


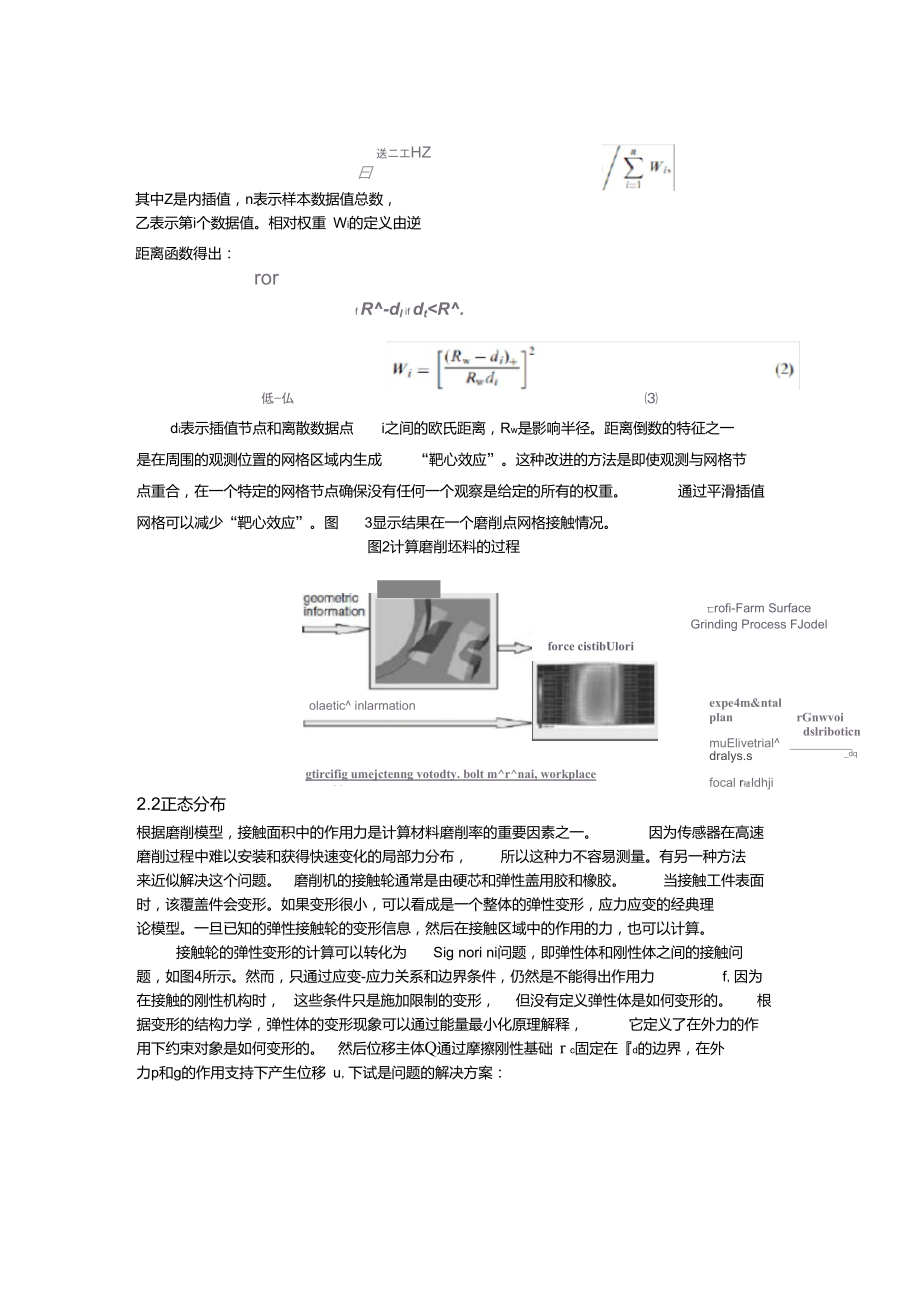

版权说明:本文档由用户提供并上传,收益归属内容提供方,若内容存在侵权,请进行举报或认领
文档简介
1、机器人砂带磨削仿真的局部过程模型摘要通过一个局部模型来估计在机器人砂带磨削的过程中的材料磨削率模拟系统。通过将工件的局部几何信息参数相结合,而非利用工件的切削深度,从而计算出所受作用力的大小, 并将其作为一个整体的磨削模型。在稳定的切削条件下, 即使是非均匀接触,仿真精度的误差也能控制在5%以下。1.简介利用砂带磨削作为一种精加工工艺,可以实现很高的材料磨削率,使加工工件获得良好的表面质量。它是一项效率很高的工作,尤其是因为它同时也改善了工作的控制力,所以不需要额外的预处理和善后工作。通过整合多自由度的工业机器人作为机械臂,可以形成柔性制造单元,它特别适合于加工表面的几何形状比较复杂的工件,如
2、涡轮叶片或水龙头。砂带磨削过程的典型情况如图1所示。在旋转的接触轮上, 磨轮与工件表面进行接触,对工件表面进行材料磨削。但对于机器人程序员来说,能够正确定义自由曲面工件的磨削路径仍然是一项 难度系数较高的工作。这篇文章主要描述了一个磨削模型,能够有助于程序员提高工作效率,模拟磨削过程和预测其结果。图1砂带磨削过程1.1相关工作由于其复杂性和非线性,如今砂带磨削工艺的优化在行业中仍然是一个最具挑战性的问题。磨削槽通常使用一个弹性接触轮来支撑皮带作为切削刃。与其他磨削加工一样,磨削完成后的表面具有许多参数,包括磨削参数和磨削带的表面形状特征。前者的主要参数包括皮带速度、进给速度、工件的几何形状和带
3、预紧力,后者包括的信息如粒度,粒距,磨损率等。在过去的几年中,已经采取过很多方法来提高磨削加工的质量。最常用的方法是使用磨削模型来进行模拟输出从而进行优化,也叫作基于模型的优化。 通常有三种主要建模技术用于估计磨削速度。第一种方法是考虑工件和一个单一晶粒之间的相互作用。磨削的最终结果如表面质量和材料磨削率,可以通过模拟预测。它已经应用到最近生产的表面磨削工具。通过对磨削过程中的活动磨粒及其攻角进行识别,实现了磨削过程的运动学仿真2-5。第二种方法是试图将所有的磨削过程中的结果数据建立出一个数学关系。进行大量的实验对其中各参数的影响进行研究,然后通过统计分析相关模型6。最后一种方法研究了另一个方
4、面,如磨粒特征强度、晶粒尺寸的影响,几何特性和热分析,然后将它们整合成一个整体的模型【7同时纳入一些智能算法以建立更广义的模型8。由于自粘结磨料的研究是相当复杂的,故而第一种方法很难适用于实际生产。更为合理的方法是把第二、第三种方法的优点结合起来。首先研究磨削过程对工件的影响,然后依次进行一系列的实验。得出这些因素之间的复杂关系,以及它们对结果的影响,同时也可以使用现代统计方法从实验结果中得出结论9。1.2研究目的大多数研究的模型都把加工表面看作是一个整体,在局部视图中不考虑接触状态。对每一个参数进行研究,在磨削模型中定量一个值,例如整体的力,整体的磨削率等,因此,这 些模型被称为整体磨削模型
5、,适用于加工简单形状的工件表面同时也有助于定性研究粉磨工 艺。但对于自由曲面磨削,粗糙的整体关系已难以满足需要。本文提出了局部模型的概念, 研究工件的局部几何信息及其对最终磨削的影响。通过将此模型集成到一个仿真系统中,机器人程序员可以输出一个模拟优化路径。2.局部过程模型磨削仿真系统是从工件的原料增量减去材料,但是它不能像车削或铳削加工过程那样,在刀具和工件之间使用布尔集合运算。相反,计算应根据经验过程模型。由于存在不确定的切削刃和大量的影响参数,所以这些磨削变量之间的关系应当在经验的基础上得出结论。自由曲面的磨削加工涉及到多个工艺变量,可以同时影响加工表面的材料磨削率、形状和表面粗糙度。在这
6、种一个复杂的情况中,由Hama nn6给出的线性整体磨削模型已经不适用了。特别是必须考虑在接触区域的局部非均匀力分布,其他制造参数的影响也需要进行研究。因此,应研究局部磨削过程模型, 从而更准确地近似磨削。 它可以分为三个步骤:接触情况的确定, 力分布计算和磨削计算。第一步描述了磨削带和工件之间的几何求交,这将用于获得在第二阶段的接触面积上的压力。然后运用其他参数来获得最终的磨削结果。整个过程如图2所示。2.1接触情况实验证明磨削率不仅取决于磨削参数,同时也受工件形状的影响。该磨床的动态特性主要取决于工件和零件之间的接触情况(各种支持和磨削带)。因此有必要进行详细的接触建模。磨削接触需要特殊的
7、处理,因为它从工件的坯料进行磨削,改变了原来的几何形状。因此,在磨削率计算的第一步,需要建立数据关联。通常用一个所谓的高度模型来描述其与工 件的磨削点在接触轮的切线曲面,然后将这个接触转移到一个有限元模型(有限元法)来计算力的分布。为适应有限元法的要求,必须建立一种基于高度模型的规则网格网格。在这项工作的应用处理中,工件由离散点表示和相关的正常,是一种形状模型适用于自由曲面加工的仿真技术13。由于工件的位置和方向被固定在预先规划的路径的每个接触点 上,被选择作为接触点的切平面作为“X-Y ”平面,工件的所有此平面内的点都要接触到接触轮。由于XYZ数据是随机分布在区域中的,并且许多“窗口”分布在
8、数据点中,规则网 格有限元就变成了一个表面网格化的过程。modified Shepard ' s method网,是根据经典的反距离力加权法加以改进,采用插值网格点加权。用谢巴德的方法令数据点进行插值,使一个数据点的影响从插值点相对于另一个点下降的距离。该算法如下:送二工HZ曰其中Z是内插值,n表示样本数据值总数, 乙表示第i个数据值。相对权重 Wi的定义由逆距离函数得出:rorf R-dl if dt<R.低仏di表示插值节点和离散数据点i之间的欧氏距离,Rw是影响半径。距离倒数的特征之一是在周围的观测位置的网格区域内生成“靶心效应”。这种改进的方法是即使观测与网格节点重合,在
9、一个特定的网格节点确保没有任何一个观察是给定的所有的权重。通过平滑插值网格可以减少“靶心效应”。图3显示结果在一个磨削点网格接触情况。con actolaetic inlarmationforce cistibUlorigtircifig umejctenng votodty. bolt mrnai, workplace tna何tai.匸rofi-Farm SurfaceGrinding Process FJodelexpe4m&ntalplanrGnwvoidslriboticnmuElivetrial dralys.s_dqfocal r破Idhji图2计算磨削坯料的过程2.2正
10、态分布根据磨削模型,接触面积中的作用力是计算材料磨削率的重要因素之一。因为传感器在高速磨削过程中难以安装和获得快速变化的局部力分布,所以这种力不容易测量。有另一种方法来近似解决这个问题。磨削机的接触轮通常是由硬芯和弹性盖用胶和橡胶。当接触工件表面时,该覆盖件会变形。如果变形很小,可以看成是一个整体的弹性变形,应力应变的经典理 论模型。一旦已知的弹性接触轮的变形信息,然后在接触区域中的作用的力,也可以计算。接触轮的弹性变形的计算可以转化为Sig nori ni问题,即弹性体和刚性体之间的接触问题,如图4所示。然而,只通过应变-应力关系和边界条件,仍然是不能得出作用力f,因为在接触的刚性机构时,这
11、些条件只是施加限制的变形,但没有定义弹性体是如何变形的。根据变形的结构力学,弹性体的变形现象可以通过能量最小化原理解释,它定义了在外力的作用下约束对象是如何变形的。然后位移主体Q通过摩擦刚性基础 r c固定在d的边界,在外力p和g的作用支持下产生位移 u,下试是问题的解决方案:EEV GlJpnQ图3接触点插值:(a)区域的随机分布点(b)网络状后的规则网格图 4 Sig nori ni 问题Blum15,16和Suttmeier17制定了一个有限元模型来解决这个Signorini接触问题。工件表面被假定为刚性体而不变形,接触轮是弹性体,只有弹性变形。有限元模型采用了优化的网格离散化策略,提高
12、了网格的效率和精度。然而,它仍然是非常繁重的计算,因为为了确保计算精度,一个足够小的网格单元是必须的。根据Zhang18研究出的新的模型,发现利用支持向量回归方法作为学习记录机,用以加快计算。在这个模型中,较耗时的阶段是在准备阶段, 而不是在运行阶段。图5( c)举例给出了接触情况对应力的分布。可以看出,在接触面积的边缘压力要高得多。图5 一种接触点的磨削计算(a)磨削路径中的接触点 (b)接触点的接触情况 (c)从接触情况计算出的力分布(d)在接触区域的最终去除率2.3磨削计算在对接触点局部受力进行计算后,应结合其它工艺参数对结果的影响进行分析。Hama nn曾制定了一个整体的关系式:其中,
13、r是芯片的平均磨削率;Ca是磨削过程的一个修正常数;Ka是工件和磨削能力因子的结合常数;kt是砂带磨损因数;V、Vw、Lw和Fa分别是磨削率,进给速度,磨削宽度和正常作用力。该模型是一个线性模型,总磨削率与影响参数成反比。它也可以应用到非线 性的模型,但仍然要把磨削过程作为一个整体且单值的过程。然而,因为两个原因,整体的关系对于自由曲面磨削是不足的。首先,要确定是整体磨削还是局部磨削(在每个小的区域的磨削);其次,由于工件的几何形状复杂,局部磨削不 均匀的分布在整个接触区。要获得详细信息,磨削区首先需要划分成网格,然后需要定义每 个网格点的局部参数。例如,局部力可以表示为在接触区域网格点的接触
14、力,局部磨削可以近似于矩阵中的每个元素都表示为被磨削的一个网格点。在本文中,局部磨削的情况也被称为 distribution 。局部磨削模型并不是简单地把力或磨削量作为单一的量,而是利用一种值模式呈现整个接触区域的局部情况。由cabaravdic 9的归纳的局部模型,可以表示为i6j其中,njm和n是离散的接触区域在 2个方向上的网格大小。在这个模型中,力Fa或磨削率r不再是一个单值的参数,而是一个矩阵,表示在整个接触面积上的离散信息。模型的系数是通过实验的统计设计所确定的,在这种情况下,由两个阶段所组成:筛选阶段和建模阶段。在筛选阶段,采用 Plackett-Burman试验计划19,通过最
15、少数量的单个实验来发现对输出变量没 有显著影响的因数。 在建模阶段,需要建立重要因素和输出变量之间的关系。对一个输入变量和输出变量的对数值之间的线性关系进行假设,并在数学回归的帮助下,估计输入变量的系数。与Hamann模型相比,由于在加工过程中消除了磨削宽度的参数,工件与磨削带之间 的接触范围发生变化。但它比整体的磨削模型包含更多的分布信息,适用于自由曲面的磨削。在一个磨削点上的这些步骤如图5所示。3仿真与实验基于工件几何形状的离线机器人编程软件,可以设计出磨削路径。但要测试结果表面质量,必须进行样品实验。 如果输出不符合预期,则程序员需要做一些修改和测试程序。这是一个非常耗时且耗资的过程,这
16、项实验的目的是消除这个过程,并用现代计算技术的虚拟验证取代它。在屏幕上显示磨削过程,并使用三维误差评估得出最终表面质量。此方法在任何意外情况发生之后,仍能够显示最终结果。此时,无需考虑实时力控制的过程;同时通过离线修改轨迹,这种方法还用于提高过程力。3.1砂带磨削仿真对工件进行磨削通常是由 b_rep和由一些样条曲面来表示。为了正常表现出生成点,它需要使用20中提出的技术。采样密度与有限元网格的分辨率有关,这是由用户指定的精度决定 的。在仿真过程中,首先在每个接触点计算接触情况,这个域将被转移到有限元法计算作用正常力,结果是以矩阵的形式得出。 然后将该过程模型结合其他影响因素,并计算在该网格域
17、的最终去除分布。对于那些不完全在网格点的点,使用双线性插值估计去除。基于过程模型的输出,通过改变设计表面逼近位移修正工件的几何形状。这些程序重新循环执行直到已计算所有的路径。指定路径中的每个接触点有2个属性:位置和方向。位置是机器人基坐标系中的笛卡尔坐标 Px,y,z。虽然不同类型的机器人有不同的方式来表示方向,但我们选择四元数Qw,x,y,z作为标准方法21。应用于各种机器人时,可能需要转换。为了保证逼近精 度,相邻接触点的距离应该足够小。定义表面离散化误差是w,量相邻刀具位置点之间的距离和是I,则接触点的最小数目n应该是n=l/w。这些点的位置可以线性插值,如图6的左图所示。关于旋转,这是
18、一个更复杂的问题。我们知道,所有的单位四元数能够映射到四维 空间中的球。线性插值(LERP )四元数的问题是它是插在两者之间的割线四元数而不是球 面距离。其导致内插的运动不具有平滑的速度:它可能会加快一些部分的速度。球面线性插值(SLERP),如图6的右图所示,通过插值沿弧形线代替正割线来解决这个问题。虽然高 阶插值可以达到 C2连续的插值,但能够以相对较低的计算成本得到期望的结果。对于Q1和Q2之间的第i个点,其插值结果为:M =你£- = (1 声卜 P1 + # sin(l - 1)6sinsin其中0 G图7磨削模型与误差评估:(a)磨削3点后的工件;(b)磨削完成的工件;(
19、c)磨削三点后的误差评估;(d)磨削完成后的误差评估3.2磨削误差评定模拟的一个目标是帮助机器人程序员估计最终的表面质量。所以对磨削误差是否有问题如gouge或undercut的情况是非常重要的。直到现在,机器人编程仍然是一个非常费力和耗时的工作。借助仿真和误差估算的帮助,程序员可以通过调整路径规划和优化磨削参数来提 高效率。磨削误差通常被描述为磨削表面与所期望的光滑表面之间的差异。所以这个验证过程通常是转换为表面近似点计算。如果最终的时间大于时间上限(假设容差范围切知),那么会发生undercut。否则,如果是在较低的范围,则导致gouge。所计算的时间只与曲面逼近点数(0(n)成比例。因为
20、只有一个接触点上的受影响的元件需要更新,所以本地化过程 已经限制了搜索区域。故而效率可以进一步提高。磨削误差评价的结果是通过不同颜色的深 浅来描绘磨削的深度。色相指数是根据所述误差内置安排和对于给定的磨削误差,选择相应的颜色来代表它。表1实殓数据的处理工件水揽头30 ill's砂帯类型:plOO进给至50 nun- *磨砂村料:SCG0,09in0.9良芾张力=0.5 N/mm;1.23E子檯块:i N. nun-力:1.96机器型号:JRB44O0例如在本实例中,中心暗区2的误差是相对于标称设计表面的公差范围内,而外部明亮区域3表示底切和内明亮区域 1表示如图gouge的量。如图7(
21、d)。实施评估的方法有: 在线评估和事后分析。在线磨削误差评定是对所设计的曲面与坯料的差进行计算,并对其进行动态显示,这种方法对观察者来说更为生动、即时,在对比分析中,分析了刀具路径的误差,显然更有效。3.3实验评价为了评估模拟系统,系列实验中都是使用卫浴产品生产商高仪公司的一个水龙头。待磨削工件由58个修补表面组成,并且在 x轴上延伸55毫米,在y轴上延伸80mm,在z轴上 延伸160毫米。它是由含有 68%的铜和32%的锌的黄铜制成的。磨削路径是由FAMOS、离线机器人编写。在表面上选择一些点,然后确定工件和接触轮之间的相对位置。虽然这种轨迹规划在很大程度上依赖于程序员的经验,但在工业中广
22、泛应用。 这些点形成磨削路径和后处理器将在预先设定的坐标系上生成相应的机器人程序。必须额外执行所生成程序的碰撞检测和奇点检测。实验中所用的工艺数据列于表1。CG, E1, E2和E3在2.3节提到。通常运营商会选择以下工业指南对车间进行优化。由于调查的重点是模拟和实际加工过程中,故而选取图5(1)中路径上的10个点,并在磨削之前和之后对正常位置进行测试,以获得最终的 材料磨削参数。对于每个点,加工是一个渐进的过程,因为邻点对它也有一些影响。所以最 终的磨削是围绕该点周围所有磨削作用的综合结果。表2第一列显示磨削后每一点的材料磨削。开始和结束点位于进给和收缩区域,量是相对的小的。在中间的路径,随
23、着磨削深度的增加,材料磨削率增加。但在7点,可以明显观察到过切。表2仿毎系魏的实瞪评价试验点实际磨模报磨除里(im)近似误差%)10.0196(悅33L5820.2020.38590595OJ220.50?56L2140.6S943150,S9J0.93S4.9261.0501.070L907IJ97I.4IS150KDM0.73214.089。币】90,721100J21Q.5302530在数值模拟过程中,工件表面离散成61K个点。在具有AMD 2600处理器和1GB内存的个人电脑中每个接触点平均用时0.25s。用户可以通过改变设计的曲面的逼近点集的密度来调整仿真速度。仿真结果显示在表2的第
24、二列。从仿真和实际加工结果的比较中,我们可以看到,在正常的磨削点,如点4, 5,6和7,模拟磨削过程误差在5%以下。过切点7也进行了准确得预测。但在那些进给量小的进料回收区,效果并不理想。有许多因素可能导致问题的发生。但主要原因是由于过程过渡状态的存在。上述模型的参数是在稳定工作条件下的实验,这意味着它可以在一个普通的磨削周期中近似的去除。然而,在进料和回缩相接触的有太多的不确定因素,从而导致不准确甚至失效。在这种情况下,需要进一步的研究来提高性能。4结论在这项工作中,使用局部砂带磨削过程模型估算材料去除率。当磨削条件稳定时,根据局部几何参数,能够估算非均匀接触面的近似磨削分布,且仿真误差控制
25、在5%以下。每个接触模型的平均计算时间约为0.25秒。基于此模型,能够构建一个有效的仿真系统,以创建磨削自由曲面的机器人程序。有了新的系统,程序员可以通过可视化的制造工艺、预测潜在的问题、测量尺寸误差的来完善路径规划。参考文献1 S.S. Law, S.M. Wu, Simulation study of the grin di ng process,Tra nsactio ns of the ASME (1973) 972 -978.2 E.J. Salisbury, K.V. Domala, K.S. Moo n, M.H. Miller, J.W.Sutherla nd, A three
26、-dime nsio nal model for the surface texture in surface grinding, part 1: surface gen eratio n model, Jour nal ofMa nufacturi ng Scie nee and En gi neeri ng 123 (4) (2001) 576 -581.3 E.J. Salisbury, K.V. Domala, K.S. Moo n, M.H. Miller, J.W.Sutherla nd, A three-dime nsio nal model for the surface te
27、xture in surface grinding, part 2: grinding wheel surface texture model,Journal of Ma nu facturi ng Scie nee and En gi neeri ng 123 (2001)582 -590.4 T.A. Nguyen, D.L. Butler, Simulation of precision grinding process,part 1: generation of the grinding wheel surface, Intern ati on alJo urnal of Machi
28、ne Tools & Manufacture 45 (11)(2005)1321 -328.5 T.A. Nguye n, D.L. Butler, Simulati on of precisi on grinding process,part 2: in teract ion of the abrasive grain with the workpiecenternatio nal Journal of Mach ine Tools & Manu facture 45 (11)(2005) 1329 -336.6 G. Hama nn, Modellieru ng des a
29、btragsverhalte ns elastischer robotergefuehrterschleifwerkzeuge, Ph.D. Thesis, Un iversity of Stuttgart,Stuttgart, 1998.7 H. Nasri, G. Bolmsjo, A process model for robotic disc grindin g,I ntern atio nal Jour nal ofMachi ne Tools & Manu facture 35 (1995)503-510.8 C.W. Lee, T. Choi, Y .C. Shin, I
30、ntelligent model-based optimizationof the surface grinding process for heat-treated 4140 steel alloys withalumi num oxide grinding wheels, Journal of Manu facturi ng Scienceand Engineering 125 (1) (2003) 65 -76.9 M. Cabaravdic, B. Kuhle nkoetter, Ban dschleifprozesse optimiere n,mo Metalloberfla che
31、 4 (2005) 44 -47.10 T. Van Hook, Real-time shaded NC milli ng display, i n: Proceedi ngsof the 13th Ann ual Conference on Computer Graphics andln teractive Tech niq ues, ACM Press, New York, 1986, pp. 15-20.11 T. Saito, T. Takahashi, NC machi ning with G-buffer method, i n:Proceedi ngs of the 18th A
32、nnual Conference on Computer Graphicsa nd In teractive Tech niq ues, ACM Press, New York, 1991,pp. 207-216.12 R.B. Jerard, S.Z. Hussa ini, R.L. Drysdale, B. Schaudt, Approximatemethods for simulati on and verificati on of nu merically con trolledmach ining programs, The Visual Computer 5 (1989) 329
33、-348.13 Y. Huang, J.H. Oliver, NC milli ng error assessme nt and tool pathcorrecti on, in: Proceedi ngs of the 21st Ann ual Conference on Computer Graphics and In teractive Tech niq ues, ACM Press, NewYork, 1994, pp. 287 -294.14 R. Fran ke, G. Nielso n, Smooth in terpolati on of large sets of scattereddata, Intern ati onalJournal for Numerical Methods in Engin eeri ng 15(1980) 1691-704.15 H.
温馨提示
- 1. 本站所有资源如无特殊说明,都需要本地电脑安装OFFICE2007和PDF阅读器。图纸软件为CAD,CAXA,PROE,UG,SolidWorks等.压缩文件请下载最新的WinRAR软件解压。
- 2. 本站的文档不包含任何第三方提供的附件图纸等,如果需要附件,请联系上传者。文件的所有权益归上传用户所有。
- 3. 本站RAR压缩包中若带图纸,网页内容里面会有图纸预览,若没有图纸预览就没有图纸。
- 4. 未经权益所有人同意不得将文件中的内容挪作商业或盈利用途。
- 5. 人人文库网仅提供信息存储空间,仅对用户上传内容的表现方式做保护处理,对用户上传分享的文档内容本身不做任何修改或编辑,并不能对任何下载内容负责。
- 6. 下载文件中如有侵权或不适当内容,请与我们联系,我们立即纠正。
- 7. 本站不保证下载资源的准确性、安全性和完整性, 同时也不承担用户因使用这些下载资源对自己和他人造成任何形式的伤害或损失。
最新文档
- GB/T 45680-2025起重机风载荷计算
- 儿童遗传性疾病诊断与护理
- 安全生产月培训总结3篇
- 小班儿歌打卡活动方案
- 小学美术节活动方案
- 小学美育书画活动方案
- 干部宣誓活动方案
- 干果折扣活动策划方案
- 带家属去公司活动方案
- 工友中秋慰问活动方案
- 2025至2030年中国月子中心行业竞争格局分析及市场前景趋势报告
- 2025年中国萤石行业市场全景调查研究报告
- 知不足而奋进 望远山而前行课件-2026届高三一轮复习总动员会
- 2025年山煤国际招聘笔试冲刺题(带答案解析)
- 2024-2025学年七年级英语下学期期末模拟试卷(外研版2024)
- 2024-2025学年初中英语七年级下册期末考试综合测试卷及参考答案
- 2024年凉山昭觉县委社会工作部选聘社区工作者真题
- 2023年全国二级建造师《矿业工程管理与实务》真题及详解
- 医院关键岗位管理制度
- 冠心病的规范化诊培训课件
- 未来中国检测市场发展趋势简析(精)
评论
0/150
提交评论