

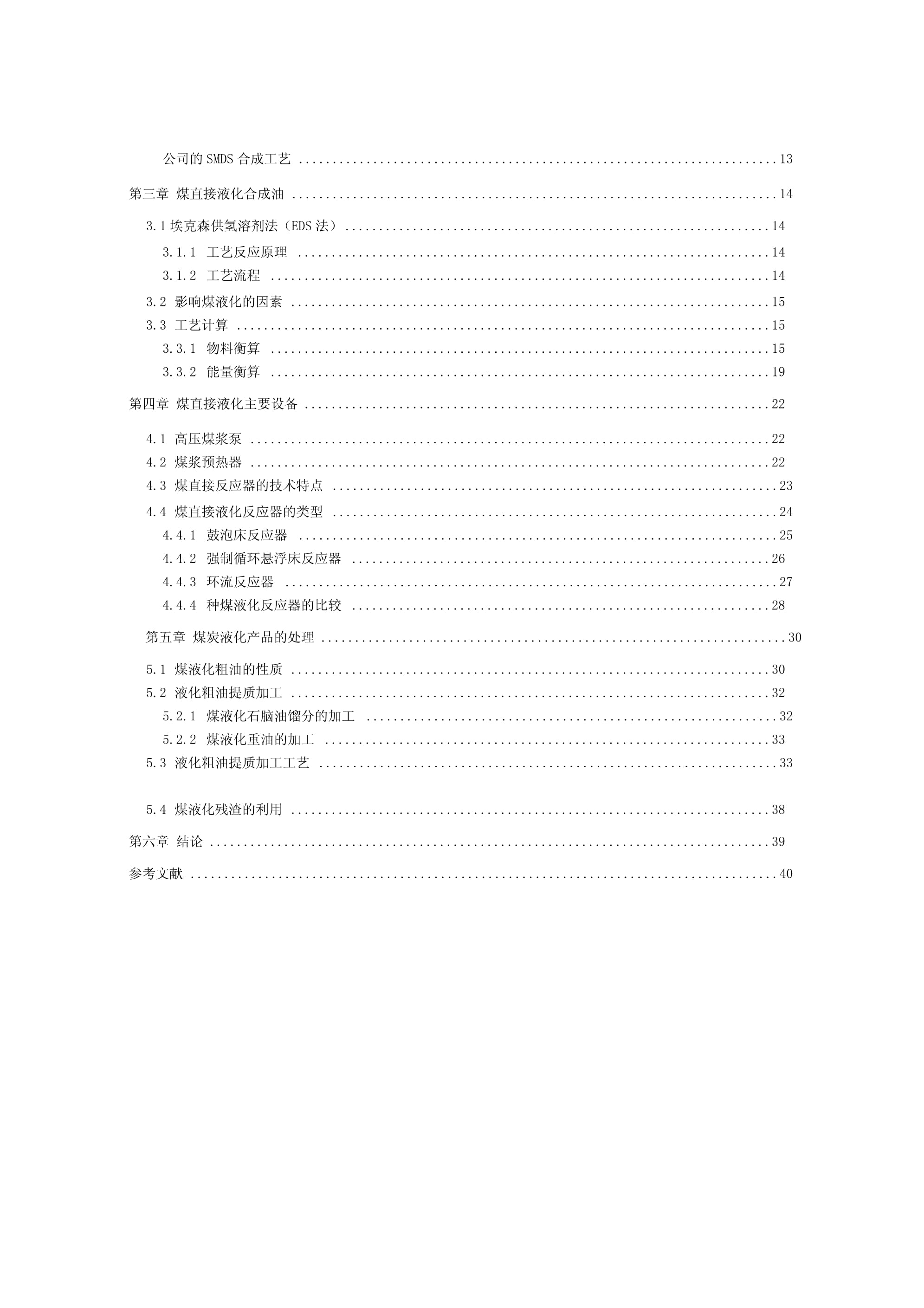
版权说明:本文档由用户提供并上传,收益归属内容提供方,若内容存在侵权,请进行举报或认领
文档简介
煤直接液化制油的设计目录TOC\o"1-5"\h\z摘要 1\o"CurrentDocument"第一章绪论 2\o"CurrentDocument"煤制油的发展历程 2煤直接液化在世界的发展史 2煤炭间接液化制油在世界的发展史 3中国煤制油 4\o"CurrentDocument"煤制油的意义 4\o"CurrentDocument"第二章 煤炭液化的工艺 6\o"CurrentDocument"直接液化的基本原理 6、反应模型 7\o"CurrentDocument"单段液化工艺 7221埃克森供氮溶剂法(EDS工艺) 7IGOR工艺流程描述 9\o"CurrentDocument"2.3、催化两段液化工艺(CTSL工艺) 10\o"CurrentDocument"2.4煤间接液化工艺 12公司MTG工艺 12SASOL工艺 12公司的SMDS合成工艺 13\o"CurrentDocument"第三章煤直接液化合成油 14\o"CurrentDocument"3.1埃克森供氢溶剂法(EDS法) 14工艺反应原理 14工艺流程 14影响煤液化的因素 15工艺计算 15物料衡算 15能量衡算 19\o"CurrentDocument"第四章煤直接液化主要设备 22\o"CurrentDocument"高压煤浆泵 22\o"CurrentDocument"煤浆预热器 22\o"CurrentDocument"煤直接反应器的技术特点 23\o"CurrentDocument"煤直接液化反应器的类型 24鼓泡床反应器 25强制循环悬浮床反应器 26环流反应器 27种煤液化反应器的比较 28\o"CurrentDocument"第五章煤炭液化产品的处理 30\o"CurrentDocument"煤液化粗油的性质 30\o"CurrentDocument"液化粗油提质加工 32煤液化石脑油馏分的加工 32煤液化重油的加工 33\o"CurrentDocument"液化粗油提质加工工艺 33\o"CurrentDocument"煤液化残渣的利用 38\o"CurrentDocument"第六章结论 39\o"CurrentDocument"参考文献 40摘要石油是一种重要的战略物质,有了它,船舰可以乘风破浪,汽车可以翻山越岭,飞机可以穿云透雾……然而,近年来国际石油价格飞涨,供需差距越来越大。以我国为例,石油年消费量约为2.5亿吨,生产能力仅约15亿吨,预计2005年和2015年消费量将超过2.6亿吨和3.1亿吨,尤其若干年后石油开采枯竭的时候,这些动力和交通工具又该靠什么来运行呢?不必担心,聪慧的科学家们早已为我们设计了一个煤变石油的方案。许多勘探资料都表明,全世界煤的可开采资源是巨大的,其能量值相当于石油资源的10倍。煤和石油的形态、形成历史、地质条件虽然不同,但是它们的化学组成却大同小异。煤中约含碳80%~85%,含氢4%~5%,平均分子量在2000以上。石油含碳85%,含氢13%,平均分子量在600以内。从组成上看,它们的主要差异是含氢量和分子量的不同。因此,只要人为地改变压力和温度,设法使煤中的氢含量不断提高,就可以使煤的结构发行变异,由大分子变成小分子。当其碳氢比降低到和石油相近时,则煤就可以液化成汽油、柴油、液化石油气、喷气燃料等石油产品了。同时还可以开发出附加值很高的上百种产品,如乙烯、丙烯、醇、酮、化肥等,经济效益十分可观。综合我国总的能源特征是“富煤、少油、有气”。2003年我国总能源消费量达11.783亿吨油。其中,煤炭占67.86%,石油占23.35%,天然气占2.5%,水电占5.43%,核能占0.83%。我国拥有较丰富的煤炭资源, 2000~2003年探明储量均为1145亿吨,储采比由2000~2001年116年下降至2002年82年、2003年69年。而石油探明储量2003年为32亿吨,储采比为19.1年。在较长一段时间内,我国原油产量只能保持在1.6~1.7亿吨/年的水平。煤炭因其储量大和价格相对稳定,成为中国动力生产的首选燃料。在本世纪前50年内,煤炭在中国一次能源构成中仍将占主导地位。预计煤炭占一次能源比例将由1999年67.8%、2000年63.8%、2003年67.8%达到2005年50%左右。我国每年烧掉的重油约3000万吨,石油资源的短缺仍使煤代油重新提上议事日程,以煤制油己成为我国能源战略的一个重要趋势。关键词:煤直接液化间接液化技术第一章绪论能源是社会、经济发展的基础。优化能源消费结构,安全保障能源供应是中国经济建康发展、实现在21世纪中叶达到中等发达国家水平战略目标的重要支持和内容。随着中国经济的高速发展,如何有效地发挥煤炭资源优势,优化能源结构,解决石油各短缺及由此造成的能源安全问题,已经引起我国政府的高度重视。我国煤炭资源丰富,煤种齐全,煤炭资源占能源储量的92%,这就决定了我国的能源生产和消费在相当长的时期仍以煤炭为主,目前占70%左右。随着能源消费总量的增加,煤炭需求总量将增加,大幅度减少煤炭消费是较难办到的。另外,我国能源分布不均,重心偏西偏北,而经济发达区域偏南偏东,常规能源需要长途运输才能满足需求,而且烟煤型污染已经给生态环境带来严重问题。因此为了减少环境污染,提高煤炭利用效率,减少消费,降低C02排放量,生产便于运输的燃料,开发出了煤炭液化技术。煤炭液化技术是指煤炭转化为液态烃的技术,可将煤转化为汽油、柴油、 LPG等产品。因此,以国内丰富的煤炭资源为基础,大力发展煤炭液化技术,尽快实现商业化生产,并最终形成新的煤炭能源转化产业,对于平衡我国能源结构,解决石油短缺具有重大战略意义,其产业前景非常乐观。从国家政策来看,以煤代油是中国长期能源政策中的重要组成部分,中央及地方政府十分支持“煤代油”技术的发展,其中煤炭液化是“煤代油”主要技术之一。我国已将发展煤炭液化列入国家“十五”发展规划,中央高层领导对煤炭液化技术的发展也十分重视和支持。发展煤炭液化作为我国保证煤炭工业可持续展,缓解环境恶化,优化能源结构,解决石油短缺,保证能源供应安全的最有效途径之一。煤制油的发展历程煤液化技术可分为直接液化和间接液化两大类。接近工业化的煤直接液化技术有:德国IG-OR工艺,美国HTI工艺,日本NEDOI工艺;已商业化的煤间接液化技术有:南非Sasol固定床高温工艺石油一直是全球各国重要的战略资源。煤直接液化在世界的发展史煤的直接液化:煤直接液化技术研究始于上世纪初的德国,1927年在Leuna建成世界上第一个10万吨/年直接液化厂。1936〜1943年间,德国先后建成11套直接液化装置,1944年总生产能力达到400万吨/年,为德国在第二次世界大战中提供了近三分之二的航空燃料和50%的汽车及装甲车用油。第二次世界大战结束,美国、日本、法国、意大利及前苏联等国相继开展了煤直接液化技术研究。50年代后期,中东地区廉价石油的大量开发,使煤直接液化技术的发展处于停滞状态。1973年,爆发石油危机,煤炭液化技术重新活跃起来。德国、美国及日本在原有技术基础上开发出一些煤直接液化新工艺,其中研究工作重点是降低反应条件的苛刻度,从而达到降低液化油生产成本的目的。目前不少国家已经完成了中间放大试验,为建立商业化示范厂奠定了基础。世界上有代表性的煤直接液化工艺是德国的新液化( IGOR)工艺,美国的HTI工艺和日本的NEDO工艺。这些新液化工艺的共同特点是煤炭液化的反应条件比老液化工艺大为缓和,生产成本有所降低,中间放大试验已经完成。目前还未出现工业化生产厂,主要原因是生产成本仍竞争不过廉价石油。今后的发展趋势是通过开发活性更高的催化剂和对煤进行顶处理以降低煤的灰分和惰性组分,进一步降低生产成本。煤炭间接液化制油在世界的发展史煤炭间接液化技术主要有三种,即的南非的萨索尔( Sasol)费托合成法、美国的莫比尔法(Mobil)和正在开发的直接合成法。目前,煤间接液化技术在国外已实现商业化生产,全世界共有3家商业生产厂正在运行,它们分别是南非的萨索尔公司和新西兰、马来西亚的煤炭间接液化厂。新西兰煤炭间接液化厂采用的是Mobil液化工艺,但只进行间接液化的第一步反应,即利用天然气或煤气化合成气生产甲醇,而没有进一步以甲醇为原料生产燃料油和其它化工产品,生产能力1.25万桶/天。马来西亚煤炭间接液化厂所采用的液化工艺和南非萨索尔公司相似,但不同的是它以天然气为原料来生产优质柴油和煤油,生产能力为50万t/年。因此,从严格意义上说,南非萨索尔公司是世界上唯一的煤炭间接液化商业化生产企业。南非萨索尔公司成立于50年代初,1955年公司建成第一座由煤生产燃料油的Sasol-1厂。70年代石油危机后,1980年和1982年又相继建成Sasol-2厂和Sasol-3厂。3个煤炭间接液化厂年加工原煤约4600万t,产品总量达768万t,主要生产汽油、柴油、蜡、氨、乙烯、丙烯、聚合物、醇、醛等 113种产品,其中油品占60%,化工产品占40%。该公司生产的汽油和柴油可满足南非28%的需求量,其煤炭间接液化技术处于世界领先地位。此外,美国SGI公司于80年代末开发出了一种新的煤炭液化技术,即LFC(煤提油)技术。该技术是利用低温干馏技术,从次烟煤或褐煤等非炼焦煤中提取固态的高品质洁净煤和液态可燃油。美国SGI公司于1992年建成了一座日处理能力为1000t的次烟煤商业示范厂。中国煤制油我国从70年代末开始进行煤炭直接液化技术的研究和攻关,其目的是用煤生产汽油、柴油等运输燃料和芳香烃等化工原料。煤炭科学研究总院通过“六五”到“九五”的科技攻关和国际合作,先后从日本、德国引进2套直接液化小型连续试验装置,从美国引进一套液化油提质加工试验装置,规模均为0.1t/天,并建有先进的原料及产品分析检验装备。经过近20年的试验研究,找出了14种适于直接液化的中国煤种;选出了5种活性较高的、具有世界先进水平的催化剂;完成了4种煤的工艺条件试验,为开发适于中国煤种的煤直接液化工艺奠定了基础;成功地将煤液化粗油加工成合格的汽油、柴油和航空煤油。目前,从煤一直到合格产品的全流程已经打通,煤炭直接液化技术在中国已完成基础性研究,为进一步工艺放大和建设工业化生产厂打下了坚实的基础。我国从50年代初即开始进行煤炭间接液化技术的研究,曾在锦州进行过4500t/年的煤间接液化试验,后因发现大庆油田而中止。由于70年代的两次石油危机,以及“富煤少油”的能源结构带来的一系列问题,我国自80年代初又恢复对煤间接液化合成汽油技术的研究,由中科院山西煤化所组织实施。“七五”期间,山西煤化所开的煤基合成汽油技术被列为国家重点科技攻关项目。1989年在代县化肥厂完成了小型实验。“八五”期间,国家和山西省政府投资2000多万元,在晋城化肥厂建立了年产2000吨汽油的工业试验装置,生产出了90号汽油。在此基础上,提出了年产10万吨合成汽油装置的技术方案。目前,万吨级煤基合成汽油工艺技术软件开发和集成的研究正在进行,从90年代初开始研究用于合成柴油的钴基催化剂技术也正处在试验阶段。经过20年的开发和研究,目前我国已经具备建设万吨级规模生产装置的技术储备,在关键技术、催化剂的研究开发方面已拥有了自主知识产权。可以这样讲,我国自己研发的煤炭液化技术已达到世界先进水平。1.2煤制油的意义我国煤炭资源丰富,煤种齐全,发展煤炭液化、气化等技术,对发挥资源优势,优化终端能源结构,大规模补充国内石油供需缺口有着现实和长远意义。主要体现在:第一,产品为清洁能源,减少污染;第二,煤炭—能源化工一体化,发展新兴产业;第三,高新技术优化集成,推动现代煤化工技术发展和产业化建设;第四,建设大型企业和产业基地;第五,有效利用煤炭资源,高效利用,使各种煤种煤质物尽其用,减少资源浪费;第六,经济效益最大化,通过建设大型工厂,提高综合经济效益;第七,人力资源得到发挥。通过产业化建设,带动其他运输、建筑、服务等行业发展,扩大就业,充分利用人力资源。第二章煤炭液化的工艺煤的液化是先进的洁净煤技术和煤转化技术之一,是用煤为原料以制取液体烃类为主要产品的技术。煤掖化分为“煤的直接液化”和“煤的间接液化”两大类。煤直接液化煤在氢气和催化剂作用下,通过加氢裂化转变为液体燃料的过程称为直接液化。裂化是一种使烃类分子分裂为几个较小分子的反应过程。因煤直接液化过程主要采用加氢手段,故又称煤的加氢液化法。煤的间接液化是以煤基合成气(CO+H2)为原料,在一定的温度和压力下,定向催化合成烃类燃料油和化工原料的工艺,包括煤气化制取合成气及其净化、变换、催化合成以及产品分离和改质加工等过程。通过煤炭液化,不仅可以生产汽油、柴油、LPG液化石油气)、喷气燃料,还可以提取BTX苯、甲苯、二甲苯),也可以生产制造各种烯烃及含氧有机化合物。煤炭液化可以加工高硫煤,硫是煤直接液化的助催化剂,煤中硫在气化和液化过程中转化成H2S再经分解可以得到元素硫产品。直接液化的基本原理反应机理大量研究证明,煤在一定温度、压力下的加氢液化过程基本分为三大步骤,首先,当温度升至300C以上时,煤受热分解,即煤的大分子结构中较弱的桥键开始断裂,打碎了煤的分子结构,从而产生大量的以结构单元分子为基体的自由基碎片,自由基的相对分子质量在数百范围。第二步,在具有供氢能力的溶剂环境和较高氢气压力的条件下,自由基被加氢得到稳定,成为沥青烯及液化油的分子。能与自由基结合的氢并非是分子氢(H2),而应是氢自由基,即氢原子,或者是活化氢分子,氢原子或活化氢分子的来源有:①煤分子中碳氢键断裂产生的氢自由基;②供氢溶剂碳氢键断裂产生的氢自由基;③氢气中的氢分子被催化剂活化;④化学反应放出的氢,如系统中供给(C0+H2。),可发生变换反应(COH2。CO2H2)放出氢。当外界提供的活性氢不足时,自由基碎片可发生缩聚反应和高温下的脱氢反应,最后生成固半焦或焦炭。第三步,沥青烯及液化油分子被继续加氢裂化生成更小的分子。所以,煤液化过程中,溶剂及催化剂起着非常重要的作用。、反应模型为了能利用计算机模拟计算煤液化反应的结果,根据以上反应机理的分析,许多研究者假设了煤加氢液化的各种反应模型。最有代表性的是日本研究者的模型,见图2-1-12-1-1煤液化反应模型该模型假设原料煤分成三种类型。CI是不反应的惰性煤。CB热解只产生沥青烯类物质。CA热解产生气体、重质油和沥青烯三种物质。沥青烯加氢产生气体、水、轻质油,CA产生的重质油加氢产生中油。通过积累大量试验数据,可算出模型中的各反应的级数及速度常数冷, 再通过不同温度下求出的k值,可求出各反应的活化能。以上反应机理实际上并不是真正的墓元反应, 由此得出的动力学模型仅仅是一种表观的形式,但被应用于反应器模拟计算时已足够了。也可以划到这两种工艺中去。同样,两种液化工艺都可改进用来做煤油共处理。2.2单段液化工艺埃克森供氮溶剂法(EDS工艺)EDS是美国公司开发的一种煤炭直接液化工艺。公司从1966年开始研究煤炭直接液化技术,对EDS工艺进行开发,并在0.5t/d的连续试验装置上确认了EDS工艺的技术可行性。1975年6月,1.0t/d规模的ETA工艺全流程中试装置投人运行,进一步肯定了ELF工艺的可靠性。1980年在德克萨斯的建了250t/d的工业性试验厂,完成了EDS工艺的研究开发工作。EDS工艺的基本原理是利用间接催化加氢液化技术使煤转化为液体产品, 即通过对产自工艺本身的作为循环溶剂的馏分,在特别控制的条件下采用类似于普通催化加氢的方法进行加氢,向反应系统提供氢的“载体”。加氢后的循环溶剂在反应过程中释放出活性氢提供给煤的热解自由基碎片。释放出活性氢的循环溶剂馏分通过再加氢恢复供氢能力,制成煤浆后又进人反应系统,向系统提供活性氢。通过对循环溶剂的加氢提高溶剂的供氢能力,是EDS工艺的关键特征,工艺名称也由此得来。烝曲>图2-1-1 工艺流程图EDS工艺流程描述煤与加氢后的溶剂制成煤浆后,与氢气混合,预热后进人上流式管式液化反应器,反应温度425~450C和液体产物,反应压力17.5MPa不需另加催化剂。反应产物进入气液分离器,分出气体产物。气体产物通过分离后,富氢气与新鲜氢混合使用。液体产物进入常、减压蒸馏系统,分离成气体燃料、石脑油、循环溶剂馏分、和其他液体产品及含固体的减压塔釜底残渣。循环溶剂馏分(中、重馏分)进入溶剂加氢单元,通过催化加氢恢复循环溶剂的供氢能力。循环溶剂的加氢在固定床催化反应器中进行, 使用的催化剂是石油工业传统的镍一钼或钻一铂铝载体加氢催化剂。反应器操作温度 370r,操作压力11MPa改变条件可以控制溶剂的加氢深度和质量。溶剂加氢装置可在普通的石油加氢装置上进行。加氢后的循环溶剂用于煤浆制备。含固体的减压塔釜底残渣在流化焦化装置进行焦化,以获得更多的液体产物。流化焦化产生的焦在气化装置中气化制取燃料气。流化焦化和气化被组合在一套装置中联合操作,被称为灵活焦化法。灵活焦化法的焦化部分反应温度为 485~650C,气化部分的反应温度为800~900C。整个停留时间为0.5—lh。EDS工艺的产油率较低,有大量的前沥青烯和沥青烯未转化为油,可以通过增加
煤浆中减压蒸馏的塔底物的循环量来提高液体收率。 EDS工艺典型的总液体收率(包括灵活焦化产生的液体)为:褐煤36%,次烟煤38%,烟煤39%~46%全(部以干基无灰煤为计算基准)。EDS工艺采用供氢溶剂来制备煤浆,所以液化反应条件温和,但由于液化反应为非催化反应,液化油收率低,这是非催化反应的特征。加重质馏分的停留时间可以改善液化油收率,虽然将减压蒸馏的塔底物部分循环送回反应器但同时带来煤中矿物质在反应器中的积聚问题,增加重质馏分的停留时间可以改善液化油收率 ,但同时带来煤中矿物质在反应器中的积聚时间问题。IGOR工艺流程描述煤与循环溶剂及“赤泥”可弃铁系催化剂配成煤浆,与氢气混合后预热。预热后的混合物一起进人液化反应器,典型操作温度470C,压力30.0MPa,反应空速0.5"(m3-h}反应器产物进入高温分离器。高温分离器底部液化粗油进人减压闪蒸塔,减压闪蒸塔底部产物为液化残渣,顶部闪蒸油与高温分离器的顶部产物一起进人第一固定床反应器,反应条件:温度350一420C,压力与液化反应器相同, 第一固定床反应器产物进人中温分离器。中温分离器底部重油为循环溶剂,去用于煤浆制备。中温分离器顶部产物进人第二固定床反应器,反应条件:温度350~420C,压力与液化反应器相同,第二固定床反应器产物进人低温分离器,低温分离器顶部副产氢气循环使用。低温分离器底部产物进人常压蒸馏塔,在常压蒸馏塔中分馏为汽油和柴油。IGOR工艺的操作条件在现代液化工艺中最为苛刻,所以适合于烟煤的液化。在处理烟煤时,可得到大于90%的转化率,液收率以无水无灰煤计算为50%~60%液化油在IGOR工艺中经过十分苛刻条件的加氢精制后,产品中的S、N含量降到10数量级(几十个ppm数量级)。表2-2-1为德国烟煤在IGOR工艺中的产率结果和产品性质表。表2-2-1为云南先锋揭煤在IGOR工艺中的液化结果。
图2-2-1德国烟煤IGORX艺产率和产品性质产物产率(质量分数)烃类气体(C1~C4)19.0轻油(C5〜200C)25.3中油(200〜325C)32.6未反应的煤和沥冃22.1产品性质轻油 中油氢%(质量分数)13.611.9氮106(质量分数)391746氧10(质量分数)15384硫106(质量分数)12<5密度/(kg/m\7729122.3、催化两段液化工艺(CTSL工艺)催化两段液化工艺是H-Coal单段工艺的发展。在美国的液化试验装置上,对该工艺进行了 15年的研究。该工艺现在已演化成在20世纪80年代和20世纪卯年代美国能源部资助的许多液化工艺的组合。采用了紧密串联结构,每段都使用活性载体催化剂。此工艺现称作催化两段液化工艺。由美国能源部资助,美国碳氢化合物研究公司(HRI)开发,包括PDU规模试验。催化两段液化工艺工艺流程见图Iftifl分隔瞎Iftifl分隔瞎图2-3-1 催化剂两段液化工艺(CTSL)流程图催化两段液化工艺(CTSL)工艺流程描述煤与循环溶剂配成煤浆,预热后,与氢气混合加入到沸腾床反应器的底部。反应器内填装载体催化剂,通常为镍一铭铝载体催化剂(有些工艺使用分散可弃催化剂),催化剂被反应器内部循环流流态化。因此反应器具有连续搅抨釜式反应器的均一温度特征。溶剂具有供氢能力,在第一反应器中,通过将煤的结构打碎到一定程度而将煤溶解。第一反应器也对溶荆进行再加氮。操作压力是17.0MPa,操作温度在400~420C。反应产物直接进人第二段沸腾床反应器中,操作压力与第一段相同但温度要高。反应器也装有载体催化剂。操作温度通常达至 420~440C。 第二反应器的产物经分离和减压后,进入常压蒸馏塔,蒸馏切割出沸点小于400C馏分,常压蒸馏塔塔底含有溶剂、未反应的煤和矿物质。常压蒸馏塔塔底物进行固液分离,脱除固体,溶剂循环至煤浆段。在有些工艺中只有部分常压蒸馏塔底进行固体分离, 这样,循环溶剂中含有矿物质和可能使用的分散催化剂。固液分离方法采用 Kerr-McGeeCSD/ROS工艺表2-3-1列出CTSLX艺液化烟煤时产品的典型性质和产率。图2-3-1催化两段液化方法产品性质产率/%(质量分数)产率/%(质量分数)产率/%(质量分数)G~C48.6氢耗/%质量分数7.9H/%(质量分数)11.73C4~272C19.7煤转化率/%质量分数96.8272~346C36.0>C4馏分油质量N/%(质量分数)0.25346~402C22.2API 27.62.4煤间接液化工艺公司MTGT艺甲醇转化成汽油MTG技术是由Mobil研究与开发公司开发成功,该技术间接克服了煤基合成甲醇直接作燃料的缺点。成为煤转化成汽油的重要途径。这一技术的核心是选择沸石分子筛催化剂ZSM-5,其优点是较F-T合成的成本低、合成汽油的芳烃含量高,特别是均四甲苯的含量达3.6%,在性能上又与无铅汽油相当。MTG反应为强放热反应,在绝热条件下,体系温度可达到610C左右。远超过反应允许的反应温度范围,因此反应生成热量必须移出,为此Mobile公司开发出两种类型的反应器。一是绝热固定床反应器,另二一个是流化床反应器, 1979年以来美国化学系统公司又成功地开发出浆态床甲醇合成技术并完成了中试研究,浆态床比其他反应器有独特优点。绝热固定床反应器把反应分为两段,第一阶段反应器为脱水反应器,在其中完成二甲醚合成反应,在第二阶段反应器中完成甲醇、二甲醚和水平衡混合物转化成烃的反应。第一、第二反应器中反应热分别占总反应热的百分数为 20%和80%。工艺流程如图2-2-1。甲醇转化反应是在催化剂上一狭窄带状区域进行,随反应时间延长,这一催化剂带失活,催化反应逐步沿反应器向下移动,最终整个反应器中的催化剂活化需要再生,图2-2-1有四个反应器,在实际生产中正常操作条件下,至少有一个反应器在再生。MTG反应器由于积炭而失活,需要周期性再生,再生周期一般为 20天,可通过通入热空气进行再生。二甲醚反应器不积炭。正常情况下无需再生。流化床反应器与固定床反应器完全不同,流化床反应器中,用一个反应器代替两段固定床反应器。甲醉与水混合后加人反应器,加料为液态或气态。在反应器上部气态反应产物与催化剂分。SASOL工艺萨索尔(Sasol)是南非煤炭、石油和天然气股份有限公司(SouthAfricanCoal,OilandGasCorp.)的简称。南非缺乏石油资源但却蕴藏有大量煤炭资源。为了解决当地石油的需求问题,于1951年筹建了SASOL公司。1955年建成了第一座由煤生产液体运输燃料的SASOL-I厂。建设由美国凯洛格公司及原西德的阿奇公司(Arge即ArbeitGemeinshaftLurgiundRuhrchemie) 承包。阿奇建造的五台固定床反应器作为第一段,年产量为53,000t初级产品,开洛格建造了两套流化床反应器(Synthol),设计年产液体燃料166000t,在SASOL-I厂成功的经验上,1974年开始,南非在赛昆达地区开工建设了SASOL-II厂,并于1980年建成投产。1979年又在赛昆达地区建设了SASOL-III厂,规模与II厂相同,造气能力大约是SASOL-I厂的8倍。随着时代的变迁和技术的进步,SASOL三个厂的生产设备、生产能力和产品结构都发生了很大的变化。目前三个厂年用煤 4590万t,其中I厂650万t/年,II厂和III厂3940万t/年。主要产品是汽油、柴油、蜡、氨、烯烃、聚合物、醇、醛等113种,总产量达760万t,其中油品大约占60%公司的SMDS^成工艺值高的条件下,可以高选择性和高收率地合成高分子长链烷烃,同时也大大降低了低碳气态烃的生成。在1985年第五次合成燃料研讨会上,该公司宣布已开发成功F-T合成两段法的新技术—SMDS(Shell多年来,荷兰皇家Shell石油公司一直在进行从煤或天然气基合成气制取发动机燃料的研究开发工作。尤其对一氧化碳加氢反应的Schulz-Flory聚合动力学的规律性进行了深入的研究,认为在链增长的MiddleDistillateSynthesis)工艺,并通过中试装置的长期运转。SMDS合成工艺由一氧化碳加氢合成高分子石蜡烃一HPS(HeavyParaffinSynthesis)过程和石蜡烃加氢裂化或加氢异构化—HPC(HeavyParaffinCoversion)制取发动机燃料两段构成。Shell公司的报告指出,若利用廉价的天然气制取的合成气(H2/CO=2.0)为原料,采用SMD工艺制取汽油、煤油和柴油产品,其热效率可达60%,而且经济上优于其他F-T合成技术。值可控制在0.80〜0.94之间。HPS技术采用管式固定床反应器。为了提高转化率,合成过程分两段进行。第一段安排了3个反应器。第二段只设一个反应器。每一段设有单独的循环气体压缩机。大约总产量的 85%在第一段生成,其余15%在第二段生成。反应系统操作参数如下:合成气组成H2/CO=2.0,反应压力2.0 Shell公司采用自己开发的热稳定性较好的钴系催化剂高选择性地合成了长链石蜡烃 (〜C50),其链增长MPa〜4.0MPa,反应温度200E〜240E,全过程CO转化率:95%单程单段CO转化率40%第三章煤直接液化合成油3.1埃克森供氢溶剂法(EDS法)工艺反应原理EDS工艺的基本原理是利用间接催化加氢液化技术使煤转化为液体产品, 即通过对产自工艺本身的作为循环溶剂的馏分,在特别控制的条件下采用类似于普通催化加氢的方法进行加氢,向反应系统提供氢的“载体”。加氢后的循环溶剂在反应过程中释放出活性氢提供给煤的热解自由基碎片。释放出活性氢的循环溶剂馏分通过再加氢恢复供氢能力,制成煤浆后又进人反应系统,向系统提供活性氢。通过对循环溶剂的加氢提高溶剂的供氢能力,是EDS工艺的关键特征,工艺名称也由此得来。工艺流程煤与加氢后的溶剂制成煤浆后,与氢气混合,预热后进人上流式管式液化反应器,反应温度425~450C,反应压力17.5MP&不需另加催化剂。反应产物进入气液分离器,分出气体产物和液体产物。气体产物通过分离后,富氢气与新鲜氢混合使用。液体产物进人常、减压蒸馏系统,分离成气体燃料、石脑油、循环溶剂馏分、和其他液体产品及含固体的减压塔釜底残渣。循环溶剂馏分(中、重馏分)进人溶剂加氢单元,通过催化加氢恢复循环溶剂的供氢能力。循环溶剂的加氢在固定床催化反应器中进行,使用的催化剂是石油工业传统的镍一钼或钻一钼铝载体加氢催化剂。反应器操作温度370C,操作压力11MPa改变条件可以控制溶剂的加氢深度和质量。溶剂加氢装置可在普通的石油加氢装置上进行。加氢后的循环溶剂用于煤浆制备。EDS的特点:EDS工艺的产油率较低,有大量的前沥青烯和沥青烯未转化为油,减压蒸馏的塔底物的循环量来提高液体收率。3.2影响煤液化的因素3.3工艺计算物料衡算1、基础数据年生产力:1600000t/a年开工时数:8000h原料采用义马褐煤,元素质量组成如表 3-3-1-1所示表3-3-1-1元素质量组成元素组分质量%元素组分质量%C70.62N2.48H6.28S1.16O18.92[P0.54(4)产品组成如表3-3-1-2所示产品组成质量%产品组成质量%气体ACH415.725.46液体AC4H10 轻质油32.8021.46C2H647.88C5〜C11汽油78.54C2H426.66气体BC3H67.618.52液体BC11〜C18柴油43.90C3H835.70C4H845.78(5)基准年工作为8000h,以1h为基准416010 8000=200t/h以100t/h为基准进行计算2、计算范围全装置如图3-3-2所示3、物料衡算(1)产品的计算生产出液体的量战总产品的比例:32.80%+43.90%=71.70%总产品的质量:200 76.70%=260.7562t/h混合气体A的质量:260.756215.70%=40.9837t/h混合气体B的质量:260.75627.60%=19.8175t/h混合液体A的质量:260.756232.80%=85.5280t/h混合液体B的质量:260.756243.90%=114.4732t/h甲烷的质量:40.983725.46%=10.4344t/h乙烷的质量:40.983747.88%=19.6016t/h乙烯的质量:40.983726.66%=10.9142t/h丙烯的质量:19.817518.52%=3.6702t/h丙烷的质量:19.817535.70%=7.7048t/h丁烯的质量:19.817545.78%=9.0724t/h轻质油的质量:85.528021.46%=18.3554t/h汽油的质量:85.528078.54%=67.1736t/h柴油的质量:260.756243.90%=114.4732t/h(2)原料的计算设制取100t/h的产品油所需的原料为At/h。则所用催化剂为:4%At/h全过程的氢耗量为:5.80%At/h其中,加氢反应器I中的氢耗量占总量的 68.00%加氢反应器U中的氢耗量占总量的32.00%另残渣内含油8.00%,全工艺流程如装置图所示:进入反应器的量:A+4%A=104.00%At/h高温分离器分离出的气体及轻油量:82.00%At/h高温分离器分离出的重质物料量:18.00%At/h减压塔分离出的油量:18.00%A76.00%t/h减压塔分离出的残渣量:18.00%A24.00%t/h残渣内含油量:18.00%A24.00%8.00%t/h实际的残渣量:18.00%A24.00%(1-8.00)t/h进入氢反应器I的气体及轻油量: 82.00%A+18.00%A76.00%t/h加氢反应器I的氢耗量:5.80%A68.00%t/h进入中温分离器分离的总量:82.00%A+18.00%A76.00%+5.80%A68.00%t/h中温分离器分离出的气体及轻质油量:(82.00%A+18.00%A76.00%+5.80%A68.00%)94.00%t/h中温分离器分离出的重质油量:(82.00%A+18.00%A76.00%+5.80%A68.00%)6.00%t/h循环溶剂的量:18.00%A24.00%+(82.00%A+18.00%A76.00%+5.80%A68.00%)6.00%t/h加氢反应器U的氢耗量:5.80%A32.00%t/h进入低温分离器的产品总量:(82.00%A+18.00%A76.00%+5.80%A68.00%)94.00%t+5.80%A32.00%t/h由a过程知总产品的质量:130.3781t/h则进入低温分离器的产品总量:( 82.00%A+18.00%A 76.00%+5.80%A 68.00% )94.00%t+5.80%A32.00%t/h=260.7562A=273.0432tt/h故得出:催化剂的加入量:4%136.5216t/h=5.4609t/h全过程氢的消耗量:5.80%136.5216t/h=7.9138t/h进入反应器的量:A+4%A=104.00136.5216t/h=141.9825t/h高温分离器分离出的气体及轻油量: 82.00%136.5216t/h=111.9477t/h高温分离器分离出的重质油量: 18.00%136.5216t/h=24.5739t/h减压塔分离出的油量:18.00%136.5216t/h76.00%t/h=18.6761t/h减压塔分离出的残渣量:18.00%136.5216t/h24.00%t/h=5.8977t/h残渣内含油量:18.00%136.5216t/h 24.00%8.00%=0.4718t/h实际的残渣量:18.00%A24.00% (1-8.00)=5.4259t/h进入氢反应器I的气体及清油量:82%136.5216t/h+136.5216t/h 76%=130.6239t/h进入反应器I的氢耗量:5.80%136.5216t/h68.00%=5.3846t/h进入中温分离器分离出的气体及轻质油量:(82%136.5216t/h+136.5216t/h 76%+5.80%136.5216t/h 68.00%)94.00%=130.5682t/h中温分离器分离的重质油量:(82%136.5216t/h+136.5216t/h 76%+5.80%136.5216t/h 68.00%)6.00%=8.1605t/h循环溶剂的量:18.00%136.5216t/h 24.00%+(82.00%136.5216+18.00%136.5216t/h 76.00%+5.80135.5216t/h 68.00%)6.00%=14.0582t/h加氢反应器U的氢耗量:5.80%135.5216t/h32.00%=2.5339t/h125136.5216= 170.6250由此知实际需煤量: 100煤液化物料衡算如表3-3-3所示表3-3-3煤液化物料衡算组分组成输入输出原料质量t产品质量t煤136.5216总产品130.3781C96.4116ch45.2115
H8.5736C2H69.8008O25.8299C2H45.4751N3.3857C3H61.8351S1.5837C3H83.5374P0.7372C4H84.5362H27.91836已。轻质油9.1772C5~C11汽油33.5868C11~C18柴油57.2360残油渣5.8977循环溶剂容量3.1605合计144.4399合计144.4399332能量衡算1.基础数据(1)各产物的比热容如表3-3-2-1所示表3-3-2-1产物的比热容产品比热容kJ/kgC产品比热容kJ/kgC甲烷1.70丁烯2.314乙烷1.44轻质油1.730乙烯1.222汽油2.200丙烷1.65柴油2.100丙烯2.436(2)已知能量公式Q=CM,进口温度350C,出口温度25C,由物料衡算知各物料的质量。计算范围对液体在低温分离器分离过程进行能量衡算能量衡算对低温分离器进口处各物料进行能量计算
对低温分离器进口处各物料进行能量计算36甲烷的能量:10.4344103170350=6.2016106kJ乙烷的能量:19.60161031.44350=9.8792106kJ乙烯的能量:10.91421031.222350=4.6680106kJ丙烷的能量:7.70481031.65350=4.0856106kJ丙烯的能量:3.67021032.436350=3.130106kJ丁烯的能量:9.07243102.314350=7.3478106kJ轻质油的能量:18.35541031.7350=11.1136106kJ汽油的能量:67.17361032.200350=5.1722107kJ37柴油的能量:114.47321032.100350=8.4136107kJ低温分离器进口处各物料的总能量:6666663.100810+9.879210+4.668010+4.085610+3.13010+7.347810+11.1167773635101.7325=7.938210kJ10+5.172210+8.4136103635101.7325=7.938210kJ甲烷的能量:10.43441031.70025=4.429810乙烷的能量:319.60161031.44525=7.056610kJ乙烯的能量:10.91421031.22225=3.3342105kJ丙烷的能量:7.70481031.6525=2.9184105kJ丙烯的能量:3.67021032.43625=2.2352105kJ丁烯的能量:39.0724102.314525=4.852410kJ轻质油的能量:18.35545kJ36汽油的能量:67.17361032.20025=3.6946106kJ36柴油的能量:114.4732102.10025=6.009810kJ
低温分离器出口处各物料的总能量:TOC\o"1-5"\h\z5 5 5 5 5 54.429810+7.056610+3.334210+2.918410+2.235210+4.852410+7.9385 6 6 6210+3.694610+6.009810=12.300410kJ7 6 7出的热量:Q放=Q进-Q出=18.284410—12.300410=16.984410kJ煤液化能量衡算如表3-3-2-2所示表3-3-2-2煤液化能量衡算各组分组成产品6输入能量Q(10kJ)输出能量Q(10kJ)ch46.20164.4298C2H69.87927.0566C2H44.66803.3342C3H63.1302.3553C3H84.08562.9184C4H87.34784.8524C4H10轻质油11.11367.9382C5~C11汽油51.72236.9460C11〜C18柴油84.13660.09852.1749(热损失)合计182.1038182.1038第四章煤直接液化主要设备煤直接液化是在高压和比较高的温度下的加氢过程,所以工艺设备及材料必须具有耐高压、以及临氢条件下耐氢腐蚀等性能。另外,直接液化处理的物料含有煤及催化剂等固体颗粒,因此,还要解决由于处理固体颗粒所带来的沉积、磨损、密封等技术问题。在此对一些关键设备作以简要介绍。4.1高压煤浆泵高压煤浆泵的作用是把煤浆从常压送人高压系统内,除了有压力要求外,还必须达到所要求的流量。煤浆泵一般选用的往复式高压柱塞泵,小流量可用单柱塞或双柱塞,大流量情况下要用多柱塞并联。柱塞材料必须选用高硬度的耐磨材料。柱塞泵的进出口煤浆止逆阀的结构形式必须适应煤浆中固体颗粒的沉积和磨损,这是必须解决的技术问题。由于柱塞在往复运动时内部为高压而外部为常压,因此密封问题也要得以解决,一般采用中间有油压保护的填料密封。荷兰生产的隔膜柱塞泵应用于煤浆输送是成功的。4.2煤浆预热器煤浆预热器的作用是在煤浆进人反应器前,把煤浆加热到接近反应温度。采用的加热方式小型装置采用电加热,大型装置采用加热炉。由于煤浆在升温过程中的翁度变化很大(尤其是烟煤煤浆),在300~400C范围内,煤浆钻度随温度的升高而明显上升。在加热炉管内,煤浆猫度升高后,一方面炉管内阻力增大,另一方面流动型式成为层流,即靠近炉管管壁的煤浆流动十分缓慢。这时如果炉管外壁热强度较大,温度过高,则管内煤浆很容易局部过热而结焦,导致炉管堵塞。解决上述间题的措施是一方面使循环氢与煤浆合并进人顶热器,由于循环气体的扰动作用,使煤浆在炉管内始终处于湍流状态。另一方面是在不同温度段选用不同的传热强度,在低温段可选择较高的传热强度,即可利用辐射传热,而在煤浆温度达到300C以上的高温段,必须降低传热强度,使炉管的外壁温度不致过高,建议利用对流传热。另外选择合适的炉管材料也能减少煤浆在炉管内的结焦。对于大规模生产装置,煤浆加热炉的炉管需要并联,此时,为了保证每一支路中的流量一致,最好每一路炉管配一台高压煤浆泵。还有一种解决预热器结焦堵塞的办法是取消单独的预热器,煤浆仅通过高压换热器升温至300C以下就进人反应器,靠加氢反应放热和对循环气体加热使煤浆在反应器内升至反应所需的温度。煤浆加热炉的设计参数选择可参照石油炼制加热炉的设计经验。煤浆加热炉的热负荷计算可以将热效应分解成以下几部分。煤粉升温所需的显热。煤粉受热分解所需的反应热(吸热,参考值:550~580kJ/kg)溶剂升温所需的显热。溶剂中轻组分蒸发所需的潜热。与煤浆一起进入的氢气升温所需的显热。有关数据可查阅有关手册。还有煤的自由基碎片有少部分加氢放出的反应热,反应热数值参见下一节。煤直接反应器的技术特点反应器是煤直接液化工艺的核心设备,其处理的物料包括气相氢、液相溶剂、少量的催化剂和固体煤粉,物料固体含量高,煤浆浓度为 40%-50%属于高固含量的浆态物料;而在反应条件下,气、液体积流量之比为8〜13[2]。这种高固含率和高气液操作比使得煤直接液化反应体系成为一个复杂的多相流动体系。一般来说,煤液化反应器的操作条件都是高温、高压。煤液化工艺不同,相应的操作条件也不同,一般煤直接液化反应器的操作条件如下[3]:压力/MPa15〜30温度/r440〜465气液比(标态V/V)700〜1000停留时间/h1〜2气含率/%0.1〜0.5进出料方式下部进料、上部出料在煤液化反应器内进行着复杂的化学反应过程,主要有煤的热解反应和热解产物的加氢反应,前者是吸热反应,后者是强放热反应,而总的热效应是放热反应[a}。因此反应器的温度一般要求严格控制,低于正常温度则反应不完全,其未反应的生煤将进入后续单元,给后续单元造成更大的操作负荷和难度;而反应温度过高,则容易使液化油气化,导致操作不稳定,油收率降低,也容易导致反应器结焦,减少了反应器的有效体积和物料在反应器内的停留时间,甚至导致反应中断。煤直接液化反应器在实践中应用时,必须考虑以下4个因素:保证足够的反应时间,主要是液相停留时间,为此,反应器内气含率不能太高。有足够的液相上升速度,目的是防!卜煤粉颗粒的沉降。保证足够的传质速率,需要有足够和均匀的气含率及气、液湍流程度。有合理的反应热移出手段,这样可以灵敏地控制反应温度,防!卜反应器飞温。在煤液化反应器的操作过程中,经常出现如下问题:①飞温,当反应器温度控制不好时,反应器内温度就会急剧上升,失去控制,这就是飞温现象,应当尽量避免该现象的发生;②固体颗粒沉积,当反应器内液相上升速度低时,就会产生煤粉及无机颗粒的沉积,沉积不仅能导致反应器内部物料的堵塞,还会因局部反应剧烈而产生飞温现象;③结焦,当反应器内液体流动有死区、煤浆溅上气体空腔壁或飞温超过470C时缩聚反应成为主要反应时,反应器内就会产生结焦,结焦严重时会导致反应器正常操作无法进行[2]。为了尽量减少以上异常情况的发生,除严格遵守操作规程外,增加反应器的操作弹性也是很有必要的。为了尽量减少以上异常情况的发生,除严格遵守操作规程外,增加反应器的操作弹性也是很有必要的。煤直接液化反应器的类型自从1913年德国的Bergius发明煤直接液化技术以来,德国、美国、日本、前苏联等国家已经相继开发了几十种煤液化工艺,所采用的反应器的结构也各不一样。总的来说,迄今为止,经过中试和小规模工业化的反应器主要有 3种类型:鼓泡床反应器,悬浮床反应器,环流反应器。
441鼓泡床反应器气液鼓泡床反应器以其良好的传热、传质、相间充分接触与高效率的可连续操作特性,而广泛应用于有机化工、煤化工、生物化工、环境工程等生产过程 ⑸。鼓泡床反应器结构简单,其外形为细长的圆筒,其长径比一般为 18〜3Q里面除必要的管道进出口外,无其他多余的构件。为达到足够的停留时间,同时有利于物料的混合和反应器的制造,通常用几个反应器串联。氢气和煤浆从反应器底部进入,反应后的物料从上部排出。由于反应器内物料的流动形式为平推流(即活塞流),理论上完全排除了返混现象,实际应用中大直径的鼓泡床反应器液相有轻微的返混, 因此也有称该种反应器为活塞流反应器的管道进出口外,无其他多余的构件。为达到足够的停留时间,同时有利于物料的混合和反应器的制造,通常用几个反应器串联。氢气和煤浆从反应器底部进入,反应后的物料从上部排出。由于反应器内物料的流动形式为平推流(即活塞流),理论上完全排除了返混现象,实际应用中大直径的鼓泡床反应器液相有轻微的返混,因此也有称该种反应器为活塞流反应器⑹。日本液化工艺和德国液化工德国在二战前的工艺(IG)和新工艺(IGOR)、日本的艺鼓泡床反应器是典型的液化鼓泡床反应器,其结构如图 德国在二战前的工艺(IG)和新工艺(IGOR)、日本的NEDOL工艺、美国的SRC和相对而言它是3种反应器中相对而言它是3种反应器中最为成熟的一种日本新能源开发机构组织了10家公司合作,开发了NEDO液化工艺,在日本鹿日本新能源开发机构组织了岛建成了150t/<1d成了1个印尼煤种和1个日本煤种的连续运行试验。NEDOIX艺反应器底部为半球形,由于长期运转后,反应器底部有大颗粒的沉积现象,因此反应器底部设有定期排渣口,定期排除沉积物。德国IG公司二战前通过工业试验发现,用某些褐煤做液化试验时,第一反应器运行几个星期后,反应器就会因为堵塞而停下来,里面积聚了大量的2〜4mm勺固体。经过分析,发现固体主要是矿物质,而没有新鲜煤,后来他们在反应器的圆锥底部进料口的旁边安装了排渣口,才解决了堵塞问题。另外他们也发现,鼓泡床反应器内影响流体流动的内构件,特别是其形状易截留固体的构件越少,反应器操作就越平稳。因此,工业化鼓泡床反应器实际上是空筒。德国煤炭研究公司于1981年在鲁尔区建成200t/d的中试装置。试验从1981年开始至1987年初结束,加煤运转时间21700h,平均可达4000h/a以上,对反应器的研究取得了重大突破。强制循环悬浮床反应器该种反应器因内部有循环杯,并带有循环泵,因此称为强制循环悬浮床反应器。应用该种反应器的煤液化工艺主要有美国的 H-Coal工艺、HTI液化工艺、中国神华煤液化工艺等[10]。因H-Coal工艺反应器内催化剂呈沸腾状态,因此也称之为沸腾床反应器。H-Coal工艺反应器结构如图3所示,中国神华煤液化工艺反应器结构如图4所示。美国HRI公司借用H-Oil重油加氢反应器的经验将其用于H-Coal煤液化工艺,使用Co/Mo催化剂,只要催化剂不粉化,就呈沸腾状态保持在床层内,不会随煤浆流出,解决了煤炭液化过去只能用一次性铁催化剂,不能用高活性催化剂的难题。为了保证固体颗粒处于流化状态,底部可用机械搅拌或循环泵协助。另外,为保证催化剂的数量和质量,一方面要排出部分催化剂再生,另一方面要补充一定量的新催化剂[10]。HRI公司采用图3所示的强制悬浮床反应器建立了220t/d的中试装置,反应器直径1.5m,高约10m该装置第一次投煤试验是1980年5月,用的是Kentucky11号煤,由于其他设备出了故障,只运行19h便停了下来。经过改造后该装置于1981年和1982年间又进行了几次试验,采用的煤种是Illinois6号煤,最长运行时间是132天,成效显著[11]。中试反应器的试验条件为:工艺条件。温度450C,压力16〜19MPa循环油:煤为1.5〜2.0物料空速0.5〜2kg/(kg.h)。反应器内物料性质。煤浆中含煤质量分数 9%〜22%;煤浆流速为(2.1〜5.5)3310mW/A气体流速为((1.2〜4.9) 10m人物料的密度为0.6〜0.7g/<m;;物2料的黏度为(0.2 〜0.5) 10g/(cm•s)。在中试试验的同时,HRI公司与Bechtel工程公司等合作进行了2500t/d工业示范装置的设计。我国神华集团借鉴美国HTI液化工艺反应器,开发了神华煤液化反应器,也有人称这种反应器为外循环全返混反应器。采用循环泵外循环方式增加循环比,以保证在一定的反应器容积下,达到一个满意的生产能力和液化效果。该种反应器采用北京煤炭科学研究总院开发的“863”高效催化剂,催化剂与煤浆一起从反应器底部加入,然后和反应后的物料一起从反应器上部排出。神华集团采用该反应器于2004年在上海建立6t/d规模的液化中试装置,反应器为2个串联。该装置进行了4次投煤运转试验,累计投煤时间为4375h消耗原煤量1319.61t在反应器的稳定运转与优化操作方面取得了丰富的经验。神华集团在内蒙古建设的煤直接液化工业示范装置采用的该种反应器,规模达到了6000t/d。2个反应器的直径均为4.34m,高度分别为41和43m该种反应器生产能力大,气体滞留少,不容易形成大颗粒沉积物,不足的是尚未经过长周期运行的证实[1]。环流反应器环流反应器是在鼓泡床反应器的基础上发展起来的一种高效多相反应器,具有结构简单、传质性能好、易于工程放大的特点,在化学工程和其他相关领域中有广泛的应用[12]。环流反应器型式多样,种类繁多,其中气升式内环流反应器是常用的一种。这种反应器利用进料气体在液体中的相对上升运动,产生对液体的曳力,使液体也向上运动,或者说利用导流筒内外的气含率不同而引起的压强差,使液体产生循环运动[13]。气升式内环流有2种类型,中心进料环流反应器结构如图5所示,环隙进料环流反应器结构如图6所示。是完全可行的。的煤液化装置进行改2007年12月,煤炭科学研究总院联合神华集团对6t/<d的煤液化装置进行改造,将2个串联的反应器中的第1个反应器改造成大概结构如图5所示的环流反应器,第2个反应器仍然是强制循环悬浮床反应器。在和2个反应器都是悬浮床相同的试验条件下进行了将近1个月的投煤试验,环流反应器试验结果与强制循环悬浮床反应器的试验结果对比见表2。表1环流与强制循环试验结果对比(干燥无灰基) [2]%第一反应器操作模式强制循环环流实际油收率(含CH4+49.0848.37水10.8311.65GC36.676.96COx2.572.08H2S0.150.17气产率9.399.21H2耗4.214.26转化率85.1987.95从表1可看出环流反应器煤转化率略高一些,但油收率略低于强制循环反应器,而总的来说差别不大。试验从工业实践上证明了环流反应器应用于煤炭直接液化体系的可行性,但在放大设计、优化设计及理论研究方而仍需要做进一步的深入研究。444种煤液化反应器的比较鼓泡床反应器内部构件少,气含率高,有足够的气液传质速度,而目—比较成熟,风险小。缺点主要有2个:①液相速度偏低,接近或低于颗粒沉降速度,使反应器内固体浓度较高,长时间运转会出现固体沉降问题,需要定期排渣 ;②由于流体动力的限制,生产规模不能太大,一般认为,最大处理量为 2500t/d。强制循环悬浮床反应器优点是液相速度高,克服了颗粒沉降问题。气含率低于鼓泡床,达到比较适中的数值,既保证了传质速度,又增加了液相停留时间。另外,由于有大量高温循环物料与新鲜进料的混合,使反应热可以通过降低进料温度的办法移出。该反应器的缺点是必须配备能在高温高压条件下运行的循环泵,以及反应器顶部必须有提供气液分离的空间及构件。这就不仅使反应器内部构件复杂化,而目 _反应器的气液比不能过高,否则气液分离不完全,易引起循环泵抽空等一系列问题。环流反应器的主要优点是反应器内流体定向流动,环流液速较快,实现了全返混模式,而目_不会发生固体颗粒的沉积;气体在其停留时间内所通过的路径长,气体分布更均匀,单位反应器体积的气泡比表面积大,因此相间接触好,传质系数也较大。与强制循环悬浮床反应器比,省去了循环泵和复杂的内构件,减少了操作费用和因循环泵故障而引起的运转风险。因此环流反应器在煤液化领域具有广泛的应用前景,应得到足够的重视。以上3种反应器虽有一些区别,但本质上有许多共同点,如化学反应过程相同,浆体都处于流动状态,温度、压力和停留时间等也十分接近,主要区别是返混程度不同和循环比不同,有的单靠高压泵和氢气的推动,有的除此外还需要借助循环泵或导流筒。第五章煤炭液化产品的处理煤炭直接液化工艺所生产的液化粗油, 保留了液化原料煤的一些性质特点,芳烃含量高,氮、氧杂原子含量高,色相与储藏稳定性差等,如要得到与石油制品一样的品质,必须要进行提质加工。但是,由于液化油的性质与石油有很大的差异,因此液化油的提质加工与石油相比,需要更苛刻的提质加工条件,也需要开发针对液化油特性的催化剂和加工工艺。表5-1为液化油汽油馏分与石油汽油馏分性质的比较,表5-2为液化油柴油馏分与石油柴油馏分性质的比较。表5-1液化油汽油馏分与石油汽油馏分性质的比较项目液化油石油GBO/%质量分数)2.20<1504S/10(质量分数)5603006N/10(质量分数)300010胶质/(哑/100ml)1500<5辛烷值(RON5665〜70>90表5-2液化油柴油馏分与石油柴油馏分性质的比较项目液化油石油GBO/%质量分数)1.30<5004S/10(质量分数)100130006N/10(质量分数)650040>45十六烷值14565.1煤液化粗油的性质表5-1-1为中国的依兰煤在NEDO工艺上的液化油性质表。表5-1-1NEDOL依兰煤液化油性质
项目馏分分析/C相对密度40C元素分析/%(质量分数)IBP10%50%70%90%EPCHN1 O) S轻质石51741391631791900.78582.4212.870.524.130.06重质石1992042062082122490.91884.8510.010.774.340.03常压轻2162252262282312460.91786.5610.460.852.110.02常压重2552662883143713800.96688.849.780.700.650.03从以上表格可以看出,对煤液化粗油的性质作一准确的描述是比较困难的,但可以概括出一些特性。煤液化粗油的杂原子含量非常高。氮含量范围为0.2%〜2.0%,典型的氮含量在0.9%〜1.1%(质量分数)的范围内,是石油氮含量的数倍至数十倍,杂原子氮可能以咔唑、氮杂菲、和氮杂萤蕙的形式存在。硫含量范围从0.05%〜2.5%,不过一般为0.3%〜0.7%(质量分数),低于石油的平均硫含量,大部分以苯并噻吩和二苯并噻吩衍生物的形态存在。煤液化粗油中的氧含量范围可以从 1.5%(质量分数)一直到7%质量分数)以上,具体取决于煤种和液化工艺,一般在 4%-5%质量分数)。有在线加氢或离线加氢的液化工艺,由于液化粗油经过了一次加氢精制,液化粗油中的杂原子含量大为降低。煤液化粗油中的灰含量取决于固液分离方法,采用旋流分离、离心分离、溶剂萃取沉降分离的液化粗油中含有灰,这些灰在采用催化剂的提质加工过程中,会引起严重的问题。采用减压蒸馏进行固液分离的液化粗油中不含灰。液化粗油中的金属元素种类与含量与煤种和液化催化剂有很大关系,一般含有铁、钛、硅和铝。煤液化粗油的馏分分布与煤种和液化工艺关系很大,一般分为轻油 (又可分为轻石脑油:初溜点〜82C和重石脑油82〜180C,占液化粗油的15%-30%(质量分数)、中油(180〜350E,占50%〜60%质量分数)、重油(350〜500E或540E),占10%〜20%(质量分数)。煤液化粗油中的烃类化合物的组成广泛,含有60%〜70%(质量分数)的芳香族化合物,通常含有1〜6环,有较多的氢化芳香烃。饱和烃含量约25%(质量分数),一般不超过4个碳的长度。另外还有10%(质量分数)左右的烯烃。煤液化粗油中的沥青烯含量,对液化粗油的化学和物理性质有显著的影响。沥青烯的分子量范围为300〜1000,含量与液化工艺有很大关系,如溶剂萃取工艺的液化粗油中的沥青烯含量高达25%(质垦分数)。5.2液化粗油提质加工液化粗油是一种十分复杂的烃类化合物混合体系。液化粗油的复杂性在对其进行提质加工生产各种产品时带来许多间题,往往不能简单地采用石油加工的方法,需要针对液化粗油的性质,专门研究开发适合液化粗油性质的工艺,包括催化剂。液化粗油的提质加工一般以生产汽油、柴油和化工产品(主要为BTX)为目的。目前液化粗油提质加工的研究,大部分都停留在实验室的研究水平,采用石油系的催化剂。煤液化石脑油馏分的加工煤液化石脑油馏分约占煤液化油的15%〜30%,有较高的芳烃潜含量,链烷烃仅占20流右,是生产汽油和芳烃(BTX)的合适原料。但煤液化石脑油馏分含有较多的杂原子(尤其是氮原子),必须经过十分苛刻的加氢才能脱除,加氢后的石脑油馏分经过较缓和的重整即可得到高辛烷值汽油和丰富的芳烃原料。表5-2-1为几种液化工艺的石脑油馏分加氢和重整结果。采用石油系Ni-Mo、Co-Mo、Ni-W型催化剂和比石油加氢苛刻得多的条件下,可6以将煤液化石脑油馏分中的氮含量降至106以下,但带来的严重问题是催化剂的寿命和反应器的结焦间题。由于煤液化石脑油馏分中氮含量高,有些煤液化石脑油馏分中6氮含量高达5000〜800010,研究开发耐高氮加氢催化剂是十分必要的,另外对煤液化石脑油馏分脱酚和在加氢反应器前增加装有特殊形状填料的保护段来延长催化剂寿命也是有效的方法。煤液化重油的加工煤液化重油馏分的产率与液化工艺有很大关系,一般占液化粗油的 10%〜20%。写(质量分数),有的液化工艺这部分馏分很少。煤液化重油馏分由于杂原子、沥青烯含量较高,加工较为困难。研究的一般加工路线是与中油馏分混合共同作为加氢裂化的原料和与中油馏分混合作为FCO®料。除此以外,主要用途只能作为锅炉燃料。煤液化中油和重油混合经加氢裂化可以制取汽油。加氢裂化催化剂对原料中的杂原子含量及金属盐含量较为敏感。因此,在加氢裂化前必须进行深度加氢来除去这些催化剂的敏感物。煤液化中油和重油混合加氢裂化采用的工艺路线为2个加氢系统:第一个系统为原料的预加氢脱杂原子和金属元素,反应条件较为缓和,催化剂为UOP-DC郦二个加氢系统为加氢裂化,采用2个反应器串联,进行深度加氢裂化,裂化产物中>190C的馏分油在第二个加氢系统中循环,最终产物全部为<1900的汽油。表5-3-1为预加氢和加氢裂化的条件和结果。煤液化中油和重油混合后采用催化裂化(FCC)的方法也可制取汽油。美国在研究煤液化中油馏分的催化裂化时发现:煤液化中油和液化重油混合物作为FCC原料,在工艺上要实现与石油原料一样的积炭率,必须要对液化原料进行预加氢,要求 FCC原料中的氢含量必须高于11%(质量分数)。这样,对煤液化中油和液化重油混合物的加氢成为必不可少,而且要有一定的深度,即使这样,煤液化中油和液化重油混合物的催化裂化的汽油收率还只有50%(体积分数)以下,低于石油重油催化裂化的汽油收率70%(体积分数)。5.3液化粗油提质加工工艺液化粗油提质加工的研究工作除日本以外,目前大部分停留在实验室的研究阶段,距工业化应用还有一定距离。日本的液化粗油提质加工工艺日本政府从1973年开始实施阳光计划,开始煤炭直接液化技术的系统研究开发。在新能源产业技术综合开发机构(NEDO的主持下,成功开发了烟煤液化工艺(NEDOL工艺,150t/dPP装置规模)和褐煤液化工艺(BCL工艺,50t/dPP装置规模),同时把液化粗油的提质加工工艺研究列人计划。1990年在完成了实验室基础研究的同时,开始设计建设50桶/d规模的液化粗油提质加工中试装置。目前该装置已在日本的秋田县建成,以烟煤液化工艺(NEDQL工艺,150t/dPP装置规模)和褐煤液化工艺(BCL工艺,50t/dPP装置规模)的液化粗油为原料,正在进行液化粗油提质加工的运转研究,预计2002年3月研究结束。日本液化粗油提质加工工艺流程描述。日本液化粗油提质加工工艺流程由液化粗油全馏分一次加氢部分、一次加氢油中煤、柴油馏分的二次加氢部分、一次加氢油中石脑油馏分的二次加氢部分、二次加氢石脑油馏分的催化重整部分等4个部分构成。在一次加氢部分,将全馏分液化粗油,通过加料泵升压, _与以氢气为主的循环气体混合,在加热炉内预热后,送人一次加氢反应器。一次加氢反应器为固定床反应器,采用Ni/W系催化剂进行加氢反应。加氢后的液化粗油经气液分离后,
温馨提示
- 1. 本站所有资源如无特殊说明,都需要本地电脑安装OFFICE2007和PDF阅读器。图纸软件为CAD,CAXA,PROE,UG,SolidWorks等.压缩文件请下载最新的WinRAR软件解压。
- 2. 本站的文档不包含任何第三方提供的附件图纸等,如果需要附件,请联系上传者。文件的所有权益归上传用户所有。
- 3. 本站RAR压缩包中若带图纸,网页内容里面会有图纸预览,若没有图纸预览就没有图纸。
- 4. 未经权益所有人同意不得将文件中的内容挪作商业或盈利用途。
- 5. 人人文库网仅提供信息存储空间,仅对用户上传内容的表现方式做保护处理,对用户上传分享的文档内容本身不做任何修改或编辑,并不能对任何下载内容负责。
- 6. 下载文件中如有侵权或不适当内容,请与我们联系,我们立即纠正。
- 7. 本站不保证下载资源的准确性、安全性和完整性, 同时也不承担用户因使用这些下载资源对自己和他人造成任何形式的伤害或损失。
最新文档
- 高中生社会实践与志愿服务计划
- 山西省晋中市太谷区2023-2024学年九年级上学期期末化学试卷
- 九年级班主任工作总结报告
- 浙江省宁波市奉化区2023-2024学年六年级上学期英语期末试卷
- 互联网行业业务代表工作报告
- 2023年贵州省黔东南自治州公开招聘警务辅助人员辅警笔试自考题1卷含答案
- 2021年山东省淄博市公开招聘警务辅助人员辅警笔试自考题1卷含答案
- 2024年内蒙古自治区包头市公开招聘警务辅助人员辅警笔试自考题1卷含答案
- 2022年河南省许昌市公开招聘警务辅助人员辅警笔试自考题1卷含答案
- 2024年河南省洛阳市公开招聘警务辅助人员辅警笔试自考题1卷含答案
- 部编版六年级语文下册第三单元大单元教学设计
- 前端组长述职报告
- 食品安全企业标准模板
- 钴酸锂结构特性
- 台州造船行业产值分析
- 2024年度医院儿童保健科医务人员述职报告课件
- 品牌部工作总结汇报
- 全麻病人苏醒期躁动的原因及处理课件
- 2024全新诚信考试课件
- 2024年大学生心理健康教育考试题库及答案(含各题型)
- 《全脑速读记忆讲座》课件
评论
0/150
提交评论