



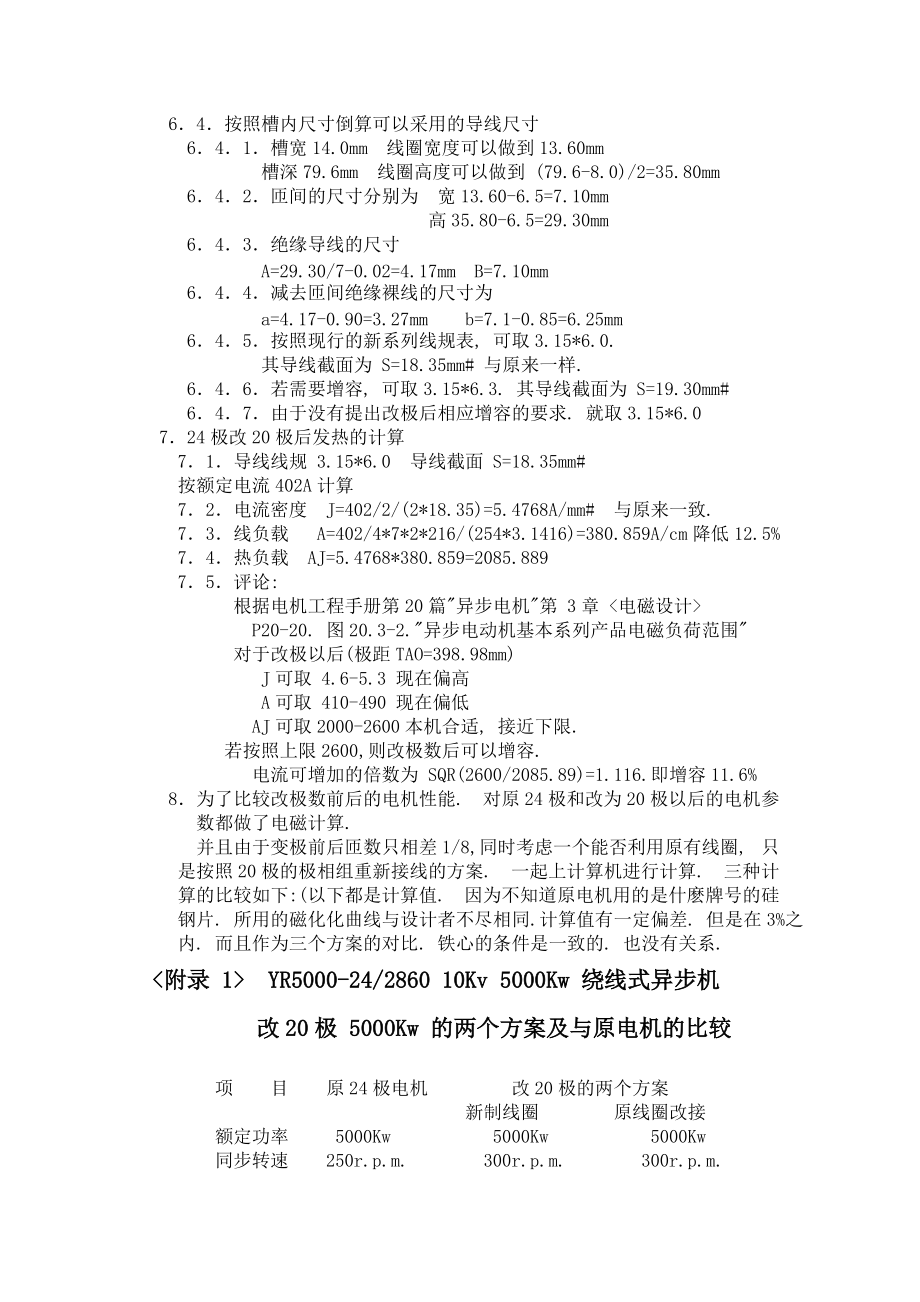
版权说明:本文档由用户提供并上传,收益归属内容提供方,若内容存在侵权,请进行举报或认领
文档简介
1、 YR5000-24/2860 10Kv 5000Kw 绕线式异步电动机 24极改20极设计计算技术总结 一. 前言 YR5000-24/2860 10Kv 5000Kw绕线式异步电动机系包钢初轧厂连轧车间 650机架的主传动电动机. 该机是1989年由哈尔滨电机厂制造并于同年 8月在包钢安装的. 以代替原来由沈阳电机厂制造的4000Kw电机. 这是国内制造的功率最大的高压绕线式异步电动机. 该电机运行 4年来一直运行正常. 1993年包钢初轧厂为了提高连轧车间的产量.提出要把这台电机改为20极. 以提高电机转速. 由于是绕线式异步电动机, 要变极数, 就要定子和转子一起改造. 根据初轧厂的委
2、托, 我对该机的改极做了设计. 包括电磁计算和线圈设计. 以下是设计总结.二. 原电机铭牌 YR5000-24/2860 5000Kw 247.5 r/m 功率因数 0.74 效率 94% 绝缘等级 F/F 级 定子电压 10Kv 定子电流 402A 接法 2Y 转子电压 1850V 转子电流 1639A 接法 2 定子重量 21500Kg 转子重量 21500Kg 总重量 640000Kg 哈尔滨电机厂 1989年 1月出品 出厂编号 7-15904 三. 原定子铁心绕组数据 1.铁心 Da=2860 Di=2540 Lt=1010 (17段) Z=216 bn*hn 14.4*80.0(迭
3、片尺寸. 迭片公差0.4mm) 2.绕组 2p=24 q=3.0 y=8 (1-9) a=2Y 3.原线圈 导线 2-3.0*6.3 SBEMB-40/155 单玻双层聚酰亚胺薄膜绕包线 绕法 上下两根并绕 匝数 4匝/只 匝间绝缘 0.13*25 有机硅玻璃云母带 4.绕组每相串联匝数 W=216/3/2*4=144匝四. 根据原线圈实物, 核算线圈尺寸, 发热参数和槽内填充. 1热负载 11导线线规 3.0*6.3 导线截面 S=18.35mm# 12电流密度 J=402/2/(2*18.35)=5.4768A/mm# 13线负载 A=402/2*4*2*216/(254*3.1416)=
4、435.2675A/cm 14热负载 AJ=5.4768*435.2675=2383.890 15评论: 根据电机工程手册第20篇"异步电机"第 3章 <电磁设计> P20-20. 图20.3-2."异步电动机基本系列产品电磁负荷范围" 对于本机 (极距TAO=332.5mm) J可取 4.5-5.2 本机偏高 A可取 400-480 本机合适 AJ可取1800-2400本机合适, 接近上限. 但是对于 F级可以. 2导线绝缘和匝间绝缘 21导线 SBEMB-40/155 单玻双层聚酰亚胺薄膜绕包线. 这个尺寸很难做双薄膜线. 22绝缘后的导
5、线尺寸为 3.4*6.7 则 A-a 0.40mm B-b 为 0.40mm 23匝间绝缘 0.13*25 有机硅玻璃云母带 根据图纸尺寸反算出匝间绝缘厚度 高度 29.5/4-2(3.4+0.02)=0.535mm 一层半迭包. 宽度 7.4-(6.7+0.1)=0.60mm 也符合一层半迭包. 24说明: 根据现行的匝间试验标准 (JB293-87) 单只线圈的冲击试验电压为2*Un+2500=22500V 平均每匝承受的试验电压是5625V 太高了. 本机现在标注的试验电压是每匝2000V.不符合要求. 匝间绝缘厚度 0.935mm是否合格没有根据. 3线圈尺寸计算: 31匝间: 高度(
6、3.40+0.02)*2+0.535)*4=29.5mm (这样与图纸相符) 宽度 6.70+0.10+0.70=7.5mm (这样与图纸相符) 32主绝缘: 由图纸标注主绝缘与匝间之间的尺寸差确定). 高度 29.5+6.2=35.7mm (这样与图纸相符) 宽度 7.4+6.2=13.6mm (这样与图纸相符) 主绝缘厚度含防晕层只有6.2mm也不厚. 4迭片以后的槽尺寸 (冲片尺寸减去迭片公差0.4mm) 宽度 14.4-0.4=14.0mm 高度 80.0-0.4=79.6mm 5槽内填充 宽度 14.0-13.6=0.4mm (松紧正常, 也不富裕) 高度 79.6-2*35.7=8
7、.2mm(对10Kv电机也不富裕) 高度分配为 槽底1.0mm,层间2.0mm,槽楔4.0mm,楔上0.5mm,共 7.5mm 楔下还有0.7mm 作为调节线圈公差用. 很紧张. 线圈必须做好.五. 改20极的计算 1改20极前后的极距 11按数值算为 24极 2540*3.141592654/24=332.48mm 20极 2540*3.141592654/20=398.98mm 12按槽数算为 24极 216/24=9槽 20极 216/20=10.8槽 2改20极前后的每极每相槽数 24极 q=216/(3*40)=3.0 20极 q=216/(3*20)=3.6 3改20极前后的槽节距
8、和短距比24极时y=8 (1-9) 8/9=0.888889 20极时 y=10(1-11) 10/10.8=0.926 y=9 (1-10) 9/10.8=0.0.8333 从抵消高次谐波的角度取 5/6的短距最好 5/6=0.83333 与第二种节距一致. 因此选 1-10 4改20极前后极后的基波绕组系数 41短距系数 24极时 Ky=Sin(8/9*90)=0.9848078 20极时 Ky=Sin(9/10.8*90)=0.9659258 42分布系数 24极时 Kp=0.5/(3*Sin(30/3)=0.9597951 20极时 Kp=0.5/(18*Sin(30/18)=0.95
9、5064 (3.6=36/10=18/5 所以按18计) 43基波绕组系数 24极时 Kw1=0.9848078*0.9597951=0.94521 20极时 Kw1=0.9659258*0.9550643=0.92252 524极改20极后的匝数计算 5124极改20极以后, 极距和每极下的面积之比为24/20=1.2 若气隙磁通密度不变. 则每极有效磁通也增加为原来的1.2倍 52原来每相串联匝数为4*3*12=144匝 (每支路12个极相组) 有效匝数 144*0.9452136=136.1076 现在每相串联匝数为可取144/1.2=120匝. 53每线圈匝数为 120/10/3.6=
10、3.333 (每支路10个极相组) 而且现在的绕组系数比原来的低. 3.3333*0.94521/0.92252=3.415 应该取3.5匝. 54这样相当于比计算值多 3.5/3.415=1.0248 多2.48% 若不考虑饱和的影响, 气隙磁密相应减小 2.48% 55上计算机上算出的实际值是8712.737/8816.925=0.9882 这是由于20极的压降系数Ke比24极的压降系数小. 感应电势略高的原因. 24极的压降系数查表值是0.922,实际的计算值是0.9445. 20极的感应电势为5484.8V.932,24极的感应电势为5427.093V.因此趋势是对的. 24极改20极
11、以后齿磁密相应减小. 轭磁密相应增加. 以后计算的趋势也是是对的. 56但是现在是分数槽, 无法做分数的匝数.可以按照等效的办法, 做成4Y接线, 每只线圈 7匝. 定子是 216槽. 20极. 每极每相槽数 q=3.6. 每 5组线圈一个轮回. 因此可以做成 4路. 最多也只能做成 4路. 57绕组排列为 A 3 4 4 4 33 4 4 4 33 4 4 4 33 4 4 4 3每相 72个. C 4 4 3 3 44 4 3 3 44 4 3 3 44 4 3 3 4每相 72个. B 3 3 4 4 43 3 4 4 43 3 4 4 43 3 4 4 4每相 72个. 58改20极以
12、后的每相串联匝数 W=72*7/4=126匝 有效匝数 126*0.92252136=116.23777 24极改20极所需的有效匝数为136.1076/1.2=113.423 实际的每相有效匝数为116.2375. 比需要值高. 116.10777/113.423=1.0248 高2.48%,与以前的计算是一致的 624极改20极后导线截面的选择 61确定匝间绝缘种类和匝间绝缘的厚度 现在线圈匝数为 7匝. 根据现行的匝间试验标准(JB/Z293-87).单只线圈的冲击试验电压为2*Un+2500=22500V 平均每匝承受的试验电压是22500/7=3214V 应该选择SBEFB-90/1
13、55-2N 自粘性玻璃丝包云母带绕包线. A-a 0.90mm B-b 0.85mm 云母带两层半迭包. 按照上海电机厂的绝缘规范用SBEFB-70/155-2N 云母带绕包线. A-a 0.70mm B-b 0.65mm 云母带两层1/4迭包.这种线因云母带的迭包率低, 我觉得不太好. 按照1991年我作为评委参加云母带绕包线的国家级鉴定会时, 会上介绍的云母带绕包线绝缘的选择原则, 每匝承受的平均冲击电压大于 3000V时就应该选择SBEFB-90/155-2N.而且本机对包钢太重要了. 匝间绝缘必须很可靠才行. 因此先按照 SBEFB-90/155-2N算. 若尺寸实在安排不下,导致电流
14、密度太大的话. 可选择新产品SBEMFB-70/155-2N自粘性双玻璃丝包云母带聚酰亚胺薄膜绕包线. 它的绝缘性能与SBEFB-90/155一致. 至SBEMB-60/155-2N聚酰亚胺薄膜绕包线, 因最大绝缘厚度只有0.60mm, 击穿电压只有5500V,也比较低. 故不做考虑. 62几种导线的性能比较如下导线型号 SBEFB-70/155-2N SBEFB-90/155-2N SBEMFB-70/155-2N导线名称 自粘玻璃丝包 自粘玻璃丝包 自粘玻璃丝包 云母带绕包线 云母带绕包线 云母带薄膜绕包线绝缘结构 0.10云446-1S 0.10云446-1S 0.03亚胺薄膜 1/4迭
15、包两层 半迭包两层 0.10云446-1S 各半迭包一层 迭包重叠率 25% 48-50% 48-50%绝缘厚度 0.70mm 0.90mm 0.70mm弯曲绝缘不开裂10a,10b 10a,10b 10a,10b 常态击穿电压 直线/8000V 直线/10000V 直线/10000V 10a/6000V 10a/7500V, 10a/7500V 63确定主绝缘种类和主绝缘的厚度 主绝缘选用 F级5440-1改性桐马环氧粉云母带. 它的介电强度可达到32-34Kv/mm, 而 B级的5438-1的介电强度只有24-26Kv/mm.而且它的机械柔韧性能也比较好. 是现在的通用的 F级云母带. 原
16、电机用的羧酸盐玻璃粉云母带和辛酸锌玻璃粉云母带因其绝缘性能不稳定, 都已不再生产. 绝缘厚度现在上海电机厂含防晕层为双边6.0mm,不含防晕层为双边5.7mm,为了保险起见希望增加0.5mm,到6.5mm. 由于该机对包钢很重要, 一旦停产损失很大. 所用高压电机应该是采用加强绝缘. 并且应该完全按照有关国家标准进行试验. 所以我把匝间绝缘和主绝缘都加强了. 64按照槽内尺寸倒算可以采用的导线尺寸 641槽宽14.0mm 线圈宽度可以做到13.60mm 槽深79.6mm 线圈高度可以做到 (79.6-8.0)/2=35.80mm 642匝间的尺寸分别为 宽13.60-6.5=7.10mm 高3
17、5.80-6.5=29.30mm 643绝缘导线的尺寸 A=29.30/7-0.02=4.17mm B=7.10mm 644减去匝间绝缘裸线的尺寸为 a=4.17-0.90=3.27mm b=7.1-0.85=6.25mm 645按照现行的新系列线规表, 可取3.15*6.0. 其导线截面为 S=18.35mm# 与原来一样. 646若需要增容, 可取3.15*6.3. 其导线截面为 S=19.30mm# 647由于没有提出改极后相应增容的要求. 就取3.15*6.0 724极改20极后发热的计算 71导线线规 3.15*6.0 导线截面 S=18.35mm# 按额定电流402A计算 72电流
18、密度 J=402/2/(2*18.35)=5.4768A/mm# 与原来一致. 73线负载 A=402/4*7*2*216/(254*3.1416)=380.859A/cm降低12.5% 74热负载 AJ=5.4768*380.859=2085.889 75评论: 根据电机工程手册第20篇"异步电机"第 3章 <电磁设计> P20-20. 图20.3-2."异步电动机基本系列产品电磁负荷范围" 对于改极以后(极距TAO=398.98mm) J可取 4.6-5.3 现在偏高 A可取 410-490 现在偏低 AJ可取2000-2600本机合适,
19、 接近下限. 若按照上限2600,则改极数后可以增容.电流可增加的倍数为 SQR(2600/2085.89)=1.116.即增容11.6% 8为了比较改极数前后的电机性能. 对原24极和改为20极以后的电机参数都做了电磁计算. 并且由于变极前后匝数只相差1/8,同时考虑一个能否利用原有线圈, 只是按照20极的极相组重新接线的方案. 一起上计算机进行计算. 三种计算的比较如下:(以下都是计算值. 因为不知道原电机用的是什麽牌号的硅钢片. 所用的磁化化曲线与设计者不尽相同.计算值有一定偏差. 但是在3%之内. 而且作为三个方案的对比. 铁心的条件是一致的. 也没有关系. <附录 1>
20、YR5000-24/2860 10Kv 5000Kw 绕线式异步机 改20极 5000Kw 的两个方案及与原电机的比较 项 目 原24极电机 改20极的两个方案 新制线圈 原线圈改接额定功率 5000Kw 5000Kw 5000Kw同步转速 250r.p.m. 300r.p.m. 300r.p.m.额定转速 247.61 297.85 297.46 额定转矩 19688.2Kg.M 16367.3Kg.M 16388.8Kg.M额定电压 10Kv 10Kv 10Kv铭牌电流 402A - -计算电流 411.6A 417.3A 383.11A线圈匝数 4匝/只 7匝/只 4匝/只每相匝数 14
21、4匝/相 126匝/相 144匝/相接线路数 2Y 4Y 线 规 2-3.0*6.30 2-3.0*6.30 2-3.0*6.30线圈节距 Y=8(1-9) Y=9(1-10) Y=8(1-9)短 距 比 8/9=0.8889 9/10.8=0.8333 8/10.8=0.7407短距系数 0.9848079 0.9659259 0.9182162分布系数 0.9597949 0.9550644 0.9550644绕组系数 0.9452136 0.9225214 0.8769556有效匝数 136.11 116.24 126.28压降系数 0.9445 0.9525 0.9532感应电势 54
22、27.09V 5484.83V 5484.83V饱和系数 1.22 1.20 1.11 每极磁通 1.827E+07 2.161E+07 1.975E+07气隙磁密 8816.9Gs 8712.7Gs 8223.2Gs定子齿磁密 16150.7Gs 15959.8Gs 15063.0Gs定子轭磁密 14447.7Gs 17082.1Gs 15618.1Gs转子齿磁密 15747.9Gs 15561.8Gs 14687.3Gs转子轭磁密 12361.7Gs 14615.7Gs 13363.1Gs励磁电流 232.3A 252.3A 190.7A标 么 值 0.804809 0.873950 0.
23、660447电抗计算系数 0.05556 0.04863 0.05739定子漏抗 x1 0.06897 0.05440 0.07089转子漏抗 x2 0.06397 0.04783 0.05735总电抗 X 0.1367 0.10462 0.13105最大转矩倍数 3.2527 4.2626 3.4185 对24极转矩 3.2527 3.5522 2.8487 功率因数 0.7374 0.7290 0.7923 效率 95.16% 94.91% 95.09% 匝间绝缘厚度 0.94mm 0.90mm 0.94mm 主绝缘厚度 6.20mm 6.20mm 6.20mm定子电流密度 5.6074
24、5.6849 5.2195 线负荷 445.64 395.33 414.82 热负荷 2498.91 2247.37 2165.14定子铜损 71.08 Kw 63.92 Kw 61.59 Kw定子铁损 82.96 Kw 101.28 Kw 86.50 Kw定子损耗 154.04 Kw 165.20 Kw 148.09 Kw 总损耗 256.79 Kw 268.41 Kw 257.98 Kw 定子铁心温升 48.92 K 44.56 K 40.64 K定子线圈温升 74.35 K 65.91 K 62.07 K转子空载电压 1836.9V 2168.5V 1997.5V转子额定电流 1653.
25、4A 1395.7A 1522.5A转子电流密度 5.6486 4.7680 5.2012 线负荷 345.36 291.51 318.00 热负荷 1950.79 1389.91 1653.99转子铁心温升 41.62 K 34.34 K 40.64 K转子线圈温升 54.43 K 39.59 K 62.07 K 9通过以上计算可以看出: 91原电机的设计气隙磁通密度较高, 铁心齿磁密和轭磁密也比较高, 气隙相对也比较大. 因此励磁电流较大, 功率因数较低,最大转矩倍数较高, 定子电流的标么值也较高. 它的参数范围特征与同期生产的前两机架的YR2000-20/2150 10Kv 2000Kw
26、 绕线式异步机和相似. 我想. 因为是作为连轧机上的电机, 其设计思想主要是提高最大转矩倍数. 因此对励磁电流和功率因数做了一定的牺牲. 92原电机所采取的定子电流密度较高,因此热负荷和定子线圈偏高. 但是还都在允许范围之内. 对于 F级绝缘.定子线圈计算温升在74.4K,还有一点裕度. 93改为20极, 采用新制线圈, 并且选用比较好的短距系数. 这时的短距系数比原电机小. 因此使得基波绕组系数有所减小. 如前面所计算, 有效匝数比保持气隙磁密不变所计算出的需要匝数增加很少. 因此气隙磁密和齿磁密稍有减少. 气隙磁密由8816.9GS减少为8712.7Gs, 减少1.18% 定子齿磁密由16
27、150.7Gs 减少为15959.8Gs,减少1.18% 转子齿磁密由15747.9GS 减为为15561.8Gs,减少1.18% 但是因为每极气隙面积增加20%, 相应地轭磁密增加. 定子轭磁密由14447.7Gs 增加为17082.1Gs,增加18.23% 转子轭磁密由12361.7GS 增加为14615.7Gs,增加18.23% 94这样使总的励磁安匝增加, 励磁电流增加. 励磁电流由232.3A增加到252.3A, 增加8.61% 励磁电流标么值由0.804809增加到0.873950 95励磁电流的增加导致功率因数的下降 功率因数由0.7374降至0.7290, 下降1.14% 96
28、励磁电流的增由导致定子电流的增加 定子电流由411.6A增加至417.3A, 增加1.38% 97由于轭磁密的增加大于齿磁密的减小, 使定子铁损增加. 定子铁损由82.96Kw 增加至101.28Kw, 增加22.1% 虽然由于匝数减少使铜损减少, 但是仍使定子损耗和总损增加, 使效率降低. 定子损耗由154.04Kw增至165.20Kw, 增加7.24% 总损耗由256.79Kw增至268.41Kw, 增加4.53% 效率由95.16%降至94.91% 98最大转矩倍数有增加 最大转矩倍数由 3.2527 增至 4.2626 但是由于转速增加, 额定转距减小, 实际上相当于绝对值 只增加3.
29、5522/3.2527=1.092 99定子电流增加, 电流密度增加. 但是由于每槽线数减少,线负荷减小. 热负荷减小. 热负荷由2498.91 减至2247.37, 减小10.07% 910相应地铁心和线圈温升降低 定子铁心温升由48.92K降至44.56K 定子线圈温升由74.41K降至65.91K 911转子空载电压升高和转子电流减小. 转子空载电压由1836.9V 增至2168.5V 转子额定电流由1653.4A 减至1395.7A 912相应地转子热负荷及铁心线圈的温升也降低 转子电流密度由5.6486降至4.7680 线负荷由345.36降至291.51 热负荷由1950.8降至1
30、389.9 转子铁心温升由41.62K降至34.34K 转子线圈温升由54.43K降至39.59K 由此比较可以看出: 新设计的24极改20极方案. 除了由于轭磁密增加引起的励磁电流增加、铁损增加、功率因数降低、定子电流增加和转子电压增加等问题外. 转距不低, 效率虽有一点降低但是符合标准要求. 定转子绕组的热负荷与铁心及线圈温升都有降低. 可以通过. 电机还可以适当增容. 根据热负荷不超过 F级允许的热负荷2700估算, 改20极后可以增容 SQR(2700/2247.37)=1.096 即增容9.6%左右. 10线圈不动, 仅极相组重新组合, 改接成20极的方案可以同时从表中看出. 也是可
31、行的. 就不再具体分析了.六. 线圈绝缘工艺 1匝间模压直线部分固化成型. 预热后上模.180度20分钟. 上下模要轻拿轻放, 待线圈冷却后再拆脱模带. 以防变形. 2引线 0.14*25 5443-1 半迭包 9层. 比电机厂的规范多一层. 再加包一层 0.10*25涤沦玻璃丝交织带. 引线绝缘包扎进斜边100mm,出鼻端30mm. 并要注意搭接处必须层层过渡形成锥体搭接. 3主绝缘 31直线部分 0.14*25 5440-2改性桐马环氧粉云母带半迭包14-15层 压缩后绝缘厚度 6.3-6.5mm (包括防晕层) 32端线部分 0.14*25 5440-2 半迭包11层. 绝缘计算厚度为6
32、.9mm(不包括防晕层和保护带) 33端部绝缘与引线层层迭压往前包. 最后一层, 下线包到斜边与鼻端相切处. 上线尽量往前包把引线紧靠鼻端. 34最后一层云母带和保护布带都要左右交叉勒紧. 35端部保护带 0.10*25涤沦玻璃丝交织带半迭包一层. 包进铁心10mm 4防晕处理 按一级恒电阻防晕处理工艺(电机工程手册P19-71表19.4-22) 进行. 5主绝缘模压 51130度预热. 时间根据云母带的胶化时间试验进行. 52前一只线圈模压完成后, 停电降温, 清理下模.下一只上模温度不超过 150度. 53上模后逐渐升温压紧. 避免流胶过多. 上压铁紧靠后 180度热压 1小时. 54下模
33、后认真测量尺寸. 按计算单所给的名义尺寸. 取下公差. 宽度公差 -0.2mm 高度公差-0.3mm七. 嵌线绝缘和工艺 1端箍绝缘 0.14*25 5440-1 半迭包11层 再包 0.04*25聚酯薄膜热收缩带 1层. 加热固化. 再包 0.10*25涤沦玻璃丝交织带半迭包一层. 端箍与线圈之间垫 1-2层 3mm厚的涤沦适形毡. 2槽内垫条 槽底 0.5*16*500 3240 环氧酚醛玻璃布板 1层. 层间 1.5*16*560 3240 环氧酚醛玻璃布板 1层. 楔下 (调节槽内填充用, 是否需要视松紧程度而定) 0.5*16*600 3240 环氧酚醛玻璃布板 1层. 短铁心的一台
34、相应地短100mm 3槽楔 5mm厚 3240 环氧酚醛玻璃布板.(槽内紧张, 可凸出铁心 1mm) 总长为480mm(每端伸出铁心15mm) 可用 160mm 3条. 短铁心的一台可用 190mm 2条. 端面要刨齐, 以免打劈. 4梆扎 用 6mm涤沦护套玻璃丝绳. 线圈下线边与端箍接触处垫入 1-2层 3mm厚涤沦毡, 并用涤沦护套玻璃丝绳梆扎牢. 上线两线圈之间绑一处. 绑在斜边中间. 5连接线绝缘 51相内线圈连接线 0.14*25 5440-1 半迭包10层 (比电机厂规范多 2层) 再包 0.10*25涤沦玻璃丝交织带半迭包一层. 52极间联接 0.14*25 5440-1 半迭
35、包12层 (比电机厂规范多 2层) 再包 0.10*25涤沦玻璃丝交织带半迭包一层. 53上下引线头各用 6mm涤玻绳绑一周. 54极间连线绑扎时互相用涤纶毡 3层垫起来, 再用涤玻绳绑紧. 每根连线绑两处. 6引出线 使用JBHF-10000V硅橡胶橡皮电缆. 35平方毫米八. 定子绕组绝缘处理 1定子嵌线后经试验合格后, 整个定子绕组浸 F级1044桐马环氧浸渍漆2次. 每次浸漆后应烘干. 2浸漆烘干后在热状态下喷西绝185#聚酯凉干红磁漆 1次.九. 试验规范 1线圈 11匝间冲击电压试验 根据JB/Z293-87规定: 冲击电压峰值为 2*Un+2500=22500V. 每只线圈冲击
36、5次 12工频耐压试验 根据JB6204-92规定: 10000Kw 以下电机, 线圈试验电压有效值为 2.75*Un+4500=32000V 增加3000V 实际耐压35000V 电极长度为 Lt(铁心长)+20mm. 耐压时间每只 1分钟.(工频耐压试验时间都为1分钟.不重复说明) 以下为考核试验. 非必做项目. 可抽样进行. 13瞬时工频击穿电压. 室温, 变压器油中进行, 升压速度1000V/S.电极长度为铁心长度. 合格品 70KV, 14瞬时工频击穿场强. 室温, 变压器油中进行, 升压速度1000V/S.电极长度为铁心长度.绝缘厚度从裸线算起. 击穿场强=击穿电压/平均绝缘厚度.
37、合格品 20KV/mm, 一等品 24KV/mm, 优等品 27KV/mm 15常态介质损失角正切 用高压电桥, 应符合GB311"高电压试验技术".室温下带护环, 0.6U 合格品 2.5%, 一等品 2.0%, 优等品 1.5% 16常态介质损失角正切增量 以0.8U和0.2U时的介质损失角正切之差作为常态介质损失角正切增量 合格品 2.0%, 一等品 1.5%, 优等品 1.0% 17热态介质损失角正切(130度 1小时) 合格品 8.0%, 一等品 6.0%, 优等品 5.0% 18起晕电压 在暗室, 以目测为准. 抽检 10% >1.5*U 为合格. 2嵌线
38、 21单只线圈下槽内 2.50*U+2500=27500V 22.接线后, 浸漆前 2.25*U+2000=24500V 3成品 电机组装后 2*U+1000=21000V 4为便于和以后的运行情况比较, 可加做直流耐压 (但是不能由此代替交流耐压) 最高试验电压为 3.5*U=35000V 每 5000V做一个点, 每档下维持 1分钟. 泄漏电流应该与电压成正比. 在最高试验电压时泄漏电流不应大于20微安. 包钢电修厂张继远 1993年 5月初稿注: 以上是24极改20极的设计和工艺要求. 后来由于5000Kw电机若改成20极以后与前两个机架不好匹配. 此改造计划未能实施. 但是把此设计方案
39、和工艺总结出来, 对于以后的工作还是有益的. YR5000-24/2860 10Kv 5000Kw 绕线式异步电动机 转子支架开裂和键松动事故的处理总结 一. 前言 YR5000-24/2860 10Kv 5000Kw绕线式异步电动机系包钢初轧厂连轧车间 650机架的主传动电动机. 该机是1989年由哈尔滨电机厂制造并于同年 8月在包钢安装的. 以代替原来由沈阳电机厂制造的4000Kw电机. 这是国内制造的功率最大的高压绕线式异步电动机.该电机运行 8年来一直运行正常. 随着初轧厂连轧车间产量的不断提高, 电机的作业率也不断提高. 于1997年发生了转子支架开裂和键松动事故. 新购一个转子需要
40、外购资金 130万元. 并且制造周期长. 生产上等不得. 电修厂依靠依靠自己的力量分析了事故发生的原因并因地制宜确定了修理方案. 对该转子进行了修复.二. 原电机铭牌 YR5000-24/2860 5000Kw 247.5 r/m 功率因数 0.74 效率 94% 绝缘等级 F/F 级 定子电压 10Kv 定子电流 402A 接法 2Y 转子电压 1850V 转子电流 1639A 接法 2 定子重量 21500Kg 转子重量 21500Kg 总重量 640000Kg 哈尔滨电机厂 1989年 1月出品 出厂编号 7-15904 三. 事故原因分析 YR5000-24/2860电机转子支架是由焊
41、在轮箍上的两道幅板上面沿轴向敷设12根筋焊接而成的笼形结构. 在这12根支架筋上开槽,并放置12对切向键. 由这12对切向键把转子铁心撑紧而传递转矩. 哈尔滨电机厂设计的这个转子支架的12根筋的两端伸出幅板的长度较长, 形成悬臂梁状态. 支架筋是沿轴向均匀传递转矩的. 这样支架筋在与幅板焊接处所受到的扭力就很大. 在有些切向键松动而不传递转矩后, 其余支架筋所受到的扭力就更大, 而发生断裂.四. 修理方案要点 1.12根支架筋加固. 特别是已经断裂的更应加固好. 可以在支架筋的悬出部位两侧沿切向加三角形撑块焊牢. 支架筋下面也可以沿径向加焊三角支撑块. 但不如切向作用大. 2.12对切向键更换
42、. 认真研配. 3.铁心加热再把键打紧打键.这是为了使传递扭矩的切向键在电机运行时不松弛. 要求在铁心比支架温度高 35-40度的条件下, 将键再楔紧. 4.由于铁心不可避免地产生变形和偏心,为此应该把转子铁心表面车园. 以免由于气隙不均而产生电磁振动. 5.以上处理的转子应该作静平衡.五.电修厂所做的工作 1.12对切向键的研配 2.铁心加热, 与支架形成需要的温差. 并均匀把键打紧. 3.核算能否车削转子表面.六. 铁心加热方案 1.若按照电机厂的加热方案是对铁心进行感应加热. 即在铁心外园上缠绕一定匝数的电缆通入工频交流电, 利用铁心的磁滞和涡流效应使铁心发热. 但现在铁心上有线圈, 就
43、不能再用感应加热. 2.于是考虑能否对线圈通电加热 (1).从滑环通三相交流 该电机转子电压U2=1850V,转子电流I2=1639A 三角形接法. 单独给转子通电时的短路电压大约为额定电压的1/5-1/6,即 308V-370V, 此电源在现场难以找到.(没有这麽大的功率) 虽然此方案的三相电流一致, 发热也均匀. 但电源解决不了, 只能放弃. (2).用直流电. 我厂有30Kw 6V/12V 5000/2500A直流发电机. 考虑能否用它供电. 从滑环上任意两个环通电, 相当于两相绕组串联后再与第三相绕组并联. 经计算每相绕组的电阻为0.0158欧姆. 按此接法, 从滑环上测得的总电阻为 0.01053欧姆. 电压12V时的电流为1140A,功率为13.68Kw 还有一种接法. 把一相短路, 另两相并联. 总电阻为0.0079 欧姆. 电压为 12V时的电流为1519A.功率为18.23Kw.比第一种接法高33% 因此选用第二种接法. 但即使这样加热功率还偏低. 把发
温馨提示
- 1. 本站所有资源如无特殊说明,都需要本地电脑安装OFFICE2007和PDF阅读器。图纸软件为CAD,CAXA,PROE,UG,SolidWorks等.压缩文件请下载最新的WinRAR软件解压。
- 2. 本站的文档不包含任何第三方提供的附件图纸等,如果需要附件,请联系上传者。文件的所有权益归上传用户所有。
- 3. 本站RAR压缩包中若带图纸,网页内容里面会有图纸预览,若没有图纸预览就没有图纸。
- 4. 未经权益所有人同意不得将文件中的内容挪作商业或盈利用途。
- 5. 人人文库网仅提供信息存储空间,仅对用户上传内容的表现方式做保护处理,对用户上传分享的文档内容本身不做任何修改或编辑,并不能对任何下载内容负责。
- 6. 下载文件中如有侵权或不适当内容,请与我们联系,我们立即纠正。
- 7. 本站不保证下载资源的准确性、安全性和完整性, 同时也不承担用户因使用这些下载资源对自己和他人造成任何形式的伤害或损失。
最新文档
- 高校生物技术专业课程设计与产学研结合路径
- 云南省昆明市云南师范大实验中学2025届九上化学期末达标测试试题含解析
- 山东省济南市章丘区2025届数学八上期末监测模拟试题含解析
- 生产基地搬迁及设备迁移合同
- 《出租车公司司机招聘与智能驾驶技术研发合同》
- 元件行业深度报告:特种玻纤布供不应求国产厂商加速渗透
- 提升用户体验的产品设计思路与方法
- 2025至2030贝类行业发展趋势分析与未来投资战略咨询研究报告
- 2025至2030房地产基金行业市场发展分析及前景趋势与投融资战略报告
- 2025至2030中国自走棋行业市场深度研究及发展前景投资可行性分析报告
- 2025年广西中考语文试题卷(含答案)
- 建设工程法律培训
- 江苏省南通市2024-2025学年高二下学期6月期末质量监测政治试题(含答案)
- (高清版)DB31∕T 1427-2023 首席质量官评价规范
- 一级医院医保管理制度
- 2025年南京市中考数学真题试卷
- 2025年呼伦贝尔农垦集团有限公司招聘笔试参考题库含答案解析
- 2025年重庆市中考数学试卷真题(含标准答案)
- 2025年内蒙古煤炭地质勘查(集团)一零九有限公司招聘笔试参考题库含答案解析
- T/CBMCA 039-2023陶瓷大板岩板装修镶贴应用规范
- 涂装厂协议书范本
评论
0/150
提交评论