



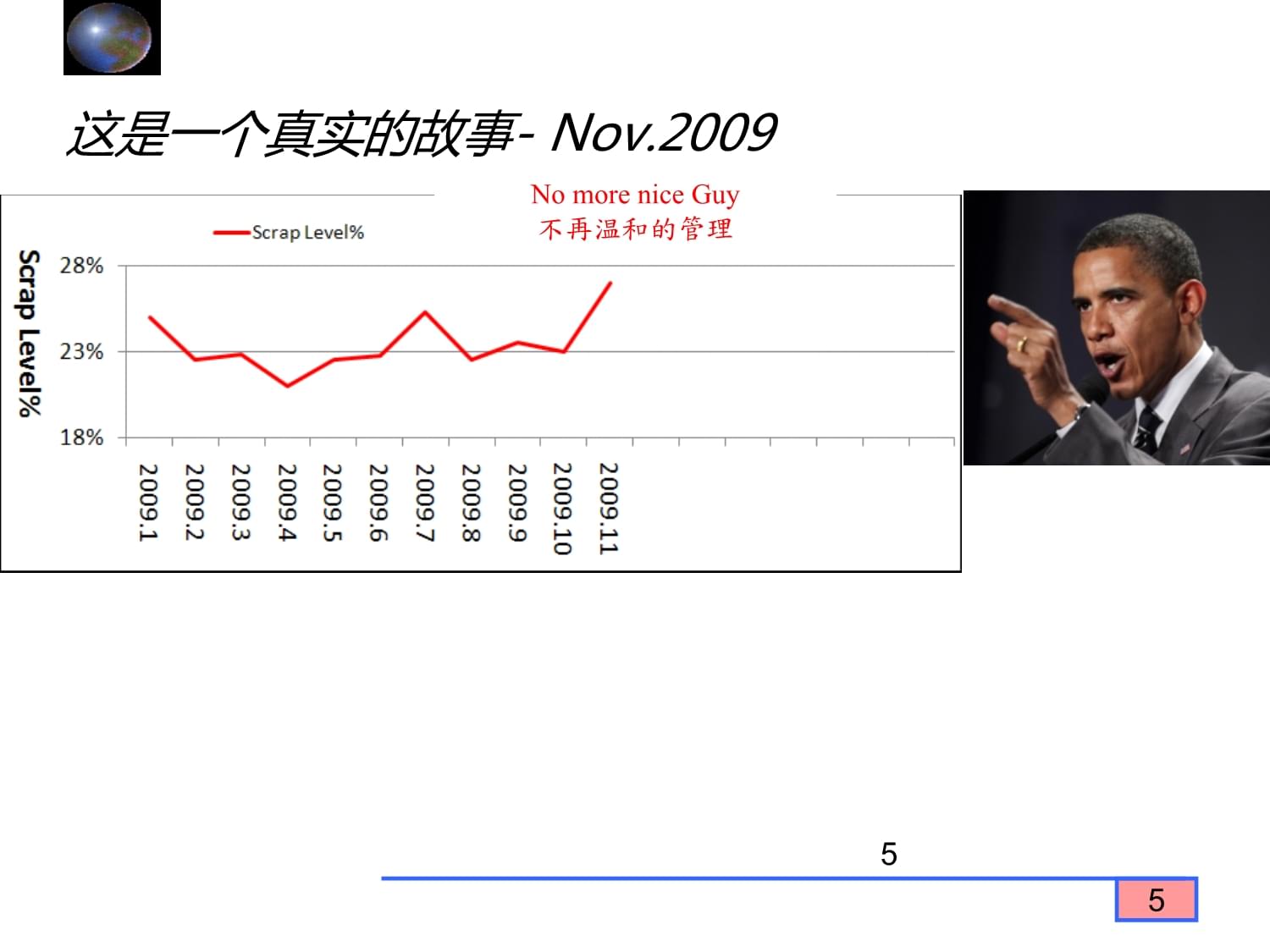
版权说明:本文档由用户提供并上传,收益归属内容提供方,若内容存在侵权,请进行举报或认领
文档简介
1、SPC 培训教材系列教材1-21为什么使用SPC什么是SPC怎么用SPCSPC使用误区和挑战Target2这是一个真实的故事-2009年4月Celebration time晚会时间3这是一个真实的故事- Jul.2009Manager wants take back the award经理想收回奖励4这是一个真实的故事- Nov.2009No more nice Guy不再温和的管理5这是一个真实的故事- Jun.2010Manager concludes: Tough Love Makes Things Happen”经理断定:粗暴的爱产生奇迹!6控制图讲述了一个不同故事-为什么?把数据放在
2、控制图中7品质管理的基本原则PROCESSOUTPUTINPUT不接受不良不制造不良不流出不良8Y=f(X)OUTPUT=YINPUT=XPROCESS PARAMETER=XY是因变数X是自变数Y只能靠检查,不好的淘汰。X才是我们所能控制的,使得Y符合我们的需求。9Y=f(x1,x2,.)Y可视为顾客所要求的产品特性。但是如果在y进行相应的统计控制,其实产品已经制造出来,只是相当于检验产品做得好不好,时效已晚。所以要去探究那些因素会影响y,进而事先控制x,如此才能起到在生产时就控制的效果,而不是等到产品做出来再做检验。10SPC&SQCPROCESS原料测量结果针对产品所做的是在做SQC针对
3、过程的重要控制参数所做的才是SPC针对原料所做的控制也可属SPC11SPC用在那里?PROCESSOUTPUTINPUT消极的地方只能防堵积极的地方可防止不良积极的地方可防止不良12SPC想法藉由以往的数据了解正常的变异范围设定成控制界限绘点判定是否超出界限纠正异常持续改进,缩小控制界限13SPC目的了解CTQ,定义Y了解影响CTQ的因子,Y=f(x1,x2.)做解析用控制图,了解正常变异范围制程稳定,控制界限延用现场绘图、点图、判图、纠异持续改进、缩小变异14SPC原理收集数据一开始要多收集数据以了解制程状况解析数据了解其正常波动的范围控制用图形运用控制限来判定制程是否异常1516正确应用S
4、PC的7项重要概念(一) SPC重要概念1 :把客户需求转换成质量特性为应用SPC的第一要务 .1617(二) SPC重要概念2:应把焦点集中在如何利用控制制程参数,以使制程维持在稳定状态,并且使其具备足够符合质量规格之能力 1718(三) SPC重要概念3:应利用适当之管制图,以判断制程是否持续维持在稳定状态 (四) SPC重要概念4:不可忽视量测系统之重要性(五) SPC重要概念5:制程不稳定的三大可能原因1. 未适当层别2. 迷信反馈控制 (即过度调整)3. 原物料不稳定1819(六) SPC重要概念6:光有稳定的制程是不够的 ,你的制程必须还要具备足够符合质量规格之能力 (七) SPC
5、重要概念7:你可能会遇到的两种问题:由管制图中判读出有偶发性的异常现象发生及制程能力不足,解决这两种问题的方法完全不同19控制图种类(以数据来分)计量值控制图平均值与全距控制图平均值与标准差控制图中位值与全距控制图个别值与移动全距控制图计数值控制图不良率控制图不良数控制图缺点数控制图单位缺点控制图20“n”=1025控制图的选定资料性质不良数或缺陷数单位大小是否一定“n”是否一定样本大小n2Cl的性质“n”是否较大“u”图“c”图“np”图“p”图X-Rm图X-R图X-R图X-s图计数值计量值“n”=1n2中位数平均值“n”=25缺陷数不良数不一定一定一定不一定控制图的选择21CASE STU
6、DY22控制图所用的统计原理计量型Xbar-RXbar-sX中位数-RX-Rm正态分布计数型Pnp二项分布计数型Cu卜氏分布23搜集数据绘解析用控制图是否稳定绘直方图是否满足规格控制用控制图寻找异常原因检讨机械、设备提升制程能力控制图的绘制流程24控制图种类(依用途来分)解析用控制图决定方针用制程解析用制程能力研究用制程管制准备用解析用稳定控制用管制用控制图追查不正常原因迅速消除此项原因并且研究采取防止此项原因重复发生之措施2568.26%95.45%99.73%+1+2+3-1-2-3正态分布概率26中央极限定理27为何样本数不同时控制限不同主要原因就是因为中央极限定理,自中央极限定理来看,
7、样本愈多时,其控制限愈狭窄。示意图如下:28个别值的正态分布平均值的正态分布控制图的正态分布控制图原理说明29管制界限和规格界限规格界限:是用以说明品质特性之最大许可值,来保证各个单位产品之正确性能。管制界限:应用于一群单位产品集体之量度,这种量度是从一群中各个单位产品所得之观测值所计算出来者。30采用Xbar-R比X-Rm好的理由检出力可以增加。可以有效判定组内变异和组间变异。经过平均值之后,其分布会更趋近于正态分布。31普通原因、特殊原因示意图普通原因的波动范围异常原因导致的波动范围异常原因导致的波动范围UCLLCL32局部措施、系统措施示意图解决普通原因的系统措施解决异常原因的局部措施解
8、决异常原因的局部措施UCLLCL33过程改进循环PLANDOSTUDYACTPLANDOSTUDYACTPLANDOSTUDYACT1、分析过程本过程应做些什么会出现什么错误达到统计控制状态确定能力2.维护过程监控过程性能查找偏差的特殊原因并采取措施3.改变过程从而更好理解普通原因变差减少普通原因变差34使用控制图的注意事项分组问题主要是使在大致相同的条件下所收集的质量特性值分在一组, 组中不应有不同本质的数据, 以保证组内仅有偶然因素的影响.我们所使用的控制图是以影响过程的许多变动因素中的偶然因素所造成的波动为基准来找出异常因素的, 因此, 必须先找出过程中偶然因素波动这个基准.35分组时的
9、重要考虑时间质量特性制程的变化让组内变化只有偶然因素让组间变化只有非偶然因素组内变异小组间变异大36错误的分组方式以及其后果如此的取样方式会造成无法有效区别组内变异和组间变异,造成控制界限变宽,无法有效侦测制造变异。时间质量特性制程的变化37每天只取一组来代表,是否能代表制程呢?每天如果取三组的样本是否更能代表制程?取样频率及样本的目的说明38取样的频率的说明初期不了解制程,制程不稳定,存在组间变异稳定期后,制程已稳定,大部份只存在组内变异,偶而出现组间变异快速而频繁的取样,才能掌握制程的情形,并将各项不稳定的因子去除由于制程已相对的较稳定,我们可以比较预测出制程变化,所以抽样频率可以较低,但
10、仍应要有代表性39初期控制界限的计算一个班次之内取二十五组,每组样本数为2-5个我们利用在一个班次当中取二十五组,此时由于人、机料、法、环、测都比较固定,所以所估计出来的组内变异会比较正确,所以相关的控制界限比较窄,可以有效的侦测出不同班别之间的变化,或则组间的变化,例如材料变化、机器变化、参数变化等。40控制图示意说明初期的二十五点计算时有些超出控制界限,此时须寻找原因。连续二十五点在控制界限内,表示制程基本上已稳定,控制界限可以延用此时有点子超出控制界限,表示此时状态已被改变,此时要追查原因,必要时必须重新收集数据,重新考虑稳定状态41使用控制图的注意事项分层问题同样产品用若干台设备进行加
11、工时, 由于每台设备工作精度、使用年限、保养状态等都有一定差异, 这些差异常常是增加产品质量波动、使散差加大的原因. 因此, 有必要按不同的设备进行质量分层, 也应按不同条件对质量特性值进行分层控制, 作分层控制图. 另外, 当控制图发生异常时, 分层又是为了确切地找出原因、采取措施所不可缺少的方法.42复合层别的说明43使用控制图的注意事项控制界限的重新计算为使控制线适应今后的生产过程, 在确定控制图最初的控制线CL、UCL、LCL时, 常常需要反复计算, 以求得切实可行的控制图. 但是, 控制图经过使用一定时期后, 生产过程有了变化, 例如加工工艺改变、刀具改变、设备改变以及进行了某种技术
12、改革和管理改革措施后, 应重新收集最近期间的数据, 以重新计算控制界限并作出新的控制图.44为何控制界限应延用45建立控制图的四步骤A收集数据B计算控制限C过程控制解释D过程能力解释46建立X-R图的步骤A阶段收集数据A1选择子组大小、频率和数据子组大小子组频率子组数大小A2建立控制图及记录原始记录A3计算每个子组的均值X和极差RA4选择控制图的刻度A5将均值和极差画到控制图上47取样的方式取样必须达到组内变异小,组间变异大样本数、频率、组数的说明48组数的要求(最少25组)当制程中心值偏差了二个标准差时,它在控制限内的概率为0.84那么连续25点在线内的概率为:49每个子组的平均值和极差的计
13、算11009899100982989998101973999710010098410010010199995101999910099平均99.698.699.410098.2极差3332250平均值和极差平均值的计算R值的计算51计算控制限B1计算平均极差及过程平均值B2计算控制限B3在控制图上作出平均值和极差控制限的控制线建立X-R图的步骤B52过程控制解释C1分析极差图上的数据点C2识别并标注特殊原因(极差图)C3重新计算控制界限(极差图)C4分析均值图上的数据点超出控制限的点链明显的非随机图形超出控制限的点链明显的非随机图形C5识别并标注特殊原因(均值图)C6重新计算控制界限(均值图)C
14、7为了继续进行控制延长控制限建立X-R图的步骤C53控制图的判读超出控制界限的点:出现一个或多个点超出任何一个控制界限是该点处于失控状态的主要证据UCLCLLCL异常异常54控制图的判读链:有下列现象之一即表明过程已改变连续7点位于平均值的一侧连续7点上升(后点等于或大于前点)或下降。UCLCLLCL55控制图的判读明显的非随机图形:应依正态分布来判定图形,正常应是有2/3的点落于中间1/3的区域。UCLCLLCL5657管制图使用十大误区没能找到正确的管制点没有适宜的测量工具没有解析生产过程,直接进行管制解析与管制脱节管制图没有记录重大事项不能正确理解X Bar图与R图的含义管制界限与规格界
15、限混为一谈不能正确理解管制图上点变动所代表的意思没有将管制图用于改善管制图是品管的事Caution!57判读:58过程能力解释D1计算过程的标准偏差D2计算过程能力D3评价过程能力D4提高过程能力D5对修改的过程绘制控制图并分析建立X-R图的步骤D59制程能力指标Cp双边规格只有上规格时只有下规格时练习题:已知条件规格8+/-1,Xbar=7,标准差=1.求:Ca Cp Cpk60制程绩效指标制程绩效指标的计算,其估计的标准差为总的标准差,包含了组内变异以及组间变异。总变异=组内变异+组间变异。61Cpk和Ppk的差异Cpk:只考虑了组内变异,而没有考虑组间变异,所以一定是适用于制程稳定时,其
16、组间变异很小可以忽略时,不然会高估了制程能力;另句话也可以说明如果努力将组间变异降低时所能达到的程度。Ppk:考虑了总变异(组内和组间),所以是比较真实的情形,所以一般想要了解真正的制程情形应使用Ppk。62A收集数据:在计算各个子组的平均数和标准差其公式分别如下:63B计算控制限64C过程控制解释(同X-R图解释)65D过程能力解释66Case study67Case study请计算出上表的X-s控制图的控制限?请判定过程是否稳定?如果是不稳定该如何处理?68A收集数据一般情况下,中位数图用在样本容量小于10的情况,样本容量为奇数时更为方便。如果子组样本容量为偶数,中位数是中间两个数的均值
17、。69B计算控制限70C过程控制解释(同Xbar-R图解释)71估计过程标准偏差:72Case study73Case study请计算出上表的X-R控制图的控制限?请判定过程是否稳定?如果是不稳定该如何处理?如果制程假设已稳定,但想将抽样数自n=4调为n=5时,那么其新控制限为何?74单值控制在检查过程变化时不如Xbar-R图敏感。如果过程的分布不是对称的,则在解释单值控制图时要非常小心。单值控制图不能区分过程零件间重复性,最好能使用Xbar-R。由于每一子组仅有一个单值,所以平均值和标准差会有较大的变性,直到子组数达到100个以上。75A收集数据收集各组数据计算单值间的移动极差。通常最好是
18、记录每对连续读数间的差值(例如第一和第二个读数点的差,第二和第三读数间的差等)。移动极差的个数会比单值读数少一个(25个读值可得24个移动极差),在很少的情况下,可在较大的移动组(例如3或4个)或固定的子组(例如所有的读数均在一个班上读取)的基础上计算极差。76B计算控制限77C过程控制解释审查移动极差图中超出控制限的点,这是存在特殊原因的信号。记住连续的移动极差间是有联系的,因为它们至少有一点是共同的。由于这个原因,在解释趋势时要特别注意。可用单值图分析超出控制限的点,在控制限内点的分布,以趋势或图形。但是这需要注意,如果过程分布不是对称,用前面所述的用于X图的规则来解释时,可能会给出实际上
19、不存在的特殊原因的信号。78估计过程标准偏差:式中,R为移动极差的均值,d2是用于对移动极差分组的随样本容量n而变化的常数。79Case study80Case study请计算出上表的X-Rm控制图的控制限?请判定过程是否稳定?如果是不稳定该如何处理?81不良和缺陷的说明结果举例控制图车辆不泄漏泄漏P图NP图灯亮不亮孔的直径尺寸太小或太大给销售商发的货正确不正确风窗玻璃上的气泡C图U图门上油漆缺陷发票上的错误82P控制图的制做流程A收集数据B计算控制限C过程控制解释D过程能力解释83建立p图的步骤A阶段收集数据A1选择子组的容量、频率及数量子组容量分组频率子组数量A2计算每个子组内的不合格品
20、率A3选择控制图的坐标刻度A4将不合格品率描绘在控制图84A1子组容量、频率、数量子组容量:用于计数型数据的控制图一般要求较大的子组容量(例如50200)以便检验出性能的变化,一般希望每组内能包括几个不合格品,但样本数如果太多也会有不利之处。分组频率:应根据产品的周期确定分组的频率以便帮助分析和纠正发现的问题。时间隔短则反馈快,但也许与大的子组容量的要求矛盾子组数量:要大于等于25组以上,才能判定其稳定性。85A2计算每个子组内的不合格品率记录每个子组内的下列值被检项目的数量n发现的不合格项目的数量np通过这些数据计算不合格品率86A3选择控制图的坐标刻度描绘数据点用的图应将不合格品率作为纵坐
21、标,子组识别作为横坐标。纵坐标刻度应从0到初步研究数据读数中最大的不合格率值的1.5到2倍。划图区域87A4将不合格品率描绘在控制图上描绘每个子组的p值,将这些点联成线通常有助于发现异常图形和趋势。当点描完后,粗览一遍看看它们是否合理,如果任意一点比别的高出或低出许多,检查计算是否正确。记录过程的变化或者可能影响过程的异常状况,当这些情况被发现时,将它们记录在控制图的“备注”部份。88计算控制限B1计算过程平均不合格品率B2计算上、下控制限B3画线并标注建立p控制图的步骤B89计算平均不合格率及控制限90画线并标注均值用水平实线:一般为黑色或蓝色实线。控制限用水平虚线:一般为红色虚线。尽量让样
22、本数一致,如果样本数一直在变化则会如下图:10020030010020010010020030010012121212329192判读:93过程控制用控制图解释C1分析数据点,找出不稳定证据C2寻找并纠正特殊原因C3重新计算控制界限超出控制限的点链明显的非随机图形建立p图的步骤C94分析数据点,找出不稳定的证据点线面以上三种方式做判定。95寻找并纠正特殊原因当从数据中已发现了失控的情况时,则必须研究操作过程以便确定其原因。然纠正该原因并尽可能防止其再发生。由于特殊原因是通过控制图发现的,要求对操作进行分析,并且希望操作者或现场检验员有能力发现变差原因并纠正。可利用诸如排列图和因果分析图等解决性
23、问题数据。96控制图的实时性processTIMEREAL TIME FIND THE CAUSE97重新计算控制限当进行初始过程研究或对过程能力重新评价时,应重新计算试验控制限,以便排除某些控制时期的影响,这些时期中控制状态受到特殊原因的影响,但已被纠正。一旦历史数据表明一致性均在试验的控制限内,则可将控制限延伸到将来的时期。它们便变成了操作控制限,当将来的数据收集记录了后,就对照它来评价。98收集数据绘图及计算控制限是否异常延伸控制限N找出异常点原因并提出相应措施制程有变化人机料法环测量Y控制限运用说明99过程能力解释D1计算过程能力D2评价过程能力D3改进过程能力D4绘制并分析修改后的过
24、程控制图建立p的步骤D100过程能力解释偶因和异因并存找出异因只剩偶因运用控制图过程稳定(连25点不超限)计算过程能力101计算过程能力对于p图,过程能力是通过过程平均不合格率来表,当所有点都受控后才计算该值。如需要,还可以用符合规范的比例(1-p)来表示。对于过程能力的初步估计值,应使用历史数据,但应剔除与特殊原因有关的数据点。当正式研究过程能力时,应使用新的数据,最好是25个或更多时期子组,且所有的点都受统计控制。这些连续的受控的时期子组的p值是该过程当前能力的更好的估计值。102评价过程能力过程稳定,不良率维持在一定的水平当中降低不良率采取管理上的措施降低偶因,如此才能缩小控制界限,降低
25、不良率缩小控制限103改善过程能力过程一旦表现出处于统计控制状态,该过程所保持的不合格平均水平即反应了该系统的变差原因过程能力。在操作上诊断特殊原因(控制)变差问题的分析方法不适于诊断影响系统的普通原因变差。必须对系统本身直接采取管理措施,否则过程能力不可能得到改进。有必要使用长期的解决问题的方法来纠正造成长期不合格的原因。可以使用诸如排列图分析法及因果分析图等解决问题技术。但是如果仅使用计数型数据将很难理解问题所在,通常尽可能地追溯变差的可疑原因,并借助计量型数据进行,将有利于问题的解决104绘制并分析修改后的过程控制图当对过程采取了系统的措施后,其效果应在控制图上明显地反应出来; 控制图成
26、为验证措施有效性的一种途径。对过程进行改变时,应小心地监视控制。这个变化时期对系统操作会是破坏性,可能造成新的控制问题,掩盖系统变化后的真实效果。在过程改变期间出现的特殊原因变差被识别并纠正后,过程将按一个新的过程均值处于统计控制状态。这个新的均值反映了受控制状态下的性能。可作为现行控制的基础。但是还应对继续系统进行调查和改进。105Case study106Case study请计算出上表的p控制图的控制限?请判定过程是否稳定?如果是不稳定该如何处理?107不合格品数np图“np”图是用来度量一个检验中的不合格品的数量,与p图不同,np图表示不合格品实际数量而不是与样本的比率。p图和np图适
27、用的基本情况相同,当满足下列情况可选用np图不合格品的实际数量比不合格品率更有意义或更容易报告。各阶段子组的样本容量相同。“np”图的详细说明与p图很相似,不同之处如下:108A收集数据受检验样本的容量必须相等。分组的周期应按照生产间隔和反馈系统而定。样本容量应足够大使每个子组内都出现几个不合格品,在数据表上记录样本的容量。记录并描绘每个子组内的不合格品数(np)。109B计算控制限110过程控制解释、过程能力解释C过程控制解释:同“p”图的解释。D过程能力解释:过程能力如下:1111001001001001001001001001001001210121202不合格品数np图112Case
28、study113Case study请计算出上表的np控制图的控制限?请判定过程是否稳定?如果是不稳定该如何处理?114缺陷数c图“c”图用来测量一个检验批内的缺陷的数量,c图要求样本的容量或受检材料的数量恒定,它主要用以下两类检验:不合格分布在连续的产品流上(例如每匹维尼龙上的瑕疪,玻璃上的气泡或电线上绝缘层薄的点),以及可以用不合格的平均比率表示的地方(如每100平方米维尼龙上暇疵)。在单个的产品检验中可能发现许多不同潜在原因造成的不合格(例如:在一个修理部记录,每辆车或组件可能存在一个或多个不同的不合格)。主要不同之处如下:115A收集数据检验样本的容量(零件的数量,织物的面积,电线的长
29、度等)要求相等,这样描绘的c值将反映质量性能的变化(缺陷的发生率)而不是外观的变化(样本容量n),在数据表中记录样本容量;记录并描绘每个子组内的缺陷数(c)116B计算控制限117过程控制解释、过程能力解释过程控制解释同p图解释过程能力解释过程能力为c平均值,即固定容量n的样本的缺陷数平均值。118Case study每一组的样本数都是固定为100。119Case study请计算出上表的c控制图的控制限?请判定过程是否稳定?如果是不稳定该如何处理?120单位产品缺陷数的u图“u”图用来测量,容量不同的样本(受检材料的量不同)的子组内每检验单位产品之内的缺陷数量。除了缺陷量是按每单位产品为基本
30、量表示以外,它是与c图相似的。“u”图和“c”图适用于相同的数据状况,但如果样本含有多于一个“单位产品”的量,为使报告值更有意义时,可以使用“u”图,并且在不同时期内,样本容量不同时,必须使用“u”图。“u”图的绘制和“p”图相似,不同之处如下:121A收集数据各子组样本的容量彼此不必都相同,尽管使它的容量保持在其平均值的正负25%以内可以简化控制限的计算。记录并描绘每个子组内的单位产品缺陷数u=c/n式中c为发现的缺陷数量,n为子组中样本容量(检验报告单位的数量),c和n都应记录在数据表中。122B计算控制限123过程控制解释、过程能力解释过程控制解释同p图解释过程能力解释过程能力为u平均,
31、即每报告单元缺陷数平均值。124Case study125Case study请计算出上表的u控制图的控制限?请判定过程是否稳定?如果是不稳定该如何处理?126Dell Quality Improve 10 steps推行SPC案例介绍1271281Characterize Process描述制程特性The entire manufacturing process has been mapped and all tests and inspection operations identified. Map is version controlled and is accurate.全部的制造过
32、程已被图文化,明确所有的测试及检查工作。此过程图版本受控并准确。2Conduct Productivity Analysis实施生产能力分析Supplier has developed the Productivity Analysis matrix and is collecting and reporting Throughput Yields, Rolled-Throughput Yields and Normalized Yields.供应商已经展开了生产能力分析的矩阵并在收集和报告生产合格率,直通率和標準化產出率。3Implement SPC for Attribute Data实施
33、计数型数据的统计制程控制Supplier is charting throughput yields with a P chart. Each data point represents daily fraction nonconforming.供应商在使用P图绘制生产合格率的图表。每个数据点表示每天的不合格部分。4Implement SPC for defects from yield failures实施来自不良率的缺点的统计制程控制Supplier has developed C or U charts and established a Pareto of defect categor
34、ies. This Pareto is updated on a regular basis.供应商已经展开C图或U图并建立缺陷种类的柏拉图。这个柏拉图定期被更新。5Cause and Effect Analysis原因及后果分析Conducts cause and effect analysis of major defect categories (Process, Material, Design, Environment, Human Factors and Measurement). Conducts Failure Analysis and FMEA to find root causes.实施主要缺陷种类(过程、材料、设计、环境、人和测量的因素)的原因及后果分析。进行失效分析和潜在失效原因和后果分析来寻找根本原因。1281296Identify Critical Parameters识别关键参数Based on Cause and Effect Analysis and inputs from Engineering department, critical processes and parameters are identified and listed with s
温馨提示
- 1. 本站所有资源如无特殊说明,都需要本地电脑安装OFFICE2007和PDF阅读器。图纸软件为CAD,CAXA,PROE,UG,SolidWorks等.压缩文件请下载最新的WinRAR软件解压。
- 2. 本站的文档不包含任何第三方提供的附件图纸等,如果需要附件,请联系上传者。文件的所有权益归上传用户所有。
- 3. 本站RAR压缩包中若带图纸,网页内容里面会有图纸预览,若没有图纸预览就没有图纸。
- 4. 未经权益所有人同意不得将文件中的内容挪作商业或盈利用途。
- 5. 人人文库网仅提供信息存储空间,仅对用户上传内容的表现方式做保护处理,对用户上传分享的文档内容本身不做任何修改或编辑,并不能对任何下载内容负责。
- 6. 下载文件中如有侵权或不适当内容,请与我们联系,我们立即纠正。
- 7. 本站不保证下载资源的准确性、安全性和完整性, 同时也不承担用户因使用这些下载资源对自己和他人造成任何形式的伤害或损失。
最新文档
- 2025版定制门窗设计与安装合同书
- 2025年车贷抵押贷款合同执行与监管
- 2025年度智能交通系统建设与运营合同
- 二零二五年度房地产项目投资分析合同模板
- 二零二五版知识产权保护服务合作协议书
- 二零二五年木工小班组家具生产与市场推广承包合同
- 2025版文化旅游产品销售代理合同
- 2025年度荒料石材买卖及石材行业人才培养合同
- 2025版电梯安装与定期维护保养合同书
- 二零二五版餐饮业与旅行社跨界融合合同
- 四川省绵阳市2024-2025学年下学期八年级期末数学试卷
- 中央空调施工组织方案
- 基于灰污特性识别的电站锅炉智能吹灰系统设计及实践应用
- 《电力建设火力发电厂工程智慧工地技术标准》
- 2025至2030年中国模型即服务(MaaS)行业市场全景调研及发展前景研判报告
- 《光伏电站项目全过程管理手册》(第三分册:施工、验收、运维)
- 设计院建筑管理制度
- 2025至2030年中国量子级联激光器(QCL)行业市场专项调研及投资前景研究报告
- 2025至2030年中国连接器制造行业市场现状调查及投资方向研究报告
- 2025至2030中国市政公用工程行业项目调研及市场前景预测评估报告
- 地勤面试笔试题目及答案
评论
0/150
提交评论