

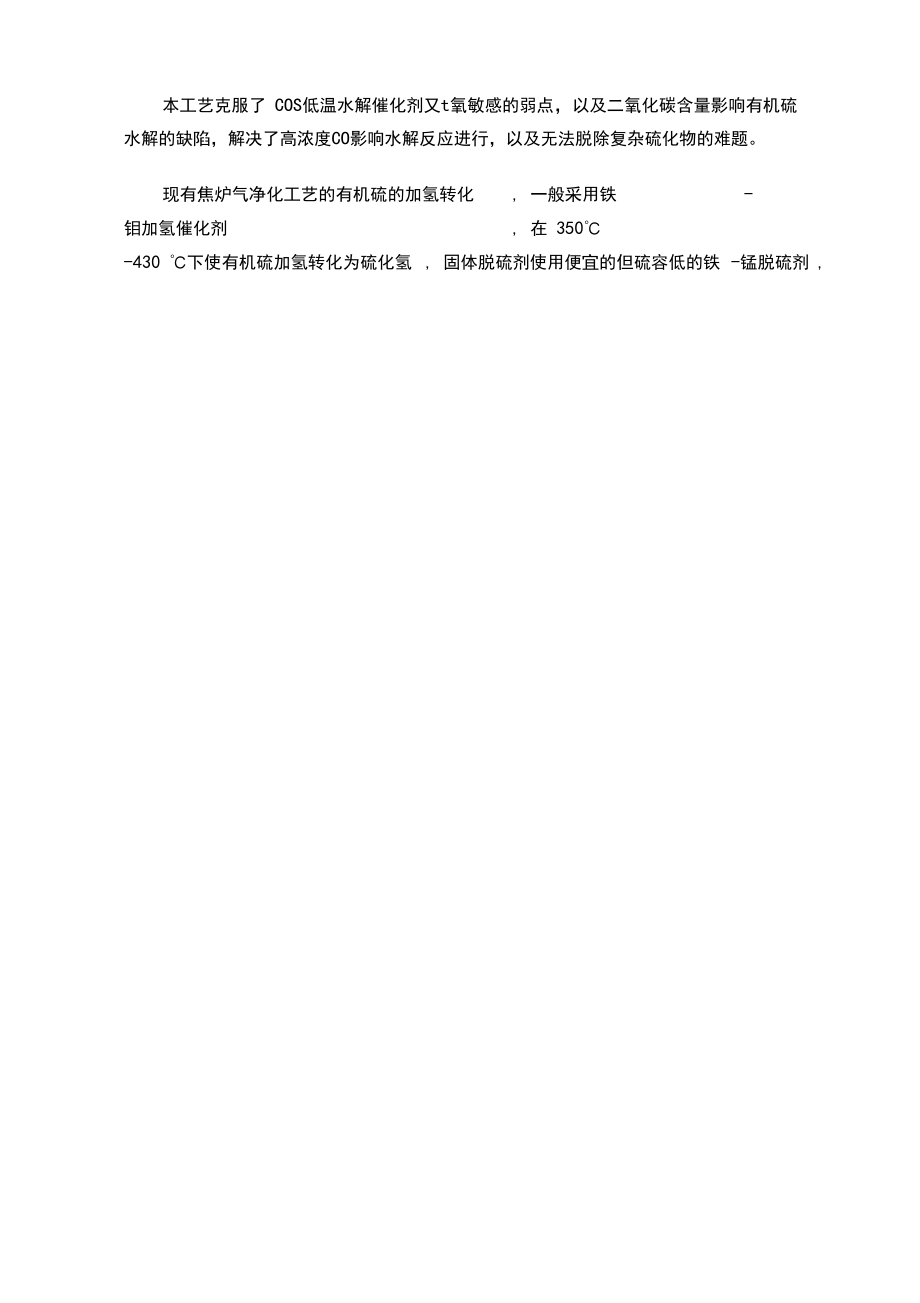


版权说明:本文档由用户提供并上传,收益归属内容提供方,若内容存在侵权,请进行举报或认领
文档简介
1、焦炉气的精制是以炼焦剩余的焦炉气为生产原料, 经化工产品回收( 焦炉气的粗制);再经压缩后(2.55MPa),进入脱硫转化工段,脱硫采用NHD湿法脱硫和干法精脱硫技 术,总硫脱至0.1 X 10-6,转化采用烧类部分氧化催化技术;制得合格的甲醇合成新鲜气 ( 又称精制气), 送去压缩工段合成气压缩机, 最后进入甲醇合成塔制得甲醇。第 1 章 焦炉气成分分析1.1 典型焦炉气的组成焦炉气的主要成分为甲烷26.49%、氢气58.48%、一氧化碳6.20%和二氧化碳2.20%等 , 还有少量的氮气、不饱和烃、氧气、焦油、萘、硫化物、氰化物、氨、苯等杂质。焦炉气基础参数: 流量62967m3/h(2
2、台焦炉生产的剩余焦炉气); 温度25 ; 压力0.105MPa(a)( 煤气柜压力)。1.2 焦炉气的回收利用焦炉气是良好的合成氨、合成甲醇及制氢的原料。根据焦炉气组成特点, 除 H2、 CO、CO2 为甲醇合成所需的有效成分外, 其余组分一部分为对甲醇合成有害的物质( 如多种形态的硫化物, 苯、萘、氨、氰化物、不饱和烃等) 。如焦炉气中的硫化物不仅会与转化催化剂的主要活性成分Ni 迅速反应, 生成 NiS 使催化剂失去活性, 而且还会与甲醇合成催化剂的主要活性组分Cu迅速反应,生成CuS,使催化剂失去活性,并且这两种失活是无法再生的。 又如 , 不饱和烃会在转化催化剂表面发生析碳反应, 堵塞
3、催化剂的有效孔隙及表面活性位 , 使催化剂活性降低。另一部分为对甲醇合成无用的物质(对甲醇合成而言为惰性组分),如CH、N等。惰性气体含量过高,不仅对甲醇合成无益,而且会增加合成气体 的功耗 , 从而降低有效成分的利用率。第 2 章 焦炉气的精制2.1 硫的脱除及加氢净化焦炉气制甲醇工艺中, 焦炉气精制的首要工作是“除毒”, 将对甲醇合成催化剂有害的物质脱除到甲醇合成催化剂所要求的精度。这是因为甲醇合成催化剂对硫化物的要求要高于转化催化剂。甲醇合成催化剂要求总硫0.1 X 10-6,转化催化剂要求总硫 0. X10-6。第二就是要减少惰性组分的含量。脱除“毒物”的方法, 根据系统选择工艺方案的
4、不同而有所差别。而降低惰性气体的组分含量主要是采用将烃类部分氧化催化转化的方法,使其转化为甲酉!合成有用的 COW H2,同时达到降低合成气中惰性组分的目的。2.1.1 无机硫的脱除焦炉气中硫质量浓度高达 6g/m3,氟化物质量浓度约为1.5g/m3。在焦炉气净化工艺中设有脱硫、脱氰、蒸苯、焦油电捕捉等一系列净化装置, 除为了减轻硫化氢和氰化物对后续装置的腐蚀, 另一方面是减轻焦炉气作燃料气时对大气的污染, 或作化工原料时,对催化剂的毒害。煤气净化装置是将焦炉气经过捕捉、冷却、分离、洗涤等多种化工操作, 脱除焦炉气中的焦油、萘、硫化氢、氰化氢、氨、苯等物质,以满足后续装置对气体质量的要求, 并
5、回收焦油、硫、氨、苯等。本系统采用NHDS法脱硫后,焦炉气中的HS质量浓度在15mg/m左右,同时可脱除 焦炉气中部分有机硫。但有机硫含量仍然很高,达95mg/m左右。如不经过精脱硫直接送 入下工段, 将使转化系统催化剂很快因硫中毒而失活, 所以必须采用精脱硫工艺对焦炉气进行处理。2.1.2 有机硫的脱除(精脱硫 )根据对国内现有焦炉气净化技术的分析和比较,考虑到COS 低温水解工艺路线存在的缺陷 , 对焦炉气的精脱硫采用高温加氢转化技术路线。这是因为焦炉气中含有的硫化物形态较为复杂, 如 : 硫醇、硫醚、噻酚等硫化物在低温水解环境下很难脱除。本系统采用铁- 钼加氢脱硫转化剂, 在高温环境下,
6、 将气体中的有机硫转化, 生成易于脱除的硫化氢, 然后再采用固体铁- 锰脱硫剂吸收转化后气体中的硫化氢。这样可使有机硫加氢转化完全, 净化度大为提高, 而且配套干法脱硫剂的硫容也高, 并且可将不饱和烯烃进行加氢饱和。氧气加氢燃烧, 达到对毒物的脱除, 满足转化甲醇合成气对气体“毒物”的净化要求。本工艺克服了 COS低温水解催化剂又t氧敏感的弱点,以及二氧化碳含量影响有机硫 水解的缺陷,解决了高浓度CO影响水解反应进行,以及无法脱除复杂硫化物的难题。现有焦炉气净化工艺的有机硫的加氢转化, 一般采用铁- 钼加氢催化剂, 在 350-430 下使有机硫加氢转化为硫化氢, 固体脱硫剂使用便宜的但硫容低
7、的铁-锰脱硫剂,最后使用价格较贵但硫容较高的氧化锌把关。2.1.3 关键技术高浓度CO CO的焦炉气加氢净化时,遇到的问题:(1)如何避免CO CO在加氢催化 剂上产生甲烷化反应。(2)如何避免CO歧化析碳和甲烷的分解析碳。(3)如何防止铁钥 催化剂床层产生的温升。2.1.4 解决方法在加氢过程的主要反应中, 含有烯烃、有机硫化物及氧的焦炉气在催化剂上进行的主要反应有:2H2+O2=2H2O+QC2H2+2H2 C2HCH+HFHCOS+H> CO+2SCOS+H> CO+H2SRSH硫醇)+H2-RH+bSRSR(硫醴)+2H2-RH+RH+HSCS+4H- 2HS+CH+QC4
8、HS(嚷酚)+4H2- C4Ho+HS可能出现的副反应有:2c8 C+C2+QCO+3H CH+H2O有机硫化物及氧的焦炉气在催化剂上进行的(1)(2)(3)(4)(5)(6)(7)(8)(9)(10)(11)(12)CH-C+2H+Q反应 (1) 、 (8) 、 (10) 为强放热反应, 可能会引起催化剂床层“飞温”。反应 (10) 所出现的歧化积碳反应产生的碳会堵塞催化剂孔道, 导致催化剂活性位减少, 因此应设法避免上述反应。另外 , 焦炉气体中的油类( 由于焦炉气压缩机气缸采用少油润滑, 可能在焦炉气中带有少量的润滑油) 、苯和焦油在加氢转化器内, 经加氢裂解、饱和, 避免了这些微量物质
9、对后续工段的不利影响。我们在工艺设置上, 采用严格的350控制 , 设有冷激副线, 及时调整加氢转化器床层温度。 通过监测床层压差变化, 及时调整床层温度以及分析槽内积碳程度, 达到抑制析碳的目的。2.2 烃类的部分氧化催化转化烂类的转化是将焦炉气中的甲烷转化成合成甲醇所用的有效气体CO和H2o为使甲醇合成气的氢碳比尽量靠近甲醇合成所需要的最佳氢碳比, 本装置焦炉气中烃类的转化选用部分氧化( 纯氧+蒸汽) 催化转化。2.2.1 部分氧化催化转化原理焦炉气部分氧化催化转化法, 是将焦炉气中的烃类( 甲烷、乙烷等) 进行部分氧化和蒸汽转化反应,在转化炉中首先发生 H、CH与Q的部分氧化燃烧反应,然
10、后气体进入催化剂层进行甲烷、乙烷等与蒸汽的转化反应, 所以这个方法也称为自热转化法。生产原理可以简单解释为甲烷、蒸汽、氧混合物的复杂的相互作用: 第一阶段为部分氧化反应,主要是氢气与氧接触发生燃烧氧化反应,生成H2O该反应是剧烈的放热反应:2H+O = 2HO+Q(13)在这个阶段, 焦炉气体中微量的氧与配入的氧完全反应, 反应后的气体中氧体积分数仅为 0.05%,不会对转化催化剂活性造成影响。第二阶段为水蒸气和二氧化碳氧化性气体在催化剂的作用下,与CH4进行蒸汽转化反应 , 该反应是吸热反应:(14)CH+HO- CO+3HQCH+COH 2CO+2HQ(15)上述两阶段的反应可合并成一个总
11、反应式:2CH+CO+O-3CO+32+H2O(16)由于第二个阶段反应是吸热反应,当转化温度越高时,甲烷转化反应就越完全,反应 后气体中的残余甲烷就越低。甲烷部分氧化通常加入一定量的蒸汽 ,目的是避免焦炉气 在受热后发生析碳的反应,使甲烷进行蒸汽转化反应,在转化反应的同时,也起到抑制炭 黑的生成。转化反应在锲催化剂作用下,反应速度加快,反应温度降低,反应平衡温距减 小到1C-5C,在960c残余CH< 0.4%。转化后的气体成分见表 2.1。COCOH2N+ArCHHO15.538.2371.863.210.450.43表2.1转化后的气体成分由表2.1可见,焦炉气催化纯氧转化制得甲醇
12、合成气中虽然氢气过剩,但其他组分比例较好,完全能够满足甲醇合成需要。2.2.2 工艺流程焦炉气中烧类部分氧化催化转化工艺流程示于图2.1 o图2.1焦炉气部分氧化催化转化工艺流程示意图2.2.3 过程特点转化催化剂的主要活性组分为Ni,对硫化物非常敏感,因此,焦炉气进入转化炉之前必须将其中大量的硫化物脱除到转化催化剂和甲醇合成催化剂对硫精度的要求。焦炉气和氧气在进入转化炉之前, 与一定比例的蒸汽混合, 为防止水蒸气冷凝, 焦炉气和氧气需在加热炉中加热, 一方面防止蒸汽冷凝, 另一方面加热后的焦炉混合气与氧气在进入转化炉后, 能迅速发生燃烧反应。为防止液状或固体颗粒进入高速运转的离心机( 合成气
13、压缩机), 损坏转子, 本装置在焦炉气压缩前, 对焦炉气进行洗涤, 利用焦炭过滤, 采用 4台往复活塞式压缩机, 提高气体压力至脱硫系统所需压力2.55MPa。焦炉气中的硫形态比较复杂,转化前采取一系列脱硫,直至总硫 0.1 X10-6。实践证明, 转化前未脱除的硫主要是噻吩, 经过铁钼加氢转化, 在高温环境下, 已经全部转化为易于脱除的H2S 和 C4H10, 此时将转化气中总硫脱除到所需精度很容易。甲醇系统驰放气主要用作转化加热炉燃料, 剩余的返回燃料气管网, 顶替部分炼焦用燃料焦炉气, 把焦炉气送回甲醇生产系统进行脱硫转化, 压缩合成。本装置设置大型加热炉, 除加热转化系统物料外, 还将
14、转化副产6.4MPa、 282次高压饱和蒸汽, 加热至480。经降温降压至3.82MPa、 450的过热蒸汽, 作为空压和合成气压缩汽轮机透平动力蒸汽。全系统蒸汽完全自给。系统副产蒸汽压力等级较多,能够适应不同需要。本装置主要副产6.4MPa饱和蒸汽 (加热后减压3.82MPa,450c过热蒸汽)。1.2MPa过热蒸汽由高压汽包直接降压获得,并 入1.2MPa管网,与来自甲醇合成的1.2MPa过热蒸汽作为甲醇精储和溶液再生的热源。0.3MPa低压蒸汽主要作除氧热源和厂区冬季采暖。冷凝液的回收利用。全系统冷凝液可回收利用, 增设一气体饱和塔, 用系统冷凝液通过加热炉加热, 进行饱和增湿。既可减少
15、系统蒸汽用量, 又合理利用了冷凝液, 省略了工艺冷凝液的排放和处理, 消除了环境的污染因素, 这是一项节能环保的技术。三废治理及环境保护与实际效果。本装置在设计中严格执行国家有关标准、地方规定 , 具有完善的“三废”及噪声治理措施。(1) 废气治理在开停车及事故工况下, 转化工段和脱硫工段排放的工艺废气( 焦炉气和合成气) 送本工程火炬系统焚烧后排放。甲醇合成系统的驰放气和膨胀气, 甲醇精馏预塔不凝气作为加热炉燃料全部消耗,不排放到空气中。NHD脱硫系统产生的含硫化氢废气,送入Cluas硫回收装置,尾气中SO浓度达标排放。(2) 废水治理甲醇装置的废水量不大, 甲醇精馏废水采用汽提预处理回收甲
16、醇, 而后送污水处理站进行生化处理。(3) 废渣治理各类废催化剂分类送催化剂制造厂回收, 不能回收的并无毒害作用的( 如 : 废锰矿石)用于铺路或填坑, 不存在废固堆放现象。因此, 本装置废渣对环境影响不大。第 3 章 关键的工艺技术和设备3.1 焦炉气湿法脱硫NHD脱硫技术主要是脱除焦炉气中的大部分无机硫(H2S)和少量有机硫(COS),并将脱硫回收的酸性气体送回硫回收。3.2 焦炉气精脱硫干法脱硫是将经过湿法脱硫的焦炉气中的有机硫, 利用铁钼触媒进行加氢反应, 转化成易于脱除的无机硫, 同时也使不饱和烃加氢饱和, 而后通过锰矿脱硫剂和氧化锌脱硫剂,将硫化氢脱除,使经过干法脱硫的焦炉气中总硫
17、 0.1 乂 10-6,达到甲醇合成触媒要求的精度。3.3 焦炉气部分氧化催化转化转化是将脱硫后焦炉气中的CH4 及其他烃类在转化炉内, 与纯氧进行部分氧化及蒸汽转化反应,生产H、CO CO等甲醇合成气,同时回收转化反应余热,副产蒸汽3.4 主要设备3.4.1 加热炉加热炉采用两段辐射、一段对流设计, 辐射段主要加热焦炉气混合气和高压废锅产次高压饱和蒸汽;对流段共加热4种介质:饱和塔循环热水、富氧蒸汽、NHD®脱硫气和预热加热炉助燃空气。3.4.2 转化炉转化炉采用圆筒式纯氧转化炉, 炉体为钢结构+耐火绝热材料+冷却水夹套。炉内装二段转化催化剂, 顶部为蒸汽冷却套中心管式烧嘴, 转化
18、所需热量通过氧气与焦炉气中氢气发生部分燃烧反应提供, 燃烧后的高温气体在催化剂床层发生甲烷与蒸汽的转化反应。转化炉出口温度控制为 960C-980C,残余CH的体积分数为 0.4%。3.4.3 高压废锅高压废锅是转化生产中最重要的设备, 本装置采用的高压废锅温差达到600以上( 出高压废锅工艺气体温度达340 ), 并且高压废锅与转化炉直连, 管道内浇筑2 层刚玉浇筑料 , 与高压废锅的浇筑料在烘炉时, 需形成一体耐火隔热层。高压废锅共分2 端 , 一端为高热端, 有 4 根汽液上升管和热水下降管, 内筑有耐火浇筑料。另一端为低热端, 有 2根汽液上升管和热水下降管。另配有汽包1 个 , 供应高压锅炉给水, 并实现汽液分离。本系统考虑到COS低温水解工艺路线存在的缺陷,对焦炉气的精脱硫采用高温加氢转化技术路线。采用铁 -钼加氢脱硫转化剂, 在高温环境下, 将气体中的有机硫转化, 生成易于脱除的硫化氢, 然后再采用固体铁- 锰脱硫剂吸收转化后气体中的硫化氢。这样可使有机硫加氢转化完全, 净化度大为提高, 并且可将不饱和烯烃进
温馨提示
- 1. 本站所有资源如无特殊说明,都需要本地电脑安装OFFICE2007和PDF阅读器。图纸软件为CAD,CAXA,PROE,UG,SolidWorks等.压缩文件请下载最新的WinRAR软件解压。
- 2. 本站的文档不包含任何第三方提供的附件图纸等,如果需要附件,请联系上传者。文件的所有权益归上传用户所有。
- 3. 本站RAR压缩包中若带图纸,网页内容里面会有图纸预览,若没有图纸预览就没有图纸。
- 4. 未经权益所有人同意不得将文件中的内容挪作商业或盈利用途。
- 5. 人人文库网仅提供信息存储空间,仅对用户上传内容的表现方式做保护处理,对用户上传分享的文档内容本身不做任何修改或编辑,并不能对任何下载内容负责。
- 6. 下载文件中如有侵权或不适当内容,请与我们联系,我们立即纠正。
- 7. 本站不保证下载资源的准确性、安全性和完整性, 同时也不承担用户因使用这些下载资源对自己和他人造成任何形式的伤害或损失。
最新文档
- 农村屋子交易合同样本
- 中介佣金合同样本简约样本
- 个人电机转让合同样本
- 【高三】【下学期期中】(高考前的“加速度”)家长会逐字稿
- 公司注销合同样本
- 出租房屋协议合同标准文本
- 乙方工地材料合同样本
- 养鸭子合同样本
- 买卖沙居间合同标准文本
- 提升企业员工忠诚度的工作思路计划
- 2025年高考思辨作文备考之17例高级思辨素材
- 2025年中国二氧化碳市场运行态势及行业发展前景预测报告
- 格构梁班组合同
- 福建省泉州市20023年第29届WMO竞赛二年级数学下学期竞赛试卷
- 2025年安全生产有限空间作业应急处理能力试题集试卷
- 四川省昭觉中学高中地理 1.2 当代环境问题的产生及特点教学实录 新人教版选修6
- 内蒙古赤峰山金红岭有色矿业有限责任公司招聘考试真题2024
- 苏州卷-2025年中考第一次模拟考试英语试卷(含答案解析)
- 撬装式承压设备系统安全技术规范
- 融资面试试题及答案
- 2024山西三支一扶真题及答案
评论
0/150
提交评论