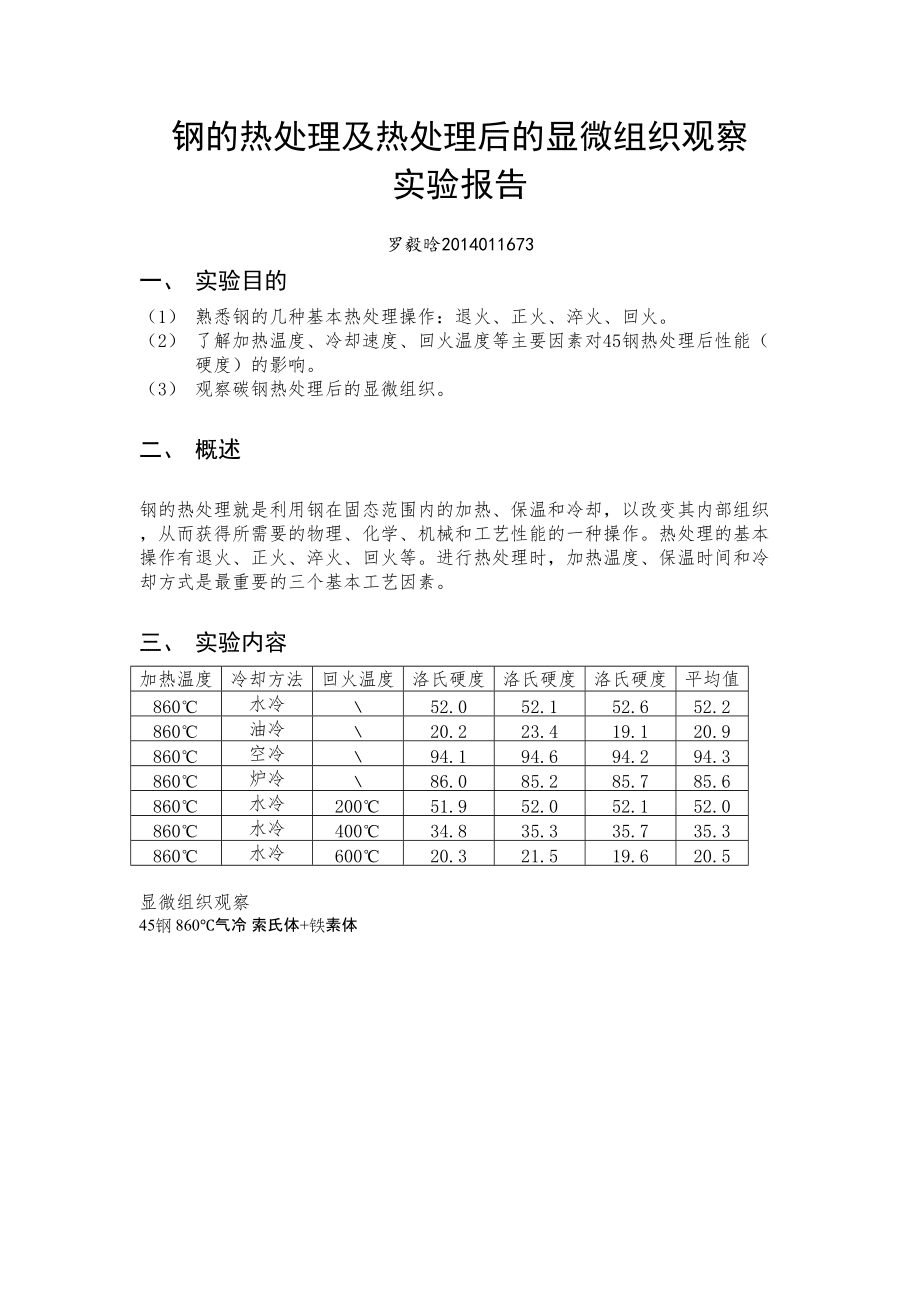




版权说明:本文档由用户提供并上传,收益归属内容提供方,若内容存在侵权,请进行举报或认领
文档简介
1、钢的热处理及热处理后的显微组织观察实验报告罗毅晗2014011673一、 实验目的(1) 熟悉钢的几种基本热处理操作:退火、正火、淬火、回火。(2) 了解加热温度、冷却速度、回火温度等主要因素对45钢热处理后性能(硬度)的影响。(3) 观察碳钢热处理后的显微组织。二、 概述 钢的热处理就是利用钢在固态范围内的加热、保温和冷却,以改变其内部组织,从而获得所需要的物理、化学、机械和工艺性能的一种操作。热处理的基本操作有退火、正火、淬火、回火等。进行热处理时,加热温度、保温时间和冷却方式是最重要的三个基本工艺因素。三、 实验内容加热温度冷却方法回火温度洛氏硬度洛氏硬度洛氏硬度平均值860水冷52.0
2、52.152.652.2860油冷20.223.419.120.9860空冷94.194.694.294.3860炉冷86.085.285.785.6860水冷20051.952.052.152.0860水冷40034.835.335.735.3860水冷60020.321.519.620.5显微组织观察45钢 860气冷 索氏体+铁素体45钢860油冷 马氏体+屈氏体45钢860水冷 马氏体45钢 860水冷+600回火 回火索氏体T12钢 760球化退火 球化体T12钢 780水冷+200回火 回火马氏体+二次渗碳体+残余奥氏体T12钢 1100水冷 粗大马氏体+残余奥氏体四、 实验分析1
3、.火温度而言,淬火温度越高,硬度越高。但是一旦达到过高温度会导致形成的马氏体,使得力学性能恶化。2.火介质而言,硬度大小:空冷炉冷水冷油冷。3.火温度而言,回火温度越高,硬度越低。图像:分析原因:据铁碳相图,淬火温度升高,45钢(亚共析钢)中铁素体含量减少,珠光体含量提高,而珠光体硬度很高,铁素体硬度低,导致硬度提高。根据C曲线,对亚共析钢的连续冷却,空冷生成F+S,炉冷生成F+P,水冷产生M,油冷产生T+M。因此,硬度大小为:空冷炉冷水冷油冷。高温回火生成回火索氏体,中温回火生成回火屈氏体,低温回火生成回火马氏体+残余奥氏体。硬度大小为:回火马氏体回火屈氏体回火索氏体。因此,回火温度越低,生
4、成产物硬度就越高。五、 思考题(1)45钢的热处理时850水淬+550回火,即淬火+高温回火(调质处理)。生成物是回火索氏体。45钢广泛用于制造齿轮、轴类件、连杆、螺栓等工件。(2)回火温度越高,硬度越低。因为高温回火生成回火索氏体,中温回火生成回火屈氏体,低温回火生成回火马氏体+残余奥氏体。硬度大小为:回火马氏体回火屈氏体回火索氏体。因此,回火温度越低,生成产物硬度就越高。(3)用金相法观察产物。若产物中观测到大量白色晶粒状的铁素体,则是淬火加热温度不足;若产物中观测到大块黑色晶团状的屈氏体,则是冷却速度不足。(4)45钢调制处理后生成回火索氏体,它是由粒状渗碳体和等轴形铁素体组成的混合物,在光学显微镜下观测到渗碳体小颗粒,它均匀地分布在铁素体中,性能方面,它具有良好的韧性和塑性,同时具有较高的强度,因此具有良好的综合力学性能。广泛用于制造汽车、拖拉机、机床和其他机器上的齿轮、轴类件、连杆、螺栓等工件。T12球化退火的产物是球化体,球化体指的是铁素体基体上分布着细小均匀的球状渗碳体。球化退火是使钢中碳化物球状化的热处理工艺。性能方面
温馨提示
- 1. 本站所有资源如无特殊说明,都需要本地电脑安装OFFICE2007和PDF阅读器。图纸软件为CAD,CAXA,PROE,UG,SolidWorks等.压缩文件请下载最新的WinRAR软件解压。
- 2. 本站的文档不包含任何第三方提供的附件图纸等,如果需要附件,请联系上传者。文件的所有权益归上传用户所有。
- 3. 本站RAR压缩包中若带图纸,网页内容里面会有图纸预览,若没有图纸预览就没有图纸。
- 4. 未经权益所有人同意不得将文件中的内容挪作商业或盈利用途。
- 5. 人人文库网仅提供信息存储空间,仅对用户上传内容的表现方式做保护处理,对用户上传分享的文档内容本身不做任何修改或编辑,并不能对任何下载内容负责。
- 6. 下载文件中如有侵权或不适当内容,请与我们联系,我们立即纠正。
- 7. 本站不保证下载资源的准确性、安全性和完整性, 同时也不承担用户因使用这些下载资源对自己和他人造成任何形式的伤害或损失。
最新文档
- 藏品征集品入库管理办法
- 融媒体办公用房管理办法
- 衡水市社区公章管理办法
- 医疗保障政策培训课件
- 装卸氧气乙炔瓶管理办法
- 西安市排污管道管理办法
- 规范公积金大厅管理办法
- 证监会强化监事管理办法
- 调机技术员考核管理办法
- 财政部呆账核销管理办法
- 公路养护统计培训
- 2024年成都农业科技中心招聘笔试真题
- 2025年陕西省中考英语试题卷(含答案)
- 2025年河南省中考语文试卷真题(含答案)
- 2025年6月22日四川省市直事业单位遴选笔试真题及答案解析
- 庆阳市陇东学院招聘事业编制笔试真题2024
- 心理学考试题及答案
- 护理领域的职业发展与前景展望
- 2025年天津高考数学试卷试题真题及答案详解(精校打印)
- 2025上海济光职业技术学院辅导员考试试题及答案
- 2024年江苏三支一扶真题
评论
0/150
提交评论