

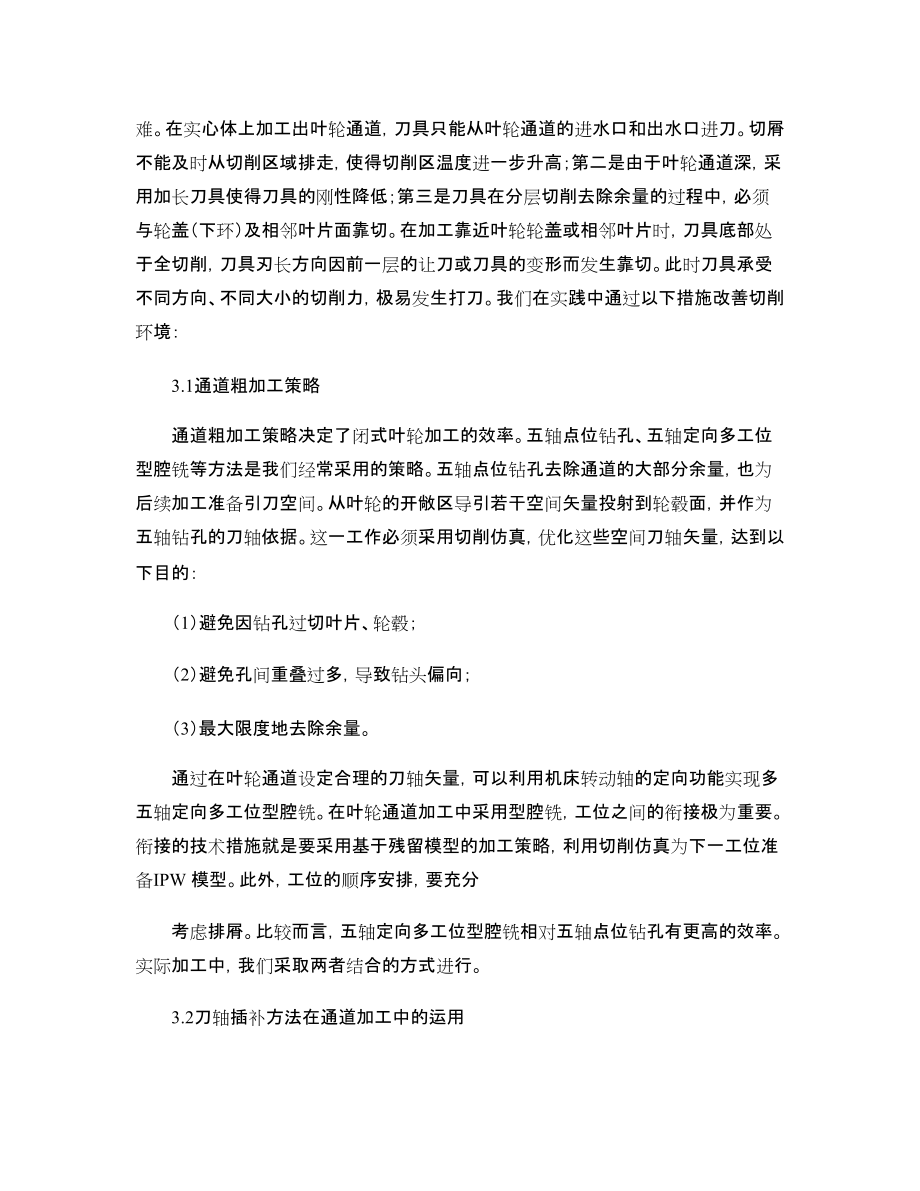


版权说明:本文档由用户提供并上传,收益归属内容提供方,若内容存在侵权,请进行举报或认领
文档简介
1、闭式叶轮五轴联动数控加工关键技术研究司徒渝1、2 周奎1、2 吴伟3 许明恒1(西南交通大学 四川工程职业技术学院东方电机股份有限公司 618000 四川德阳 123摘 要: 本文研究了闭式叶轮在五轴联动机床中加工的流程及关键技术,并结合DMU-100T 机床的特点与性能实现了闭式叶轮的数控加工。关键词: 五轴联动;闭式叶轮;DMU-100T ;后置处理中图号: TP391.72 文献标识码:A1 引 言闭式透平叶轮为轮盖,轮毂与叶片一起整体成型,其几何结构和加工工艺过程极为复杂,既要保证几何形状的要求还要保证叶片表面质量的要求,相邻的叶片之间,叶片与轮盖之间空间较小,切削环境恶劣,极易产生干
2、涉,刀轴矢量约束较多;闭式透平叶轮材料为0Cr18Ni10Ti 不锈钢, 切削性能较差。选择合理的刀具及切削用量,改善切削环境,定制合理的刀具轨迹和刀轴矢量,准确的后置处理,成为我们必须要解决的关键技术。2 材料特性对切削性能的影响及对策叶轮材料为0Cr18Ni10Ti, 切削性能较差。大量的Cr 和Ni 使钢在常温下呈奥氏体状态,不但有高的抗腐蚀能力,而且其塑性和韧性也较高。高的塑性和韧性,降低了切削性能。塑性愈高,则切削力大,切削区温度高,切屑易粘结,刀具磨损大。材料的韧性愈高,则断屑愈困难,容易打刀。 0Cr18Ni10Ti 导热性能差,加工过程中,切削热不易通过切屑和工件传出,使得切削
3、区温度较高。较高的温度不仅使切削刃硬度下降,降低刀具使用寿命,而且切屑易粘结,加速刀具磨损。 加工硬化是0Cr18Ni10Ti 的一个突出特性。加工硬化是指加工经过切削加工后,加工表面硬度增高,而塑性下降的现象。这种现象产生的原因是由于加工面表层受力作用而产生塑性变形。塑性变形使晶体间剪切滑移,晶格严重扭曲、拉长、纤维化以及破碎,从而引起加工面表层硬度的增加。材料的塑性愈高,冷硬性能也就愈高。如果说材料的高塑性是加工硬化的内在原因的话,那么切削刀具和切削用量是加工硬化的外在原因。经试切对比实验和经济性的综合考虑,闭式透平叶轮加工刀具选择国产铝高速钢【501(W6Ma5Cr4V2Al】刀具,铝高
4、速钢中Al 能提高W 、Mo 在钢中的溶解度,产生固溶强化,同时Al 的化合物在钢中起“钉扎”作用。Al 的加入增加了高速钢的碳化物析出量,从而提高了钢的抗回火性和红硬性,故钢的常温、高温硬度和耐磨性均能提高,强度和韧性也都比较高。同时,铝的加入改善了钢的韧性,并使刀具切削时不产生钢屑粘刀现象。另外,铝高速钢刀具采用比硬质合金刀具更大的前角,刃口锋利,切削轻快,被切削金属的变形和前刀面的挤压摩擦就小,需要的变形功和摩擦功少,从而产生的切削热也少。前角增大也使得加工面表层塑性变形减小,切削力减小,大大减轻了加工硬化现象,从而提高了生产效率。为了延长刀具寿命得到良好的加工质量,加工中及时对刀具进行
5、研磨也是必须的,定时对刀具的前刀面、后刀面进行研磨,清理刀具刃部的细微粘结,提高前后刀面的光洁度。保证刀具前后刀面具有较低的粗糙度,可以减少刀具与切屑及工件表面的摩擦,从而减少摩擦产生的热量,减少切屑粘结,减少磨损和崩刃。另外,在切削过程中加入植物性切削液起到冷却和润滑作用,可以降低切削区的温度,使前后刀面形成润滑膜,减少刀具与金属表面的直接接触,减轻摩擦和粘结。 3 切削环境对切削性能的影响及对策闭式叶轮为轮盖,轮毂与叶片一起整体加工成型,闭式叶轮相邻叶片间的通道为实心体,通道加工受轮盖、相邻叶片遮挡的限制,刀具只能从叶轮通道的进水口和出水口进刀,切屑不能及时从切削区域排走。使得切削环境极为
6、恶劣。首先是排屑困难。在实心体上加工出叶轮通道,刀具只能从叶轮通道的进水口和出水口进刀。切屑不能及时从切削区域排走,使得切削区温度进一步升高;第二是由于叶轮通道深,采用加长刀具使得刀具的刚性降低;第三是刀具在分层切削去除余量的过程中,必须与轮盖(下环)及相邻叶片面靠切。在加工靠近叶轮轮盖或相邻叶片时,刀具底部处于全切削,刀具刃长方向因前一层的让刀或刀具的变形而发生靠切。此时刀具承受不同方向、不同大小的切削力,极易发生打刀。我们在实践中通过以下措施改善切削环境:3.1通道粗加工策略通道粗加工策略决定了闭式叶轮加工的效率。五轴点位钻孔、五轴定向多工位型腔铣等方法是我们经常采用的策略。五轴点位钻孔去
7、除通道的大部分余量,也为后续加工准备引刀空间。从叶轮的开敞区导引若干空间矢量投射到轮毂面,并作为五轴钻孔的刀轴依据。这一工作必须采用切削仿真,优化这些空间刀轴矢量,达到以下目的:(1)避免因钻孔过切叶片、轮毂;(2)避免孔间重叠过多,导致钻头偏向;(3)最大限度地去除余量。通过在叶轮通道设定合理的刀轴矢量,可以利用机床转动轴的定向功能实现多五轴定向多工位型腔铣。在叶轮通道加工中采用型腔铣,工位之间的衔接极为重要。衔接的技术措施就是要采用基于残留模型的加工策略,利用切削仿真为下一工位准备IPW 模型。此外,工位的顺序安排,要充分考虑排屑。比较而言,五轴定向多工位型腔铣相对五轴点位钻孔有更高的效率
8、。实际加工中,我们采取两者结合的方式进行。3.2刀轴插补方法在通道加工中的运用叶片扭曲且包角较大,刀具要在通道内要合理摆动,使得刀具尽可能地接近叶片的两侧面而又不过切轮毂及轮盖,采用通常的刀轴驱动方法很难实现。刀轴插补(Tool Axis Interpolation)这一功能对于叶轮通道加工非常有用,它通过在叶片与轮毂的交线上定义一系列的矢量以控制刀轴,轮毂面上其余刀具位置点的刀轴矢量由U 、V 双向线性插值或样条插值获得。这样,刀轴能很好地按照加工的需要而得到控制,在不过切的情况下,最大限度地减少叶片面与轮毂之间的残留区。边界矢量的定义是一个十分细致的工作,基本原则是:避免刀轴的突变,保证刀
9、轴平滑变化。3.3 SWARF方法在叶片精加工中的运用SWARF 方法也叫侧刃或表面驱动法,SWARF 驱动刀轴随叶片直纹面的U 向或V 向连续变化,刀具底部接触轮毂面。侧面接触叶片表面形成单条刀路,从而实现叶片的精加工。3.4切削仿真、机床仿真与刀轴优化计算机仿真技术在数控编程中的应用已日臻成熟,切削仿真与机床仿真已成为多轴编程的重要的验证手段。单纯的基于经验的刀位轨迹目测检查已不能满足生产需要。切削仿真能在刀位计算阶段及时发现刀位可能产生的过切、刀柄与工件、夹具的碰撞。采用切削仿真是优化叶轮加工刀位计算的必须手段。切削仿真系统直接读入STL 文件和CLS 文件,并设置刀具结构和刀柄结构,即
10、可进行切削仿真。在切削仿真过程中如发现干涉和碰撞,需反复修改刀轴控制参数,直至完善。采用切削仿真是叶轮加工中最繁琐的工作, 但正是由于大量采用切削仿真,两种不图1 叶轮五轴加工机床仿真同型线的叶轮均是一次加工成功,未发生过切、干涉与碰撞。机床仿真能依据后处理产生的数控程序,模拟零件装夹与加工中机床的真实运动情况,及时发现铣头、滑枕等机床本体与工作台、工件、夹具等的碰撞,如图1所示。4 闭式叶轮数控加工在DMU-100T 机床中的实现闭式叶轮数控加工流程如图2所示,经数控加工工艺规划,刀位轨迹计算,切削仿真与干涉检查,参数优化后便形成了一系列的刀位文件(CLS )。刀位文件以APT 语句方式定义
11、了刀具参数、主轴参数、进给参数等,并按照工件坐标系描述了刀位点的运动轨迹和刀轴向量(I ,J ,K )。机床控制系统还不能直接用刀位文件控制机床的动作或状态。因此,我们必须据机床的控制系统及行程参数,利用专门的后置处理器(后置处理程序),通过数据转换、坐标变换等方式将刀位文件处理成机床坐标系中,数控系统识别的指令和数据,从而实现对机床的控制。图2 闭式叶轮数控加工的主要流程DMU-100T 是从德国DMG 公司引进的一台全闭环五轴联动数控加工中心,采用主轴摆动+圆工作台旋转结构。行程参数为:X 轴 1080mm ,Y 轴 710mm, Z轴 710mm ,B 轴(主轴摆动)103°,
12、C 轴(工作台旋转)360°。该机床具有转速高、联动结构稳定性高、五轴联动技术成熟的特点。机床控制系统采用HEIDENHAIN iTNC 530系统。利用UG/Post Builder软件构建DMU-100T 机床专用的后置处理器如图3所示,并将B 轴矢量定义如下:set mom_kin_4th_axis_vector(0 0set mom_kin_4th_axis_vector(1 1set mom_kin_4th_axis_vector(2 0B 轴转角限制变量定义如下: set mom_kin_4th_axis_min_limit -91set mom_kin_4th_axis
13、_max_limit 12图3 DUM-100T后置处理器经DUM-100T 后置处理器对刀位文件后置处理后,闭式叶轮部分数控加工程序如下: 31 L X-295.584 Y-17.641 Z370.086 B-51.438 C30.089 F4000. M3 M2532 L Z60.476 F2000.33 L X-236.146 Z37.143 F850.34 L X-236.482 Y-17.382 Z37.846 B-51.55 C30.134 F1000.35 L X-236.811 Y-17.414 Z37.902 B-51.638 C30.18936 L X-236.923 Y-
14、17.646 Z38.054 B-51.826 C30.2441371 M127 1372 M1291373 L M5 1374 M50 1375 M23 1376 L B+0 R0 F2000 1377 M30 1378 END PGM BLADE_f MM 图4 闭式叶轮数控加工 数控加工程序经后经模拟仿真及机床空运行验证后, 完全能满足 DMU-100T 机床及闭式叶轮数控加工的需要,其加工现场如图示 4 所示。 4 结束语 五轴联动数控加工是数控加工中的高技术之一,它涉及三维造型技术、刀位计算技术、计算机 仿真技术、 后置处理技术、 金属切削技术等多个环节。 我们依靠自主技术开发, 较
15、短的时间里在 DMU 100T 机床上完成五轴联动加工技术开发并应用于叶轮的生产。通过对 TCPM 技术的深入研究,在曲 面五轴联动加工中实现刀长和机床几何的自动补偿。结合 DMU 100T 机床特点对叶轮加工进行技术 优化,在通道五轴联动加工技术方面有了新的突破。 参考文献: 1 刘雄伟. 数控加工理论及编程技术 .北京:机械工业出版社, 2003. 2 吴 伟.数控加工扭曲型面成型机理及计算方法研究 .成都: 机械, 1990(3 3 HEIDENHAIN. Users manual for Conversation format. Germany :HEIDENHAIN, 2002. 作者简介: The key technique of 5-axis NC machining research and manufacturing for closed integral impeller Situ Yu (Sichuan Engineering Technical College,Sichuan
温馨提示
- 1. 本站所有资源如无特殊说明,都需要本地电脑安装OFFICE2007和PDF阅读器。图纸软件为CAD,CAXA,PROE,UG,SolidWorks等.压缩文件请下载最新的WinRAR软件解压。
- 2. 本站的文档不包含任何第三方提供的附件图纸等,如果需要附件,请联系上传者。文件的所有权益归上传用户所有。
- 3. 本站RAR压缩包中若带图纸,网页内容里面会有图纸预览,若没有图纸预览就没有图纸。
- 4. 未经权益所有人同意不得将文件中的内容挪作商业或盈利用途。
- 5. 人人文库网仅提供信息存储空间,仅对用户上传内容的表现方式做保护处理,对用户上传分享的文档内容本身不做任何修改或编辑,并不能对任何下载内容负责。
- 6. 下载文件中如有侵权或不适当内容,请与我们联系,我们立即纠正。
- 7. 本站不保证下载资源的准确性、安全性和完整性, 同时也不承担用户因使用这些下载资源对自己和他人造成任何形式的伤害或损失。
最新文档
- 聚焦2025:医药企业研发外包(CRO)模式下的数据安全与隐私保护分析
- 2025年城市新区规划调整可能导致的社区治理风险分析报告
- 镇区道路维护管理办法
- 新人入职行政制度培训
- 臂丛神经超声解剖
- 文丘里教学课件
- 顺德员工餐厅管理办法
- 教学课件怎么下
- 化妆品公司培训部年终回顾
- 初中英语人教版说课课件
- 2025年7月国开电大行管本科《城市管理学》期末纸质考试试题及答案
- 企业间车辆无偿互借合作协议
- 中科大水污染控制工程课件04活性污泥法-2活性污泥净化反应影响因素与主要设计、运行参数
- 2025年中国旅游集团招聘笔试备考题库(带答案详解)
- 中国IBD蓝皮书-中国炎症性肠病医患认知暨生存质量报告:克罗恩病部分
- 住院医师规范化培训汇报
- 2025至2030中国电动踏板车行业项目调研及市场前景预测评估报告
- 中国公安信息化市场前景预测及未来发展趋势报告
- 粮食机收减损培训课件
- 2025至2030中国耐腐蚀高温合金行业发展趋势分析与未来投资战略咨询研究报告
- 人文关怀病区管理制度
评论
0/150
提交评论