

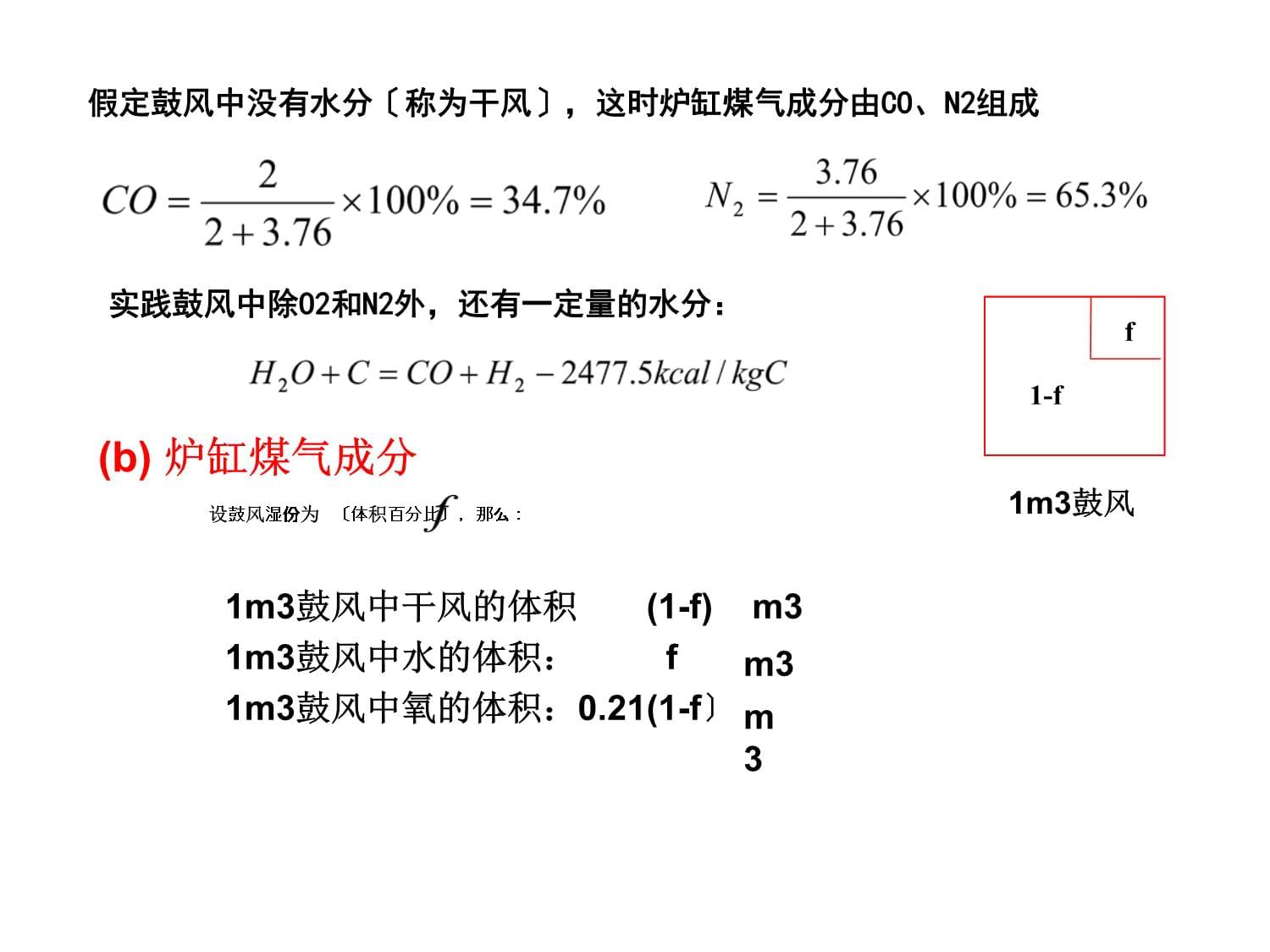


版权说明:本文档由用户提供并上传,收益归属内容提供方,若内容存在侵权,请进行举报或认领
文档简介
第四章高炉炉料和煤气运动4.1炉缸反响4.2煤气运动4.3炉料运动4.4高炉能量利用计算4.1炉缸反响从炉顶参与的焦炭,其中70~75%是在风口前与鼓风中的O2熄灭,17~21%参与直接复原反响,10%左右溶解进入铁水。焦炭在风口前熄灭:〔1〕产生热量和气体复原剂;〔2〕产生空间使炉料下降;〔3〕直接复原、渗碳、渣铁间的反响1.炉缸熄灭反响机理(a)碳素熄灭反响完全燃烧:不完全熄灭:
假定鼓风中没有水分〔称为干风〕,这时炉缸煤气成分由CO、N2组成实践鼓风中除O2和N2外,还有一定量的水分:(b)炉缸煤气成分设鼓风湿份为〔体积百分比〕,那么:1m3鼓风中干风的体积(1-f)m31m3鼓风中水的体积:f1m3鼓风中氧的体积:0.21(1-f〕1-ffm3m31m3鼓风1m3鼓风的熄灭反响:CO的体积=H2的体积=N2的体积=1m3鼓风产生的煤气总体积:
熄灭反响产物成分鼓风湿度(%)燃烧产物组成(%)COH2N20123534.735.035.235.4535.9300.81.62.434.065.364.263.262.1160.06结论:鼓风湿度越高,煤气中CO、H2浓度添加,N2减少
f=1.25%相当于10g/m3f=1%相当于:不同鼓风湿度煤气的变化(C〕1kgC熄灭需求的风量和产生的煤气量i〕熄灭1kg碳素所需求的风量24kg22.4m31kgx=22.4/24=0.933m3O2/kgC当时当时ii〕熄灭1kg碳素生成的煤气体积1m3鼓风产生的煤气总体积:知1kgC熄灭需求的风量:其中:
,其中时时时时结论:〔1〕湿份添加,炉缸煤气体积变化不大;〔2〕炉缸煤气体积大约是风量的1.21倍;〔3〕但炉顶煤气体积是鼓风量的1.3~1.4倍。不同鼓风湿度煤气的变化2:熄灭带与风口盘旋区〔1〕风口盘旋区鼓风以100~200m/s的速度从风口吹入充溢焦炭的炉缸区域,在风口前构成一个近似球形的空间。在球形空间内部,气流夹带着焦炭作盘旋运动,焦块的运动速度4~20m/s〔前苏联测定〕,称这一球形区域为风口盘旋区。〔2〕熄灭带在盘旋区外围有一层100~200mm的焦炭疏松层称中间层,将盘旋区和中间层统称为熄灭带。实际中常以CO2降至1~2%的位置定为熄灭带界限。大型高炉的熄灭带长度在1000~15000mm左右风口盘旋风口附近煤气成分的变化强化供风风口附近煤气成分的变化3.熄灭带对高炉冶炼过程的影响1〕熄灭带是炉内焦炭熄灭的主要场所,而焦炭熄灭所腾出来的空间是促使炉料下降的主要要素。消费中的高炉的熄灭带上方总是比其它地方松动,且下料快〔称焦炭松动区或活性焦炭区〕,熄灭带内熄灭的焦炭的80%来自风口上方。因此,当熄灭带占整个炉缸面积的比例大时,炉缸活泼面积大,料柱比较松动,有利于高炉顺行。因此,从高炉顺行的角度来说,希望熄灭带程度投影面积大些,多伸向炉缸中心,并尽量减少风口之间炉料的凝滞区〔多风口设计思想〕(下)2〕熄灭带是炉缸煤气的发源地,熄灭带的大小影响煤气流的初始分布。熄灭带伸向中心,那么中心气流开展,炉缸中心温度升高;相反,熄灭带小,边缘气流开展,中心温度较低,对各种反响进展不利。炉缸中心不活泼和热量缺乏,对高炉顺行极为不利。因此,从煤气流分布合理和炉缸中心温度充足的角度来说,也希望熄灭带向中心延伸〔上〕盘旋区截面积占炉缸截面积的47~48%时高炉消费目的最好,小高炉可达50%。对d=6.8~13.4m〔相当于1000~4000m3〕的高炉,盘旋区深度L=0.424+0.068d+0.003d2。4.下部调剂原理定义:单位时间内进入高炉的鼓风质量所具有的动能,它是选择风口直径的主要根据。鼓风动能大,熄灭带加长,有利于吹透中心。,〔〕—单位时间的鼓风质量〔〕—风速〔〕每秒钟进入一个风口的鼓风质量:〔〕—高炉风量〔〕—标态下空气重度〔1.2875〕—送风风口个数—重力加速度〔〕影响熄灭带的要素---鼓风动能、熄灭反响速度、炉料分布情况1〕鼓风动能及其与熄灭带的关系假设风温为T〔=273+t〕,风压,那么每秒进入一个风口的实践鼓风体积:注:为吹入高炉的实践风量〔Nm3/min〕,用每天烧掉的焦炭量来反推:每天参与高炉的焦炭高炉中参与1吨焦炭需求的风量——每天参与高炉的焦炭〔t〕;——焦炭固定碳含量〔%〕;——风口前烧掉的碳量占入炉总碳量之比,那么高炉内每参与1吨焦炭所需求的风量普通动摇在2500~3000Nm3/t,假设取当休风率为0时:,即每天装入高炉内的焦炭的2倍。日本统计了大型高炉鼓风动能与高炉有效容积的关系:我国:1000m3以上的高炉鼓风动能在40~70kW300m3左右的高炉30~40kW100m3以下的小高炉10~15kW55m3高炉6~9kW13m3高炉2~5kW随冶炼强度升高,鼓风动能相应减小。2〕影响鼓风动能的要素鼓风动能熄灭带大小a〕风量E=f(V2)b〕风温E=f(T2)c)风压E=f(1/p2)d)风口截面积E=f(1/S2)5熄灭温度及炉内温度分布〔1〕实际熄灭温度定义:风口前焦炭熄灭产生的煤气所能到达的最高温度,即假定风口前焦炭熄灭放出的热量全部用来加热熄灭产物时所能到达的最高温度。——风口前碳熄灭成CO放出的热量〔kCal/t〕铁〕;——鼓风带入的物理热〔kCal/t铁〕;——燃料带入的物理热,包括进入高温区的焦碳的物理热〔1500℃)、煤粉的物理热;——鼓风和喷吹煤粉中的水分解吸热〔kCal/t铁〕;——煤粉分解吸热〔kCal/t铁〕;——CO和N2的比热,;——H2的比热,;——炉缸煤气中CO、N2、H2的体积,m3/tFe。实际熄灭温度可达1800~2400℃,它代表风口区最高温度,其数值表示了传热推进力的大小,但它并不代表炉缸铁水温度和生铁含硅量的高低。〔2〕影响实际熄灭温度的要素在实践运用过程中,各高炉根据实践消费数据,以及按上述定义公式计算的,经过回归得到运用方便的阅历公式:日本君津厂:日本中山厂:澳大利亚BHP:以上各式中:——鼓风温度〔℃〕;
——鼓风富氧量〔m3/1000m3鼓风〕;——喷吹重油量〔kg/1000m3鼓风〕;——喷煤量〔kg/1000m3鼓风〕;——鼓风湿份〔g/m3〕首钢1高炉:武钢1高炉:kg/tg/m3从以上公式可以看出:富氧1%:提高实际熄灭温度40~45℃;湿份1g/m3:影响实际熄灭温度6℃左右;↓100℃风温:提高影响实际熄灭温度75~80℃;喷煤10kg/t:影响实际熄灭温度15~20℃;↓高炉冶炼过程中必需维持一定的实际熄灭温度才干保证顺行。过低:传热推进力小,渣铁温度缺乏,流动性差,脱硫困难;过高:炉缸煤气体积膨胀,压差升高,且大量产生SiO。日本高炉实际熄灭温度与高炉有效容积的关系有效容积(m3)10002000300040005000下限21152170230023002350上限22402300242024202470首钢1号高炉燃料比与实际熄灭温度的关系时间1950.61954.31957.51966.21980.1燃料比(kg/t)1050892789532515(℃)19302056216422072263燃料比↓——要求↓喷煤100kg/t,需求补偿风温130~180℃武钢100℃风温可添加喷煤59kg/t(100kg/t169℃)实际熄灭温度与焦比关系①K=600kg/t、C固=82%、冶炼1吨生铁需在风口前熄灭的碳量=600×0.82×0.7=344.4kg鼓风物理热燃料带入高温区的物理热水份分解热煤粉分解热(风口前碳素熄灭率)②当K=700kg/t时,结论:t理与焦比关系不大,但焦比升高,吨铁煤气量添加,每吨生铁的总热量添加,炉子变热。
〔3〕炉缸内温度分布炉缸内温度分布当炉缸中心渣铁温度<1400℃时,炉缸中心堆积,排泄渣铁才干变差4.2煤气运动1煤气上升过程中体积、成份变化炉内煤气成分变化炉缸煤气中CO%达35%左右,高炉喷煤及富氧后,CO%可达40%以上。CO︰煤气上升过程中,首先吸收直接复原产生的CO,但至中温区,由于间接复原反响耗费了CO,故CO先添加后减少。CO2:在炉缸、炉腹处几乎为零,以后由于间接复原和石灰石分解才逐渐添加。由于间接复原时气体体积不变,图中虚线之左半部为间接复原产生,而右半部为石灰石分解产生。H2:风口前鼓风中的水分分解、喷吹煤粉中的H2、焦炭有机物和挥发份中的H2是H2的主要来源,它在上升过程中有1/3~1/2参与复原反响变成水。CH4:在高温下少量H2与C反响生成CH4,上升过程中又参与了焦炭挥发份中的CH4,但数量很少。N2:鼓风带入的N2,焦炭有机物和挥发份中的N2,上升过程中N2的绝对量不变。炉顶煤气成分:CO2CON2H2CH416~22%18~2555~57~4~0.3CO2+CO≈40%普通情况下鼓风量:炉缸煤气量:炉顶煤气量=1:1.21:1.3~1.42与炉顶煤气成分有关的现场计算炉顶煤气是炉内反响的产物,它的变化反响了炉内冶炼情况的变化,所以用炉顶煤气成分可以推断炉况的变化。设炉顶煤气成分:CO2%、CO%、N2%、H2%、CH4高炉焦比:K〔kg/t〕,焦炭含碳量C%K生铁含碳:[C]石灰石量:Φ〔kg/t〕,石灰石中的CO2含量为CO2%Φ喷煤量:M〔kg/t〕,煤粉含碳C%m;〔1〕根据碳平衡计算1吨生铁的煤气量1m3煤气含碳量=1吨生铁生成的煤气中的碳=气化的碳量那么,1吨生铁的煤气体积〔2〕根据N2平衡计算风量忽略焦炭及煤粉中的N2:知道后也可以反推风口前熄灭的碳量风口前碳素熄灭率风口前焦炭熄灭率例题:某高炉冶炼条件如下:焦比:K=650kg/t、C%K=82%、C炉尘=10kg/t熔剂:Φ=120kg/t,CO2%φ=43%鼓风湿度=1%炉顶煤气成分:CO212.3%、CO27.2%、CH40.3%、N257.7%求:吨铁煤气量、风量及风口前碳素熄灭率?解:吨铁煤气量吨铁风量风口前碳素熄灭率热量传送给炉料3高炉内换热过程煤气上升过程中本身温度下降炉料下降过程中温度升高—————→高炉下部:煤气温度比渣铁温度高>500℃煤气温度>2000℃,渣铁温度1450~1550℃高炉上部:煤气温度比炉料温度高100~250℃概念:水当量〔热容比〕W:
流股每小时流量(质量或体积)与相应流股比热的乘积,即流股每升(降)温1℃所吸收(放出)的热量。由于散料在热交换时还有化学反响,所以把比热的概念加以扩展,它包括了化学反响热效应对炉料温度变化的影响。Wm=Gm·CmGm:每小时经过高炉某一截面的炉料质量〔t/h〕Wg=V·CgV:每小时经过高炉某一截面的煤气体积〔m3/h〕水当量在高炉高度上的变化:HW
高炉上下的煤气成分及体积流量稍有变化,引起Wg变化不大;煤气水当量:Wg炉料水当量:Wm高炉上部水当量较小〔炉料吸热、水分蒸发、石灰石分解吸热+间接复原放热〕;高炉下部炉料水当量很大〔直接复原大量吸热、熔化渣铁及过热吸热〕高炉上部:
高炉中部:空区高炉下部:理想高炉纵向温度分布〔1〕上部热交换区:矿、焦进入高炉后温度很快升高,煤气温度那么下降很慢,到900~1000℃范围内,二者温差很小,热交换趋于停顿:特点:炉料温度升高〔950-20〕=930℃>煤气温度降低〔950-250〕=700℃根据热平衡关系:(20℃炉料温度250℃煤气出口温度950℃空区温度)〔2〕下部热交换区煤气温度降低:2000-950=1050℃(950经过空区后的温度)炉料温度升高:1550-950=600℃炉料进展直接复原大量吸热、渣铁熔化及过热耗热根据热平衡关系:〔3〕热交换空区〔热贮藏区〕大、小高炉空区高度比较煤气与炉料的温差很小〔25~50℃〕,空区的温度普通在850~1000℃。不加熔剂时为900~1000℃(取决于直接复原开场温度),加大量熔剂时为石灰石大量分解温度850~1000℃。空区起着缓冲作用,如高炉偶尔间坐料或崩料,不会影响到焦比。空区越大,高炉热惯性越大、动摇就越小;相反,空区越小,高炉热惯性小,炉况容易动摇。〔4〕炉顶煤气温度和渣铁温度上部热交换区:上部换热区a〕焦比K:K↓煤气量↓b)富氧:煤气量↓c)风温:风温↑K↓d)喷煤:煤气量↑e〕热烧结矿:f〕冶炼强度:同步变化〔料速↑〕〔焦炭耗费量/天〕g)炉顶打水:下部热交换区:下部换热区a〕焦比K:↓煤气量↓K↑b)富氧:煤气量↓c)风温:风温↑K↓d)喷煤:煤气量↑煤气量↓煤气量↓4.3炉料运动矿石:块矿、烧结矿、球团矿、锰矿焦炭熔剂:石灰石附加物:碎铁批料大高炉:负荷可达3.5~4.5中小高炉:负荷可达2.5~3.0负荷大小决议于:〔1〕矿石复原性;〔2〕风温程度;〔3〕喷煤量;〔4〕冶炼铁种;〔5〕焦炭质量;〔6〕操作程度确定料批的顺序:〔1〕先确定批焦〔2〕根据负荷确定批矿〔3〕根据炉渣碱度确定石灰石用量4.3.1炉料下降1.炉内存在使其下降的空间(必要条件)(1)焦炭在风口前熄灭占35~40(2)焦炭参与直接复原反响占15%(3)矿石、熔剂熔化时体积收缩占30%(4)定期排放渣铁重点(1)焦炭熄灭:添加风量,可使炉料下降变快;(2)勤放渣铁:使炉缸腾出空间2.炉料下降的力学条件(充分条件)
1〕决议炉料下降的力:
其中:—炉料自重—炉料与炉墙之间的摩擦力—料块之间的内摩擦力—煤气经过料柱时的阻力损失〔压降〕称为炉料有效分量称为炉料有效分量系数
散料料柱的特点:炉料顺利下降难行、悬料
不同于普通的大块固体,内部无结合力不同于普通的流体,有很大的内摩擦力雅森公式〔Janssen〕:料柱下降力的另一表达式式中:—散料在h处所受的静压力,
D—散料柱直径,mH—散料柱总高度,m—散料柱内气流产生的阻力损失,—散料堆比重,—炉料与炉墙的摩擦系数,取0.7—炉料的侧压力系数〔炉料与炉料之间的摩擦系数〕,取0.5—压降梯度,相当于把炉料放入比重为的流体中所受的浮力当炉料顺利下降难行、悬料2〕影响的要素(1)炉身角和炉腹角炉身角越小炉腹角越大高炉越矮胖,(2)料柱高度在一定范围内:料柱高度↑H超越一定值后且会构成料拱(3)风口数目风口数目添加,熄灭带程度投影面积占炉缸面积比例大,料柱松动,炉料之间内摩擦系数下降;(4)炉料堆比重高炉喷煤粉后,焦炭负荷升高—(5)高炉操作形状炉渣粘度大、炉墙不平〔结厚、结瘤〕、煤气分布失常,4.3.2影响的要素料柱压差的表达式=P缸-P喉=P热-P顶根据流膂力学,气体经过散料层时的阻力损失为:〔1〕式中:—高度为H的料柱内的阻损—上升气流的重度—上升气流速度—散料层空隙率—颗粒外形系数
—颗粒平均直径〔m〕—与雷诺数有关的常数—重力加速度9.8Ergun经过实验研讨指出:—流体动粘度将(2)、(3)代入(1)——粘度动能气体密度〔kg/m3〕气体粘度——〔2〕〔3〕〔4〕〔5〕上式中第一项表示由流体粘度产生的阻力,在层流流动〔低流速〕时起作用;第二项表示由流体动能产生的阻力,在高速气流〔紊流〕时起决议作用。高炉中煤气实践流速高达10~20=1000~3000〔6〕〔7〕K称为透气性指数,是散料特性的函数。现场用K=V风/代表料柱的透气性指数。4.3.3改善料柱透气性上式中第一项表示由流体粘度产生的阻力,在层流流动〔低流速〕时起作用;第二项表示由流体动能产生的阻力,在高速气流〔紊流〕时起决议作用。高炉中煤气实践流速高达10~20=1000~3000现场用K=V风/代表料柱的透气性指数,是散料特性的函数。不同炉料的透气性指数炉料息止角(mm)K焦炭36~4400.5390.724球团28~3200.3612.70.920.48烧结32~3600.487~100.650.594.3.3改善料柱透气性不同炉料的透气性指数炉料息止角(mm)K焦炭36~4400.5390.724球团28~3200.3612.70.920.48烧结32~3600.487~100.650.59公式〔6〕1)只适用于块状带;2)只适用于固定床;3)矿、焦分层计算。但实践测定值>实际计算值,主要是在矿、焦界面上发生了渗混景象。4)5)1改善块状带透气性a〕炉料颗粒尺寸筛除<5mm的颗粒。小颗粒比外表积大,气流与颗粒间产生的摩擦阻力大。但颗粒太大影响其复原性,故普通矿粒下限取8mm,上限取45mm。b〕料柱空隙度炉料颗粒尺寸差越大,越小,大块料体积占70%时,最小。40~25mmk=0.625i〕分级入炉25~12mmk=0.4812~5mmk=0.417ii)减少粉末:-5mm
实践空隙率在30~40%c〕冶炼强度I↑—上升气流速度煤气量e〕喷煤焦炭负荷iii〕提高矿石和焦炭强度d〕高风温—煤气体积膨胀—料柱透气性——f〕富氧—煤气量——g〕高压操作—h〕加湿鼓风——〔上升气流速度〕
2改善软熔带透气性
正常的填充床中,料柱的阻力与气流实践流速的关系为:或按阅历高炉中吹出管道时呈部分流态化。液泛—炉腹有液态渣铁充填时的流膂力学景象液态渣〔铁〕贴壁流动,气体在中心经过,两者不发生矛盾液渣数量增多,直至下泄困难,并开场在料层内积聚,;当液相数量积聚到一定数量时,其质量产生的浮力,液体下泄,料层,此过程反复出现.煤气以气泡方式穿越渣层,,煤气将泡沫渣向上吹,因上部温度低,粘度聚增,直至凝固,呵斥下部悬料,
在逆流接触的气-液反响器或传质分别设备中,气体从下往上流动,当气体的流速增大至某一数值,液体被气体阻拦不能向下流动,愈积愈多,最后从塔顶溢出,称为液泛。
大渣量、高冶炼强度操作、焦炭质量差时能够出现液泛景象。悬料因子公式中:—煤气流空炉速度,cm/s;—散料空隙率—重力加速度980cm/s2;—煤气和炉渣的密度,g/cm3;—炉料比外表积,cm2/cm3;—炉渣粘度,厘泊流量比液体与气体的空炉速度比L、G——分别为液体与气体的空炉质量流速〔g/〕cm2.s高炉是周围侧面进风,发生液泛景象的压力降要比自然底部进风高出5倍。所以实践高炉炉腹处发生液泛景象的流速还是比较高的。大渣量、高冶炼强度操作、焦炭质量差时能够出现液泛景象。流量比悬料因子
冶炼强度高时下部压力添加较快,而上部压力添加较慢,阐明下部料柱透气性是限制要素。高炉喷吹煤粉时,K↓高炉富氧大喷煤的前提是提高入炉矿石档次,减少渣量。3软融带外形“∧〞型软融带:冶炼强度高、中心气流大、炉缸活泼、热量充足的大型高炉。这种软融带由于中心气流开展、炉缸活泼,软融带高度高、面积大、焦窗数量多,对煤气阻力小,可得到较好的消费目的。同时煤气流相对集中在中心,边缘气流较小,可减轻边缘热负荷和煤气流对炉墙的侵蚀,有利于延伸高炉寿命。“V〞型软融带:冶炼强度低、中心气流小、炉缸不活泼、热量不充足的小型高炉。这种软融带由于中心气流不开展,软融带高度低、面积小、焦窗数量少,对煤气阻力大,消费目的较差。同时煤气流产生边缘效应,中心热负荷加重,煤气流对炉墙的侵蚀严重,不利于延伸高炉寿命。“W〞型软融带:冶炼强度高、中心气流大、炉缸活泼、热量充足的大型高炉。这种软融带是适当开展中心和边缘气流的结果,能坚持高炉顺行,改善煤气能量利用,不能进一步强化和降低燃料耗费。软融带愈窄、焦炭层数愈多、夹层愈高,空隙率愈大,那么软溶带透气阻力愈小,透气性愈好。“中心装焦〞:日本钢管公司提出的理想煤气分布煤气走中心,减小整个料柱阻力;边缘较均匀的煤气分布改善煤气热能利用;抑制边缘气流,减小炉体热损失。4.3.4煤气流合理分布两股煤气流1〕煤气流经过料层时的阻力损失结论:煤气流经过烧结矿层产生的阻力损失是经过焦层时阻力损失的8倍单位矿石经过的煤气量相等,但料柱阻力最大。煤气热能和化学能得到最大限制利用,但煤气阻力最大,对高炉顺行不利。大量煤气经过阻力小的焦层,料柱阻力最小,但单位矿石经过的煤气量最少。煤气阻力最小,高炉顺行,但煤气热能和化学能利用最差。焦炭多的一侧经过的煤气多。煤气能量利用界于上述两者之间,煤气阻力界于上述两者之间。这种布料方式兼顾了高炉顺行和煤气能量利用。2〕炉料分布方式与煤气流阻力的关系3〕炉喉煤气成分检测方法煤气走的多的地方:焦炭布得多,CO2↓、温度↑煤气走得少得地方:焦炭布得少,CO2↑、温度↓煤气是热量的载体,煤气流通多的地方,温度也较高。CO2高的部位,煤气流经少,温度低,透气性差。曲线2:边缘轻、中心重,由于边缘流过的煤气多,称为边缘气流型;〔原燃料条件差时〕4〕高炉内煤气的合理分布曲线3:中心轻,边缘重,称中心气流型〔大高炉用〕;曲线1:两股气流相当,称双峰曲线。煤气曲线分析:a〕b〕曲线平坦程度,用来衡量煤气利用情况c〕曲线对应性:看炉内煤气分布能否均匀,有无管道或者长期某侧透气性差,甚至出现炉瘤病症的煤气曲线。d〕分析各点煤气的CO2%:由于煤气曲线上各点的间隔不相等,而各点所代表的圆环面积不一样,所以各点的CO2%值对应的煤气利用不一样,其中2点最大,1、3点次之。煤气最高点从3点移到2点,虽然最高值相等,也能使煤气能量利用改善。4.3.5上部调剂原理下部----供风、喷吹、富氧等上部----炉料〔外形、大小、加料方式等〕1〕影响炉喉布料的要素种类---粒度---自然堆角---料层厚度装料设备---钟式、旋转溜槽炉料堆角首钢1号高炉不同料线深度时的炉料堆角炉料H=1.7mH=1.9mH=2.1m矿石30.8031.150-31.50焦炭28.320-30.450320矿石在炉内堆角大于焦炭堆角武钢1号高炉实测炉料堆角烧结矿批重焦炭批重烧结矿堆比重焦炭堆比重自然堆角H=1.6m时的堆角炉料堆角烧结焦炭3008’28014’24024’18030’2〕装料制度a料线高炉正常操作时,料线深度普通是固定不变的,并且料线深度普通不超越碰撞点。在其它条件不变时,料线越深,矿石堆尖越接近边缘,相应加重了边缘。因此,为加重边缘,可适当降低料线。b.批重当料线一定时,炉料堆尖位置也一定,此时炉料在边缘和中心的厚度决议于批重的大小。批重特征数:D越大阐明炉料在边缘分布越多。矿石批重过小:中心布不到矿石,边缘矿石也很少,出现边缘和中心两头轻的煤气分布。
临界矿石批重:矿石刚好能布到高炉中心〔=0〕。批艰苦于临界批重时,随矿批添加,矿石在炉内分布均匀,D变小,相对加重中心。因此,减小批重加重边缘,添加批重加重中心。批重过大时:炉料在边缘和中心的厚度均很大,此时不仅加重中心,也加重边缘,出现边缘、中心两头堵的煤气分布添加了料柱阻力,不利于高炉顺行。合理批重应选择在缓变区,普通中心矿层150~300mm,=2.5~4c〕装料顺序〔钟式高炉〕分装——矿石和焦炭分开两次入炉同装——矿石和焦炭只开一次大钟同时入炉双装——将两批矿石和焦炭分别加在一同,一次装入炉内正装:边缘重、中心轻(焦、矿)正同装正分装倒装:边缘轻、中心重(矿、焦)倒同装倒分装由于炉内边缘下料较快,经过一段时间后料面变平坦,先入炉的料首先在炉墙边上堆起一个堆角,以后以平行层往炉喉料面铺开,所以先入炉的料边缘布得较多,而后入炉的料在曾经构成的堆角上那么较多滚向中心。所以正装加重边缘,倒装加重中心。分装时,后下料与先下料之间有一段时间间隔,在这段时间内,料面变得平坦一些了,所以较同装有更多的料落在边缘。
上述规律的前提是:—————边缘最重边缘最轻—
出现布料反常:正装加重中心,倒装加重边缘装料次序的改动不影响煤气分布。同装改分装时,界面效应减小,能改善料柱透气性。正分装界面效应最小。装料方法:将5~7批料组成一个循环无料钟炉顶布料方式无料钟炉顶的布料操作旋转溜槽:旋转、倾动,炉料可布到炉喉截面的任一位置。合理批重下限炉喉直径m2.53.54.75.96.77.38.29.81111.4高炉容积m31002506001200150020003000400050005500进入缓变区批重t4.57.912.8202734426387964.4高炉能量利用计算1直接复原度计算2配料计算3物料平衡4热平衡计算5Rist操作线1直接复原度计算〔碳平衡计算法〕Fe2O3Fe3O4FeOFeCOCO、Ca.计算COFeOCFeH2FeO+CO=Fe+CO256121000[Fe]×ri=X气化碳量=K×C焦%+M×C煤%+C附加物+C熔剂-C生铁-C炉尘(煤气中的总碳量)K、M——分别是焦比和煤比(Kg/t)C焦%、C煤%—分别为焦炭和煤粉中的总碳量〔%〕〔包括挥发分中CO、CO2、CH4中的碳〕C附加物—碎铁带入高炉中的碳=碎铁量〔Kg/t〕×碎铁含碳量〔%〕C熔剂—熔剂分解出的CO2中的碳=Ø×CO2%Ø×12/44C生铁—1000[C]C炉尘—炉尘量〔Kg/t〕×炉尘含碳量〔%〕CO2气化的碳CO炉顶煤气,其中变成CO2的为:CH4炉顶煤气中的CO2中的碳扣除部分:①Fe2O3FeO+CO2
②MnO2MnO+CO2A为矿比〔Kg/t〕③石灰石和焦炭挥发分中的CO2中的碳:12/44(Ø×CO2%溶剂+K×CO2%焦炭)b计算FeO+H2=Fe+H2OH还—参与复原反响的H2β—Fe3O4+H2=FeO+H2O①FeO+H2=Fe+H2O②β为参与反响②的H2的比例β=0.6~0.7H还=入炉总H2量(H2总)×50%(=50%为H2在高炉中的利用率)入炉总H2量〔H2总〕=各种燃料带入高炉的H2的量〔H2燃料〕+2/18×〔H2O鼓风+H2O煤粉〕2配料计算目的:根据知的原料条件和冶炼条件,确定矿石和熔剂的耗费量,为冶炼规定成分的生铁获得最适宜的炉渣成分。a〕原料成分原料成分表〔%〕
TFeMnPSFe2O3FeOMnO2MnOCaOMgOSiO2Al2O3P2O5FeS2FeSSO2烧损CO2
∑烧结矿52.80.0930.0470.03155.3018.180.1210.803.749.761.000.110.090.9100天然矿43.000.1650.0210.13451.109.200.269.002.1016.342.320.050.259.38100混合矿52.490.0950.0470.03455.1417.90.010.1210.763.709.961.050.110.010.091.15100石灰石0.0040.00340.6812.151.380.340.010.0145.4100炉尘48.210.1120.0370.08761.106.800.1455.211.9010.048.540.0850.24C5.94100注:配矿比烧结矿:天然矿=97:3b〕焦炭成分焦炭成分表〔%〕Cs灰份12.17%挥发份0.9%有机物1.3%∑游离水全硫SiO2Al2O3CaOMgOFeOFeSP2O5
CO2COCH4H2N2H2N2S85.635.654.830.760.120.750.050.010.330.330.030.060.150.40.40.51004.80.52c〕喷吹物成分煤粉成分表〔%〕
成分品种CH2O2H2ON2S灰分%21.25ΣSiO2Al2O3CaOMgOeO煤粉67.844.354.050.790.420.6611.487.420.600.301.45100d〕焦比450kg/t(干焦)煤比75kg/t炉尘量50kg/te)元素分配率各种元素分配率表元素FeMnPSTi生铁0.9970.51.00.02~0.03炉渣0.0030.500.98~0.97煤气0000.06注:冶炼铸造生铁时,Mn的收得率可达0.6~0.75;炉渣碱度高时,Mn的收得率也提高,如宝钢高炉渣R=1.25时,ηMn=0.7~0.75。f)生铁成分〔炼钢生铁〕设[Fe]=95%,[Si]=0.7%[S]=0.03%,估计生铁中的其它成份如下:[Si]=0.7%[S]=0.03%[P]=0.085%[C]=4.3-0.27×[Si]-0.32×[P]+0.03×[Mn]-0.032×[S]=4.1[Fe]=100-[C]-[Si]-[Mn]-[P]-[S]=94.99%经过生铁成分预算,如某种元素成分超出铁种范围,如[P]超越制钢生铁上限,那么应改动配矿,减少高磷矿配比。预算生铁成份表(%)成份SiMnSPCFe∑%0.70.0860.030.0854.194.99100g〕炉渣碱度R高碱度低MgO渣:R2=1.2~1.25,MgO6~8%(脱硫渣)低碱度高MgO渣:R2=0.95~1.1,MgO>10%(<15%)<排碱渣里取R=1.03.h〕碎铁参与量:P碎铁=0以下以冶炼一吨生铁为单位做配料计算:⑴根据铁平衡求矿比A(kg/t)〔2〕根据炉渣碱度计算石灰石量ΦSiO2SiO2矿=1854.33×9.96%=184.63kgSiO2焦=450×5.65%=25.43kgSiO2煤=75×11.48%=8.61kgSiO2尘=50×10.04%=5.02kgSiO2生铁=1000[Si]×60/28=15kgSiO2碎铁=0CaOCaO矿=199.46kgCaO焦=3.42kgCaO煤=0.45kgCaO炉尘=2.61kgCaO碎铁=0CaO有效=CaO%Φ-R×SiO2%Φ=39.26%对于大型高炉,要求炉料中不加生石灰,此时首先要确定烧结料矿配比:设冶炼一吨生铁需求的高碱度烧结矿Xkg、块矿Ykg铁平衡:Fe%烧结×X+Fe%块矿×Y=Fe生铁+Fe渣+Fe尘-Fe焦-Fe煤碱度平衡:解上述方程组:烧结矿:、块矿:〔3〕炉渣成分及渣量硫进入渣中的硫量:S渣S渣=S矿+S焦+S煤粉+S石灰石-S生铁-S煤气S矿=1854.33×0.034%=0.63kgS焦=450×0.52%=2.34kgS煤粉=75×0.66%=0.5kgS石灰石=8.94×0.003%=0ΣS入=S矿+S焦+S煤粉+S石灰石为硫负荷S生=1000[S]=0.3kgS煤气=ΣS入×0.06=0.21kgS生=0.63+2.34+0.5-0.3-0.21=2.96kg/t生铁渣中FeO量渣中MnO量渣中SiO2量渣中CaO量渣中Al2O3量渣中MgO量渣中K2O、Na2O量炉渣中排碱率按80~85%计算注:渣中S全部以CaS形状存在。因此,渣中的Ca2+是以CaO和CaS两种形状存在,但在计算渣量时CaO量包括了CaS中的Ca2+,即把CaS中的Ca2+折合成相应Ca2+量的CaO量。由于CaS与CaO的分量差刚好为S渣/2,因此在计算渣量时,S只计入一半。终成分表成份FeOMnOSiO2CaOAl2O3MgOS/2ΣRkg3.681.14198.77204.3644.9770.472.96/2524.871.03%0.700.2237.8738.948.5713.420.28100校验炉渣物性:将四元总和调成100%37.87+38.94+8.57+13.42=98.8%SiO2’=37.87/0.988=38.33%CaO‘=38.94/0.988=39.41%Al2O3’=8.57/0.988=8.67%MgO'=13.42/0.988=13.58%(4)生铁成分校验(a)生铁含磷量:(b)生铁含硫量:[S]=0.03%(c)生铁含硅量:[Si]=0.7%(d)生铁含锰量:(e)生铁含铁量:[Fe]=94.99%[Fe]=0.997×(A×Fe%矿+K×Fe%焦+M×Fe%煤-炉尘量×Fe%尘)/1000(f)生铁含碳量:[C]=100-[Si]-[Mn]-[P]-[S]-[Fe]=4.093%生铁成分表FeSiMnPSCΣ94.990.70.0880.0890.034.093100以下物料平衡计算,必需以上表为根据。3物料平衡物料平衡是在配料计算的根底上编算的,计算内容包括风量、煤气成分及煤气量,列出收支平衡表。它能协助了解冶炼过程物化反响,检查配料计算的正确性,校核高炉冷风流量表的误差,核定煤气量和煤气成分,并能检查现场炉料称量的准确性,进一步为热平衡作预备。3-1原始条件(2)鼓风湿度,取大气自然湿度12g/Nm3(f=1.5%)武汉地域气候资料〔55年平均〕月份123458101112湿度g/m3679.814.519.929.315.210.510.7(1)选定直接复原度:可以根据类似条件下的煤气成分来计算包钢1#BF实测:rd=0.5915梅山1#BFrd=0.4743本例题选rd=0.45生成CH4的碳量喷煤时:占焦炭和煤粉固定碳量的1.2%C+2H2=CH4纯焦冶炼时:占焦炭固定碳量的0.5~1.0%3-2根据碳平衡计算风量〔Nm3/t生铁〕焦炭C碎铁碳C炉尘碳C耗碳生铁CO2+C=2COC+2H2=CH4耗碳FeO+C=Fe+CO
MnO+C=Mn+COC+1/2O2=CO〔1〕风口前熄灭的碳量C风〔kg/t铁〕C风=C焦+C煤+C碎铁-C生-C直-CCH4-C尘入炉总固定碳量:C总=C焦+C煤-C尘(a)C焦=450×85.63%=385.335kg(b)C煤粉=75×67.84%=50.88kg(c)C碎铁=0(d)C炉尘=50×5.94%=2.97kgC总=385.335+50.88-2.97=433.245kg(e)C生铁=1000[C]=40.93Kg(f)C直=CSi+CMn+CP+CFe+CCO2+CSSiO2+2C=Si+2COMnO+C=Mn+COP2O5+5C=2P+5COFeO+C=Fe+COCO2+C=2COFeS+CaO+C=Fe+CaS+CO1232g〕CCH4=C总×1.2%=433.245×1.2%=5.2kgC风=385.335+50.88-2.97-40.93-100.87-5.2=286.245kg风口前熄灭的碳量占入炉总碳量的比:〔2〕风量计算V风a)鼓风中的氧=0.21+0.29×f+0.79×O22C+O2=2COb)熄灭C风量的碳耗费的氧量=c)喷吹物中提供的氧〔煤分中的H2O和有机物中的O2〕3-3计算煤气成分和煤气量煤气体积=VCH4+VH2+VCO2+VCO+VN2C+2H2=CH4(1)甲烷体积VCH4=由碳素反响生成的CH4+焦炭挥发分中的CH4(2)H2的体积VH2VH2=入炉总H2-参与复原反响的H2-生成CH4耗费的H2a)参与复原反响的H2=入炉总H2×40%=32.624m3(参与复原反响的H2为入炉总H2的40%)c)生成甲烷反响耗:VH2=81.56-32.624-21.47=27.47m3C+2H2=CH41244.8CCH4x(3)CO2体积VCO2=间接复原生成的CO2+石灰石分解出的CO2+焦炭挥发分中的CO2+混合矿中的CO2a)间接复原反响生成的CO2Fe2O3+CO=2FeO+CO2Fe2O3+H2=2FeO+H2OFeO+CO=Fe+CO2FeO+H2=Fe+H2OMnO2+CO=MnO+CO2MnO2+H2=MnO+H2OFe2O3+CO=2FeO+CO216022.4(A×Fe2O3%矿-炉尘量×Fe2O3%尘)×(A×Fe2O3%矿-炉尘量×Fe2O3%尘)FeO+CO=Fe+CO25622.4(1-rd)(1000[Fe]-Fe碎铁)yy=(1-rd)(1000[Fe]-Fe碎铁)×22.4/56MnO2+CO=MnO+CO28722.4A×MnO2%矿ZZ=A×MnO2%矿×22.4/87间接复原生成的CO2=X+Y+Z-参与复原反响的H2=318.37m3b)石灰石分解的CO2石灰石分解的CO2的50%进入煤气中石灰石分解的c)焦炭挥发分中的d)混合矿中分解出的VCO2=331.95(4)CO的体积VCOVCO=风口前熄灭生成的CO+各元素直接复原反响生成的CO+焦炭及煤粉中的CO–间接复原耗费掉的COa)风口前熄灭生成的b)各元素直接复原反响生成的c)焦炭及煤粉中的d)间接复原耗费掉的CO=间接复原生成的CO2量=318.37m3VCO=534.32+188.3+1.32–318.37=405.57m3(5)N2的体积VN2VN2=鼓风中的N2+焦炭及煤粉中的N2=V风×〔1-f〕×0.79+(K×N2%焦+M×N2%煤)×22.4/28=960.84+2.45=963.29m3炉顶煤气成分表成分CO2CON2H2CH4ΣV煤气/V风m3331.95405.57963.2927.4710.941739.22%19.0923.3255.391.580.631001.413-4编制物料平衡表〔1〕计算鼓风质量〔鼓风实践含氧〕(2)计算煤气质量煤气分量=1.365×1739.22=2373.63kg(3)煤气中的水a)H2参与复原反响生成的水=32.624b)焦炭中的H2O=c〕混合矿带入的水:结晶水物料平衡表
收入kg支出kg1混合矿1854.331生铁10002焦炭(湿)468.752炉尘503石灰石8.943炉渣524.874煤粉754煤气2373.635鼓风1580.55水分45.856碎铁0Σ3987.523994.354热平衡计算〔全炉热平衡〕热平衡计算的目的是为了了解高炉内热量供应和耗费分配情况,碳的热能利用系数和高炉有效热量利用系数,以确定高炉冶炼过程中热能利用的好坏,找出改善热能利用的途径。供应高炉的热量之和应该等于各项热量耗费之和。知条件:风温t风,炉顶煤气温度t顶,烧结矿温度t烧结热收入项:〔1〕碳的氧化放热Q1kcal〔2〕鼓风物理热Q2kcal〔3〕成渣热Q3kcal〔4〕氧化放热及CH4生成放热Q4Kcal〔5〕炉料带入的物理热Q5Kcal热支出项:〔1〕氧化物分解热Q1’〔2〕脱硫耗热Q2’〔3〕碳酸盐分解热Q3’〔4〕水分分解热Q4’〔5〕炉料游离水的蒸发热Q5’〔6〕铁水带走物理热Q6’〔7〕炉渣带走热Q7’〔8〕喷吹物分解热Q8’〔9〕炉顶煤气带走热Q9’〔10〕冷却水带走及其它热损失Q10’4-1冶炼一吨生铁的热收入Q1=4275×VCO2+1254×VCOkcalC+O2=CO2+95.76Kcal/molC(7980Kcal/KgC)2C+O2=2CO+56.16kcal/molO2VCO2=VCO2煤气-VCO2炉料带入VCO2炉料带入=焦炭挥发分中的CO2+混合矿烧损中的CO2+石灰石分解出的CO2×50%+煤粉中的CO2(虽然它在风口前曾经烧掉,但在前面计算煤粉中含氧量时没有思索煤粉中CO2中的氧,故这里应计入)VCO=VCO煤气-VCO炉料带入〔焦炭挥发物中和煤粉中的CO〕〔2〕鼓风物理热Q2Q2=〔V干风×C干风+V水汽×C水汽〕×t风温V干风、V水汽——分别为鼓风中干风体积和水汽体积〔Nm3/吨生铁〕C干风、C水汽——分别为干风和水汽的比热〔kcal/Nm3℃〕不同温度下干风、水汽之比热〔kcal/Nm3℃〕温度℃70080090010001100120013001400干风比热0.32710.33110.33450.33760.34050.34330.34580.3481水汽比热0.39150.39760.40370.40990.41610.42210.42780.4334〔3〕成渣热Q3炉料中以碳酸盐方式存在的CaO和MgO,在高炉内生成钙铝硅酸盐时,每kg能放出270kcal/kg。混合矿中的烧损,主要来自烧结矿中未矿化的碳酸盐和天然矿中的碳酸盐,1mol碳酸盐可分解出1molCO2,因此可根据混合矿中的烧损量中的CO2计算出混合矿中的碳酸盐量。石灰石中的CaO+MgO量=Φ×〔CaO%Φ+MgO%Φ〕Q3=[(CaO+MgO)混合矿+〔CaO+MgO〕熔剂]×270Kcal/吨生铁〔4〕氢的氧化放热及CH4生成时的放热Q4氢氧化放热QH2=2581×参与复原反响的氢量〔m3〕(KCal)每m3H2氧化生成水时的放热量生成CH4时放热QCH4=1124×生成甲烷体积Q4=QH2+QCH4〔5〕炉料带入的物理热Q5〔忽略焦炭、块矿物理热〕Q5=A×烧结矿配比×C烧结矿×t烧结跨矿t(℃)100200300400500C烧结矿
(kcal/kg.℃)0.160.170.180.190.2烧结矿CP=[0.115+0.275×10-7×〔T-373〕-0.0125×10-5×(T-373)2]kcal/Kg.℃甲烷生成热〔Kcal/Kg〕4-2冶炼一吨生铁的热支出〔1〕氧化物分解热Q1包括:氧化铁、氧化锰、二氧化硅、五氧化二磷等的分解热,首先应了解炉料中氧化物的存在方式:烧结矿中的FeO有20~25%存在于硅酸盐中,其他FeO以Fe3O4形状存在;天然矿中都以Fe3O4方式存在。焦炭、煤粉中的FeO主要以硅酸盐方式存在。FeO2FeO•SiO2氧化铁Fe3O4Fe2O3a)铁氧化物分解热QFei)FeO:以硅酸盐存在的FeO收入FeOFe2SiO4烧结=〔A×烧结矿配比%×FeO%烧结-炉尘量×FeO%炉尘〕×20~25%FeOFe2SiO4焦炭=K×FeO%焦FeOFe2SiO4煤粉=M×FeO%煤粉支出FeOFe2SiO4炉渣=渣量×FeO%渣ΣFeOFe2SiO4=FeOFe2SiO4烧结+FeOFe2SiO4焦炭+FeOFe2SiO4煤粉-FeOFe2SiO4炉尘Ⅱ〕FeOFe3O4=A×烧结配比×FeO%烧结×75%+A×块矿配比×FeO%块Fe2O3Fe3O4=FeOFe3O4×160/72Ⅲ〕自在Fe2O3Fe2O3自在=A×Fe2O3%混-Fe2O3Fe3O4–炉尘量×Fe2O3%氧化铁分解热:FeOFe2SiO4:973.33kcal/kgFe3O4:1146.38kcal/kgFe2O3自在:1230.69kcal/kgQFe=ΣFeOFe2SiO4×973.33+Fe3O4×1146.38+Fe2O3自在×1230.69kcalb)SiO2分解热QSi由SiO2分解出1KgSiO2吸热7423KcalQSi=1000×[Si]×7423kcalc)P2O5分解吸热QP由P2O5分解出1kgP需求吸热8540kcal/kgQP=1000×[P]×8540kcald)锰氧化物分解吸热QMn1KgMnO2分解成MnO需求吸热333.5Kcal,由MnO分解成1kgMn需吸热1758.5Kcal。QMnO2→MnO=A×MnO2%混×333.5KcalQMnO→Mn=1000×[Mn]×1758.5KcalQMn=QMnO2→MnO+QMnO→Mne)氧化铜分解吸热QCuQCu=A×CuO%混×481.25kcalQ1‘=QFe+QMn+QP+QSi+QCu(2)脱硫耗热Q2‘炉渣中CaO、MgO同时参与脱硫,按普通阅历:当渣中MgO>3~4%时,脱除每千克硫耗热1995Kcal/kgS当渣中MgO<3~4%时,脱除每千克硫耗热7Kcal/kgS∴Q2‘=1995×S渣Kcal(3)碳酸盐分解吸热Q3‘CaCO3分解1kgCO2吸热966KcalCaCO3→CaO+CO2MgCO3分解1kgCO2吸热594KcalMgCO3→MgO+CO2MnCO3分解1kgCO2吸热522Kcala)熔剂中以CaCO3方式存在的CO2:CO2CaCO3Φ=Φ×CaO%Φ×44/56b)熔剂中以MgCO3方式存在的CO2:CO2MgCO3Φ=Φ×MgO%Φ×44/40c)混合矿中以CaCO3方式存在的CO2:CO2CaCO3混=A×烧损%×d)混合矿中以MgCO3方式存在的CO2:CO2MgCO3混=A×烧损%×Q3‘=〔CO2CaCO3熔+CO2CaCO3混〕×966+〔CO2MgCO3Φ+CO2MgCO3混〕×594〔4〕水分分解热Q4Q4‘=2581×V水汽kcal(分解1m3水需耗热2581KCal)V水汽=鼓风中的水(V风×f)+煤粉中的水〔M×H2O%煤×22.4/18〔5〕炉料游离水的蒸发热〔焦炭中〕和结晶水分解蒸发热〔矿中〕Q5‘1Kg水中由20℃升到100℃吸热80KCal,再变成100℃水蒸气吸热540Kcal,总吸热为620Kcal.烧结矿温度比较高〔无论冷矿或热矿〕,普通无游离水Q5‘=湿焦比×焦炭游离水%×620〔天然矿中结晶水忽略不计〕〔6〕铁水带走的热Q6‘生铁含热值q铁〔kcal/kg〕炼钢生铁碱性转炉生铁铸造生铁硅铁锰铁270~280260~270300~310320~330280~290Q6‘=1000×q铁〔7〕炉渣带走的热Q7‘Q7‘=渣量×q渣炉渣热焓值〔kcal/kg〕炉渣种类q渣熔化热(kcal/kg)出炉温度(℃)温度—黏度曲线转折点温度℃碱性转炉生铁炉渣400~4301300~1350铸造生铁炉渣450~480400~4201440~1520锰铁炉渣440~4801425~1480硅铁炉渣480~500最高达1680含氟炉渣420~4851300~1550含钒钛炉渣1300~1400〔8〕喷吹物分解热Q8‘煤粉分解吸热300kcal/kg无烟煤分解吸热240kcal/kg重油分解吸热500kcal/kg烟煤分解吸热280kcal/kg炼铁91NO.4P37Q8‘=煤比×300〔9〕炉顶煤气带走热Q9‘a)干煤气带走热b)水蒸气带走热c)炉尘带走热a)煤气带走热Q煤气Q煤气=V煤气×C煤气×t煤气C煤气=CCO×CO%+CCO2×CO2%+CN2×N2%+CH2×H2%+CCH4×CH4%气体比热〔kcal/Nm3•℃〕℃RO2N2O2H2O干空气湿空气COH2H2SCH4C2H400.38700.31030.31230.35620.31070.31640.31110.3050.3620.3740.4221000.41080.31080.31510.35870.31170.31740.31110.3080.3680.3950.5032000.43180.31120.31930.36240.31280.31860.3130.3100.3760.4220.5563000.44920.31240.32440.36730.31480.32070.3150.3110.3840.4520.6044000.46420.31460.32950.37240.31770.32370.3180.3110.3930.4830.655000.48850.31750.33450.37810.32100.32710.3210.3120.4020.5120.6916000.49180.32050.33900.38400.32440.33050.3250.3130.4110.5420.7287000.50340.32370.34320.39020.32780.33400.3280.3140.4200.5690.7628000.51390.32680.34700.39650.33110.33740.3320.3150.4290.5960.7989000.52340.33000.35020.40280.33420.34060.3350.3160.4370.620.82410000.53180.33290.35350.40920.33720.34370.3380.3170.4450.6440.85211000.53960.33570.35630.41550.34000.34660.3410.3190.4520.66512000.54660.33830.35880.42170.34260.34930.3440.3200.4590.68513000.55310.34130.36120.42770.34520.35200.3460.3230.46514000.55900.34330.36350.43350.34750.35440.3490.3250.47115000.56450.34560.36570.43920.34970.35670.3510.3270.47716000.56960.34760.36780.44470.35180.35890.3530.32917000.57420.34930.36980.450.35370.36090.3550.331b)水蒸气带走热Q水汽Q水汽=C水汽×VH2O×(t顶-100)煤气中的水炉尘带走热Q尘=C尘×t顶×炉尘量C尘=0.18~0.2kcal/kgQ9‘=Q煤气+Q水汽+Q尘〔
温馨提示
- 1. 本站所有资源如无特殊说明,都需要本地电脑安装OFFICE2007和PDF阅读器。图纸软件为CAD,CAXA,PROE,UG,SolidWorks等.压缩文件请下载最新的WinRAR软件解压。
- 2. 本站的文档不包含任何第三方提供的附件图纸等,如果需要附件,请联系上传者。文件的所有权益归上传用户所有。
- 3. 本站RAR压缩包中若带图纸,网页内容里面会有图纸预览,若没有图纸预览就没有图纸。
- 4. 未经权益所有人同意不得将文件中的内容挪作商业或盈利用途。
- 5. 人人文库网仅提供信息存储空间,仅对用户上传内容的表现方式做保护处理,对用户上传分享的文档内容本身不做任何修改或编辑,并不能对任何下载内容负责。
- 6. 下载文件中如有侵权或不适当内容,请与我们联系,我们立即纠正。
- 7. 本站不保证下载资源的准确性、安全性和完整性, 同时也不承担用户因使用这些下载资源对自己和他人造成任何形式的伤害或损失。
最新文档
- 品牌管理相关试题及答案
- 大规模系统架构的设计思路试题及答案
- 2025年液体气体过滤、净化机械合作协议书
- 数据中心建设中的核心考试题试题及答案
- 酒店信息技术的应用与发展试题及答案
- 实体营销与电商结合试题及答案2024
- 2025年高纯低羟基石英玻璃合作协议书
- 网络配置管理试题及答案手册
- 网络工程师数据库连接问题试题及答案
- 儿童结核病的基本知识
- 高二数学选择性必修二同步练习与答案解析(基础训练)
- 新闻采编人员考试复习材料
- 北京市丰台区2023-2024学年高三上学期期中考试语文试题(解析版)
- 中低空飞行的大气环境
- 河北医疗服务价格手册指南
- 农业无人设备智能控制与决策
- 长江师范学院《C语言程序设计》2019-2020学年期末考试试卷
- 中国灭绝姓氏的研究报告
- 从政经验交流发言3篇
- 35770-2022合规管理体系-要求及使用指南标准及内审员培训教材
- APQP项目小组人员能力矩阵图
评论
0/150
提交评论