

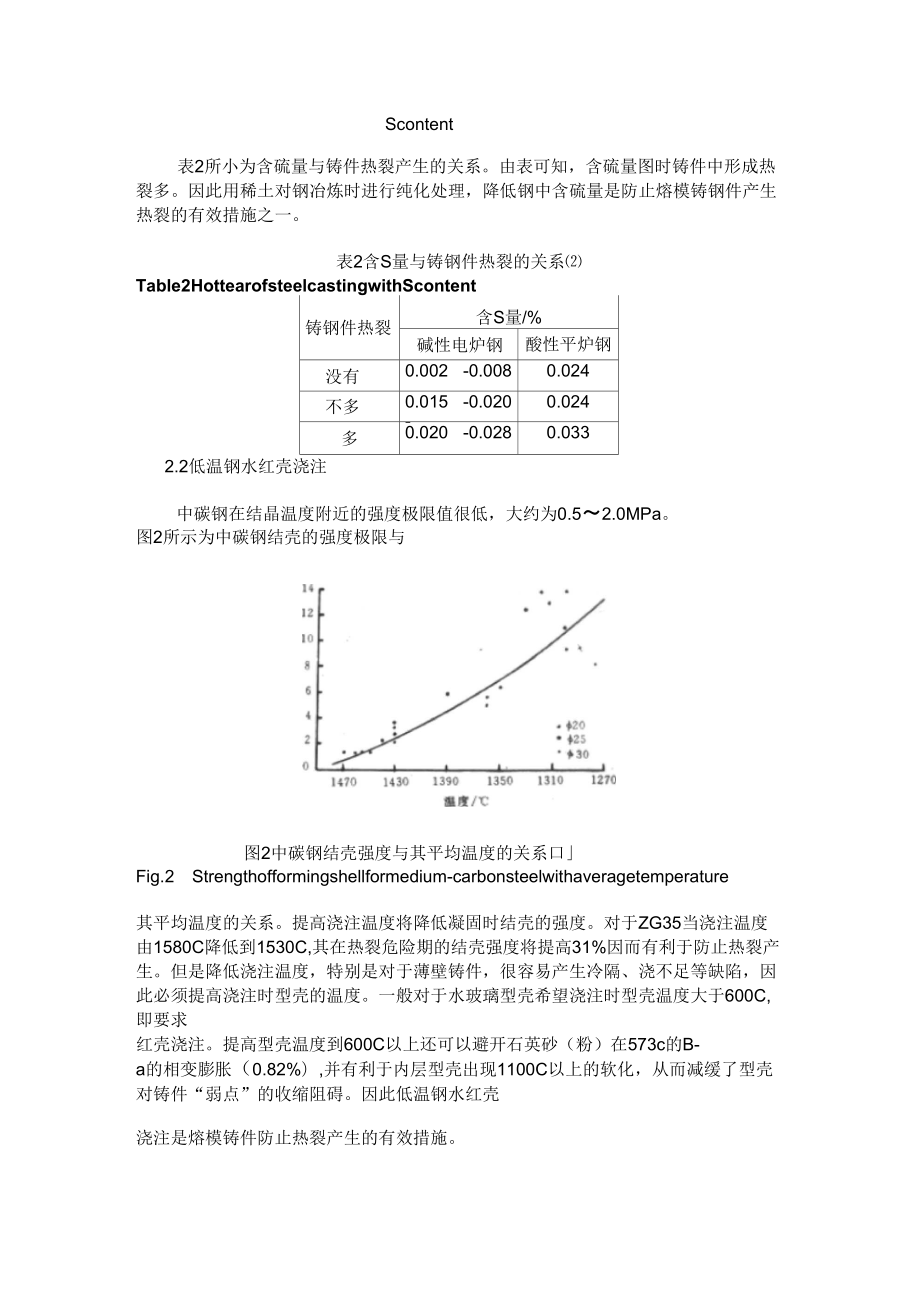


版权说明:本文档由用户提供并上传,收益归属内容提供方,若内容存在侵权,请进行举报或认领
文档简介
1、铸钢件热裂的产生和防止摘要分析了熔模铸钢件热裂产生的原因和过程,论述了防止热裂的工艺措施,并介绍了自割内浇口转移热裂及其设计方法。关键词:熔模铸造铸钢热裂热裂是熔模铸钢件常见的缺陷之一。随着熔模铸造的发展,复杂件、薄壁件越来越多,型壳的强度也得到了很大提高,熔模铸钢件中热裂缺陷的比例也随之上升。如何防止热裂成了熔模铸造技术工作人员关心和棘手的问题。1热裂产生的原因当铸件某个部位的应力达到或超过其材质的强度极限时,铸件该部位将会产生裂纹。铸件的裂纹分为热裂和冷裂两类。如果裂纹是在凝固过程中形成,则此裂纹称为热裂。热裂的裂口断面呈氧化色,裂口粗糙,其微观组织为晶间断裂。如果裂纹是在铸件完全凝固后形
2、成的,则此裂纹称为冷裂。铸件在凝固时会产生较大的收缩,当此收缩受铸型的阻碍或受铸件其余部分的牵制,则会产生应力。而铸件材质在凝固阶段的强度极限极低,因此应力很可能达到或超过其强度极限而使铸件局部产生裂纹。如果裂纹是在凝固前期形成,而此时仍存在着较大比例的液相且具有良好的流动充填性,则裂纹被液相焊合。但当裂纹在凝固后期形成(一股指周相率0.7),此时固相骨架已经比较致密,所残余的液相难以充填弥合裂纹,则裂纹将会进一步发展并残留下来,热裂形成点大致在固相线附近。热裂往往产生在铸件“弱点”部位,所谓“弱点”即铸件凝固过程中结壳最薄部位。这些“弱点”通常是铸件壁连接的内角或浇注系统引入部位等一些局部过
3、热部位。热裂的产生过程大致如下:铸件凝固初期,在其平面和圆柱表面部位以及外圆角部位凝固结壳而具有了一定强度和刚度。之后在内圆角部位也凝固结壳而具有一定强度和刚度。同时结壳因凝固冷却而产生收缩,此时结壳将受到与其相连的铸型型壁的阻碍而产生应力,特别是铸件的突起部位。随着凝固的进行,结壳增厚,浇注金属的比强度增大,结壳的总强度也增大。但是由于铸型型壳受热产生膨胀、烧结而使铸件的收缩受阻增大,引起了凝固结壳中应力增大。当铸件凝固结壳的“弱点”部位处的应力达到了浇注金属的强度极限,则在“弱点”部位产生裂纹,此裂纹穿透了“弱点”部位结壳的整个厚度。在此裂纹形成的同时,应力将相应缓解。随着凝固的继续进行,
4、在断裂点形成了新的凝固结壳,应力又将重新产生和增大,且集中在原断裂点的相对部位。当此“弱点”部位的应力再次达到浇注金属材料的强度极限时,则会再次断裂。如此裂纹继续发展直到贯穿铸件“弱点”部位整个截面。但是如果型壳表面层过热超过11001200C以后产生软化,则能激烈降低收缩应力,裂纹的发展也会中止。提高模壳退让性!2热裂的防止由上可知,热裂的产生部位是在铸件的“弱点”上,止匕“弱点”可以是铸件结构不合理引起的,例如铸件壁的连接结构不合理,内圆角半径过小等。也可以是铸造工艺不合理引起的,例如浇注系统设计不合理,导致局部过热而形成“弱点”。本文主要是从铸造工艺角度来分析探讨如何防止熔模铸钢件的热裂
5、缺陷。2.1选择热裂敏感小的铸造合金,严格控制有害元素S的含量不同铸造合金,对热裂的敏感性也不同。凡是凝固过程中收缩系数较小,凝固时形成的固相的强度较高的合金,其热裂敏感性较小。因此凡有利于提高固相线附近结壳高温强度和降低结壳收缩率的因素都有利于减缓热裂的产生。表1所示为某些合金钢在固相线以上3040c时的高温强度。ZG20虽然其凝固时的高温强度较高,但由于其凝表1合金钢在固相线以上3040c时的高温强度L1JTable1Hightemperaturestrengthofalloysteeloversolidus3040C钢的牌号Mn131Cr13T10ZG555ZG3530CrNiM(,工业
6、纯铁ZG201Cr18Ni9Ti高温强度/MPa0.30.40.50.71.21.21.42.12.5周时会发生6一丫的相变而产生大的线收缩,因此该合金仍然具有较大的热裂敏感性而较容易产生热裂。硫是钢中有害元素。图1所示为不同浇注温度时硫对钢高温强度的影响。钢在凝固时,由于硫的存在,在晶界处出现FeS和Fe的低熔点共品,而使钢在高温时的强度降低。因此含硫高的钢,其热裂敏感性大。图1含硫量对钢在结晶温度附近的强度影响Fig.1 StrengthofsteelnearbycrystallizationtemperaturewithScontent表2所小为含硫量与铸件热裂产生的关系。由表可知,含硫
7、量图时铸件中形成热裂多。因此用稀土对钢冶炼时进行纯化处理,降低钢中含硫量是防止熔模铸钢件产生热裂的有效措施之一。表2含S量与铸钢件热裂的关系Table2HottearofsteelcastingwithScontent铸钢件热裂含S量/%碱性电炉钢酸性平炉钢没有0.002.-0.0080.024不多0.015-0.0200.024多0.020.-0.0280.0332.2低温钢水红壳浇注中碳钢在结晶温度附近的强度极限值很低,大约为0.52.0MPa。图2所示为中碳钢结壳的强度极限与图2中碳钢结壳强度与其平均温度的关系口Fig.2 Strengthofformingshellformedium-
8、carbonsteelwithaveragetemperature其平均温度的关系。提高浇注温度将降低凝固时结壳的强度。对于ZG35当浇注温度由1580C降低到1530C,其在热裂危险期的结壳强度将提高31%因而有利于防止热裂产生。但是降低浇注温度,特别是对于薄壁铸件,很容易产生冷隔、浇不足等缺陷,因此必须提高浇注时型壳的温度。一般对于水玻璃型壳希望浇注时型壳温度大于600C,即要求红壳浇注。提高型壳温度到600C以上还可以避开石英砂(粉)在573c的B-a的相变膨胀(0.82%),并有利于内层型壳出现1100C以上的软化,从而减缓了型壳对铸件“弱点”的收缩阻碍。因此低温钢水红壳浇注是熔模铸件
9、防止热裂产生的有效措施。2.3薄壁铸件采用扁宽浇口,浇口的模数大于铸件的模数随着熔模铸造的发展,熔模铸造薄壁铸钢件的品种、数量呈增长趋势。由于熔模铸钢件浇注系统设计长期以来采用以补缩为主的原则,薄壁铸钢件的内浇口厚度习惯上不小于薄壁件的壁厚,加上浇注温度较高,导致铸件浇注系统引入处局部过热而成为“弱点”。这些局部过热的“弱点”凝固收缩时,其四周的铸件薄壁本体已经凝固,因此过热的“弱点”的收缩受到铸件薄壁本体的牵制,收缩受阻,因而往往在铸件的内浇口附近出现热裂。避免这类热裂的方法就是将内浇口改为扁宽内浇口。内浇口厚度一般可取铸件壁厚的1/2。为了不降低浇注速度,避免局部过热,增强模组的装配强度,
10、内浇口宽度比正常值增大12倍。扁宽内浇口有利于缓和浇注系统引入部位过热而防止热裂产生。图3所示为板手铸件的浇注系统设计方案。图3a为改进前的方案,该铸件在内浇口附近出现热裂。图3b将内浇口厚度减薄一半,宽度增宽一倍,热裂基本消除。图3板手精铸件浇注系统方案示意图Fig.3Schemeofthegatingsystemfortheinvestmentcastingofspanner2.4浇注金属应尽量均匀充填型腔,避免因浇注金属冲击型腔固定点后分流而形成“热点”浇注金属进入型腔的流向、速度受内浇口的设置位置、大小、形状的限制。不合理地设计内浇口的设置点、大小、形状可以导致浇注金属冲击型壳某个部位
11、,然后分流,使受冲击部位局部过热而成为“热点”,此“热点”也即是容易产生热裂的“弱点”。图4所示拐臂精铸件由某厂携压型来我厂进行生产,原浇注系统设计如图所示有两个内浇口A和B,浇注金属液从B内浇口进入型腔后冲击型腔K处然后分流,使K处过热,导致铸件相应该处成为“弱点”而产生热裂。我们去掉了B内浇口,并适当增大内浇口A的长度后,此热裂随即消除图4拐臂精铸件原内浇口方案及液流示意简图Fig.4Schemeoftheformergateandliquid-flowfortheinvestmentcastingofcorner-arm2.5浇注系统设计应尽量避免框形结构熔模铸造技术人员对具有两个热节的
12、精铸件或长精铸件往往设计两个内浇口,于是使得铸件-内浇口-直浇道成为一个框形结构系统,这类结构最容易出现收缩受阻,而很容易在内浇口附近产生热裂,也容易产生变形,因此应尽量避免框形结构。图5a所示为这类铸件-内浇口-直浇道系统框形结构示意图。铸件A和B处局部厚大形成两个热节,为了保证A和B热节的补缩,在A和B部位设置两个内浇口,内浇口附近过热而成为“弱点”,其收缩受铸件本身以及c处型壳的阻碍,“弱点”部位很容易产生热裂。如将浇注系统改为图5b所示楔条形结构,则浇注金属从整个楔条进入型腔,而不是从两个热节部位集中进入,因而降低了原内浇口附近的过热程度,同时楔条增大了铸件散热面积,提高了凝固结壳强度
13、,c处型壳的阻碍收缩也得以缓和,因此减缓了热裂的产生。如果再采用低温钢水红壳浇注,基本上可避免这类铸件的热裂产生。图5铸件-内浇口-直浇道系统框形结构示意图Fig.5Schemeofframestructureforthecasting-gate-spruesystem设置防裂工艺肋如果用户允许铸件结构改进,可以在易产生热裂的部位设置防裂工艺肋。防裂工艺肋不仅可以提高铸件热裂部位的强度,更主要是可起散热片作用,改善散热条件,也可使浇注金属合理分流,从而减缓“热点”集中程度,缓解热裂的产生。因此防裂工艺肋不宜厚,一般为相应部位壁厚的1/3左右,但为保证浇足,厚度应大于2mm图6所示为防裂工艺肋设
14、置举例。如果用户不同意改变铸件结构,可以在铸件退火消除应力后去除工艺肋。图6防裂工艺肋设置举例Fig.6Exempleoftechnicalribforpreventinghottear热裂的转移一一自割浇口的应用设计浇注系统时可以采用控制浇注系统各组元凝固速度的方法,让热裂转移到内浇口或工艺肋上。图7所示为热裂往内浇口上转移的设计实例。这类浇注系统称为自割浇口。自割浇口还能减少浇口切割工作量,特别是对于大型精铸铸钢件能大大减轻铸件清理、切割工作量,很有推广价值。图7自割浇口的设计结构示意图Fig.7Schemeofstructurefortheself-cut-gate图7所示为自割浇口的设
15、计结构示意。图中内浇口处设置了过热套4o过热套采用导热性差的耐火材料混合成水玻璃砂经硬化制成。制作蜡模时将过热套嵌在压型中,使过热套与蜡模成为一个整体,经制壳、脱蜡、焙烧后,过热套成为型壳的一部分。过热套的传热系数与型壳的传热系数之比应小于0.8。浇注后由于过热套导热性差、散热慢,而使内浇口的该部位成为“弱点”形成热裂而断裂。断裂后框形结构破坏,应力消失,起到热裂转移的目的。同时由于浇口自行断裂从而减少铸件清理、切割工作量。自割浇口的设计主要是计算A,l。其中A为过热套的厚度,要求A>Mg式中M内浇口白热模数,mn±i热套白长度l可用下列公式计算I*告u3fL+2此式中l过热套
16、长,mmL内浇口长,mmA,K钢在固相线附近的热裂敏感性系数,对于碳钢,分别取21.65MPa和6.9MPa(T0型壳阻力系数,Xt于水玻璃型壳取0.05MPah横浇道图,mmm横浇道长,mms横浇道截面积,mn2当将上述值代入后,得£鼻2L65-0Q5hm/s十2M(3)3结论(1)热裂是由于在凝固过程中铸件的“弱点”(局部过热部位)收缩受阻,在应力达到其凝固结壳的高温极限强度时产生。(2)选择热裂敏感性小的铸造合金;采用低温钢水红壳浇注;薄壁铸件设计扁宽内浇口;避免浇注金属液冲击型腔固定部位而成为“热点”;尽量不采用框形结构浇注系统;设置防裂工艺肋等工艺措施,能有效防止熔模铸钢件的热裂产生。(3)自割浇口不仅可以转移热裂产生部位而避免铸件内形成热裂,而且可以大大减轻铸件清理、切割的工作量。具体方法:降低浇注温度;合理设计浇注系统,尽量使用一个交口同时补缩几个热节(高温出炉,低温浇注,保证红壳);增加模壳退让性;铸件上增加防裂肋;
温馨提示
- 1. 本站所有资源如无特殊说明,都需要本地电脑安装OFFICE2007和PDF阅读器。图纸软件为CAD,CAXA,PROE,UG,SolidWorks等.压缩文件请下载最新的WinRAR软件解压。
- 2. 本站的文档不包含任何第三方提供的附件图纸等,如果需要附件,请联系上传者。文件的所有权益归上传用户所有。
- 3. 本站RAR压缩包中若带图纸,网页内容里面会有图纸预览,若没有图纸预览就没有图纸。
- 4. 未经权益所有人同意不得将文件中的内容挪作商业或盈利用途。
- 5. 人人文库网仅提供信息存储空间,仅对用户上传内容的表现方式做保护处理,对用户上传分享的文档内容本身不做任何修改或编辑,并不能对任何下载内容负责。
- 6. 下载文件中如有侵权或不适当内容,请与我们联系,我们立即纠正。
- 7. 本站不保证下载资源的准确性、安全性和完整性, 同时也不承担用户因使用这些下载资源对自己和他人造成任何形式的伤害或损失。
最新文档
- 【正版授权】 IEC 60884-2-7:2025 EXV-RLV EN Plugs and socket-outlets for household and similar purposes - Part 2-7: Particular requirements for cord extension sets
- 【正版授权】 IEC 60287-1-2:1993 EN-D Electric cables - Calculation of the current rating - Part 1: Current rating equations (100 % load factor) and calculations of losses - Section 2: Sh
- 【正版授权】 IEC 60071-1:2006 FR-D Insulation co-ordination - Part 1: Definitions,principles and rules
- 压力性尿失禁循证护理
- 2025年物业圣诞节活动策划方案
- 高二班主任2025年下学期工作方案
- 新人教版部编本2025年秋五班级上册语文教学工作方案附教学进度支配
- 2025年员工年度工作方案
- 绩效考核工具适用场景
- 003理论分布与抽样分布28
- 小学科学实验教学与现代教育技术融合研究
- 热镀锌钢管栅栏施工方案
- 2025年兴业银行股份有限公司招聘笔试参考题库含答案解析
- 2025中国电信湖北黄冈分公司招聘30人高频重点提升(共500题)附带答案详解
- 2025陕煤研究院西安分公司公开招聘高频重点提升(共500题)附带答案详解
- 2025年沈阳铁路局集团招聘笔试参考题库含答案解析
- 2025届华能安阳热电限责任公司毕业生招聘高频重点提升(共500题)附带答案详解
- 2025中考数学复习专题:八类最值问题汇-总(瓜豆隐圆胡不归阿氏圆将军饮马逆等线费马点构造二次函数求最值)(原卷版)
- 外研版(2025新版)七年级下册英语Unit 2 学情调研测试卷(含答案)
- 完整版医院CT机房装饰改造工程施工组织设计方案
- gis在城乡规划中的应用
评论
0/150
提交评论