


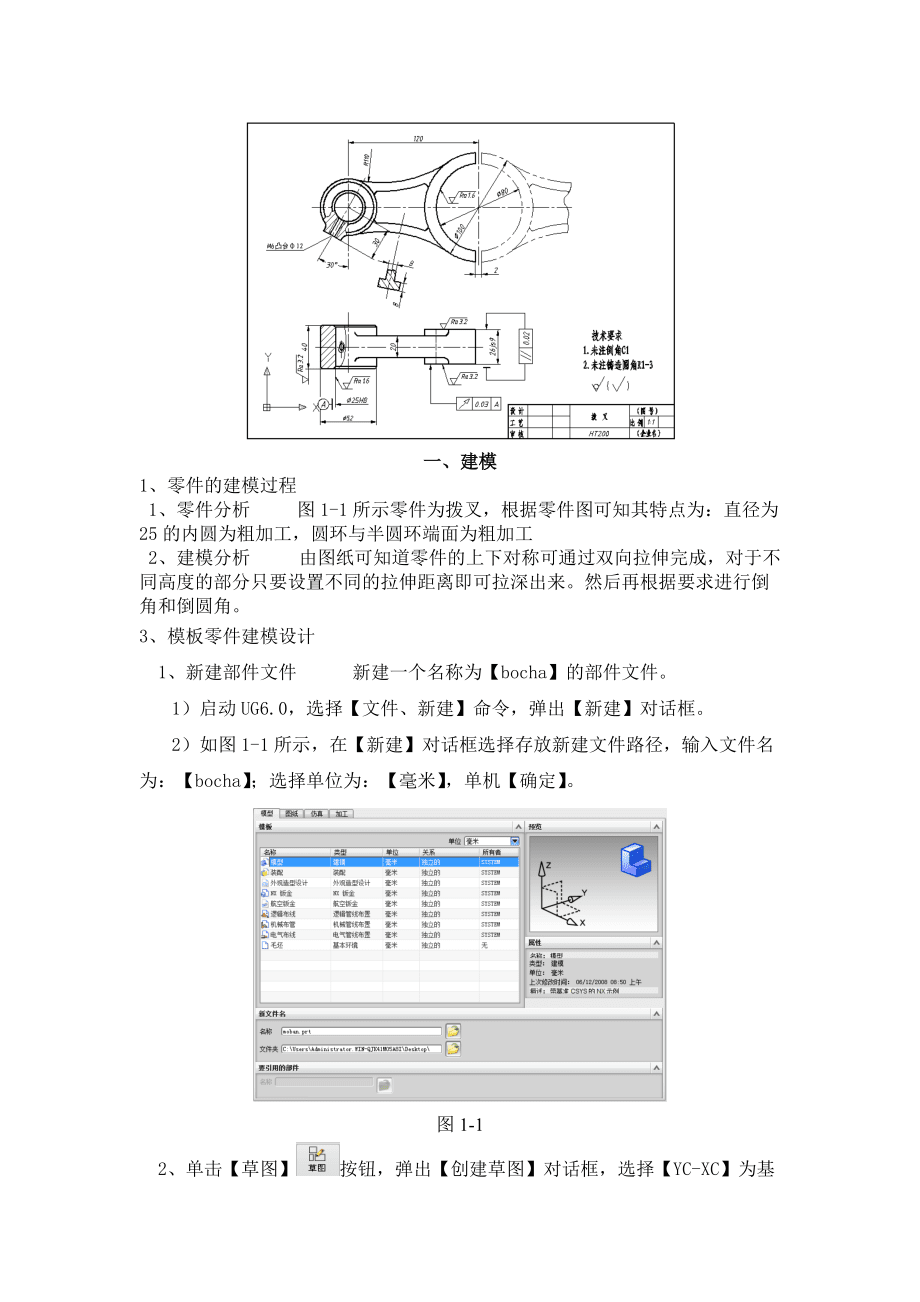

版权说明:本文档由用户提供并上传,收益归属内容提供方,若内容存在侵权,请进行举报或认领
文档简介
1、学号: 201125050117中 州 大 学CAD/CAM课程设计说明书设计题目: 拨叉成型加工专 业: 机械制造与自动化设 计 者:马振杨班 级:11机制一班 指导教师:孟雅俊 评定成绩:设计日期:2013 年 9 月 27 日至 2013 年 11 月 2 日目录前言 1计任务书.21、 建模.31 零件的建模过程.32 毛坯的建模过程.15二、零件工艺分析.17三、创建操作 .174、 设计心得与体会.39五、参考资料.39前言 模板应用广泛,是非常重要的机械零件之一。模板的一般作用是:(a)起定位作用;(b)防尘和密封,除本身可以防尘密封外,也常和密封件配合以达到密封的作用;(c)位
2、于车床电动机的顶端,主要起减震的作用,使主轴箱的转动平稳。 因此,该零件应具有足够的强度、刚度、耐磨性和韧性,以适应端盖的工作条件。该零件的主要工作表面为上表面,在设计工艺规程时必须重点考虑。端盖的加工工艺的可行性与合理性直接影响零件的质量、生产成本、使用性能和寿命等。设计任务书1、总体介绍:设计包括CAD与CAM两大模块,重点在于CAM。2、具体要求:根据平面图建模,并对该零件上所有能够铣、钻的表面进行加工。完成指定题目的设计后,要求每人编写说明书一份(包括封面、目录、设计任务书、正文、设计心得与体会、参考资料等七部分,可以打印,请上交前自己检查是否缺项)。同时上交电子稿与相应prt文件。正
3、文应包括:零件的建模过程、毛坯的建模过程、零件工艺分析与编制的工艺过程、具体加工过程(每个操作的创建详细过程,要求说明各个参数是如何配置的、每个操作生成的刀轨)、车间工艺文档4、设计要求:设计包括CAD与CAM两大模块,根据平面图建模,并对该零件上所有能够铣,钻的表面进行加工5、 零件图零件的外形图如图0-1所示:一、建模1、零件的建模过程 1、零件分析 图1-1所示零件为拨叉,根据零件图可知其特点为:直径为25的内圆为粗加工,圆环与半圆环端面为粗加工 2、建模分析 由图纸可知道零件的上下对称可通过双向拉伸完成,对于不同高度的部分只要设置不同的拉伸距离即可拉深出来。然后再根据要求进行倒角和倒圆
4、角。3、模板零件建模设计 1、新建部件文件 新建一个名称为【bocha】的部件文件。1)启动UG6.0,选择【文件、新建】命令,弹出【新建】对话框。2)如图1-1所示,在【新建】对话框选择存放新建文件路径,输入文件名为:【bocha】;选择单位为:【毫米】,单机【确定】。图1-1 2、单击【草图】按钮,弹出【创建草图】对话框,选择【YC-XC】为基准平面,绘制草图如图1-2所示。图1-24、选择【拉伸】按钮,弹出【拉伸参数设置】对话框,使用单条曲线选择图1-2草图中间,在【开始距离】文本框中输入【-4mm】,在【终点距离】文本框内输入【4mm】;单击【应用】按钮,完成拉伸如图1-3所示。图1-
5、35完成拉伸操作后如图1-4图1-46、 然后选择图1-2中上下两部分,在【开始距离】文本框中输入【-10mm】,在【终点距离】文本框内输入【10mm】;单击【应用】按钮,完成拉伸如图1-5所示。图1-57、 拉伸后如图1-6所示图1-68、 选择图1-2中左右两部分,在【开始距离】文本框中输入【-20mm】,在【终点距离】文本框内输入【20mm】;单击【应用】按钮,完成拉伸如图1-7所示。图1-79、 拉伸后如图1-8所示图1-810、选择【求和】,选中拉伸后的所有实体图单机应用,操作如图1-9所示图1-911、 求和后如图1-10所示图1-1012、 选择【基准平面】按钮,以XC-ZC平面
6、来创建基准平面,【距离】文本框中输入【0 mm】,单机【应用】。如图1-11所示图1-1113、 然后将类型改为【成一角度】,平面对象选择图1-11中创建的平面,线性对象选择Z轴,【角度】文本框中输入【30】,单机【应用】,如图1-12所示图1-1214、 将类型改为【按某一距离】,平面对象选择图1-12中创建的平面,【距离】文本框中输入【-30】,单机【应用】,如图1-13所示图1-1315、 基准平面建好后如图1-14所示图1-1416、 单击【草图】按钮,选择图1-14中建好的基准平面,如图1-15图1-1517、 在所建平面上绘制直径为12的圆,完成后的草图如图1-16所示图1-161
7、8、 选择【拉伸】按钮,弹出【拉伸参数设置】对话框,使用单条曲线选择图1-16中的草图,将【结束】文本框中的字改为【直至选定对象】布尔类型改为【求和】;如图1-17所示图1-1719、 拉伸后的实体如图1-18所示图1-1820、 单击【草图】按钮,选择图1-14中建好的基准平面,单机【确定】,如图1-19所示图1-1921、 在草图上绘制直径为6的圆,完成后的草图如图1-20所示图1-2022、 选择【孔】按钮,将孔类型改为【螺纹孔】,指定点时选择图1-20中绘制的圆心,螺纹尺寸【size】对话框中选择M6 x 1.0,螺纹深度改为25,孔深改为25,尺寸【尖角】对话框中输入120,【布尔】
8、类型选择求差,选择整个实体,其它值为默认,如图1-21所示图1-2123、 完成操作后如图1-22所示图1-2224、 给螺纹孔上螺纹,依次选择插入、设计特征、螺纹,选择详细,其操作如图1-23所示1、 2、 3、 图1-2325、 完成操作后如图1-24所示26、选择按钮,边选择四个圆,距离为1,如图1-25所示图1-2527、完成操作后如图1-26所示图1-2628、 选择按钮,选择有螺纹孔凸台的相贯线,边导员半径为1mm,如图1-27所示图1-2729、单机应用完成操作如图1-28所示图1-2830、 选择按钮,边倒圆半径为3,其操作如图1-29所示图1-2931、 单机应用完成操作后如
9、图1-30所示图1-3032、至此,完成了整个拨叉模型的创建。单击【保存】按钮,将文件【bocha.prt】另存一份以备后续使用。2、毛坯的建模过程 1)使用已建好的实体进行加工,选择部件导航器中的【草图】双击,将草图中的小圆删除,删除后的草图如图1-31所示图1-31 2)选择部件导航器中的【拉伸(4)】双击,修改拉伸参数,其操作如图1-32所示图1-32 3)拉伸后的实体如图1-33所示图1-33 4)删除部件导航器中的【倒斜角】操作,然后选择按钮,选择左侧圆柱的棱角,边倒圆半径为1,其操作如图1-34所示图1-34 5)操作后如图1-35所示图1-35至此,完成整个拨叉毛坯的创建。单击【
10、保存】按钮,将文件【bochamaopi.prt】单独保存一份以备后续使用。二、零件工艺分析确定装夹方式 由于毛坯的形状不规则、且需加工上下两个表面,根据零件形状可确定需分两次装夹。第一次装夹加工上表面及孔;第一次装夹采用两边共同装夹的装夹方式。第二次装夹加工整个毛坯的下表面,第二次装夹采用与第一次一样的装夹方式。确定加工坐标系原点 为了便于加工时对刀,第一次装夹,加工坐标系原点设置在零件顶面的中心;第二次装夹,加工坐标系原点设置在零件底面的中心。确定工步 第一次装夹:分析图可得,由于有粗糙度的限制,可用10的平底铣刀对上表面进行粗加工。用麻花钻和铰刀对25的两个通孔进行加工,用锪刀对27进行
11、加工,为了保证加工精度,用4的中心钻打定位孔。具体工步安排见表3-1。表2-1序号加工工步加工方式刀具加工余量主轴速度进给速度1模板左上表面及右上表面粗加工CAVITY_MILL10平底刀01000rpm350mmpm24的定位孔加工SPOT_DRILLING4中心钻01200rpm60mmpm324.8的扩孔加工DRILLING24.8麻花钻0550rpm40mmpm425的铰孔加工REAMING25机用铰刀0300rpm30mmpm5倒角1×45°的加工DRILLING27锪刀0200rpm350mmpm第二次装夹:分析图可得,仍可用10的平底铣刀对模板下表面加工,具体
12、工步安排见表3-2。 表2-2序号加工工步加工方式刀具加工余量主轴速度进给速度1模板下表面加工CAVITY_MILL10平底刀01000rpm350mmpm2倒角1×45°的加工DRILLING27锪刀0200rpm350mmpm三、创建操作打开零件建模过程中创建的部件【bochamaopi】。进入加工模组设置初始化1.进入加工模块 单击【开始】按钮,选择【加工】命令,进入自动加工模块,弹出【加工环境】对话框,在【加工环境】对话框的【要创建的设置】列表框中选择模板文件【mill_contour】(型腔铣)。如图3-1所示。单击【确定】按钮,进入加工环境。图3-13、创建刀具
13、 1)创建第一把刀具:平底刀。单击【加工创建】工具栏中的【创建刀具】按钮,弹出【创建刀具】对话框,在【创建刀具】对话框中,选择类型为:【mill_contour】;选择子类型为:铣刀;输入名称为:【D10】;如图3-2所示,单击【确定】按钮,弹出【铣刀-5参数】对话框,在【铣刀-5参数】对话框中设置刀具直径为:【10】;刀具补偿:【1】;长度补偿:【0】刀具号:【1】;如图3-3所示。设置完参数后,单击【确定】按钮,完成第一把刀具的创建。图3-2 图3-32)创建第二把刀具:中心钻。单击【加工创建】工具栏中的【创建刀具】按钮,弹出【创建刀具】对话框。在【创建刀具】对话框中,选择类型为:【dri
14、ll】;选择子类型为:中心钻;输入名称为:【D4】如图3-4所示,单击【确定】按钮,弹出【钻刀】对话框。在【钻刀】对话框中设置刀具直径为:【4】;刀具号:【】;长度补偿:【0】;如图3-5所示。单击【确定】按钮,完成第二把刀具的创建。 图3-4 图3-52) 按照同样方法,分别创建好3、4、5把刀具,名称和参数见下表4-1所示。表3-1 创建刀具参数表刀号子类型图标名称类型刀具直径/mm有效长度/mm1D10平刀10752D4中心钻4503D24.8麻花钻24.8504D25铰刀24755D27平底锪钻27505)刀具创建如图3-6所示图3-64、设置几何视图参数1) 单击【操作导航器】工具栏
15、中的【几何视图】图标,切换操作导航器至几何视图。2) 定义加工坐标系:双击几何视图中的【_】节点,弹出【ill rient】对话框,如图3-7所示。在该对话框中选择的【构造器】按钮,弹出【】对话框,如图3-8所示。 图3-7 图3-83) 设置安全平面:在【ill rient】对话框中的【间隙】复按选框中设置安全设置选项为:【平面】,单击按钮,进入【平面构造器】对话框,在绘图区选择模板上表面作为参考对象,然后在【偏置】文本框中输入偏置值为:【20】,如图3-9所示。单击【确定】按钮,即在相对于毛坯的上表面上部距离为20的高度创建一个安全平面,安全平面以高亮小三角显示。图3-94)导入毛坯:选择
16、【文件导入部件】命令,弹出【导入部件】对话框,如图3-10所示,单击【确定】按钮,弹出【导入部件】对话框,选择第一章中创建的【mobanmaopi.prt】”文件,如图3-11所示。单击【】按钮,弹出【点】对话框,设置坐标相对为XC:【0】;YC:【0】;ZC:【0】;单击【确定】按钮。完成毛坯的导入。如图3-12所示。图3-10 图3-11图3-12 图 3-135)选择零件几何:在几何视图中,单击【_】节点前的【】号,再双击【WORKPIECE】节点,弹出【铣削几何体】对话框,如图3-13所示。在该对话框中选择【指定部件】图标,单击弹出【部件几何体】对话框,如图3-14所示。在绘图区选择拨
17、叉模型作为零件几何,单击【确定】按钮,完成零件几何的选择,并返回到【铣削几何体】对话框,单击【确定】按钮。 图3-146) 选择【指定毛坯】图标,单击弹出【部件几何体】对话框,如图3-15所示。在绘图区选择拨叉模型作为零件几何,单击【确定】按钮,完成零件几何的选择,并返回到【铣削几何体】对话框,单击【确定】按钮图3-154、 创建加工方式1、上平面的加工 1)、单击【插入】工具条的创建操作按钮,或在【插入】下拉菜单中单击【操作】按钮,进入【创建操作】对话框。在【类型】下拉菜单选项中选择【mill_contour】,即型腔铣操作类型,在【操作子类型】区域选择CAVITY_MILL按钮,在【刀具】
18、下拉选项中选择【D10】作为加工刀具,在【方法】下拉选项中选择【MILL_ROUGH】作为加工方法,【几何体】选择【WORKPIECE】,其他默认,完成以上操作后,单击【确定】按钮,如图4-1所示。图4-1 2)、单机隐藏按钮,选择毛坯单机确定,如图4-2所示图4-2 3)、单机型腔铣对话框中的【指定切削区域】,选择左侧圆环及右侧半圆环的上表面,单机确定,如图4-3所示,方法改为【MILL-FINISH】,切削模式改为【跟随周边】,全局每刀深度改为【1】,切削参数的余量为0如图4-4所示、进给和速度的设置如图4-5所示图4-3 图4-4 图4-5 单机生成按钮,生成刀轨如图4-6所示图4-6仿
19、真刀具轨迹)在【型腔铣】对话框中,单击【确认】图标,弹出【导轨可视化】对话框,选择【动态】选项卡。)单击【播放】按钮,系统会以实体的方式进行切削仿真,通过仿真过程查看刀具轨迹是否正确,仿真结果如图4-7所示。)仿真完成后,单击【确定】按钮,返回到【面铣削区域】对话框。)单击【确定】按钮,完成模板左上表面精加工操作的创建。图4-72、 下平面的加工 1)选择第一步已做好的操作【CAVITY_MILL】复制粘贴,双击复制好的新的操作进入型腔铣对话框,单机指定切削区域后面的按钮,单机全重选然后选择部件的两个下表面如图4-8所示图4-8 2)更改刀轴,其操作如图4-9所示图4-9单机生成按钮,生成刀轨
20、如图4-10所示图4-10仿真刀具轨迹)在【型腔铣】对话框中,单击【确认】图标,弹出【导轨可视化】对话框,选择【动态】选项卡。)单击【播放】按钮,系统会以实体的方式进行切削仿真,通过仿真过程查看刀具轨迹是否正确,仿真结果如图4-11所示。)仿真完成后,单击【确定】按钮,返回到【面铣削区域】对话框。)单击【确定】按钮,完成模板左上表面精加工操作的创建。图4-113、创建25的孔加工操作1、创建中心钻操作 1)单击【加工创建】工具栏中的【创建操作】按钮,弹出【创建操作】对话框。2)如图4-12所示,在弹出的【创建操作】 对话框中,选择类型为:【drill】;选择子类型为:中心钻;使用几何体:WOR
21、KPIECE;使用刀具:【D4】;使用方法:【DRILL_METHOD】,单击【确定】按钮,弹出如图4-13所示的【点钻】对话框。图4-12图4-132定位加工孔的位置)在【点钻】对话框中单击【指定孔】的图标,弹出【点到点几何体】对话框。在【点到点工几何体】对话框中单击【选择】按钮,然后再弹出的对话框中单击【类选择】按钮,选择如图4-14所示的圆,单击确定图4-14 2)在弹出的对话框中单击【选择结束】,返回【点到几何体】对话框,点击【优化】,具体步骤如图4-15所示。图4-15 3)在返回的【点钻】对话框中选择指定部件表面按钮,弹出如图4-16所示的【部件表面】对话框,然后选择左侧圆环的上表
22、面,单机确定图4-16 4)然后单机进给和速度对话框,弹出进给和速度对话框如图4-17所示,其参数设置如图4-17所示,单机确定图4-16 图4-177) 单机生成按钮,生成刀轨如图4-17所8)仿真刀具轨迹)在【型腔铣】对话框中,单击【确认】图标,弹出【导轨可视化】对话框,选择【动态】选项卡。)单击【播放】按钮,系统会以实体的方式进行切削仿真,通过仿真过程查看刀具轨迹是否正确,仿真结果如图4-18所示。)仿真完成后,单击【确定】按钮,返回到【面铣削区域】对话框。)单击【确定】按钮,完成模板左上表面精加工操作的创建。图4-184、创建24.8的麻花钻扩孔加工操作1)单击【加工创建】工具栏中的【
23、创建操作】图标,弹出【创建操作】对话框。2)在弹出的【创建操作】 对话框中,选择类型为:【drill】;选择子类型为:钻;使用几何体:【WORKPIECE】;使用刀具:D24.8;使用方法:DRILL_METHOD,如图4-19所示。图4-19 图4-203)单击【确定】按钮,弹出如图4-20所示的【钻】对话框。 4)在【点钻】对话框中单击【指定孔】的图标,弹出【点到点几何体】对话框。在【点到点工几何体】对话框中单击【选择】按钮,然后再弹出的对话框中单击【类选择】按钮,选择如图4-14所示的圆,单击确定 5)在返回的【点钻】对话框中选择指定部件表面按钮,弹出如图4-16所示的【部件表面】对话框
24、,然后选择左侧圆环的上表面,单机确定5) 在返回的点钻对话框中选择指定底面按钮,弹出如图4-21所示的【底面】对话框,然后选择左侧圆环的底面,单击确定图4-21 6)然后单机进给和速度对话框,弹出进给和速度对话框如图4-22所示,其参数设置如图4-22所示,单机确定 图4-22 图4-23 7)单机生成按钮,生成刀轨如图4-23所 8)仿真刀具轨迹9)在【型腔铣】对话框中,单击【确认】图标,弹出【导轨可视化】对话框,选择【动态】选项卡。10)单击【播放】按钮,系统会以实体的方式进行切削仿真,通过仿真过程查看刀具轨迹是否正确,仿真结果如图4-24所示。11)仿真完成后,单击【确定】按钮,返回到【
25、面铣削区域】对话框。12)单击【确定】按钮,完成拨叉左侧孔加工操作的创建。图4-245、创建25的铰刀加工操作1)单击【加工创建】工具栏中的【创建操作】图标,弹出【创建操作】对话框。2)在弹出的【创建操作】 对话框中,选择类型为:【drill】;选择子类型为:钻;使用几何体:【WORKPIECE】;使用刀具:D25;使用方法:DRILL_METHOD。如图4-25所示。图4-25 图4-263)单击【确定】按钮,弹出如图4-26所示的【铰】对话框。 4)在【铰】对话框中单击【指定孔】的图标,弹出【点到点几何体】对话框,单击【选择】按钮,在弹出的对话框中,单击【类选择】按钮,选择直径为25的通孔
26、,如图4-14所示,单机确定 5)在返回的点钻对话框中选择指定部件表面按钮,弹出如图4-16所示的【部件表面】对话框,然后选择左侧圆环的上表面,单机确定 5)在返回的点钻对话框中选择指定底面按钮,弹出如图4-17所示的【底面】对话框,然后选择左侧圆环的底面,单击确定 6)然后单机进给和速度对话框,弹出进给和速度对话框如图4-18所示,其参数设置如图4-18所示,单机确定 图4-18 图4-19 7)单机生成按钮,生成刀轨如图4-19所 8)仿真刀具轨迹)在【型腔铣】对话框中,单击【确认】图标,弹出【导轨可视化】对话框,选择【动态】选项卡。)单击【播放】按钮,系统会以实体的方式进行切削仿真,通过
27、仿真过程查看刀具轨迹是否正确,仿真结果如图4-20所示。)仿真完成后,单击【确定】按钮,返回到【面铣削区域】对话框。)单击【确定】按钮,完成拨叉左侧圆孔加工操作的创建。图4-206、创建普通钻孔锪操作 1)单击【加工创建】工具栏中的【创建操作】图标,弹出【创建操作】对话框。 2)在弹出的【创建操作】 对话框中,选择类型为:【drill】;选择子类型为:锪锥孔;使用几何体:【WORKPIECE】;使用刀具:【D27】;使用方法:【DRILL_METHOD】。如图4-21所示。 3)单击【确定】按钮,弹出如图4-22所示的【钻埋头孔】对话框。图4-21图4-22 4)在【钻埋头孔】对话框中单击【指
28、定孔】的图标,在弹出的对话框中单击【选择】按钮,在绘图区选择25的简单通孔,单击【确定】按钮,返回到【点到点几何体】对话框,单击【确定】按钮,完成加工孔位置的定义,返回到【钻埋头孔】对话框。 5)在返回的点钻对话框中选择指定部件表面按钮,弹出如图4-16所示的【部件表面】对话框,然后选择左侧圆环的上表面,单机确定 6)在返回的点钻对话框中选择指定底面按钮,弹出如图4-17所示的【底面】对话框,然后选择左侧圆环的底面,单击确定 7)【钻埋头孔】对话框中,默认循环类型为:【标准钻埋头孔】,单击【编辑参数】图标,弹出【指定参数组】对话框。 8)在【指定参数组】对话框中,默认循环参数组为:【1】,单击
29、【确定】按钮,弹出【cycle参数】对话框。在【cycle参数对话框】中,单击【sink直径-2.0000】按钮,弹出【sink直径】对话框,在【sink直径】对话框中,输入直径值为:【27】。单击【确定】按钮,返回到【ycle参数】对话框。在【cycle参数对话框】中,单击【入口直径-.0000】按钮,弹出【入口直径】对话框。在【sink直径】对话框中,输入直径值为:【25】,如图4-23所示,单击【确定】按钮,返回到【ycle参数】对话框。 9)单击【确定】按钮,完成循环参数的设置,返回到【钻埋头孔】对话框。图4-23 10)在【钻埋头孔】对话框,设置最小安全距离为:【10】。 11)在【
30、钻埋头孔】对话框中,单击【进给和速度】按钮,弹出【进给和速度】对话框。 12)选择【速度】选项卡,选中【主轴速度】复选框,设置主轴速度为:【500rmp】。 13)选择【进给】选项卡,设置切削速度为:【200mmpm】,其他参数保持默认值。 14)单击【确定】按钮,完成进给率的设置。返回到到【钻埋头孔】对话框。 15)在到【钻埋头孔】对话框中单击【生成】图标,即可生成定位孔加工操作的刀具轨迹,如图4-24所示。图4-249仿真刀具轨迹)在【钻埋头孔】对话框中,单击【确认】图标,弹出【可视化刀轨轨迹】对话框,选择【2动态】选项卡。)单击【播放】按钮,系统会以实体的方式进行切削仿真,通过仿真过程可查看刀具轨迹是否正确,仿真结果可见图4-25。图4-25)仿真完成以后,单击确定按钮,返回到到【钻埋头孔】对话框。)单击【确定】按钮,完成倒角加工操作的创建。7、创建普通钻孔锪操作 1)选择第一步已做好的操作【COUNTERSINKING
温馨提示
- 1. 本站所有资源如无特殊说明,都需要本地电脑安装OFFICE2007和PDF阅读器。图纸软件为CAD,CAXA,PROE,UG,SolidWorks等.压缩文件请下载最新的WinRAR软件解压。
- 2. 本站的文档不包含任何第三方提供的附件图纸等,如果需要附件,请联系上传者。文件的所有权益归上传用户所有。
- 3. 本站RAR压缩包中若带图纸,网页内容里面会有图纸预览,若没有图纸预览就没有图纸。
- 4. 未经权益所有人同意不得将文件中的内容挪作商业或盈利用途。
- 5. 人人文库网仅提供信息存储空间,仅对用户上传内容的表现方式做保护处理,对用户上传分享的文档内容本身不做任何修改或编辑,并不能对任何下载内容负责。
- 6. 下载文件中如有侵权或不适当内容,请与我们联系,我们立即纠正。
- 7. 本站不保证下载资源的准确性、安全性和完整性, 同时也不承担用户因使用这些下载资源对自己和他人造成任何形式的伤害或损失。
最新文档
- 北京师范大学-香港浸会大学联合国际学院《大学英语(1)》2023-2024学年第一学期期末试卷
- 第一课第二框土地改革与三大战役课件
- 2025年中国原子吸收光谱仪行业发展现状、市场前景、投资方向分析报告(智研咨询发布)
- 采茶厂应收账款催收责任分工制度
- 空调专卖店行业跨境出海项目商业计划书
- 新型物理治疗及康复设备行业深度调研及发展项目商业计划书
- 监理资料员职责在铁路项目中的应用
- 港口用房管理暂行办法
- 焦作公路注浆管理办法
- 煤矿班组培训管理办法
- 《护理不良事件》课件
- 无创眶周抗衰规范
- 2024年1月黑龙江高中学业水平合格考政治试卷真题(含答案详解)
- 花岗岩路面铺设工艺流程
- 钢结构厂房水电安装施工设计方案
- 国开《演讲与口才》形考任务1-4答案
- 储粮害虫与技术和化学防治
- 2021年华南理工大学软件工程专业《计算机组成原理》科目期末试卷B(有答案)
- 自适应前照灯控制系统
- 电梯招标文件示范文本
- 上海市安装工程预算定额(2000)工程量计算规则
评论
0/150
提交评论