa管壳式(又称列管式)换热器是管壳式换热器主要有壳体、管束、管板和封4.614000w/m2.k,大大提高生产效率,更换胶条价格昂贵(胶条的更换费用大约占整个过程的1/3-1/2).主要应用于换热器的选型外形和规格的压降越大,为了满足允许的压力降一般选用Ф19mm的管子。对于易结垢的物低。所以,在管程结垢不是很严重,又允许压力降较高的情况下,采用Φ19mm×2mm的管子是合理的。属耗量,更为经济。因此,一般选用管长4~6m。对于大面积或无相变的换热器8~9m洁不便、壳程压降增大,一般选用范围为管外径的1.25~1.5倍。壳程和台数6~8工艺条件限制60℃,以免结垢严重。高温端的温差不应小于温差不应小于20℃。在冷却或者冷凝工艺物流时,冷却剂的温度应高于工用温度,一般高15°C。压力介于9.8×104𝑃𝑎至16.7×104𝑃𝑎之间时,允许压力降介于3.3×103𝑃𝑎至3.9×⑥较脏和易结垢的物流应走管程,以便和控制结垢。若必须走壳程,⑦流量较少的物流应走壳程,因为在壳使物流成为湍流状态,从而增换热器设计工艺数据汇总换器》以及《化工工艺设计手册第二版(下》第四版,使用AspenDesignandRatingV8.8表5.8E0101换热器物流参操作条件参壳管MDEAMDEA质量流量进口温度出口温度进口压力出口压力类型选择3.1L、ML对于壳体而言,“E”型较为经济,是选择壳体时的首选类型,“F”型当换必须为偶数。根据介质情况,这里选择E型壳体。温度和压力该换热器的壳程工作温度为110℃,管程工作温度为50℃,温差大于为160℃,管程的设计温度为90℃。这里取壳程设计压力为0.3MPa,管程的设计压力为1.1MPa这里也要考虑压降小于0.1MPa(真空条件压降不大于进口压强的40%,出口绝压大于0.1MPa,压降不大于进口压强的20%。传热系数EDR自动默认值。该换热器的管程为冷却水,根据《化工工艺设二氧化硫腐蚀气体气相,同样查得手册上的平均污垢系数为0.000073m2K/W。尺EDRGB/T28712.2-换热管数量为504EDR默认值。进而确定换热器E0101型号为BES700-1.1/0.3-165.3-3/19-封头管箱:700-换热器公称直径(mm。1.1-管程设计压力(MPa,0.3-壳(MPa3详细结
5.85.9换热器的机械设计及校核化氢,因此管子选择S30408钢板制造,壳体使用Q345R比较妥当。5.9入数目目输入数 项 计算结果5.10SW6算项 计算结果上封头壁 设备筒体壁上封头壁 管板壁 下封头壁管板壁 设备法兰复 合5.11入设计计 件程pt程t设计温度t管箱圆筒内径简图计算内容5.12前段管箱筒体计计算所依据的标 GB150.3-设计温度内径(板材负偏差 = e=n-C1-C2= n n
pT=pT= 平T
T0.90ReL pT.(Die)2e.T= ( (Die)=pc(Die 算应 t
=结 合 校核条结 合 设计温度设计温度
计算所依据的标 GB150.3-计算条 椭圆封头简计算条 椭圆封头简内径内径 负偏差系数]pT]的应 T
pT.(KDi0.5eh压力试验允许 T压力试验允许 T0.90ReL过的应力校核条校核条 T
校核结 合
21 D22 ih2[]h2[]t0.5=K i=eh=nh-C1-C2=min=nh= 2[]teh w [p KDi0.5ehw 2[]t=5.13后端管箱筒体计后端管箱筒体计 计算单计算条 筒体简 计算条 筒体简 t 内径 (板材 试验温度下屈服点 负偏差 腐蚀裕量 焊接接头系数 e=n-C1-C2=n [试验压力 [ pT= T0.90ReL 的应力水平pT.(DieT 2e =T2e[]t (Die)= pc(Die
= t 表5.14后端管箱封头计算 设计温度 计算压力设计温度 曲面深度 内径曲面深度 材
负偏差负偏差 焊接接头系数 腐蚀裕量焊接接头系数
力T力T0.90ReL
校核条 T校核条 T
pT.(KDi0.5eh2eh =
校核结 合
1
D22 i6 2h计算厚 计算厚 =2[]t0.5 =heh=nh-C1-C2=min=nh=
i= w 2[]teh [p]= KDi0.5 w5.15内压圆筒校核 计算压力t内径(板材试验温度下屈服点负偏差腐蚀裕量焊接接头系数 2[]t=e=n-C1-C2=n [] pT=[ (或由用户输入T0.90ReL的应力水平pT.(DieT 2e=T (Die)=pc(Die
= 校核条 表5.16直管换热管内压计算计算压力设计温度外径aCm负偏差(管材计算压力设计温度外径aCm负偏差(管材腐蚀裕量m焊接接头系数 =2[]t = e=n-C1-C2= n Do=tPc(Doe)=结 直管换热管内压计算合表
温馨提示
- 1. 本站所有资源如无特殊说明,都需要本地电脑安装OFFICE2007和PDF阅读器。图纸软件为CAD,CAXA,PROE,UG,SolidWorks等.压缩文件请下载最新的WinRAR软件解压。
- 2. 本站的文档不包含任何第三方提供的附件图纸等,如果需要附件,请联系上传者。文件的所有权益归上传用户所有。
- 3. 本站RAR压缩包中若带图纸,网页内容里面会有图纸预览,若没有图纸预览就没有图纸。
- 4. 未经权益所有人同意不得将文件中的内容挪作商业或盈利用途。
- 5. 人人文库网仅提供信息存储空间,仅对用户上传内容的表现方式做保护处理,对用户上传分享的文档内容本身不做任何修改或编辑,并不能对任何下载内容负责。
- 6. 下载文件中如有侵权或不适当内容,请与我们联系,我们立即纠正。
- 7. 本站不保证下载资源的准确性、安全性和完整性, 同时也不承担用户因使用这些下载资源对自己和他人造成任何形式的伤害或损失。
最新文档
- 物业电工维修车合同范本
- 消防合同续期协议书范本
- 珠海对口帮扶协议书范本
- 香港投资项目合作协议书
- 销售合作协议中间商合同
- 高中教室出租协议书模板
- 防洪堤项目工程合同范本
- 汽车商贸怎样拟合同协议
- 机构运营合作合同协议书
- 私人幼儿园老师合同范本
- 贵州贵州省建设投资集团有限公司招聘笔试真题2024
- 广西钦州市2024-2025学年高二下学期期末检测英语试题【含答案解析】
- 2025年温州市交通发展集团招聘考试试题(含答案)
- 医药电商区域销售数据特征研究-洞察阐释
- 2025年新修订《治安管理处罚法》
- 【政治 云南卷】2025年云南省高考招生统一考试真题政治试卷(含答案)
- 2025年新疆中考语文真题(原卷版)
- 中式烹调考试试题及答案
- 管道非开挖修复技术课件
- 海上试验活动方案
- 2025至2030中国工业大麻行业深度调研与投资咨询报告
评论
0/150
提交评论