

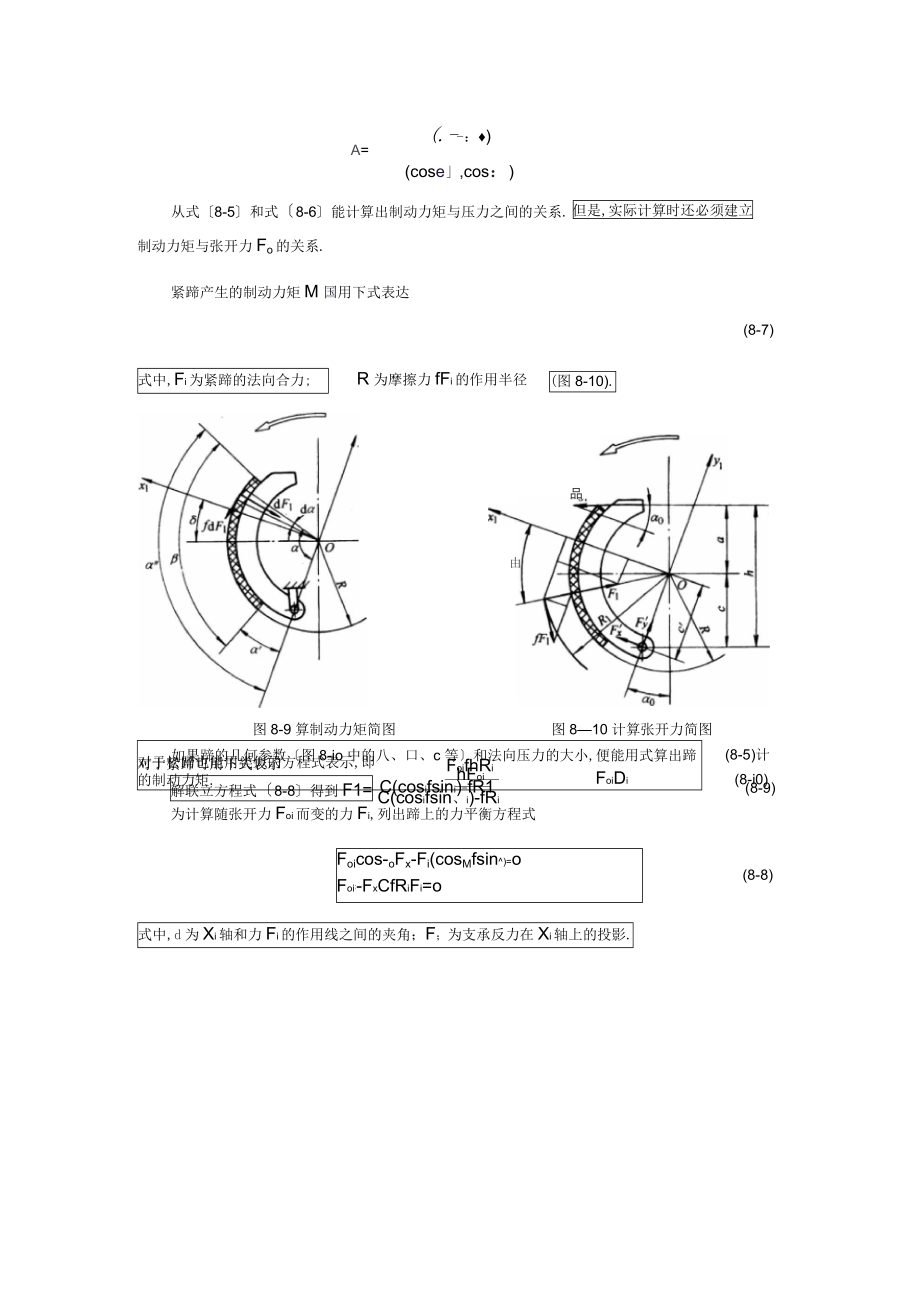


下载本文档
版权说明:本文档由用户提供并上传,收益归属内容提供方,若内容存在侵权,请进行举报或认领
文档简介
1、第四节制动器的设计与计算一、鼓式制动器的设计计算1.压力沿衬片长度方向的分布规律除摩擦衬片因有弹性容易变形外,制动鼓、蹄片和支承也有变形,所以计算法向压力在摩擦衬片上的分布规律比拟困难.通常只考虑衬片径向变形的影响,其它零件变形的影响较小而忽略不计.制动蹄有一个自由度和两个自由度之分.首先计算有两个自由度的紧蹄摩擦衬片的径向变形规律.如图8-8a所示,将坐标原点取在制动鼓中央O点.y1坐标轴线通过蹄片的瞬时转动中央A点.制动时,由于摩擦衬片变形,蹄片一面绕瞬时转动中央转动,同时还顺着摩擦力作用的方向沿支承面移动.结果蹄片中央位于Oi点,因而未变形的摩擦衬片的外表轮廓EiEi线,就沿OQ方向移动
2、进入制动鼓内.显然,外表上所有点在这个方向上的变形是一样的.位于半径OB上的任意点B1的变形就是BB;线段,所以同样一些点的径向变形储为di=BiCiBiBIcos匕考虑到中i=%+%90和BiBi=OOi=6imax,所以对于紧蹄的径向变形61和压幻的图8-8计算摩擦衬片径向变形简图a有两个自由度的紧蹄b有一个自由度的紧蹄力Pi为:6i=6imaxSin口i+中i:8-iPi=PimaxSin%+-iJ式中,豆i为任意半径OBi和yi轴之间的夹角;i为半径OBi和最大压力线OOi之间的夹角;肉为为轴和最大压力线OO1之间的夹角.其次计算有一个自由度的紧蹄摩擦衬片的径向变形规律.如图8-8b所
3、示,此时蹄片在张开力和摩擦力作用下,绕支承销A转动d丫角.摩擦衬片外表任意点Bi沿蹄片转动的切线方向的变形就是线段B1B;,其径向变形分量是这个线段在半径OBi延长线上的投影,即为BiCi线段.由于d很小,可认为/ABiB;=90,故所求摩擦衬片的变形应为=B1C1=BBsinABsin1d考虑到OA=OB=R,那么分析等腰三角形AOB1,那么有A%inL/in所以外表的径向变形和压力为、=Rsin一2(8-2)Pi=PmaxSin:综上所述可知,新蹄片压力沿摩擦衬片长度的分布符合正弦曲线规律,可用式(8-i)和式(8-2)计算.沿摩擦衬片长度方向压力分布的不均匀程度,可用不均匀系数评价=Pm
4、ax/(8-3)式中,Pf为在同一制动力矩作用下,假想压力分布均匀日的平均压力;Pmax为压力分布不均匀时蹄片上的最大压力.2.计算蹄片上的制动力矩计算鼓式制动器制动力矩,必须查明蹄压紧到制动鼓上的力与产生制动力矩之间的关系.为计算有一个自由度的蹄片上的力矩,在摩擦衬片外表取一横向微元面积,如图8-9所示.它位于a角内,面积为bRda,其中b为摩擦衬片宽度.由鼓作用在微元面积上的法向力为(8-4)dFi=PbRd:=PmaxbRsin二d:同时,摩擦力fdFi产生的制动力矩为(f为摩擦因数,计算时取0.3)2dM*=dF|fR=PmaxbRfsin:d:从a到口区段积分上式得到(8-5)M布=
5、PmaxbR2f(cos:-cos:)法向压力均匀分布时(8-6)dFi=PfbRd:M由-PfbR2f(-)从式(8-5)和式(8-6)能计算出不均匀系数(.-:)A=(cose,cos:)但是,实际计算时还必须建立从式8-5和式8-6能计算出制动力矩与压力之间的关系.制动力矩与张开力Fo的关系.紧蹄产生的制动力矩M国用下式表达(8-7)R为摩擦力fFi的作用半径(图8-10).式中,Fi为紧蹄的法向合力;品1由图810计算张开力简图图8-9算制动力矩简图如果蹄的几何参数图8-io中的八、口、c等和法向压力的大小,便能用式算出蹄的制动力矩.(8-5)计为计算随张开力Foi而变的力Fi,列出蹄
6、上的力平衡方程式Foicos-oFx-Fi(cosMfsin)=oFoi:-FxCfRiFi=o(8-8)式中,d为Xi轴和力Fi的作用线之间的夹角;F;为支承反力在Xi轴上的投影.解联立方程式8-8得到F1=hFoiC(cosifsin、i)-fRi(8-9)对于紧蹄可用下式表示FoifhRiC(cosifsini)-fR1FoiDi(8-i0)对于松蹄也能用类似的方程式表示,即F02fhR2C(cos、2-fsin、2)fR21=F02D2为计算61、62、R1、R2值,必须求出法向力F及其分量,沿着相应的轴线作用有dFx和dFy力,它们的合力为dF(图8-9).根据式(8-4)有2,Fx
7、=dFsin:-pmaxbR.sin一:d=aapmaxbR(2:sin22二sin2.:)4(8-12).、工PmaxbR(COs21-cos2:)Fy=dFcos=PmaxbR.sin:cos:d:=(8-13)4所以6=arctan5Larctanj,cos2a一cos20)21Fx,(2Psin2+sin2)式中,=*M二根据式(8-5)和式(8-7)并考虑到F1=Jf2xF2yr4R(cos-cos:)(cos2-cos2:)2(2:-sin2二二二sin2:)2如果顺着制动鼓旋转的蹄片和逆着制动鼓旋转的蹄片的a,和口角度不同,很显然两块蹄片的&和Ri值也不同.制动器有两块蹄片,鼓上
8、的制动力矩等于它们的摩擦力矩之和,即Mj=M.iM.t2=FiDiF02D2用液力驱动时,F01=F02.所需的张开力为MjF0=(DiD2)用凸轮张开机构的张开力,可由前述作用在蹄上的力矩平衡条件得到的方程式求出F010.5MDiF020.5MD2(8-10)得出自锁条件.计算鼓式制动器,必须检查蹄有无自锁的可能.由式当式(8-10)中的分母等于零时,蹄自锁,即c(cos、1fsin1)-fR|二0ccos1如果f就不会自锁.R-csin、1由方程式(8-5)和式(8-10)可计算出领蹄外表的最大压力为FmhRpmax12,1bR(cos-cos.)匕(cos、1fsin、1)一fR11二、
9、盘式制动器的设计计算假定衬块的摩擦外表全部与制动盘接触,且各处单位压力分布均匀,那么制动器的制动力矩为M=2fF0RR等于平均半径Rm,式中,f为摩擦因数;Fo为单侧制动块对制动盘的压紧力;R为作用半径.对于常见的具有扇形摩擦外表的衬块,假设其径向宽度不很大,取或有效半径Re,在实际上已经足够精确.如图8-11,平均半径为RmR1R22式中,R1和R2为摩擦衬块扇形外表的内半径和外半径.设衬块与制动盘之间的单位压力为p,那么在任意微元面积RdRd邛上的摩擦力对制动盘中央的力矩为fpR2dRd中,而单侧制动块加于制动盘的制动力矩应为2QfpRdRd=-fp(R3-R3尸3单侧衬块加于制动盘的总摩
10、擦力为fF.=fpRdRd:=fp(R;-R2尸一口R1故有效半径为RM2(R3-R13)-2fFo-3(R|-R12)图811钳盘式制动器的作用半径计算参考图可见,有效半径Re即是扇形外表的面积中央至制动盘中央的距离.上式也可写成R41RRJR+RLJmR3JRi+R2212J31+m2m式中,m=R1.R2m1由于m1,2Rm,且m越小,那么两者差值越大.1m4应当指出,假设过m小,即扇形的径向宽度过大,衬块摩擦面上各不同半径处的滑磨速度相差太远,磨损将不均匀,因而单位压力分布均匀这一假设条件不能成立,那么上述计算方法也就不适用.m值一般不应小于0.65.制动盘工作面韵.加工精度应到达下述
11、要求:平面度允差为0.012mm,外表粗糙度为Ra0.71.3Rm,两摩擦外表的平行度不应大于0.05mm,制动盘的端面圆跳动不应大于0.03mm.通常制魂盘采角摩擦性能良好的珠光体灰铸铁制造.为保证有足够的强度和耐磨性能,其牌号不应低于HT250.三、衬片磨损特性的计算摩擦衬片衬块的磨损受温度、摩擦力、滑磨速度、制动鼓制动盘的材质及加工情况,以及衬片衬块本身材质等许多因素的影响,因此在理论上计算磨损性能极为困难.但试验说明,影响磨损的最重要的因素还是摩擦外表的温度和摩擦力.从能量的观点来说,汽车制动过程即是将汽车的机械能动能和势能的一局部转变为热量而耗散的过程.在制动强度很大的紧急制动过程中
12、,制动器几乎承当了汽车全部动能耗散的任务.此时,由于制动时间很短,实际上热量还来不及逸散到大气中,而被制动器所吸收,致使制动器温度升高.这就是所谓制动器的能量负荷.能量负荷越大,那么衬片衬块磨损将越严重.对于盘式制动器的衬块,其单位面积上的能量负荷比鼓式制动器的衬片大许多倍,所以制动盘的外表温度比制动鼓的高.各种汽车的总质量及其制动衬片衬块的摩擦面积各不相同,因而有必要用一种相对的量作为评价能量负荷的指标.目前,各国常用的指标是比能量耗散率,即每单位衬片衬块摩擦面积的每单位时间耗散的能量.通常所用的计量单位为Wmm2.比能量耗散率有时也称为单位功负荷,或简称能量负荷.双轴汽车的单个前轮及后轮制
13、动器的比能量耗散率分别为maVi2-vf一4tAimav;-vf62二4tA21:ei;-式中,ma为汽车总质量;s为汽车回转质量换算系数;Vi、V2为制动初速度和终速度m/s;j为制动减速度ms2;t为制动时间s;A、A2为前、后制动器衬片衬块的摩擦面积mm2;3为制动力分配系数.在紧急制动到停车的情况下,v2=O,并可认为8=1,故2mav1e18-144tAi262=61-8-154tA2据有关文献推荐,鼓式制动器的比能量耗散率以不大于1.8W/mm2为宜,计算时取减速度j=O.6g.制动初速度v1:轿车用lOOkmZh27.8m/s;总质量3.5t以下的货车用80km/h22.2m/s
14、;总质量3.5t以上的货车用65km/h18m/s.轿车的盘式制动器在同上的2v1和j的条件下,比能量耗散率应不大于6.0W/mm.对于最局车速低于以上规定的制动初速度的汽车,按上述条件算出的e值允许他大于1.8W/mm2.比能量耗散率过高不仅引起衬片衬块的加速磨损,且有可能使制动鼓或制动盘更早发生龟裂.另一个磨损特性指标是每单位衬片衬块摩擦面积的制动器摩擦力,称为比摩擦力f0.比摩擦力越大,那么磨损将越严重.,单个车轮制动器的比摩擦力为f0MRA(8-16)式中,M心单个制动器的制动力矩;R为制动鼓半径衬块平均半径Rm或有效半径Q;A为单个制动器的衬片衬块摩擦面积.在j=O.6g时,鼓式制动
15、器的比摩擦力f0以不大于O.48N/mm2为宜.与之相应的衬片与制动鼓之间的平均单位压力pm=f0/f=1.371.60N/mm2设摩擦因数f=O.3O.35o这比过去一些文献中所推荐的pm许用值22.5N/mm2要小,由于磨损问题现在已较过去受到更大程度的重视.四、前、后轮制动器制动力矩确实定为了保证汽车有良好的制动效能,要求合理地确定前、后轮制动器的制动力矩.为此,首先选定同步附着系数cp0,并用下式计算前、后轮制动力矩的比值M.iL2%(8-17)Li-0hg式中,M性、M他为前、后轮制动器的制动力矩;Li、L2为汽车质心至前轴和后桥的距离;hg为汽车质心高度.然后,根据汽车满载在柏油、
16、混凝土路面上紧急制动到前轮抱死拖滑,计算出前轮制动器的最大制动力矩Mumax;再根据前面已确定的前、后轮制动力矩max的比值计算出后轮制动器的最大制动力矩M.2max.五、应急制动和驻车制动所需的制动力矩1、应急制动应急制动时,后轮一般都将抱死滑移,故后桥制动力为FB2=F2:=ML:Lhg此时所需的后桥制动力矩为M=工(8-18)式中,mag为汽车满载总质量与重力加速度的乘积;L为轴距;L1为汽车质心到前轴的距离;hg为汽车质心高度;F2为路面对后桥的法向反力;少为附着系数;re为车轮有效半径.如用后轮制动器作为应急制动器,那么单个后轮制动器的应急制动力矩为FB2re/2.假设用中央制动器进
17、行应急制动,那么其应有的制动力矩为Fb2re/i05i0为王传动比.2、驻车制动图8-12表示汽车在上坡路上停驻时的受力情况.由此不难得出停驻时的后桥附着力为F2:=mag1Lhgcos-sin;L汽车在下坡路上停驻时的后桥附着力为F2=magLihgcosotsinaLLJ某货车的F2cp/mag、F,2平/mag、FB2/mag、三者对坡路倾角口的关系,如图8-13所示.汽车可能停驻的极限上坡路倾角0fl可根据后桥上的附着力与制动力相等的条件求得,即由jLlhg.mag中cosa1+sina1=magsina1lLLJ:L倚至1:1二arctan1LJhg式中,必是保证汽车上坡行驶时的纵向稳定性的极限坡路倾角,图8-13所例如车的%=32芍0,少=0.7时同理可推导出汽车可能停驻的极限下坡路倾
温馨提示
- 1. 本站所有资源如无特殊说明,都需要本地电脑安装OFFICE2007和PDF阅读器。图纸软件为CAD,CAXA,PROE,UG,SolidWorks等.压缩文件请下载最新的WinRAR软件解压。
- 2. 本站的文档不包含任何第三方提供的附件图纸等,如果需要附件,请联系上传者。文件的所有权益归上传用户所有。
- 3. 本站RAR压缩包中若带图纸,网页内容里面会有图纸预览,若没有图纸预览就没有图纸。
- 4. 未经权益所有人同意不得将文件中的内容挪作商业或盈利用途。
- 5. 人人文库网仅提供信息存储空间,仅对用户上传内容的表现方式做保护处理,对用户上传分享的文档内容本身不做任何修改或编辑,并不能对任何下载内容负责。
- 6. 下载文件中如有侵权或不适当内容,请与我们联系,我们立即纠正。
- 7. 本站不保证下载资源的准确性、安全性和完整性, 同时也不承担用户因使用这些下载资源对自己和他人造成任何形式的伤害或损失。
最新文档
- 2025年部编版二年级上册语文分层教学计划
- 半导体厂重要环境因素控制措施
- 机场跑道施工进度计划和进度保证措施
- 四年级健康与安全教育方案计划
- 2024-2025学年度网络安全保护计划
- 2025年小学五年级科学教学信息化发展计划
- 小学科学教研计划课外拓展
- 口腔诊所前台接待话术及工作流程
- 五年级下册体育课程安全保障计划
- 以建模教学为翼展数学应用之翅:探索数学教育新路径
- 河南省郑州市第十七中学2025年英语七年级第二学期期末质量跟踪监视试题含答案
- 设备技改项目管理制度
- 浙江万泰公司安全设施试运行总结报告
- 2025至2030中国天然水晶手镯行业商业模式及发展前景与投资报告
- 应急救援无人机系统应用解析
- 复读班课堂管理制度
- 关于教育减负的议论文
- 2025至2030年中国电力大数据行业市场动态分析及发展前景研判报告
- 2025年安徽省中考英语试卷(含答案)
- 思想道德与法治2023年版电子版教材-1
- 2025至2030年中国侧背光源行业投资前景及策略咨询报告
评论
0/150
提交评论