

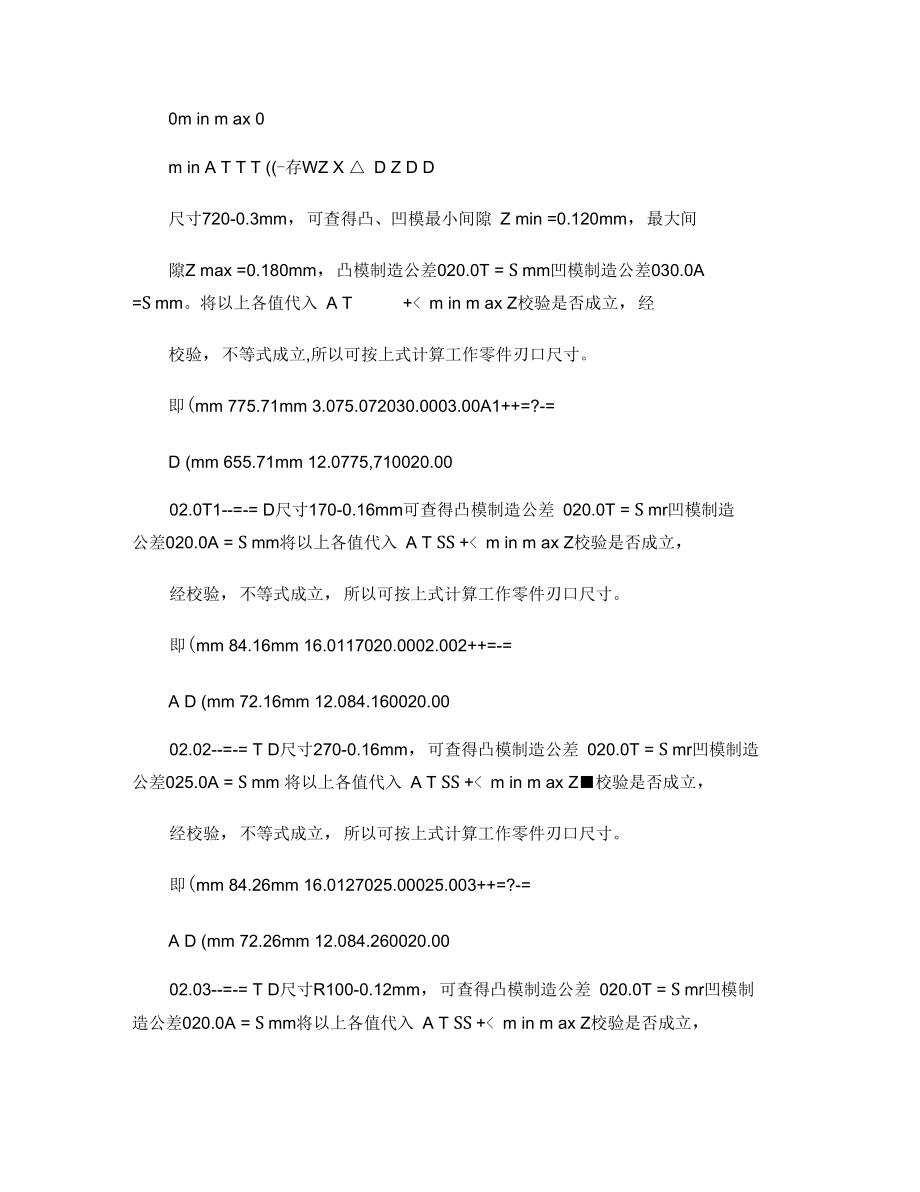
版权说明:本文档由用户提供并上传,收益归属内容提供方,若内容存在侵权,请进行举报或认领
文档简介
1、齿轮垫片冲孔落料复合模设计一题目:二原始数据数据如图1所示,大批量生产 材料为Q235,t =1mm图1产品零件图三冲压件工艺性分析O1材料:Q235为普通碳素结构钢,具有较好的冲裁成形性能。O2零件结构:零件结构简单对称,无尖角,对冲裁加工较为有利。零件中有两圆孔,孔的最小尺寸为 11mm,满足冲裁最小孔径m in d> 10.1=t mm要求。另外,经计算孔距零件外形之间的最小孔边距为4.5mm,满足冲裁件最小孔边距 min l > 1.55.1=t m的要求。所 以该零件的结构满足冲裁的要求O3尺寸精度:零件图上未标注公差的尺寸属于自由尺寸,可按IT14级确定工件 尺寸的公差
2、。查公差表2-3可得各尺寸公差为:零件外形:720-0.3mm 170-0.16mm 270-0.16mm R100-0.12mmR10-0.12mm R1.50-0.18mm R2.50-0.18mm孑L内形:110+0.1 mm孔心距:40 ±.12mm结论:适合冲裁。四冲裁工艺方案及模具类型的确定该零件包括落料、冲孔两个基本工序,可提出的加工方案如下:方案一:先落料, 后冲孔。采用两套单工序模生产。方案二:落料一冲孔复合冲压,采用复合模生产。方案三:冲孔一落料连续冲压,采用级进模生产。方案一模具结构简单,但需两道工序、两副模具,生产效率低,零件精度较差,在生 产批量较大的情况下
3、不适用。方案二只需一副模具,冲压件的形位精度和尺寸精度 易保证,且生产效率高。尽管模具结构较方案一复杂,但由于零件的几何形状较简单, 模具制造并不困难。方案三也只需一副模具,生产效率也很高,但与方案二比生产的 零件精度稍差。欲保证冲压件的形位精度,需在模具上设置导正销导正,模具制造、 装配较复合模略复杂。所以,比较三个方案欲采用方案二生产。现对复合模中凸凹模壁厚进行校核 ,当 材料厚度为1mm时,可查表2-24得凸凹模最小壁厚为2.7mm,现零件上的最小孔边 距为4.5mm,所以可以采用复合模生产,即采用方案二。五零件工艺计算1刃口尺寸计算根据零件形状特点,刃口尺寸计算采用分开制造法。(1落料
4、件尺寸的基本计算公式为A 0m ax A (-=+ D D0m in m ax 0m in A T T T (-存WZ X D Z D D尺寸720-0.3mm,可查得凸、凹模最小间隙 Z min =0.120mm,最大间隙Z max =0.180mm,凸模制造公差020.0T = S mm凹模制造公差030.0A=S mm。将以上各值代入 A T+< m in m ax Z校验是否成立,经校验,不等式成立,所以可按上式计算工作零件刃口尺寸。即(mm 775.71mm 3.075.072030.0003.00A1+=?-=D (mm 655.71mm 12.0775,710020.000
5、2.0T1-=-= D尺寸170-0.16mm可查得凸模制造公差 020.0T = S mr凹模制造 公差020.0A = S mm将以上各值代入 A T SS +< m in m ax Z校验是否成立,经校验,不等式成立,所以可按上式计算工作零件刃口尺寸。即(mm 84.16mm 16.0117020.0002.002+=-=A D (mm 72.16mm 12.084.160020.0002.02-=-= T D尺寸270-0.16mm,可查得凸模制造公差 020.0T = S mr凹模制造 公差025.0A = S mm 将以上各值代入 A T SS +< m in m ax
6、 Z校验是否成立,经校验,不等式成立,所以可按上式计算工作零件刃口尺寸。即(mm 84.26mm 16.0127025.00025.003+=?-=A D (mm 72.26mm 12.084.260020.0002.03-=-= T D尺寸R100-0.12mm,可查得凸模制造公差 020.0T = S mr凹模制 造公差020.0A = S mm将以上各值代入 A T SS +< m in m ax Z校验是否成立,经校验,不等式成立,所以可按上式计算工作零件刃口尺寸。即(mm 88.9mm 12.0110020.00020.004+=-=A D (mm 76.9mm 12.088.
7、90020.0002.04-=-= T D尺寸R10-0.12mm,可查得凸模制造公差 020.0T = S m凹模制造 公差020.0A = S mm将以上各值代入 A T+< m in m ax Z校验是否成立,经校验,不等式成立,所以可按上式计算工作零件刃口尺寸。即(mm 88.0mm 12.011020.00020.005+=-=A D (mm 76.0mm 12.088.00020.0002.05-=-= T D尺寸R1.50-0.18mm,可查得凸模制造公差 020.0T = S mrW模制 造公差020.0A = S mm将以上各值代入 A T SS +< m in
8、m ax Z校验是否成立,经校验,不等式成立,所以可按上式计算工作零件刃口尺寸。即(mm 365.1mm 18.075.05.1020.00020.006+=-=A D (mm 245.1mm 12.0365.10020.0002.06-=-= T D尺寸R2.50-0.18mm,可查得凸模制造公差 020.0T = S mrW模制 造公差020.0A = S mm将以上各值代入 A T SS +< m in m ax Z校验是否成立,经校验,不等式成立,所以可按上式计算工作零件刃口尺寸。即(mm 365.2mm 18.075.05.2020.00020.007+=?-=A D (mm
9、245.2mm 12.0365.20020.0002.07-=-= T D (2冲孔基本公式为m in T T ( -+=X d dA 0m in m in A ( S +=Z X d d尺寸110+0.1,查得其凸模制造公差 mm 02.0T = S凹模制造公差 mm 02.0A = S经验算,满足不等式A T SS +< m in m ax乙因该尺寸为单边磨损尺寸,所以计算时冲裁间隙减半,得mm 075.11mm 1.075.011(002.0002.0T -=? +=dmm 135.11mm 2/120.0075.11(02.0002.00A +=+=d(3中心距:尺寸 40
10、77;).12mm(+40+L.0mm.0404/mm2.排样计算分析零件形状,应采用单直排的排样方式,零件可能的排样方式有图2所示两 种。a b图2零件可能的排样方法比较方案a和方案b,方案b所裁条料宽度过窄,剪板时容易造成条料的变形和 卷曲,所以应采用方案a。现选用4000mrX 1000 mm的钢板,则需计算采用不同的裁 剪方式时,每张板料能出的零件总个数。(1裁成宽78.4mm、长1000mm的条料,则一张板材能出的零件总个数为220545492210004.784000=? =? ? ? (2裁成宽78.4mm、长4000mm的条料,则一张板材能出的零件总个数为21721811222
11、40004.781000? =? ?比较以上两种裁剪方法,应采用第1种裁剪方式,即裁为宽81.4mm、长1000mm的条料。其具体排样图如图3所示。图3零件排样图3.冲压力计算可知冲裁力基本计算公式为t KLT F =此例中零件的周长为256mm,材料厚度1mm ,Q235钢的抗剪强度取350MPa , 则冲裁该零件所需冲裁力为kN 117116480N 35012563.1 勺? =N F模具采用弹性卸料装置和推件结构,所以所需卸料力X F和推件力T F为kN 85.5kN 11705.0X X =?=F K F kN 3.19kN 117055.03T T ? =F NK F则零件所需得冲
12、压力为kN 15.142kN 3.1985.5117(T X =+=+=F F F F初选设备为开式压力机J23- 35。4.压力中心计算零件外形为对称件,中间的异形孔虽然左右不对称,但孔的尺寸很小,左右两边圆 弧各自的压力中心距零件中心线的距离差距很小,所以该零件的压力中心可近似认为就是零件外形中心线的交点。六、冲压设备的选用根据冲压力的大小,选取开式双柱可倾压力机 JH23 35,其中主要技术参数如下公称压力:350kN滑块行程:80mm最大闭合高度:280 mm闭合高度调节量:60 mm滑块中心线到床身距离:205mm工作台尺寸:380 mm 810 mm工作台孔尺寸:200 mm 89
13、0 mm模柄孔尺寸:© 50 mm 8 70 m垫板厚度:60 mm七、模具零部件结构的确定1标准模架的选用标准模架的选用依据为凹模的外形尺寸,所以应首先计算凹模周界的大小。由 凹模高度和壁厚的计算公式得,凹模高度m m 21m m 7228.0 ?=Kb H ,凹模壁 mm 38mm 218.125.1(齐=H C。所以,凹模的总长为 mm 148mm 38272(=? +=L (取160mm,凹模的宽度为 mm 107mm 40227(=? +=B。模具采用后置导柱模架,根据以上计算结果,可查得模架规格为上模座160mm X125mm X35mm,下模座 160mm X125mm
14、 X40mm,导柱 25mmX150mm,导套 25mm >85mmX33mm。2.卸料装置中弹性元件的计算模具采用弹性卸料装置,弹性元件选用橡胶,其尺寸计算如下:(1确定橡胶的自 由高度0H工(H H 45.30=mm10mm 712(105(1=+=+=+=t h h H 修磨工作工由以上两个公式,取mm 400=H。(2确定橡胶的横截面积Ap F A /X =查得矩形橡胶在预压量为10%15%时的单位压力为0.6MPa所以2mm 16417MPa6.0N9850=A(3确定橡胶的平面尺寸根据零件的形状特点,橡胶垫的外形应为矩形,中间开有矩形孔以避让凸模。结 合零件的具体尺寸,橡胶垫
15、中间的避让孔尺寸为82 mm X30mm,外形暂定一边长为 160mm,则另一边长b为mm118mm 1603082164173082160 孕+=? -?b A b (4校核橡胶的自由高度0H为满足橡胶垫的高径比要求,将橡胶垫分割成四块装入模具中,其最大外形尺寸 为80mm所以5.080400=D H橡胶垫的高径比在0.51.5之间,所以选用的橡胶垫规格合理。橡胶的 装模高度约为0.85 >40 mm =34mm。3.其他零部件结构凸模由凸模固定板固定,两者采用过渡配合关系。模柄采用凸缘式模柄,根据设 备上模柄孔尺寸,选用规格A50X100的模柄。八、模具装配图模具装配图见图纸A2。九
16、、模具零件图凸凹模、凸模、凹模图纸见 A3、A4。十、模具零件加工工艺模具零件加工关键是工作零件、固定板和卸料板,若采用线切割加工技术,这些 零件的加工变的简单,表7-2所列为圆孔直径11mm的凸模加工工艺,表7-3所列为凹模加工工艺过程。表7-2圆孔直径11mm的凸模加工工艺工序号工序名称工序内容1备料备圆柱料2热处理退火3粗车车外圆柱面,留单边余量0.5mm4热处理调质,淬火硬度达58-62HRC5精磨按图纸加工并达到图纸要求6钳工精修全面达到图纸要求7检验表7-3凹模加工工艺过程工序号工序名称工序内容I 备料 160X125 >352热处理退火3刨刨六面互为直角,留单边余量0.5m
17、m4热处理调质5磨平面磨六面互为直角6钳工画线划出各孔位线7线切割加工各孔8热处理按热处理,淬火硬度达58-62HRC9磨平面精磨上下面10线切割按图纸线切割工件轮廓至尺寸要求II 12钳工精修 全面达到图纸要求 检验注:凸凹模为配作件,并同属板类零 件致谢非常感谢聂老师、 葛永成老师在我大学的最后学习阶段 一一毕业设计阶 段给自己的指导,从最初的定题,到资料收集,到写作、修改,到论文定稿他 们给了我耐心的指导和无私的帮助。为了指导我们的毕 业论文,他们放弃了自己的休息时间,他们的这种无私奉献的敬业精神令人钦佩,在此我向他们表示我诚挚的谢意。同时,感谢所有任课 老师和所有同学在这四年来给自己的指导和帮 助,是他们教会了我专业知识,教会了我如何学习,教会了我如何做人。正是由 于他们,我 才能在各方面取得显著的进步,在此向他们表示我由衷的谢意,并祝所有的老师培养出越来越多的优秀人才,桃李满天下!通过这一阶段的努力,我的课程设计终于完成了,这意味着大 学生活即将结束。在大学阶段,我在学习上 和思想上都受益非浅,这 除了自身的努力外,与各位老师、同学和朋友的关心、 支持和鼓励是 分
温馨提示
- 1. 本站所有资源如无特殊说明,都需要本地电脑安装OFFICE2007和PDF阅读器。图纸软件为CAD,CAXA,PROE,UG,SolidWorks等.压缩文件请下载最新的WinRAR软件解压。
- 2. 本站的文档不包含任何第三方提供的附件图纸等,如果需要附件,请联系上传者。文件的所有权益归上传用户所有。
- 3. 本站RAR压缩包中若带图纸,网页内容里面会有图纸预览,若没有图纸预览就没有图纸。
- 4. 未经权益所有人同意不得将文件中的内容挪作商业或盈利用途。
- 5. 人人文库网仅提供信息存储空间,仅对用户上传内容的表现方式做保护处理,对用户上传分享的文档内容本身不做任何修改或编辑,并不能对任何下载内容负责。
- 6. 下载文件中如有侵权或不适当内容,请与我们联系,我们立即纠正。
- 7. 本站不保证下载资源的准确性、安全性和完整性, 同时也不承担用户因使用这些下载资源对自己和他人造成任何形式的伤害或损失。
最新文档
- 模拟芯片市场分析
- 宿迁辅警考试题库2025(有答案)
- 2025年山东省环保发展集团有限公司招聘考试试题(含答案)
- 老年清洁护理课件
- 老年护理沟通教学课件
- 2025年白板市场调研报告
- 2025年安全工作述职报告范例(三)
- 老师健康课件
- 景观园林彩钢房安装与维护合同
- 餐饮业员工权益保护与劳动仲裁协议
- 职业行为习惯课件
- 租赁住房培训课件下载
- 高校智能化教学评价体系变革的技术创新路径研究
- 高中复读协议书
- 2024年甘肃省临泽县教育局公开招聘试题含答案分析
- 2025-2030中国戊烷发泡剂市场深度解析及前景运行动态研究报告
- 糖尿病足截肢术后护理
- 广东省东莞市2022-2023学年高二下学期期末物理试题(含答案)
- 2024年深圳市中考生物试卷真题(含答案解析)
- 新疆维吾尔自治区2024年普通高校招生单列类(选考外语)本科二批次投档情况 (理工)
- 绿化养护服务投标方案(技术标)
评论
0/150
提交评论