


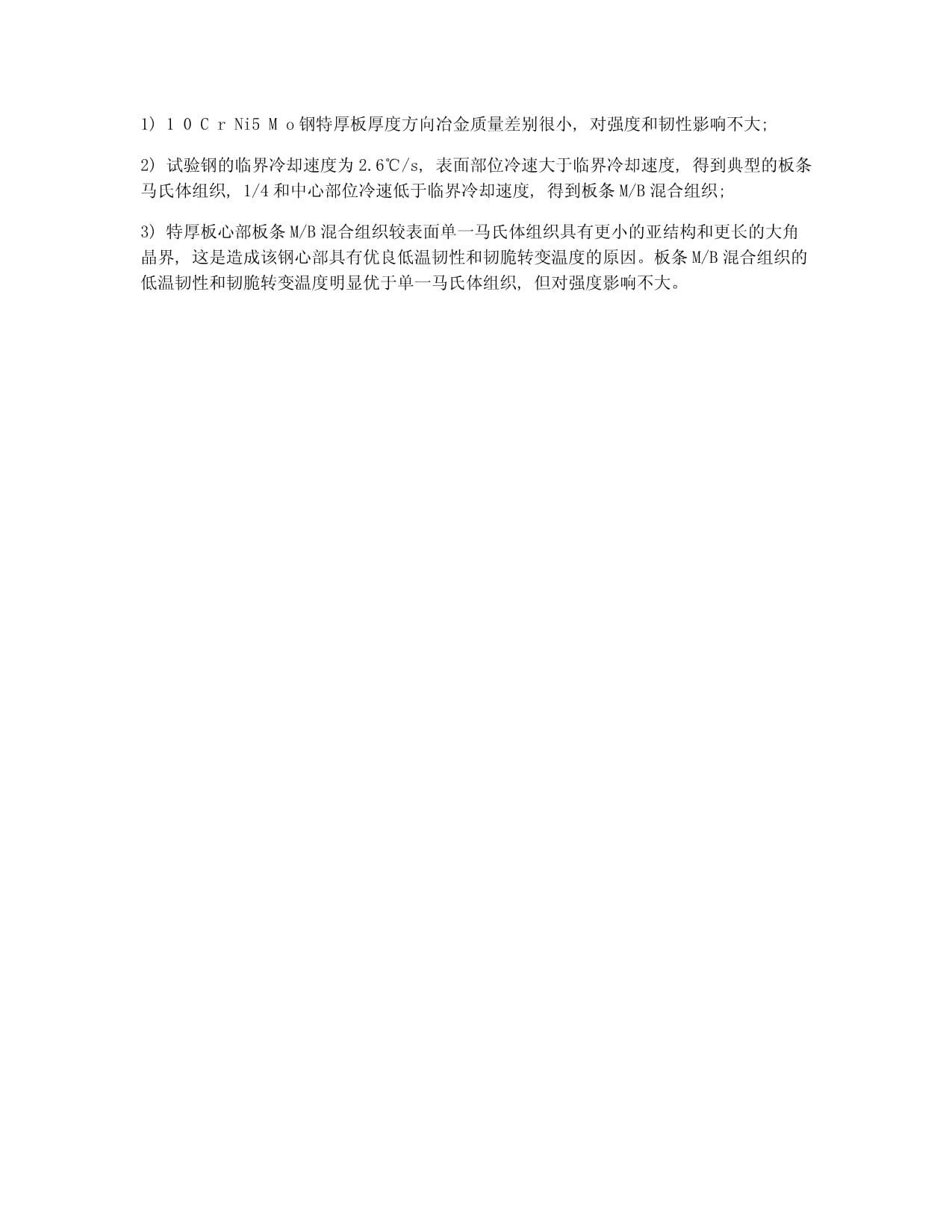
下载本文档
版权说明:本文档由用户提供并上传,收益归属内容提供方,若内容存在侵权,请进行举报或认领
文档简介
mb混合组织对低碳马氏体钢强韧性的影响
10碳马氏体钢厚板是一种专用结构钢。实际设计对其性能要求非常严格。在大的厚度上,不仅需要高强度,还需要良好的低温耐寒性。此外,还需要良好的焊接性和抗海水侵蚀性。特厚钢板的生产、轧制和热传递过程均受厚度的影响,造成了从表面到心部相变过冷度、动力学条件的不同。在整个厚度方向上难以完全达到临界冷却速度,形成了马氏体、贝氏体多相组织。本文采用有限元模拟、彩色金相以及背散射电子衍射(EBSD)技术,分析板条M/B混合组织对低碳马氏体钢强韧性的影响,并研究板条M/B混合组织改善强韧性的原因,为工业生产提供理论指导。1热分析测试方法试验材料为板厚120mm的高强度低碳马氏体钢,化学成分见表1。沿钢板表面、1/4厚以及中心分别取横向试样进行试验。拉伸试样尺寸为ue78810mm×110mm;V型冲击试样尺寸为10mm×10mm×55mm,开槽方向垂直于轧制面。组织用4%的硝酸酒精腐蚀,晶粒度用过饱和苦味酸水溶液腐蚀。马氏体、贝氏体组织分离采用Lepera(4%苦味酸酒精溶液+1%偏重亚硫酸钠溶液1∶1)试剂腐蚀。利用热场发射SEM中集成的EBSD/EDS系统分析和统计亚结构晶界长度。EBSD取向图步长尺寸为0.8μm,其步长尺寸的选定根据板条块宽度而定,比板条块宽度小。对特厚板(钢板宽厚规格为2000mm×120mm)淬火冷却过程进行有限元模拟,建立数学模型,采用ANSYS分析软件建立钢板2-D模型,选择plane55热单元划分网格。获得厚板不同部位的瞬态温度场分布和温度随时间变化曲线,为淬火冷却过程组织转变提供有力的指导。试验钢的热物性参数示于表2。分别在特厚板表面和中心部位取样,采用相同热处理工艺(900℃保温1h后淬火,然后经630℃、640℃、650℃×2h回火)进行冶金质量验证,分析表面和心部冶金质量差异对力学性能的影响。为了排除冶金质量的影响,在特厚板同一位置(表面位置)取样,加热到900℃,保温1h后分别以水淬和快风冷方式冷却,然后640℃×2h回火进行分析表面和心部的组织差异对性能的影响。2试验结果与分析2.1低碳板条马氏体组织工业生产120mm特厚板表面、1/4位置和中心各部位淬火组织示于图1。图1表明,表面(图3a)板条结构整齐,是典型的低碳板条马氏体组织。1/4位置和中心淬火组织(图3b和3c)与表面组织稍有差别,而板条结构依然整齐,出现板条贝氏体组织。采用Lepera着色腐蚀,马氏体呈白色,贝氏体呈现棕褐色。着色腐蚀表明1/4位置和中心得到板条M/B混合组织。统计结果表明,1/4位置贝氏体含量达到10%,而心部贝氏体含量达到20%。2.2冷却速度对各部位组织转变的影响对120mm特厚板淬火冷却过程温度场变化进行ANSYS有限元模拟,分析不同部位的瞬态温度场分布,温度随时间变化关系。图2(a)是10CrNi5Mo钢连续冷却转变曲线,图2(b)是ANSYS有限元模拟厚度方向各部位的冷速曲线和CCT曲线的叠加图。图2(a)连续冷却曲线表明,当冷却速度大于2.6℃/s时,钢连续冷却组织全部转变为马氏体;当冷却速度在0.79~2.6℃/s范围内,组织转变为马氏体/贝氏体混合组织;当冷却速度小于0.79℃/s时,全部转变为贝氏体组织。由图2(b)分析知,在距表面20mm位置平均冷速达到2.72℃/s,淬火冷却过程只经过马氏体组织转变区,全部转变为马氏体组织;距表面30mm(1/4)位置和心部的平均冷速分别为2.15℃/s、1.72℃/s,在淬火冷却过程中组织转变为马氏体/贝氏体混合组织。平均冷速越小,经过M/B混合组织转变区的时间越长,贝氏体含量越多。从表面到心部,贝氏体含量逐渐增加。2.3晶粒尺寸对力学性能的影响本实验钢特厚板显微组织见图3。图3(a)、3(b)表明,表面是B1细系氧化铝类夹杂,而中心是B1粗系氧化铝类夹杂。晶粒统计表明表面晶粒尺寸20.1μm(8.0级),而中心晶粒尺寸24.1μm(7.5级),从表面到中心由于产品厚度大,变形渗透困难,晶粒平均尺寸有一定的上升,对心部强韧性具有一定的不利影响。在特厚板表面和中心分别取样,进行冶金质量验证试验,其强韧性变化示于图4。在调质过程中奥氏体化温度和保温时间相同,认为表面和中心试样晶粒尺寸相同,排除晶粒尺寸对强韧性影响;本试验采用20mm×20mm×200mm小试样,在淬火冷却过程中完全形成马氏体组织,排除组织对强韧性的影响。由图4可见,在相同回火温度下,表面和中心的强度和韧性差别很小,表明特厚板厚度方向各部位冶金质量差别很小,对强度和韧性基本没有影响。故认为冶金质量对10CrNi5Mo钢特厚板没有产生截面效应。2.4性能分析和晶界及微观组织10CrNi5Mo钢特厚板表面、1/4部位和中心部位强度、塑性和韧性变化示于图5。图5表明,表面、1/4部位和中心部位的Rm、RP0.2、A%和Z%变化很小,而冲击功从表面至中心依次增加,尤其在-84℃时冲击值大幅度提高,表面位置冲击功仅为30J,而1/4部位达到92J,心部远远高于表面达到138J。特厚板不同部位系列温度冲击功、纤维断面率及侧膨胀随温度变化曲线图示于图6(a)、6(b)和6(c)。分别根据能量、断口形貌和塑性变形来分析试验钢的韧脆转变特性,图6(a)表明,中心部位冲击韧性(尤其是低温韧性)高于1/4部位,1/4部位高于表面。根据50%断面纤维率对应的温度作为韧脆转变温度(Tk),表面、1/4部位和中心部位的韧脆转变温度分别为-60、-80和-100℃。若把0.38mm侧膨胀量对应的温度作为韧脆转变温度,表面的韧脆转变温度约为-92℃,而1/4部位和中心都低于-100℃。表明心部具有更高的韧性和更低的韧脆转变温度。在水淬和快风冷方式下获得组织见图7,水冷方式下获得单一马氏体组织,快风冷方式下得到板条M/B混合组织。由图7表明试验钢水淬后获得单一马氏体组织,板条结构清晰,是典型的低碳板条马氏体;经快风冷方式后,获得板条M/B混合组织,仍是板条结构,但变得模糊。板条马氏体和板条M/B混合组织强韧性对比见图8。图8表明,板条M/B混合组织的抗拉强度比单一马氏体组织稍高,屈服强度比单一马氏体下降45MPa。而板条M/B混合组织比单一马氏体组织在-20℃冲击功高30J,在-84℃的冲击功却提高117J。表明板条M/B混合组织在保证强度下降不多的情况下,可以大幅度提高钢的韧性,特别是低温韧性。故认为10CrNi5Mo钢特厚板调质处理后,表面和中心的组织差异是造成心部获得优良低温韧性和韧脆转变温度的主要原因。在120mm特厚板表面和心部分别取EBSD试样,选取相等(250μm×160μm)区域进行扫描,马氏体和M/B混合组织单元图和单位面积晶界分布图示于图9。经TSLOIM软件统计单位面积晶界长度示于表3。图10为单一马氏体和M/B混合组织单位面积大角晶界长度和冲击功关系曲线。从图9(a)和9(b)可以看出,板条M/B混合组织较单一马氏体组织具有更小的亚结构,晶界图统计结果表明M/B混合组织具有较长的大角晶界长度。图10表明冲击功随着单位面积大角晶界长度的增加而增加,大角晶界主要分布在45°<θ<65°范围内,而分布在15°<θ<45°范围内较短。原因是由奥氏体晶粒转变来的马氏体有24种相等意义晶体学变量,这24种变量中有16种相邻变体(板条块)之间的取向差角分布在45°<θ<65°范围内。由于两种试样EBSD扫描区域面积相等,原始奥氏体晶粒尺寸相等且是大角晶界,故认为它们的原始奥氏体晶界长度相等。研究指出,裂纹扩展遇到大角晶界(原始奥氏体晶界、板条束界和板条块界)发生明显的转折,吸收较多能量提高冲击功,而遇到小角晶界(板条界)没有明显的转折。因此可认为,两种组织中韧性变化主要是亚结构晶界(板条束和板条块界)所起的决定性作用,裂纹扩展至这些晶界处发生明显转折,且随着它们的长度增加冲击功增加。10CrNi5Mo钢特厚板心部具有20%的贝氏体较1/4(10%B)和表面(0%B)具有更高的韧性和更低的韧脆转变温度。表明马氏体、贝氏体组织混合后,强韧性优于单一马氏体组织,且并非贝氏体含量越多韧性越好,而存在最佳含量比例。不同比例的马氏体、贝氏体混合后细化板条束和板条块,增加大角晶界长度,裂纹扩展吸收更多能量提高冲击功是板条M/B混合组织改善强韧性的微观机理。3特厚板心部m/b混合组织的制备1)10CrNi5Mo钢特厚板厚度方向冶金质量差别很小,对强度和韧性影响不大;2)
温馨提示
- 1. 本站所有资源如无特殊说明,都需要本地电脑安装OFFICE2007和PDF阅读器。图纸软件为CAD,CAXA,PROE,UG,SolidWorks等.压缩文件请下载最新的WinRAR软件解压。
- 2. 本站的文档不包含任何第三方提供的附件图纸等,如果需要附件,请联系上传者。文件的所有权益归上传用户所有。
- 3. 本站RAR压缩包中若带图纸,网页内容里面会有图纸预览,若没有图纸预览就没有图纸。
- 4. 未经权益所有人同意不得将文件中的内容挪作商业或盈利用途。
- 5. 人人文库网仅提供信息存储空间,仅对用户上传内容的表现方式做保护处理,对用户上传分享的文档内容本身不做任何修改或编辑,并不能对任何下载内容负责。
- 6. 下载文件中如有侵权或不适当内容,请与我们联系,我们立即纠正。
- 7. 本站不保证下载资源的准确性、安全性和完整性, 同时也不承担用户因使用这些下载资源对自己和他人造成任何形式的伤害或损失。
最新文档
- 2025年绿色照明项目合作计划书
- 2025年丝绢纺织及精加工产品项目建议书
- 五年级数学(小数乘除法)计算题专项练习及答案
- 三年级数学计算题专项练习及答案集锦
- 右肺低分化腺癌护理查房
- 陕西青年职业学院《药学专业创新创业拓展》2023-2024学年第二学期期末试卷
- 集宁师范学院《物流管理前沿讲座》2023-2024学年第一学期期末试卷
- 集美大学诚毅学院《英语视听说(四)》2023-2024学年第二学期期末试卷
- 青岛工学院《机能实验学》2023-2024学年第二学期期末试卷
- 青岛幼儿师范高等专科学校《建筑给水排水》2023-2024学年第一学期期末试卷
- T-CSOE 0003-2024 井下套管外永置式光缆安装要求
- 合肥鼎材科技有限公司光阻车间光刻胶生产线技术改造项目环评报告书
- 北师大版(2024)七年级下册生物第6章 人体的营养 学情评估测试卷(含答案解析)
- 2025体育单招英语备考100个高频名词精讲(精校打印版)
- 9.1.2 用坐标描述简单几何图形(课件)-2024-2025学年新教材七年级下册数学
- 精神科叙事护理案例分享
- 数学教师个人发展规划
- 金属加工机械制造行业分析报告
- 2025年陕西延长石油集团矿业公司招聘笔试参考题库含答案解析
- 《论民本课件》课件
- 塔吊司机安全培训
评论
0/150
提交评论