

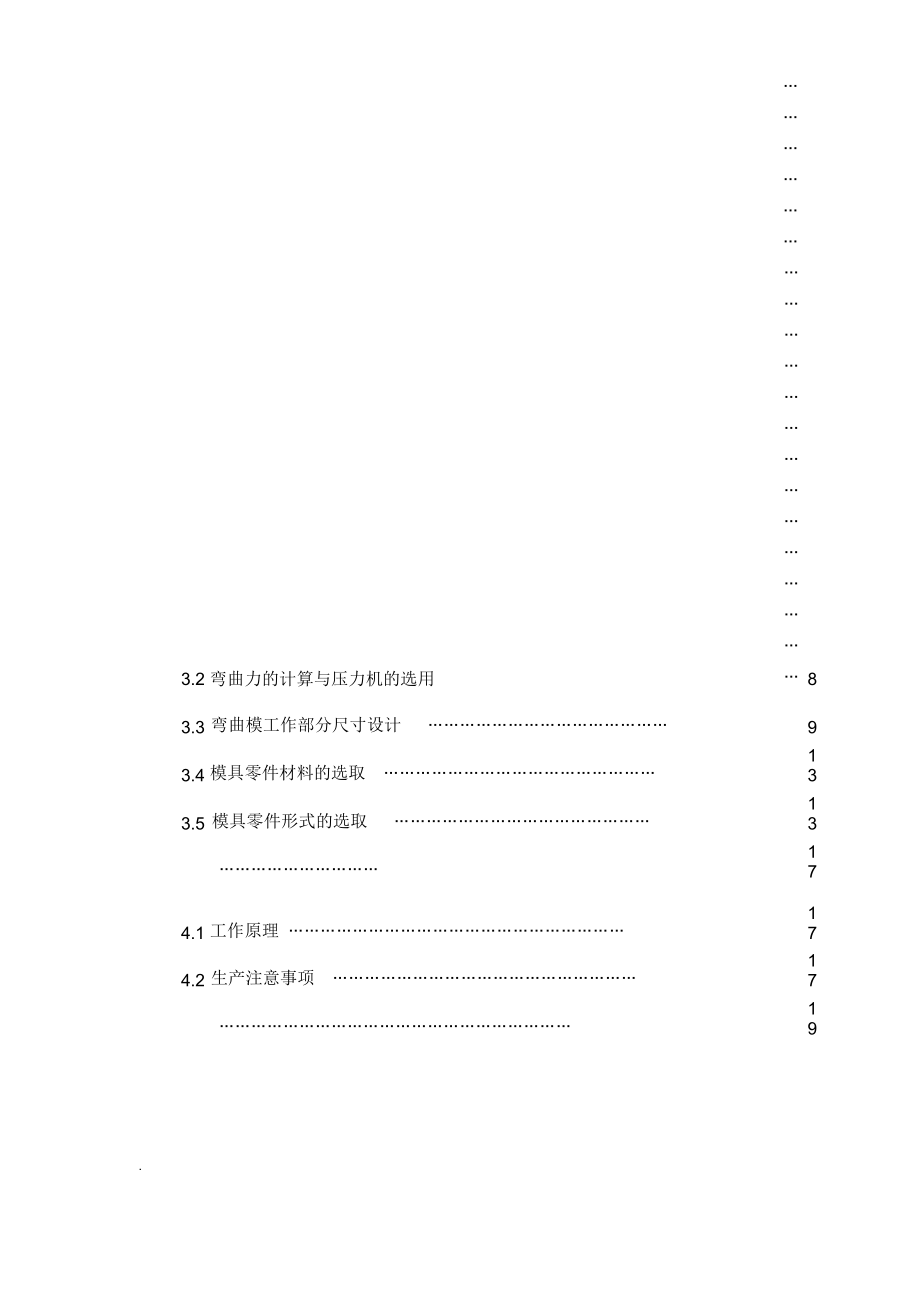


版权说明:本文档由用户提供并上传,收益归属内容提供方,若内容存在侵权,请进行举报或认领
文档简介
1、.目录 11.1设计的目的 11.2设计要求 11.3模具设计的意义122.1模具设计的内容 22.2弯曲件的质量分析32.3弯曲件的工艺性673.1弯曲件坯料展开尺寸的计算73.2弯曲力的计算与压力机的选用83.3弯曲模工作部分尺寸设计 93.4模具零件材料的选取 133.5模具零件形式的选取 13174.1工作原理 174.2生产注意事项 1719.第一章 概述1.1 设计的目的课程设计是冲压模具课程设计重要的综合性与实践性教学环节。课程设计的基本目标是:(1)综合运用冲压模具设计、机械制图、公差与技术测量、机械原理及零件、模具材料及热处理、 模具制造工艺等先修课程的知识,分析和解决冲压模
2、具设计过程中遇到的问题,进一步加深对所学知识的理解;(2)通过设计实践,逐步树立正确的设计思想,增强创新意识,基本掌握塑料模具设计的一般规律,培养分析问题和解决问题的能力。(3)通过计算绘图和运用技术标准、规范、设计手册等有关设计资料,进行冲压模具设计技能训练,为此后的模具设计及其机械设计打下良好的基础。1.2 设计要求详尽的设计计算说明书1 份、工作零件图2 张、模具装配图 1 份。1.3 模具设计的意义冲压成形 /塑料成型工艺与模具设计是机制专业的专业基础课程。通过模具的课程设计使学生加强对课程知识的理解,在掌握材料特性的基础上掌握金属成形工艺和塑件成型工艺, 掌握一般模具的基本构成和设计
3、方法,为学生的进一步发展打下坚实的理论、实践基础。.第二章冲压件的工艺分析2.1 模具设计的内容设计一副如下图 2.1 所示弯曲件的成形模具:图 2.1 弯曲件2.2 弯曲件的质量分析该弯曲件名为压块,形状对称,尺寸无精度要求,材料是Q345,低合金钢。采用复合模冲压成形,本模具是完成1 个 U 形和 2 个 V 形弯曲的冲压工艺,弯曲角都是 90。在实际生产中,弯曲件的质量主要受回弹、滑移、弯裂等因素的影响,重点介绍回弹因素,具体如下。2.2.1 弯曲件的回弹.回弹常温下的塑性弯曲和其它塑性变形一样,在外力作用下产生的总变形由塑性变形和弹性变形两部分组成。当弯曲结束, 外力去除后, 塑性变形
4、留存下来,而弹性变形则完全消失。 弯曲变形区外侧因弹性恢复而缩短,内侧因弹性恢复而伸长,产生了弯曲件的弯曲角度和弯曲半径与模具相应尺寸不一致的现象。这种现象称为弯曲件的弹性回跳(简称回弹)。弯曲件的回弹现象通常表现为两种形式:一是弯曲半径的改变, 由回弹前弯曲半径 r0 变为回弹后的r1。二是弯曲中心角变变,由回弹前弯曲中心角度0(凸模的中心角度)变为回弹后的工件实际中心角度1。2.2.2 影响回弹的主要因素1)材料的力学性能金属材料的变形特点与材料的屈服强度成正比,与弹性模数E 成反比,即材料的屈服强度 s 越高,弹性模量E 越小,弯曲弹性回跳越大。2)相对弯曲半径 rt相对弯曲半径rt 越
5、大,板料的弯曲变形程度越小,在板料中性层两侧的纯弹性变形区增加越多, 塑性变形区中的弹性变形所占的比例同时也增大。故相对弯曲半径 rt 越小,则回弹也越小。3)弯曲中心角4)弯曲方式及弯曲模板料弯曲方式有自由弯曲和校正弯曲。 在无底的凹模中自由弯曲时, 回弹大;在有底的凹模内作校正弯曲时,回弹值小。原因是:校正弯曲力较大,可改变弯曲件变形区的应力状态,增加圆角处的塑性变形程度。5)弯曲件形状工件的形状越复杂, 一次弯曲所成形的角度数量越多,各部分的回弹值相互牵制以及弯曲件表面与模具表面之间的摩擦影响,改变了弯曲件各部分的应力状态(一般可以增大弯曲变形区的拉应力),使回弹困难,因而回弹角减小。如
6、形件的回弹值比U 形件小, U 形件又比 V 形件小。6)模具间隙在压弯 U 形件时,间隙大,材料处于松动状态,回弹就大;间隙小,材料.被挤压,回弹就小。2.2.3 减少回弹的措施1)选用合适的弯曲材料在满足弯曲件使用要求的条件下,尽可能选用弹性模量E 大、 屈服极限 s小、加工硬化指数n 小、机械性能较稳定的材料,以减少回弹。2)改进弯曲工艺(1)采用热处理工艺对一些硬材料和已经冷作硬化的材料, 弯曲前先进行退火处理, 降低其硬度以减少弯曲时的回弹,待弯曲后再淬硬 。在条件允许的情况下,甚至可使用加热弯曲。(2)增加校正工序运用校正弯曲工序, 对弯曲件施加较大的校正压力, 可以改变其变形区的
7、应力应变状态,以减少回弹量。通常,当弯曲变形区材料的校正压缩量为板厚的2%5% 时,就可以得到较好的效果 。(3)采用拉弯工艺3)改进零件的结构设计在变形区压加强肋或压成形边翼,增加弯曲件的刚性,使弯曲件回弹困难 。4)改进模具结构(1)补偿法利用弯曲件不同部位回弹方向相反的特点,按预先估算或试验所得的回弹量,修正凸模和凹模工作部分的尺寸和几何形状, 以相反方向的回弹来补偿工件的回弹量。( 2) 校正法当材料厚度在 0.8mm 以上,塑性比较好,而且弯曲圆角半径不大时,可以改变凸模结构, 使校正力集中在弯曲变形区, 加大变形区应力应变状态的改变程度(迫使材料内外侧同为切向压应力、切向拉应变 )
8、,从而使内外侧回弹趋势相互抵消。( 3) 采用聚氨酯弯曲模利用聚氨酯凹模代替刚性金属凹模进行弯曲, 弯曲时金属板料随着凸模逐渐进入聚氨酯凹模, 激增的弯曲力将会改变圆角变形区材料的应力应变状态, 达到类似校正弯曲的效果,从而减少回弹 。2.2.4 回弹值的确定.1)小变形( r/t 10)自由弯曲时的凸模弯曲角和凸模圆角半径rTrsr; T(1800)( r / rT1)1 3Et式中: rT 凸模圆角半径; r弯曲件圆角半径;弯曲件弯曲角;T 凸模弯曲角;s 材料屈服点; E材料弹性模量;t板料厚度;2) 大变形 ( r/tR+2t,如弯曲边高度太小, 则难以形成足够的弯矩。.第三章设计方案
9、的确定3.1 弯曲件坯料展开尺寸的计算3.1.1 中性层的确定由于中性层的长度在弯曲变形前后不变,其长度就是弯曲件坯料展开尺寸的长度。而欲求中性层长度就必须找到其位置,用曲率半径0 表示。中性层位置与板料厚度 t、弯曲半径 r、变薄系数等因素有关,在实际生产中为了使用方便,通常采用下面的经验公式来确定中性层的位置:0rxt式中:0 中性层半径; r弯曲件内弯半径;x 为中性层位移系数,其值件下表:表3.1r/tx3.00.464.00.48 5.00.5从弯曲件图可以看到:圆角半径都为r=5mm,板料厚度t=1mm,查表3.1得 x=0.5,则中性层半径为:0rxt20.3222.64 mm0
10、rxt50.515.5mm3.1.2 毛坯展开尺寸的计算由于圆角半径 r0.5t,所以毛坯展开长度等于弯曲件直线部分长度与弯曲部Llii0 (rixi t)分中性层展开长度的总和,即180。弯曲件有 5 段直线部分和 4 段弯曲部分,因此L2(15565)()()-1-5 255-5-5-1 65-5-5 425 0.52278885545.5255.54mm2.3.2 弯曲力的计算与压力机的选用3.2.1 弯曲力的计算弯曲力是指弯曲件在完成预定弯曲时所需要的压力机施加的压力,是设计冲压工艺过程和选择设备的重要依据之一。弯曲力的大小与毛坯尺寸、零件形状、材料的机械性能、 弯曲方法和模具结构等多
11、种因素有关,理论分析方法很难精确计算,在实际生产中常按经验公式进行计算。1)自由弯曲时的弯曲力公式V 形弯曲件 : FVz0.6KBt 2b; U 形弯曲件 : FUz0.7 KBt 2b ;r tr t式中 : FVz 、 FUz 自由弯曲力 ; B 弯曲件的宽度 ; t 弯曲件厚度 ; r 内圆弯曲半径 ;b 弯曲材料的抗拉强度 ; K 安全系数 , 一般取 1.3。2)、校正弯曲力公式FJFq A式中 : FJ 校正力 ; Fq 单位面积上的校正力 ,Mpa;A 弯曲件被校正部分的投影面积 ,mm2。3)计算本弯曲件弯曲部分,其中两处V 形弯曲,一处U 形弯曲。 Q345 的b500MP
12、 V形弯曲力:F0.6KBt 2b0.61.35512500V Z5 13575 Nr t0.7KB t2b0.71.35512500U 形弯曲力 : FUZ5 14170.8Nr t总弯曲力 : F23575 4170.87745.8N校正弯曲力 :Fq50MPa ; 弯曲件被校正部分的投影面积A50552750mm2.FJFqA502750137500N自由弯曲力与校正弯曲力之和: FFJF 21375007745.8145245.8N3.2.2 压力机的选用压力机的选取总原则:压力机的公称压力必须大于弯曲时的所有工艺力之和。由于本模具采用自由弯曲和校正弯曲,所以压力机的公称压力必须大于自
13、由弯曲力与校正弯曲力之和,即FxjF145245.8N 。压力机选用还决定于压力机的调整与板料厚度误差的大小。由上述可知,该弯曲件弯曲所需的压力是145245.8N,查取模具设计手册,可选取具有以下规格的压力机,具体如下表3.2:表 3.2 压力机参数型号公称压滑块行行程次最大闭闭合高工作台尺垫板尺模柄孔力程数合高度度调节寸寸尺寸量J11-50160KN50mm150220m45mm前后厚度直径次 /minm,40mm,300mm40mm左右孔径深度450mm210mm60mm3.3 弯曲模工作部分尺寸设计3.3.1 凸模圆角半径当弯曲件的相对弯曲半径 r/t 较小时,取凸模圆角半径等于或略小
14、于工件内侧的圆角半径 r,但不能小于材料所允许的最小弯曲半径 rmin。那么,凸模的圆角半径应等于工件内侧圆角半径,即Rt5mm 。3.3.2 凹模圆角半径凹模圆角半径的大小不会直接影响到弯曲件的圆角半径, 但是过小的凹模圆角半径会使弯矩的弯曲力臂减小毛坯如凹模困难, 会擦伤毛坯表面。 另外,凹模两侧的圆角半径必须相等, 否则会引起板料偏移。 在实际生产中通常根据材料厚度选取凹模圆角半径:.当 t2mm, Ra(3 6)t; t2 4mm, Ra(2 3)t; t于采取复合模弯曲,凹模还要实现两处V 型弯曲工艺,且4mm, Ra2t。由r=5mm,因此,取R5mm 。3.3.3 凹模深度凹模深
15、度要适当,若过小则弯曲件两端自由部分太长, 工作回弹大,不平直;若深度过大则凹模过高,浪费模具材料并需要较大的压力机工作行程。对于 U 型弯曲件,如果弯曲件直边较长,凹模深度可以小于工件高度,凹模深度 l0 值见下表 3.3表 3.3弯曲 U 型件的凹模深度 l 0(mm)弯曲件边长 lt 11 t 22 t 44 t 66 t 1013191925253235螺钉规格M4、M5M5、M6M6、M8M8、M10M10、M12.第四章模具的工作原理及生产注意事项4.1 工作原理模具由上模座、凸模、销钉、螺钉、凹模、压边圈、橡皮、卸料螺钉、顶件块、推杆、下模座、紧固螺钉等组成。模具的工作过程:开启
16、模具后,将板料放在凹模上,通过导料板和定位销可靠定位,并通过顶板上定位销与板件上的中间孔配合固定,防止在弯曲时板件移动,凸模下行完成弯曲工艺。当行程终了时,凸模回程,顶料件将弯曲件顶出,完成一个工作流程。4.2 生产注意事项4.2.1 模具的安装和搬运冲模的使用寿命、工作安全和冲件质量等与冲模的正确安装有着极大的关系。1)冲模应正确安装在压力机上,使模具上下部分不发生偏斜和位移,这样可以保证模具有较高的准确性,避免产生废品。而且可保证模具寿命。2)模具安装时,将带有导向的模具,上下应同时搬到工作台面上。由于大型模具在工作台面上不便移动,应按材料的送料方向、 产品的取出方式、 气垫顶杆孔的位置等
17、尽量准确定位。先固定上模,然后根据上模的位置固定下模。3)固定上模的方法有压板压紧、螺钉紧固、燕尾槽配合和模柄固定等。对中小型模具, 最常用的方法是模柄固定。模柄装入曲柄压力机模柄孔后,采用模柄夹持器来固定。夹紧模柄时,旋紧夹持器上两螺母,再用方头螺钉顶紧模柄。4)凡大型模具用模柄固定时,为增强固定的可靠性,制成带固定斜面的模柄把用固定螺钉紧固,或模具的上模座用吊挂螺丝安装。5)当模柄外形尺寸大小模柄孔尺寸时,禁止用随意能够得到的铁块、铁片等杂物作为衬垫,必须采用专门的开口衬套或对开衬套。6)固定下模的方法主要有螺钉固定和压板固定。螺钉固定准确可靠,但增加了冲模制造工时,且装拆冲模也不方便,适
18、用于大、中型冲模。特别注意的是在安装下模座时,不要将废料孔堵住。.7)在冲压生产过程中,由于压力机的振动,可能引起固定冲模的坚固零件松动,操作者必须随时注意和检查各紧固零件的工作情况。8)对于笨重的冲模,为了便于安装和搬运,应设置起重吊钩,通常采用螺栓吊钩或焊接吊钩等 .4.2.2 模具的使用注意事项1)、使用模具前,应检查模具是否完好,所用的模具名称、编号和基本结构是否与工艺规程一致。 有导向装置的模具, 检查其润滑是否良好。 并清除模具表面油污、赃物。 2)、冲压用毛坯表面要洁净,并均匀涂抹润滑剂。3)、定期检查压力机,保证其精度和完好状态。4)、定期进行维护性修理。4.2.3 压力机应具有安全保护装置压力机安全装置应具有下列各项中的某一项功能,以杜绝人身事故的发生。1)压力机滑块运行期间,人体的任一部分不会进入危险区。2)滑块下行程时,当人体的任一部分进入危险区之前,滑块能停止下行程或停于下死点之前。3)滑块下行程时,能将进入危险区的人体某一部分推出。4)滑块下行程时,能将进入危险区的操作者手臂拉出。5)当操作者双手脱离启动离合器的操纵按钮(或操纵手柄)
温馨提示
- 1. 本站所有资源如无特殊说明,都需要本地电脑安装OFFICE2007和PDF阅读器。图纸软件为CAD,CAXA,PROE,UG,SolidWorks等.压缩文件请下载最新的WinRAR软件解压。
- 2. 本站的文档不包含任何第三方提供的附件图纸等,如果需要附件,请联系上传者。文件的所有权益归上传用户所有。
- 3. 本站RAR压缩包中若带图纸,网页内容里面会有图纸预览,若没有图纸预览就没有图纸。
- 4. 未经权益所有人同意不得将文件中的内容挪作商业或盈利用途。
- 5. 人人文库网仅提供信息存储空间,仅对用户上传内容的表现方式做保护处理,对用户上传分享的文档内容本身不做任何修改或编辑,并不能对任何下载内容负责。
- 6. 下载文件中如有侵权或不适当内容,请与我们联系,我们立即纠正。
- 7. 本站不保证下载资源的准确性、安全性和完整性, 同时也不承担用户因使用这些下载资源对自己和他人造成任何形式的伤害或损失。
最新文档
- 社会学视角下的冲突与和谐
- Cu、Ni对厌氧氨氧化脱氮的影响:微生物机制
- 燕青的课件介绍
- 研究工商业储能系统的智能化进展及其应用前景
- 根本原因分析法结合七何分析法在“贴”贴敷工作中应用的有效性探讨
- 燃料电池专题课件
- 动态服务发现与协同-洞察阐释
- 生物医学与人工智能的交叉研究-洞察阐释
- 物联网在APP开发中的应用-洞察阐释
- 资源循环利用在化学采矿中的应用研究-洞察阐释
- 2025年事业单位医疗卫生类招聘考试《综合应用能力(E类)医学技术》试卷真题及详细解析
- 护理急诊急救培训课件
- 2025年卫生系统招聘考试(公共基础知识)新版真题卷(附详细解析)
- 2025包头轻工职业技术学院工作人员招聘考试真题
- 超声科专业管理制度
- GB/T 8097-2025收获机械联合收割机测试程序和性能评价
- 2025年供应链管理与运作考试题及答案分享
- 2025至2030年中国粒度仪行业市场运行格局及发展趋势研究报告
- 2025邯郸武安市选聘农村党务(村务)工作者180名笔试备考试题及答案详解一套
- 重庆市普通高中2025届高一下化学期末学业质量监测试题含解析
- 井下探矿管理制度
评论
0/150
提交评论