
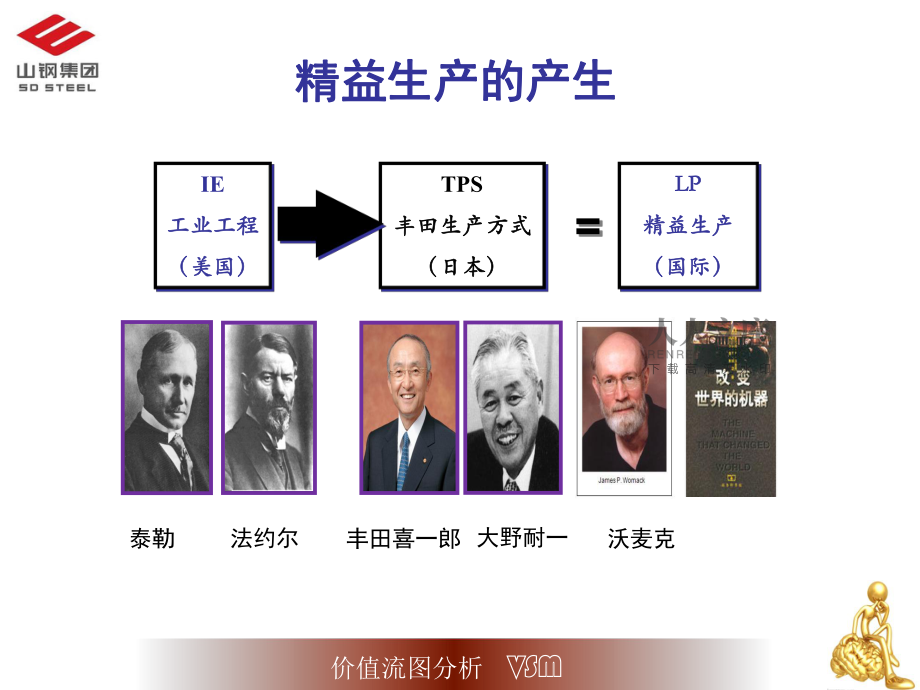



版权说明:本文档由用户提供并上传,收益归属内容提供方,若内容存在侵权,请进行举报或认领
文档简介
1、价值流图分析 VSM价值流图分析价值流图分析查找和发现浪费的精益改善工具莱钢培训中心莱钢培训中心/党校党校 彭双双彭双双 Tel: 6929437 E-mail:价值流图分析 VSMIE工业工程工业工程(美国)(美国)TPS丰田生产方式丰田生产方式(日本)(日本)LPLP精益生产精益生产(国际)(国际) =泰勒法约尔大野耐一丰田喜一郎沃麦克 精益生产的产生精益生产的产生精益管理的本质精益管理的本质价值流图分析 VSM创造 价值价值价值流图分析 VSM精益的基本逻辑精益的基本逻辑目标利润目标利润销售收入目标成本目标成本管理彻底消除浪费 满足客户需求价值流图分析 VSM 价值 浪费 结果过程好的来
2、自于好的?精精益益少投入少投入多产出多产出精益的核心精益的核心价值流图分析 VSM价值流图分析内容纲要价值流图分析内容纲要价值流图分析基本概述价值流图分析基本概述价值、价值流、价值流图分析定义价值、价值流、价值流图分析定义价值流图分析价值流图分析绘制价值流图的基本方法、步骤绘制价值流图的基本方法、步骤 价值流图基本术语、符号说明价值流图基本术语、符号说明 如何界定如何界定VSM范围、对象范围、对象 如何获取正确数据信息如何获取正确数据信息现状价值流图现状价值流图&未来价值流图未来价值流图案例分析案例分析价值流图分析 VSM价值流图基本概述价值流图基本概述 价值流图析(价值流图析(Val
3、ue Stream Mapping,VSM) 。它源于丰田精益。它源于丰田精益制造(制造(Lean Manufacturing)生产系统框架下的一种用来描述物)生产系统框架下的一种用来描述物流和信息流的形象化工具。它通常包括对流和信息流的形象化工具。它通常包括对“当前状态当前状态”和和“未来状未来状态态”两个状态的描摹,两个状态的描摹, 从而作为生产活动战略的基础。从而作为生产活动战略的基础。 适用范围适用范围:VSM帮助管理人员、工程师、生产制造人员、流程规划帮助管理人员、工程师、生产制造人员、流程规划人员、供应商以及顾客去发现浪费人员、供应商以及顾客去发现浪费,它贯穿于生产制造的所有流程、
4、它贯穿于生产制造的所有流程、步骤,步骤, 直到终端产品离开仓储。直到终端产品离开仓储。 主要作用主要作用:VSM能够辨识和减少生产过程中的浪费,寻找浪费根源能够辨识和减少生产过程中的浪费,寻找浪费根源的起点。的起点。 (符合(符合MECE分解原则。分解原则。MECE:Mutually Exclusive,Collectively Exhaustive 。要素之间要相互独立(有排他性),完全穷尽;达到。要素之间要相互独立(有排他性),完全穷尽;达到整体把握问题、整体分析问题。)整体把握问题、整体分析问题。)价值流图分析 VSM 发现浪费发现浪费 并消除浪费并消除浪费构成商品的重要构成商品的重要因
5、素(客户需求)因素(客户需求)创造价值的全过程创造价值的全过程(增值和非增值)(增值和非增值)使创造价值的全过使创造价值的全过程可视化的图示。程可视化的图示。价值价值价值流价值流价值流图价值流图消除一成浪费等于增加一倍利润消除一成浪费等于增加一倍利润 大野耐一大野耐一浪费浪费价值流图基本概述价值流图基本概述价值流图分析 VSM客户客户一切战略、管理的出发点和归宿点都是客户。一切战略、管理的出发点和归宿点都是客户。价值:价值:精益思想中的精益思想中的“价值价值”概念首先是从概念首先是从客户客户的角度定的角度定义义 的,根据的,根据客户客户的需求来定义产品的价值,再由生产的需求来定义产品的价值,再
6、由生产 者创造,最后通过者创造,最后通过客户客户需求的最大满足来实现。需求的最大满足来实现。 (以前的认识是我们创造了产品的价值,并且由此确定了其价值。)(以前的认识是我们创造了产品的价值,并且由此确定了其价值。) 总之,永远站在总之,永远站在客户客户立场上看待我们的工作价立场上看待我们的工作价 值。谁对我们的工作进行最终评判和衡量,谁就是值。谁对我们的工作进行最终评判和衡量,谁就是 我们的我们的客户客户。价值流图基本概述价值流图基本概述价值流图分析 VSM一个产品以下两条流程至关重要:(一个产品以下两条流程至关重要:(价值流图析的主要过程价值流图析的主要过程)从原材料到产品交到客户手中的生产
7、流程。(从原材料到产品交到客户手中的生产流程。(物流物流)从概念到投产的设计流程。(从概念到投产的设计流程。(信息流信息流)一个产品通过这些主要流程所需要的全部活动:一个产品通过这些主要流程所需要的全部活动:增值和非增值活动增值和非增值活动增值活动:增值活动:真正能创造出顾客可以接受的价值的行动。真正能创造出顾客可以接受的价值的行动。非增值活动:非增值活动:必要但不创造价值必要但不创造价值(减少)。(减少)。 如目前产品开发、补充订货、生产系统还需要,因而不能马上取消的活动。为了消如目前产品开发、补充订货、生产系统还需要,因而不能马上取消的活动。为了消除这类型的浪费需要对现有的运作系统作出较大
8、的改变,这些改动不可能马上实施;除这类型的浪费需要对现有的运作系统作出较大的改变,这些改动不可能马上实施;非必要且无价值非必要且无价值(消除)。(消除)。 如那些不能创造价值,并且可以立即取消的活动(纯粹的浪费)如那些不能创造价值,并且可以立即取消的活动(纯粹的浪费)价值流价值流:是为满足客户要求是为满足客户要求,当前产品(不论是一个商品、一项服务,或两者当前产品(不论是一个商品、一项服务,或两者 的结合)通过其基本生产过程所必须的全部活动。的结合)通过其基本生产过程所必须的全部活动。价值流图基本概述价值流图基本概述价值流图分析 VSM 设计原材料总装厂发货客户零件生产需求 统计研究发现,企业
9、生产活动中,增值活动约占企业生产和经营活动统计研究发现,企业生产活动中,增值活动约占企业生产和经营活动的的5 。必要但非增值活动约占。必要但非增值活动约占60 ,其余,其余35 为浪费。价值流管理就是为浪费。价值流管理就是通过绘制价值流图,进行价值流图分析来发现并消灭浪费、降低成本,赢取通过绘制价值流图,进行价值流图分析来发现并消灭浪费、降低成本,赢取最高的边际利润最高的边际利润价值流图基本概述价值流图基本概述价值流图分析 VSM价值流图分析 VSM价值流图:价值流图:查找和发现浪费的精益改善工具。它可以使整个价值流查找和发现浪费的精益改善工具。它可以使整个价值流通常通常 是纷乱复杂的,变为可
10、视的一张价值流现状图。它可以是纷乱复杂的,变为可视的一张价值流现状图。它可以 使得价值流中的问题显现出来。使得价值流中的问题显现出来。 搭建良好沟通平台,从而设定改善方向以及行动计划搭建良好沟通平台,从而设定改善方向以及行动计划 从全盘看待问题,而不是集中于某个单独的过程。从全盘看待问题,而不是集中于某个单独的过程。价值流图的基本构成有四大部分:价值流图的基本构成有四大部分: 顾客部分。顾客发出信息,可能是订单,新产品,等等;顾客部分。顾客发出信息,可能是订单,新产品,等等; 公司系统部分。可能是公司系统部分。可能是ERP, SAP任何系统,顾客信息进入公司系统;任何系统,顾客信息进入公司系统
11、;供应商部分。供应商部分。 内部物料流。主要指产线部分,至少需要人机料内部物料流。主要指产线部分,至少需要人机料(Man, Machine, Material) 价值流图关注的重点部分:价值流图关注的重点部分: 原材料到成品整个制程、工艺上的信息;原材料到成品整个制程、工艺上的信息; 成品到顾客;成品到顾客;关注信息流部分。顾客关注信息流部分。顾客公司系统公司系统-供应商供应商 计算计算L/Time, 同时包含同时包含VA(有价值有价值),NVA(无价值)部分及有价值比例。(无价值)部分及有价值比例。 缩短产品的生产周期是迅速适应市场需求的关键,而价值流程图(缩短产品的生产周期是迅速适应市场需
12、求的关键,而价值流程图(VSM)分析方)分析方法正是了解产品生产周期的有效工具。法正是了解产品生产周期的有效工具。价值流图基本概述价值流图基本概述价值流图分析 VSM简易价值流图简易价值流图部门部门C部门部门B部门部门A客户客户工序工序5工序工序4工序工序3工序工序2工序工序1信信 息息 流流【设计过程 信息管理过程】物物 料料 流流【物料转化过程】 价值流图析图析主要对象价值流图析图析主要对象 (浪费浪费) VSM分析的主旨是立即暴露存在的浪费问题,并彻底排除浪费。只有识别了分析的主旨是立即暴露存在的浪费问题,并彻底排除浪费。只有识别了问题,才能改善,很多不熟悉精益生产的人之所以会遇到一大堆
13、难题,是因为他们问题,才能改善,很多不熟悉精益生产的人之所以会遇到一大堆难题,是因为他们没有找到问题点。因此,要改善企业组织生产过程中的浪费问题,首先要认识浪费。没有找到问题点。因此,要改善企业组织生产过程中的浪费问题,首先要认识浪费。价值流图分析 VSM价值流图基本概述价值流图基本概述信信息息流流物流价值流图分析 VSM价值流图与流程图区别价值流图与流程图区别价值流图价值流图: 让所有人看见整体情况 根据真实数据 改善蓝图 持续改善流程图流程图: 只能反映局部工艺周期、流程 根据工程标准或旧数据 一年一次的大计划价值流图基本概述价值流图基本概述价值流图分析 VSM价值流图析步骤价值流图析步骤
14、 采用采用5W1H方法方法171. Who确定谁来做确定谁来做 需要一位了解产品价值流而且能推进其改进的人,这个人具有领导职责需要一位了解产品价值流而且能推进其改进的人,这个人具有领导职责 (价值流经理价值流经理),由他来领导一个小组进行价值流图析工作。),由他来领导一个小组进行价值流图析工作。2. What确定做哪些产品的价值流图析(确定做哪些产品的价值流图析(正确选择确定物流正确选择确定物流) 通常我们首先按照通常我们首先按照8020原则,对影响企业最大的产品进行图析。原则,对影响企业最大的产品进行图析。3. When确定何时做(确定何时做(正确选择确定物流正确选择确定物流) 应在实施改进
15、之前对价值流进行分析,以确定应首先改进哪些过程。应在实施改进之前对价值流进行分析,以确定应首先改进哪些过程。4. Where确定在哪里做(确定在哪里做(如何获取真实、正确的数据信息如何获取真实、正确的数据信息) 在现场!只有在现场收集的数据才能真正反映价值流的状况。在现场!只有在现场收集的数据才能真正反映价值流的状况。5.Why为什么做价值流图析为什么做价值流图析 明确价值明确价值,消除浪费消除浪费6、 How进行图析进行图析 静静“思思”于事前于事前 细细“做做”重重过程过程价值流图分析 VSM 认识基本术语认识基本术语周期周期(Cycle Time) -工件/产品由一个工序制造一个工序制造
16、所需的时间增值时间增值时间(Value Added Time) -增值活动增值活动所需的时间交付周期交付周期(前置期Lead Time) -物料流过整条价值流整条价值流所需的时间一切都是缩短时间一切都是缩短时间 时间就是金钱!时间就是金钱!缩短交付周期缩短交付周期(周期1+周期2+)缩短周期(增值时间&非增值时间)压缩非增值时间实现精益目标(增值时间(增值时间+非增值时间)非增值时间)炼钢时刻表 以时间为轴线,统揽全厂各工序以时间为轴线,统揽全厂各工序生产状况,以减少过程浪费!生产状况,以减少过程浪费!价值流图分析 VSM认识基本图示认识基本图示工序名称工序名称加工时间:加工时间:15
17、S转款时间:转款时间:1hrIFIFOKaizenBurst生产看板生产看板生产过程生产过程库存库存手动资讯手动资讯电子资讯电子资讯作业人员作业人员货车运送货车运送推动物料推动物料送产品到客户送产品到客户先入先出先入先出改善标志改善标志提取物料提取物料超市超市缓存缓存/备用备用库存库存供应商供应商/客户客户提取看板提取看板信号看板信号看板看板收集处看板收集处 根据各公司情况增添一些与自己生产产品相关的图标信息,但根据各公司情况增添一些与自己生产产品相关的图标信息,但整个公司各类图标信息的含义必须一致。整个公司各类图标信息的含义必须一致。价值流图分析 VSM绘画现况的价值流图的步骤绘画现况的价值
18、流图的步骤1.了解客户需求了解客户需求2.绘制基本生产工序绘制基本生产工序3.设定要收集的数据及输入数据设定要收集的数据及输入数据4.绘制库存,标注库存量绘制库存,标注库存量5.设定供应商数据设定供应商数据6.加入资讯流加入资讯流7.计算现况的状态计算现况的状态价值流图分析 VSM绘制现状价值流图绘制现状价值流图 从顾客要求开始,门到门的层面展开从顾客要求开始,门到门的层面展开 第一步:明确并简化顾客要求第一步:明确并简化顾客要求 如:国家大道装配厂采用两班制,如:国家大道装配厂采用两班制,这个顾客每月使用这个顾客每月使用1840018400件转件转向盘支架并要求每天送货。一向盘支架并要求每天
19、送货。一般每月需要般每月需要12001200件件“左置左置”支支架和架和64006400件件“右置支架。要求右置支架。要求一只周转箱内放一只周转箱内放2020个支架,每个支架,每一个集装箱最多放一个集装箱最多放1010个周转箱个周转箱价值流图分析 VSM第二步:画出基本的生产过程(即生产流程步骤)第二步:画出基本的生产过程(即生产流程步骤) 材料流的绘制在图的下半部分由左向右进行。在该工厂,材料流的绘制在图的下半部分由左向右进行。在该工厂,转向盘支架需要进行六个过程:冲压、点焊转向盘支架需要进行六个过程:冲压、点焊1 1工位、点焊工位、点焊2 2工位、装配工位、装配1 1工位、装配工位、装配2
20、 2工位、发运工位、发运冲压冲压200T点焊点焊1#1点焊点焊2#1装配装配1#1装配装配2#1发运发运平台价值流图分析 VSM第三步:画数据箱第三步:画数据箱冲压冲压200T点焊点焊1#1点焊点焊2#1装配装配1#1装配装配2#1发运发运平台C/T=1SC/O=1h使用率=85%有效时间27600s准备量2周C/T=38SC/O=10min使用率=100%有效时间27600s两班工作C/T=45SC/O=10min使用率=80%有效时间27600s两班工作C/T=62SC/O=0使用率=100%有效时间27600s两班工作C/T=40SC/O=0使用率=100%有效时间27600s两班工作沿
21、材料流动,需收集(决定未来状态)的重要数据沿材料流动,需收集(决定未来状态)的重要数据价值流图分析 VSM第四步:画出库存,标注第四步:画出库存,标注“库存量库存量”(同时用数量和时间标记)(同时用数量和时间标记)沿着产品价值流走动,会发现库存堆积的地方沿着产品价值流走动,会发现库存堆积的地方 冲压冲压200T点焊点焊1#1点焊点焊2#1装配装配1#1装配装配2#1发运发运平台C/T=1SC/O=1h使用率=85%有效时间27600s准备量2周C/T=38SC/O=10min使用率=100%有效时间27600s两班工作C/T=45SC/O=10min使用率=80%有效时间27600s两班工作C
22、/T=62SC/O=0使用率=100%有效时间27600s两班工作C/T=40SC/O=0使用率=100%有效时间27600s两班工作I5天的天的卷材卷材I4600左左2400右右I1100左左600右右I1600左左850右右I1200左左640右右I2700左左1440右右内部指标外部指标外部指标价值流图分析 VSM第五步:画出成品运达顾客,另一头画出供应商供货情况第五步:画出成品运达顾客,另一头画出供应商供货情况冲压冲压200T点焊点焊1#1点焊点焊2#1装配装配1#1装配装配2#1发运发运平台C/T=1SC/O=1h使用率=85%有效时间27600s准备量2周C/T=38SC/O=10
23、min使用率=100%有效时间27600s两班工作C/T=45SC/O=10min使用率=80%有效时间27600s两班工作C/T=62SC/O=0使用率=100%有效时间27600s两班工作C/T=40SC/O=0使用率=100%有效时间27600s两班工作I5天的天的卷材卷材I4600左左2400右右I1100左左600右右I1600左左850右右I1200左左640右右I2700左左1440右右每日1次周二、四各1次价值流图分析 VSM第六步:绘制信息流,在图的上半部从右向左画第六步:绘制信息流,在图的上半部从右向左画 冲压冲压200T点焊点焊1#1点焊点焊2#1装配装配1#1装配装配2
24、#1发运发运平台C/T=1SC/O=1h使用率=85%有效时间27600s准备量2周C/T=38SC/O=10min使用率=100%有效时间27600s两班工作C/T=45SC/O=10min使用率=80%有效时间27600s两班工作C/T=62SC/O=0使用率=100%有效时间27600s两班工作C/T=40SC/O=0使用率=100%有效时间27600s两班工作I5天的天的卷材卷材I4600左左2400右右I1100左左600右右I1600左左850右右I1200左左640右右I2700左左1440右右每日1次周二、四各1次生产控制部生产控制部MRP90/60/30d 预测每日订货6周
25、预测每周传真每周计划每日发运计划价值流图分析 VSM5d5d1s1s7.6d7.6d38s38s1.8d1.8d45s45s2.7d2.7d62s62s2d2d40s40s4.5d4.5d增值时间增值时间=188s=188s周期周期= 23.6d= 23.6d第七步:画出时间线第七步:画出时间线价值流图分析 VSM 从以上案例我们可以看出,188秒的生产时间只占然整个周期时间23.6天的不到1%,大量的时间浪费在库存和等待上了。 188秒 23.6 天*24小时*60分钟*60秒 (非增值活动,我们改善针对的主要对象)(非增值活动,我们改善针对的主要对象)0.0092%价值流图分析 VSM现况
26、价值流图现况价值流图 VS 将来价值流图将来价值流图 现况价值流图现况价值流图(current state map) 企业变革的起点,改进的基本前提企业变革的起点,改进的基本前提 未来价值流图未来价值流图(future state map) 关注价值流未来设计的方向,精益变革中关注价值流未来设计的方向,精益变革中 要达到的预期目标要达到的预期目标现况价值流图现况价值流图 VS 将来价值流图将来价值流图价值流图分析 VSM为何进行价值流图分析?为何进行价值流图分析?现状图的目的就是要使当前生产状况所存在现状图的目的就是要使当前生产状况所存在的浪费用画图和计算的方式充分显现出来,的浪费用画图和计算
27、的方式充分显现出来,找出找出根本根本原因,采取措施原因,采取措施逐步逐步完善。完善。 (浪费浪费)未来状态图就是使得当前价值流变成精益的未来状态图就是使得当前价值流变成精益的价值流。通过解决问题(价值流。通过解决问题(浪费浪费)得到理想状)得到理想状态的未来价值流图态的未来价值流图利用分析得到的结论做为重要依据,进行持利用分析得到的结论做为重要依据,进行持续稳步的改进,创造更多价值达到完美状态续稳步的改进,创造更多价值达到完美状态的精益目标的精益目标(改善改善 Kaizen)产品系列产品系列 未来状态图未来状态图 工作计划与实施工作计划与实施 现状图现状图分析的目的分析的目的(关键的最终目标)
28、(关键的最终目标)“图析图析”并不能实现精益,它仅仅是一种技术,重要的是如何利用它实现增值流并不能实现精益,它仅仅是一种技术,重要的是如何利用它实现增值流动。动。 价值流图分析 VSM如何更好的做好价值流图分析?如何更好的做好价值流图分析? 问题树问题树应用问题树的目的在于对问题的应用问题树的目的在于对问题的 思考更完整、更有条理;思考更完整、更有条理;确定各问题要素的优先顺序;确定各问题要素的优先顺序;对问题进行分解和细化,有利于下对问题进行分解和细化,有利于下一步有针对性地收集数据。一步有针对性地收集数据。 应用问题树工具进行全面分析应用问题树工具进行全面分析有利于在项目中建立共识,抓住重
29、有利于在项目中建立共识,抓住重点,找到问题的根解,防止问题解点,找到问题的根解,防止问题解决的片面性,对问题背景整体的、决的片面性,对问题背景整体的、系统的把握是非常重要的。系统的把握是非常重要的。 5W法法5W法找到问题发生点深入挖掘根法找到问题发生点深入挖掘根本原因,治标更治本。避免救火式本原因,治标更治本。避免救火式解决问题,只管灭火不管起火根源解决问题,只管灭火不管起火根源的解决之道。的解决之道。5why法的关键所在:鼓励解决问法的关键所在:鼓励解决问题的人要努力避开主观或自负的假题的人要努力避开主观或自负的假设和逻辑陷阱,从结果着手,沿着设和逻辑陷阱,从结果着手,沿着因果关系链条,顺
30、藤摸瓜,直至找因果关系链条,顺藤摸瓜,直至找出原有问题的根本原因。出原有问题的根本原因。案例案例价值流图分析 VSM问题树:问题树:把现状图中把现状图中发现的所有问题进行发现的所有问题进行逻辑梳理并排序,决逻辑梳理并排序,决定改善的优先序定改善的优先序现状图:现状图:企业变革的起点企业变革的起点 一切改善活动的基础。显露现状中一切改善活动的基础。显露现状中 所有问题的基础工具。所有问题的基础工具。未来图:未来图:以现状图为基础,设计未来理想的价值流图,实现以现状图为基础,设计未来理想的价值流图,实现 精益变革目标精益变革目标5W法:法:找到现状图中找到现状图中发现问题的根源所在,发现问题的根源
31、所在,从根本上解决问题彻从根本上解决问题彻底消除浪费底消除浪费如何更好的做好价值流图分析?如何更好的做好价值流图分析?价值流图分析 VSM21 价值流图分析实现的精益的目标(价值流图分析实现的精益的目标(实现尽善尽美实现尽善尽美) 计算(Takt Time 生产节拍)使生产节拍和需求同步 满足客户(尽量缩短 交付周期对非增值时间的压缩是关键对非增值时间的压缩是关键) 建立连续流 在不能连续的地方建立拉动超市 改善价值流中的关键环节 确立未来状态 检查未来状态是否消除了浪费的根本原因计划与执行价值流图流分析计划与执行价值流图流分析价值流图分析 VSM 就改善策略来说,无论是公司级大项目还是员工操
32、作过程,我们就改善策略来说,无论是公司级大项目还是员工操作过程,我们可以参照工业工程所提出的可以参照工业工程所提出的ECRS改善原则进行。改善原则进行。E:排除(:排除(Eliminate):除掉不必要的步骤和重复步骤;):除掉不必要的步骤和重复步骤; C:结合(:结合(Combine):和别的作业结合一起进行,省去浪费;):和别的作业结合一起进行,省去浪费; R:重新配置(:重新配置(Rearrange):改变作业的顺序):改变作业的顺序,省去浪费;省去浪费;S:简单化(:简单化(Simplify):使作业单纯化,改善细微顺序来省去):使作业单纯化,改善细微顺序来省去 浪费。浪费。 这样,流
33、程的连续性、平稳性就会向这样,流程的连续性、平稳性就会向“好好”转变,向未来价值转变,向未来价值流图所提出的目标迈进。流图所提出的目标迈进。价值流图分析 VSM完整的现况价值流图完整的现况价值流图供应商供应商周二及周二及周四周四6周预算周预算每周每周FAX生产控制生产控制MRP90/60/30日预算日预算每天订单每天订单出货时出货时间表间表客户客户18.400件件/月月12.000件(左)件(左)6.400件(右)件(右)20件件/箱箱每天每天一次一次生产流程生产流程发送组装21组装11冲压1焊接11焊接21IIIIII来料来料5天天4600左左2400右右1100左左600右右1600左左8
34、50右右1200左左640右右2700左左1440右右加工加工转款转款生产生产1秒秒1小时小时460分钟分钟加工加工转款转款生产生产39秒秒10分钟分钟460分钟分钟加工加工转款转款生产生产46秒秒10分钟分钟460分钟分钟加工加工转款转款生产生产62秒秒0秒秒460分钟分钟加工加工转款转款生产生产40秒秒0秒秒460分钟分钟4.6天天7.6天天1.8天天2.7天天2天天5天天1秒秒39秒秒46秒秒62秒秒40秒秒23.6天天188秒秒每周生产计划每周生产计划11265347增值比增值比=加工时间加工时间/生产前置期生产前置期 =188/(23.6*24*3600)=0.0092%价值流图分析
35、 VSM实际生产节拍实际生产节拍=客户需求节拍客户需求节拍节拍时间节拍时间 =有效工作时间有效工作时间(增值时间增值时间+非增值时间非增值时间)客户需求量客户需求量价值流图分析 VSM将来价值流图将来价值流图供应商供应商每日每日6周预算周预算每日订单每日订单生产控制生产控制MRP90/60/30日预算日预算每天订单每天订单每日配送规划每日配送规划客户厂房客户厂房18.400件件/月月12.000件(左)件(左)6.400件(右)件(右)20件件/箱箱每日每日一次一次交付周期时间交付周期时间=5天天500吨吨1.5天天冲压冲压2000吨吨1.5天天周期时间周期时间=1秒秒换模时间换模时间=1小时
36、小时开机率开机率=85%1人人数量数量焊接焊接+装配装配6020单位制造时间单位制造时间=20分钟分钟右左右左右左。右左右左右左。2020204123节拍时间节拍时间=60秒秒周期时间周期时间=55秒秒3人人总工作量总工作量165秒秒焊接换模焊接换模连续开机时间连续开机时间加工时间加工时间=166秒秒1.5天天1.5天天2天天1秒秒165秒秒2天天发货发货配送配送920件件/天天节拍时间节拍时间=60秒秒460件件460分钟分钟46盘盘增值比增值比=加工时间加工时间/生产前置期生产前置期 =166/(5*24*3600)=0.038%价值流图分析 VSM增值性环节只占整个生产周期的很小部分增值
37、性环节只占整个生产周期的很小部分传统的成本节约活动致力于对增值环节的改进传统的成本节约活动致力于对增值环节的改进精益改进活动致力于对非增值环节的压缩与消除精益改进活动致力于对非增值环节的压缩与消除 时时 间间 原原 料料 成成 品品 等等 待待 存存 放放 运运 输输 检检 验验 切切 换换 = 增增 值值 时时 间间 = 非非 增增 值值 时时 间间 (浪浪 费费 ) 机机 加加 工工 组组 装装 铸铸 造造 价值流图分析揭示的问题价值流图分析揭示的问题价值流图分析 VSM 今天我们需要化繁为简,重新回归管理的本质,就是为客户创造今天我们需要化繁为简,重新回归管理的本质,就是为客户创造价值这
38、一句话,没有第二句。价值这一句话,没有第二句。价值流图基本概述价值流图基本概述聚焦客户聚焦客户简化管理简化管理活力创新活力创新实现价值实现价值这十六个字是因果关系,相互承接,一切管理都要忘记概念,回归本质。这十六个字是因果关系,相互承接,一切管理都要忘记概念,回归本质。 价值流图分析 VSM案案 例例 分分 析析价值流图分析 VSM 炼钢厂炼钢厂4#4#切割机流程分析切割机流程分析价值流图分析 VSM主要问题(称重不精准)主要问题(称重不精准) 一是母坯切割定尺不准、摄像定尺镜头产生的检测误差;二是火切机行速快造成一是母坯切割定尺不准、摄像定尺镜头产生的检测误差;二是火切机行速快造成定位误差;
39、三压下距离偏大、压力不稳。定位误差;三压下距离偏大、压力不稳。改善:改善: 母坯切割采用激光精准定位母坯切割采用激光精准定位 ,降低火切机速度精准压下定位,调整压下间隙及增加,降低火切机速度精准压下定位,调整压下间隙及增加辅助设备,减少压下时间及增加压下稳定性辅助设备,减少压下时间及增加压下稳定性亮点:亮点: 通过对流程的主动梳理发现了速赢机会;通过对流程的主动梳理发现了速赢机会; 通过对系统资源的优化配置及合理改善带来可观的效益。通过对系统资源的优化配置及合理改善带来可观的效益。效益:效益: 增效增效68.76万元万元/月,预计年增效月,预计年增效700万元以上。万元以上。炼钢厂炼钢厂4#4
40、#切割机流程分析切割机流程分析详细案例价值流图分析 VSM第一步:确定边界 (顾客,供应商)顾客:顾客:宽厚板厂供应商:供应商:连铸机铸坯质量符合要求铸坯质量符合要求定尺要求:定尺要求:-10mm+50mm定重要求:定重要求:0 30kg价值流图分析 VSM第二步:画出物料流各主要环节检测压下切割定位检测找位切割定位价值流图分析 VSM第三步:在每个物料流环节下方标注主要指标情况切割车使用编码器定位精度误差在0-10mm使用镜头检测误差在10mm200断面压下距离:160mm250断面压下距离:110mm300断面压下距离:60mm同一断面压下延时误差0.2秒切割枪:存在变形切割车使用编码器定
41、位精度误差在0-10mm使用镜头检测误差在8mm切割车使用编码器找位精度误差15mm切割枪:存在变形一切二切检测压下切割定位检测找位切割定位价值流图分析 VSM第四步:画出信息流第四步:画出信息流连铸机火切工宽厚板铸坯质量符合要求定尺要求:定尺要求:-10mm+50mm定重要求:定重要求:0 30kg切割车使用编码器定位精度误差在0-10mm使用镜头检测误差在10mm200断面压下距离:160mm250断面压下距离:110mm300断面压下距离:60mm同一断面压下延时误差0.2秒切割枪:存在变形切割车使用编码器定位精度误差在0-10mm使用镜头检测误差在8mm切割车使用编码器找位精度误差15
42、mm切割枪:存在变形一切二切检测压下切割定位检测找位切割定位设定定尺参数设定定尺参数调整割枪调整割枪价值流图分析 VSM第五步:识别浪费第五步:识别浪费 1、摄像定尺镜头产生的检测误差。 2、火切机走位产生的执行误差。 3、人工修正产生的修正误差。 4、称重产生的称重误差。 5、复测时产生的复测误差。 6、计划下达错误造成的误差。价值流图分析 VSM分析查找问题标注改善机会连铸机火切工宽厚板铸坯质量符合要求定尺要求:定尺要求:-10mm+50mm定重要求:定重要求:0 30kg切割车使用编码器定位精度误差在0-10mm使用镜头检测误差在10mm200断面压下距离:160mm250断面压下距离:
43、110mm300断面压下距离:60mm同一断面压下延时误差0.2秒切割枪:存在变形切割车使用编码器定位精度误差在0-10mm使用镜头检测误差在8mm切割车使用编码器找位精度误差15mm切割枪:存在变形一切二切检测压下切割定位检测找位切割定位设定定尺参数设定定尺参数调整割枪调整割枪定位不准压下距离偏大压下压力不稳定定位不准割枪变形价值流图分析 VSM4#机激光定位提高定尺精度措施机激光定位提高定尺精度措施1、对火切机走位产生的误差使用激光定位来准确检测火切机位置并指导停、对火切机走位产生的误差使用激光定位来准确检测火切机位置并指导停位。同时将火切机行走驱动机构的慢速减慢,转矩提高。提高位置检测位
44、。同时将火切机行走驱动机构的慢速减慢,转矩提高。提高位置检测和停位的准确度。目前该工作已完成和停位的准确度。目前该工作已完成2、针对人工修正操作误差造成的误差,对人工修正参数做了程序记录,使、针对人工修正操作误差造成的误差,对人工修正参数做了程序记录,使操作人员的操作能够自我监督以及他人监督。操作人员的操作能够自我监督以及他人监督。3、称重的误差使用定尺复测系统和定重比对称进行校验。、称重的误差使用定尺复测系统和定重比对称进行校验。4、对于复测系统的误差,目前复测考虑使用激光复测进行精度提高。复测、对于复测系统的误差,目前复测考虑使用激光复测进行精度提高。复测准确度提高了,可以准确反馈生产的信
45、息。准确度提高了,可以准确反馈生产的信息。5、对摄像镜头的本身误差,目前考虑增加镜头以及使用激光辅助来提高。、对摄像镜头的本身误差,目前考虑增加镜头以及使用激光辅助来提高。6、生产计划下达的准确度,修改计划下达程序,使错误能够修改,并提高、生产计划下达的准确度,修改计划下达程序,使错误能够修改,并提高调度室人员的操作责任心。调度室人员的操作责任心。价值流图分析 VSM型钢型钢265烧结机燃料破碎系统烧结机燃料破碎系统圆盘筛分四辊数量6个,全部使用;来料种类4-6种;仓位控制不定。朝鲜煤水分10%时,粘仓、悬仓严重数量:6台转度:4.74m/s3#为变频(供料量可调),其余5台为非变频(供料量不
46、可调)。间距12mm;晒面面积为1.5*1.7m筛棒夹料严重,筛分能力40t/h。来料粒度较粗且不定上辊不起作用,故障率高。破碎粒度75%左右仓位1/2-2/3单仓用时8-12小时矿槽配料粒度78-82%配料误差4% %使用2个秤配比合适烧结矿含量稳定终点控制合适烧结筛分供混一车间棒磨机破碎电流:14-15破碎能力50-60 /功率:710台数:1台烧结一车间配料一车间调度配料班组燃料班组上料信息倒仓完成倒仓完成粒度、水分、仓位信息开始使用通知燃料倒仓信息设定量、粒度、配比要求配料室倒仓完成供料充足水分合适、成分合适品种准确、无混料煤粗焦粉小焦混煤燃仓-1外加焦皮带供量连续充足;配比准确;粒度
47、合适;转1-1筛-1、筛-2配5.6.7.13.14汽车倒运汽车外运转21-1棒-1破-6棒-2棒-3、棒-4棒磨机耗电量大维修费用高存在较大浪费熔燃仓焦仓-1转2-1、转4-1破-1、破-2价值流图分析 VSM熔燃仓圆盘皮带筛分四辊数量6个,全部使用;来料种类4-6种;仓位控制不定。朝鲜煤水分10%时,粘仓、悬仓严重有备用的空料仓;(现状不满足)来料为焦粉和煤粉;(现状不满足)仓位控制1/2;(现状不满足)料种进仓水分10%(现状不满足)供料量可调且充足;(现状不满足)数量:6台转度:4.74m/s3#为变频(供料量可调),其余5台为非变频(供料量不可调)。带宽650mm 带速1.6m/s
48、能力50%,5mm%10%;(现状不满足)上辊必须正常使用。(现状不满足)破碎粒度(802)%(现状不满足)来料粒度较粗且不定;上辊不起作用,故障率高。破碎粒度75%左右燃料系统精益流程分析燃料系统精益流程分析实例实例价值流图分析 VSM问题:问题: 一是棒磨机环节,用电量比较大;二是棒磨机钢材消耗比较多;三是维修工作量一是棒磨机环节,用电量比较大;二是棒磨机钢材消耗比较多;三是维修工作量比较大。比较大。改善:改善: 在不增加投入的情况下(同时停用棒磨机)在不增加投入的情况下(同时停用棒磨机) ,充分发挥原有设备潜能,对四辊机、,充分发挥原有设备潜能,对四辊机、振筛、圆盘、皮带机进行调整。既保
49、证了原料供应,还消除了浪费环节,实现了精振筛、圆盘、皮带机进行调整。既保证了原料供应,还消除了浪费环节,实现了精益管控。益管控。亮点:亮点: 通过对流程的主动梳理发现了速赢机会;通过对流程的主动梳理发现了速赢机会; 通过对系统资源的优化配置,以较小的投入甚至零投入也能够换来可观的效益。通过对系统资源的优化配置,以较小的投入甚至零投入也能够换来可观的效益。效益:效益: 节电节电20万度万度/月,降低成本月,降低成本15万元万元/月,节约钢材消耗月,节约钢材消耗10万元万元/月,年可降本月,年可降本300万元。万元。 燃料系统精益流程分析燃料系统精益流程分析实例实例价值流图分析 VSM认识价值流图
50、应用价值流图分析实现最终精益目标提升企业核心竞争力价值流图分析 VSM焦点问题焦点问题什么是什么是浪费浪费不为产品增加价值的任何事情不为产品增加价值的任何事情不利于生产不符合客户要求的任何事情不利于生产不符合客户要求的任何事情顾客不愿付钱由你去做的任何事情顾客不愿付钱由你去做的任何事情尽管是增加价值的活动,但所用的资源超过了尽管是增加价值的活动,但所用的资源超过了 “绝对最少绝对最少”的界限,也是浪费的界限,也是浪费价值流图分析 VSM1. 生产过剩的浪费生产过剩的浪费 2. 等待的浪费等待的浪费 3. 搬运的浪费搬运的浪费 4. 过度加工的浪费过度加工的浪费 5. 库存的浪费库存的浪费 6.
51、 动作的浪费动作的浪费 7. 纠正错误的浪费纠正错误的浪费 浪费的种类浪费的种类 价值流图分析 VSM搬运搬运 等待等待 库存库存 过度加工过度加工 动作动作 纠错纠错 生产生产过剩过剩 七种浪费彼此息息相关七种浪费彼此息息相关价值流图分析 VSM制造过多或过早,造成库存而产生的浪费。制造过多或过早,造成库存而产生的浪费。是浪费(产生库存)的源头是浪费(产生库存)的源头是最大的浪费是最大的浪费 生产过剩的浪费生产过剩的浪费 流程阻碍,半成品的增加,材料、零件的滥用,资金周转率下降,不良的发生、库存。价值流图分析 VSM 库存的浪费库存的浪费 库存:库存: 一切目前闲置的、用于未来的、有经济价值
52、的资源一切目前闲置的、用于未来的、有经济价值的资源。库存是万恶之源库存是万恶之源 生产过剩的结果生产过剩的结果 材料、零件、加工品的停滞,导致交付期的延长,空间的使用浪费,搬运、检查的产生,周转资金的增加。价值流图分析 VSM生产过剩生产过剩库库 存存两大浪费两大浪费 的相互关系的相互关系拉动式生产拉动式生产导导 致致反反 映映价值流图分析 VSM 明确的能够创造价值的活动时间(明确的能够创造价值的活动时间(增值时间增值时间) 不能创造价值,但在现有技术与生产条件下不可避免的不能创造价值,但在现有技术与生产条件下不可避免的活动时间(活动时间(非增值时间非增值时间 浪费的载体浪费的载体) 不能创
53、造价值而且可以立即去除的活动时间(不能创造价值而且可以立即去除的活动时间(非增值时非增值时间间 浪费的载体浪费的载体)价值流图分析 VSM炼钢生产时刻表炼钢生产时刻表价值流图分析 VSM所有工序所有工序调度工序调度工序转炉界面:(转炉界面:(2#炉)炉)吹氩平台吹氩平台连铸画面连铸画面价值流图分析 VSM所有工序所有工序价值流图分析 VSM调度工序调度工序价值流图分析 VSM转炉界面:(转炉界面:(2#炉)炉)价值流图分析 VSM吹氩平台吹氩平台价值流图分析 VSM连铸画面连铸画面价值流图分析 VSM泰勒泰勒-科学管理之父科学管理之父弗雷德里克弗雷德里克温斯洛温斯洛泰勒(泰勒(Frederic
54、k Winslow Taylor,1856年年1915年年),美国美国著名著名管理学家管理学家,经济学家经济学家,被后世称为,被后世称为“科学管理之父科学管理之父”,一个影响了人类工业化进程的人,其代表作为,一个影响了人类工业化进程的人,其代表作为科学管理原理科学管理原理20世纪初,工业开始进入世纪初,工业开始进入“科学管理时代科学管理时代”,美国工程师,美国工程师泰勒泰勒(F.W.Taylor)发表的)发表的科学管理原理科学管理原理是这一时代的代表作和工业工是这一时代的代表作和工业工程的经典著作。程的经典著作。 1917年成立了年成立了IE协会和泰勒协会。协会和泰勒协会。 价值流图分析 VS
55、M法约尔法约尔-经营管理学之父经营管理学之父亨利亨利法约尔法约尔(Henri Fayol,1841年年1925年)年)),法国,法国古典管理理论古典管理理论的主要代表人之一,的主要代表人之一,经营管理学经营管理学之父,亦为之父,亦为管理过程学派管理过程学派的创始人。的创始人。法约尔的法约尔的14原则和原则和5要素在要素在现代管理现代管理中的理论成为管理史上的一个重中的理论成为管理史上的一个重要的里程碑。要的里程碑。法约尔与泰勒一样同属于法约尔与泰勒一样同属于管理学派管理学派,泰勒的理论侧重于在工厂中提高,泰勒的理论侧重于在工厂中提高劳动生产率的问题,注重劳动生产率的问题,注重“哲学哲学”和方法
56、,而法约尔则侧重于高层管和方法,而法约尔则侧重于高层管理理论,注重理理论,注重“原则原则”和要素,他们的理论互为补充,他们的思想共和要素,他们的理论互为补充,他们的思想共同构成了同构成了古典管理理论古典管理理论的基础。的基础。价值流图分析 VSM丰田喜一郎丰田喜一郎丰田丰田喜一郎喜一郎(Kiichiro Toyoda,1894 11.06 - 1952 03.27)丰田汽车公司丰田汽车公司的创始人,的创始人,日本日本汽车工业的先驱者汽车工业的先驱者 丰田喜一郎丰田喜一郎丰田汽车公司的创始人。他缔造了丰田汽车工业股份有限公丰田汽车公司的创始人。他缔造了丰田汽车工业股份有限公司,实现了父亲的遗愿:
57、生产司,实现了父亲的遗愿:生产“日本制造日本制造”的汽车。的汽车。价值流图分析 VSM大野耐一大野耐一 大野耐一大野耐一(Taiichi Ohno 1912-1990),著名的,著名的丰田生产方丰田生产方式式的创始人,被日本人称为:的创始人,被日本人称为:“日本复活之父日本复活之父”、“生产生产管理的教父管理的教父”、“穿着工装的圣贤穿着工装的圣贤”大野耐一,大野耐一,1912年年出生于中国大连。出生于中国大连。 大野耐一在其所著的大野耐一在其所著的丰田生产方式丰田生产方式一书中评价一书中评价“: “准时化准时化”和和“自働化自働化”是丰田生产方式的两大支柱。是丰田生产方式的两大支柱。 价值流
58、图分析 VSM沃麦克沃麦克沃麦克博士是沃麦克博士是“精益企业精益企业”的先驱者,倡导用较少的资源创造更的先驱者,倡导用较少的资源创造更大的价值。他与丹尼尔大的价值。他与丹尼尔琼斯教授合著了琼斯教授合著了改变世界的机器改变世界的机器,此,此著作是汽车工业生产方式演进的一部简化的编年史。著作是汽车工业生产方式演进的一部简化的编年史。1997年沃麦克博士创立了精益企业研究院(年沃麦克博士创立了精益企业研究院(Lean Enterprise Institute,LEI),为精益思想的创新做出贡献。),为精益思想的创新做出贡献。价值流图分析 VSM探索精益需求探索精益需求 USA Motors丰丰 田田
59、1950年年: 劳动生产率是日本的劳动生产率是日本的8-9倍倍1982:人均年产人均年产11.5辆车辆车1950年年与美国汽车制造业的差距至与美国汽车制造业的差距至少相差少相差10倍倍 1982: 人均生产人均生产54.6辆车辆车32年之后的年之后的1982美国与日本的汽车产业美国与日本的汽车产业价值流图分析 VSM精益生产的精益生产的“流流”管理管理价值流图分析 VSM 因问题主要来自配料线上料达不到产量需求,应用价值流图对因问题主要来自配料线上料达不到产量需求,应用价值流图对265原料场存原料场存取供流程进行系统梳理,如图取供流程进行系统梳理,如图1。图1 265原料场存取供价值流分析现状
60、诊断现状诊断价值流图分析 VSM 应用价值流图梳理发现了配料上料流程中存在的浪费,对其进行评价,列应用价值流图梳理发现了配料上料流程中存在的浪费,对其进行评价,列表如表表如表1。序号浪费项目浪费描述评价影响分值%备注1皮带空转因皮带运转、换取料上料情况等生产实时信息缺失,需电话联系,每次换堆皮带空转时间约6min,即每班换堆耽误时间达144min(2.4h)352换堆操作次数多每班换堆次数约24次。当货位定置不合理时,换堆操作影响时间与皮带空转时间基本重合303HY2矿槽换仓时间长每次换仓时间约6min,即每班换堆耽误时间达144min(2.4h),与皮带空转时间基本重合154库存量大,料种多造成一次料场货位
温馨提示
- 1. 本站所有资源如无特殊说明,都需要本地电脑安装OFFICE2007和PDF阅读器。图纸软件为CAD,CAXA,PROE,UG,SolidWorks等.压缩文件请下载最新的WinRAR软件解压。
- 2. 本站的文档不包含任何第三方提供的附件图纸等,如果需要附件,请联系上传者。文件的所有权益归上传用户所有。
- 3. 本站RAR压缩包中若带图纸,网页内容里面会有图纸预览,若没有图纸预览就没有图纸。
- 4. 未经权益所有人同意不得将文件中的内容挪作商业或盈利用途。
- 5. 人人文库网仅提供信息存储空间,仅对用户上传内容的表现方式做保护处理,对用户上传分享的文档内容本身不做任何修改或编辑,并不能对任何下载内容负责。
- 6. 下载文件中如有侵权或不适当内容,请与我们联系,我们立即纠正。
- 7. 本站不保证下载资源的准确性、安全性和完整性, 同时也不承担用户因使用这些下载资源对自己和他人造成任何形式的伤害或损失。
最新文档
- 四川省乐山市重点中学2025年高考化学三模试卷含解析
- 湖南名师联盟2025年高三第二次模拟考试化学试卷含解析
- 幼儿教育实训大厅
- 关注安全珍惜生命
- 河北省张家口市尚义县第一中学2025届高三考前热身化学试卷含解析
- 学前教育专业绘本故事的重要性与应用
- 福建省泉州市20023年第29届WMO竞赛四年级数学下学期竞赛试卷
- 2024-2025学年河南省创新发展联盟3月天一大联考高一下学期阶段性测试(三)数学试卷(含答案)
- 2025届安徽省黄山市屯溪第二中学高三3月份第一次模拟考试化学试卷含解析
- 成人肺部感染的监测与护理
- 涡街流量计选型参数表
- 实习证明模板(红头文件)
- 隐患排查奖励制度
- 广东佛山生育保险待遇申请表
- 电子课件《英语(第一册)(第三版)》A013820英语第一册第三版Unit5
- IPQC制程检验作业流程
- 《航空气象》课件1.4 空气的垂直运动
- XX小学体育期末考试方案
- 高铁站智能化设计方案
- 35KV集电线路铁塔组立专项方案
- 板的配筋面积表
评论
0/150
提交评论