


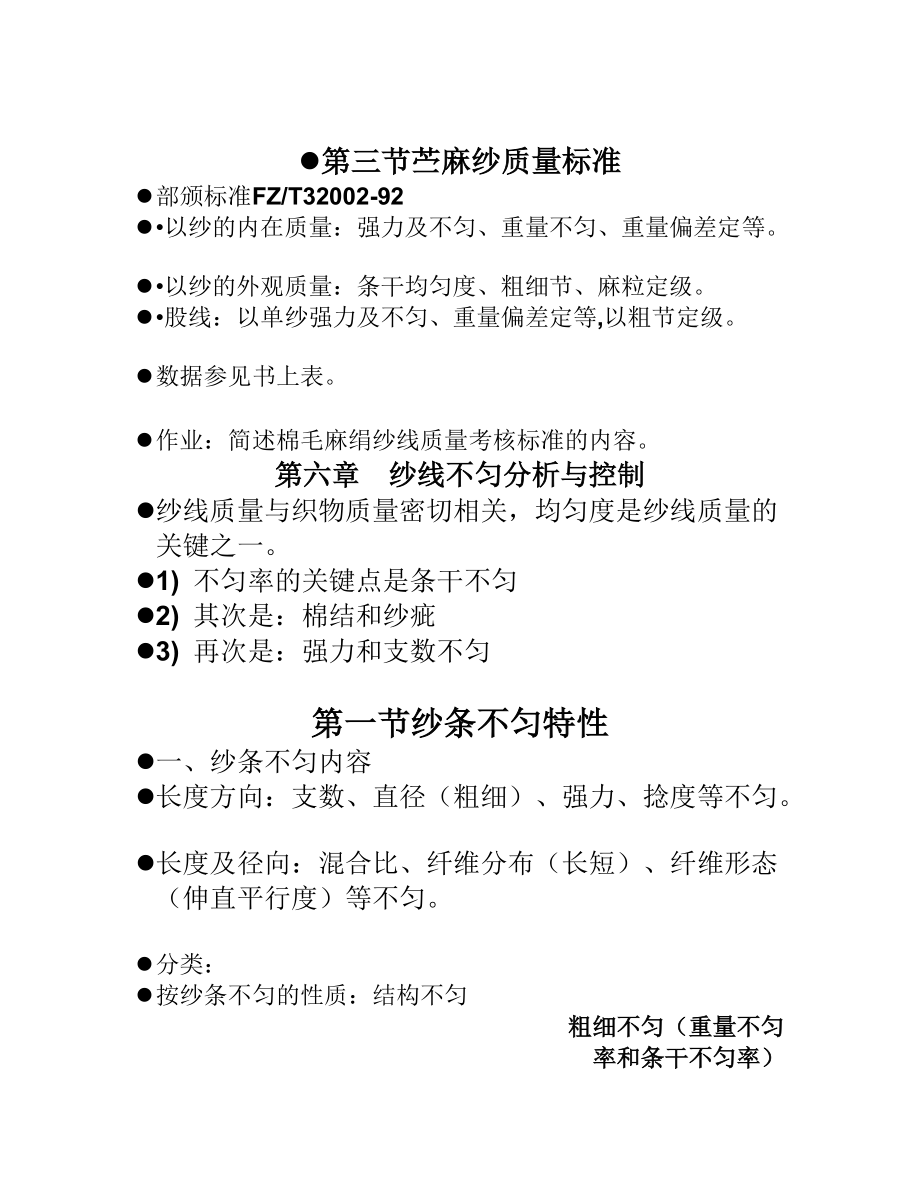

版权说明:本文档由用户提供并上传,收益归属内容提供方,若内容存在侵权,请进行举报或认领
文档简介
1、第五章 纱线质量标准l 第一节棉纱质量标准l 作为售纱和企业下道工序输入的半制品,本白棉纱的检验分等,一般按国家技术监督局发布的GB/T398-93执行。由于未再制定新的标准,因此,国内多数厂家只用此标准评定纱线等级,而更多是用乌斯特公报来衡量纱线质量。l 第二节 毛纱线质量标准l 一般毛纱线均作为企业内部的半制品加以考核,没有国家标准,只有行业标准或地方企业标准。l 一般以物理指标分等,外观疵点分级,分等指标有:l 特数偏差;重量不匀;捻度不匀;l 平均强力不小于CN(断裂长度);低档纤维含量;l 含油率;染色牢度。l 其中三项指标是在售纱时考虑l 分级指标有:纱疵大肚纱l 用黑板条干或us
2、ter条干l 粗纺、精纺参见书上表。l 第三节苎麻纱质量标准l 部颁标准FZ/T32002-92l 以纱的内在质量:强力及不匀、重量不匀、重量偏差定等。l 以纱的外观质量:条干均匀度、粗细节、麻粒定级。l 股线:以单纱强力及不匀、重量偏差定等,以粗节定级。l 数据参见书上表。第四节绢丝l 质量标准部颁标准FZ/T42002-97桑蚕绢丝指标:断裂长度;支数不匀;条干不匀;洁净度;千米疵点数;支数偏差;强力不匀;断裂伸长度;捻度偏差率;捻度不匀率。其中:对织物外观有影响用黑板观察第五章 纱线质量标准l 第一节棉纱质量标准l 作为售纱和企业下道工序输入的半制品,本白棉纱的检验分等,一般按国家技术监
3、督局发布的GB/T398-93执行。由于未再制定新的标准,因此,国内多数厂家只用此标准评定纱线等级,而更多是用乌斯特公报来衡量纱线质量。l 是全世界纺织工业中纤维、条子、粗纱和纱线进行分类的质量分级的参考指标。上一期统计公报出版于2007年,2012年将出版新的统计公报。采用乌斯特统计公报作为比较的标准时,纱的总质量中的特殊疵点和缺陷能很明显地表现出来,从而能迅速转化为生产过程中的改进措施。 USTER公司在世界各地用户和在瑞士的工厂中进行纤维、半制品、细纱的测试,然后进行数据整理分析,每相隔35年发表一次试验结果的统计值即USTER统计值。统计值一般分5%、25%、50%、75%、95%几档
4、,通常认为50%统计值属一般水平;25%及以下属先进水平;75%及以上属较差水平。从1957年开始,乌斯特公司推出乌斯特统计值,它是用乌斯特仪器将世界各地取样的纱线测试结果的统计值,每隔几年在乌斯特新闻公报(USTER NEWS BULLETIN)上发布一次包括棉、毛两大款纱线产品共分五档水平,用统计图的方式表示,横座标为纱的线密度(号数),纵座标为质量指标的数值,采用的是双对数座标。 l 一、国内有六项指标l 1单强l 2单强不匀l 3条干:Uster条干、黑板条干l 4重量不匀率l 5重量偏差l 6纱疵点:10万米纱疵、黑板条干纱疵l 1、普梳棉纱技术要求(参见书上表)l 2、精梳棉纱技术
5、要求(参见书上表)l 二、Uster的2001公报l 参见书上公报统计。l 第二节 毛纱线质量标准l 一般毛纱线均作为企业内部的半制品加以考核,没有国家标准,只有行业标准或地方企业标准。l 一般以物理指标分等,外观疵点分级,分等指标有:l 特数偏差;重量不匀;捻度不匀;l 平均强力不小于CN(断裂长度);低档纤维含量;l 含油率;染色牢度。l 其中三项指标是在售纱时考虑l 分级指标有:纱疵大肚纱l 用黑板条干或uster条干l 粗纺、精纺参见书上表。l 第三节苎麻纱质量标准l 部颁标准FZ/T32002-92l 以纱的内在质量:强力及不匀、重量不匀、重量偏差定等。l 以纱的外观质量:条干均匀度
6、、粗细节、麻粒定级。l 股线:以单纱强力及不匀、重量偏差定等,以粗节定级。l 数据参见书上表。l 作业:简述棉毛麻绢纱线质量考核标准的内容。 第六章 纱线不匀分析与控制l 纱线质量与织物质量密切相关,均匀度是纱线质量的关键之一。l 1) 不匀率的关键点是条干不匀l 2) 其次是:棉结和纱疵l 3) 再次是:强力和支数不匀第一节纱条不匀特性l 一、纱条不匀内容l 长度方向:支数、直径(粗细)、强力、捻度等不匀。l 长度及径向:混合比、纤维分布(长短)、纤维形态(伸直平行度)等不匀。l 分类:l 按纱条不匀的性质:结构不匀 粗细不匀(重量不匀率和条干不匀率)l 按不匀的形式:周期性和非周期性不匀l
7、 按产生的原因:随机不匀和附加不匀l 按所检验的范围:内不匀 外不匀 总不匀l 粗细不匀与片段长度的大小有关:l 短片段不匀:纤维长度(1-10)倍l 中片段不匀:纤维长度(10-100)倍l 长片段不匀:纤维长度100倍以上l 周期不匀机械因素造成l 非周期不匀牵伸波l 结构不匀:纤维分离度,纤维伸直平行度(弯钩、卷曲、倾斜),某类纤维集聚造成疵点常用于计算半制品的条干,如萨氏条干l 三、纱条不匀率结构特性l 1、内不匀、外不匀、总不匀l 内不匀反映某片段内部均匀度变化l 外不匀几个片段间的不匀率l 总不匀不分片段为整个纱的不匀率l C2总=C2内+C2外l 2、纱条不匀与片段长度的关系l
8、有限长度的不匀为内不匀CV(L)表示内不匀CV(L)值随L而增高,开始时快,随后逐渐减慢,L在1m以上时为稳定值,接近纱条CV() 的总不匀。 纱条的外不匀CB(L) CB(L)与L的函数关系则是随L而减少 L0时 CB(L) CB(0) CV(L) 2 + CB(L) 2 = CV() 2=CB(0) 2l CV值,Uster一般200米以上则认为总不匀。l CB(L) 0的变化率称为变异长度曲线。l 它的变化程度反映产品的不匀好坏,变化率斜率大说明产品好l 3、纱条不匀组成l 理想纱条随机不匀(CV1 ) l 由于纤维完全随机排列于纱条中,纤维也会形成片段内不匀称随机不匀。当纤维数n,在某
9、截面出现的概率为0,泊松分布。l 随机不匀与截面根数多少有关。l 附加不匀CV2%l 机械波,牵伸波l 纱条l 随着牵伸次数的增加,附加不匀产生叠加,使纱条粗细呈现复合波。附加不匀的大小,可以表征纺纱工艺的完善程度。l 纱条不匀与纺纱支数有关:高支纱不匀较高。l 不匀率指数I,表示纱条均匀度达到的理想程度和纺纱工艺过程的完善性。l 二、纱线不匀的测试l 1、测长切断称重法l 棉卷条子粗纱细纱均可用此法l 片段1m 5m 10m 100ml 2、目测黑板条干l 根据标样评定,可观察片段不匀的程度和内容:l 阴影、云斑、粗细节、竹节、毛羽。l 3、电容式均匀度试验仪Uster可测纱线不匀,粗细节,
10、结粒数。测试的基本原理:l 1) 检测头电容极板内纤维量转为电量的变化l 2) 基本原理:电极中有纤维通过,可看作两串联电容组合。l (3)测试方法l 常使保持在0.10.2之间。为了保证很小,实际上根据不同纱条,设档不同宽度极槽使用。l 测条子:1,2,3档20mml 测粗纱:4,5 档15mml 测细纱:6,7,8档8mm l 细纱为8mm片段长度之间的不匀值l 在恒温恒湿下进行:202,相对湿度653l 测试速度l 条子:8米/分 细纱:50200米/分l 由条干曲线的波长分析疵病部位(Y311型条干分析仪)第二节提高条干均匀度l 一、重要性 1、条干不匀:一般为2.55cm短片段不匀
11、严重的条干不匀形成粗节、细节、棉结、纱疵 2、条干不匀重要性 1) 影响外观; 布面:平整度、纹路 条影 雨状 白条影 黑条影 细节 粗节+15% 粗节+10% 2) 影响纱线强力; 3) 影响细纱断头及后道断头; 4) 影响捻度不匀;l 5)条干是技术与管理水平的综合反应。l 二、影响条干的综合因素l 1、原料对条干的影响l (1)长度:长度与牵伸区长度相适应,并要求纤维长度整齐度好,短绒率低。整齐度差,牵伸时,往往对短纤维难以控制,而使条干变差。l 棉纺:配棉长度差异24mml 短绒率:美国标准:1/2”以下的百分率 中国:33mm,19.5mm以下 33mm,15.6mm以下 棉籽上自然
12、短绒率为9,轧棉后10 -12 清钢为15%,要求高的在10-13, 在16%以上时纺纱质量下降 其中10mm以下的对条干影响最大。所以要增加排除短绒的机会,选棉时应考虑皮辊棉和锯齿棉的不同。l 毛纺l 梳毛配毛时,长度差异20%;混毛配毛时,长度10mm;绢纺精绵配绵时,相邻级相配,长度相近。短纤率16;麻绢注意超长纤维,超长纤维造成纤维同时被前后罗拉握持而造成牵伸不匀。l (2)细度:纤维细度影响纱条截面中纤维根数。l 纱线截面根数:l 由根数分布引起的不匀:l n增加,成纱条干均匀度好,所以当纺高支纱时,由于成纱中纤维根数少,应选用纤维细度细的,可提高成纱条干均匀度。同时要求纤维细度不匀
13、率小,以提高不匀率。l 配棉时,要求纤维细度差异500800公支;l 配毛时,要求直径100m 片段才能反映出来 要降低细纱重量不匀率,主要是控制细纱之前各工序的不匀 l 棉纺: 1 、提高棉卷均匀度 l 控制棉卷重量不匀率(1 )、重量偏差(1 1.5 )(开清棉工序) l 注意: 1 )提高机器运转率在85 以上,保证定量供应 2 )控制棉箱内储棉高度和密度 影响均匀混合和开松。棉高度占棉箱2/3 3/4 ,化纤1/2 ,棉箱中棉量波动少,密度均匀。 3 )天平调节装置动作正确、灵敏 4 )尘笼气流:影响棉卷横向均匀度 要求尘笼气流均匀,不产生涡流,不跑偏,不翻滚,上下集棉比7 :3 。
14、5 )防粘卷措施 l 2、降低梳理生条重量不匀率4l 1)统一落棉:落棉均匀,台间差异0.5;l 2)统一工艺,机械状态良好;l 3)换卷与生头:防接头不良;l 4)张力牵伸合理;l 5)控制车间湿度,防止棉卷粘卷,棉网破洞、破边;l 6)采用清钢联(自调匀整)。l 3、控制熟条重量偏差和不匀关键工序。l 控制熟条偏差1,(粗支2.5)l 1) 轻重条搭配;l 2) 每台每眼一个班试验3次,及时更换牵伸牙。l 4、控制粗纱重不匀l 粗纱、细纱不能降低前边的重量不匀率,只能做到不恶化或少恶化l 主要控制张力。(前后排,锭间,大中小纱)l 张力差异伸长差异1.5l 5、细纱l 1) 定设备:同品种
15、使用同一机型l 2) 加强巡回;l 3)加强设备维修l 6、自调匀整装置的应用l 清钢并上已普遍使用。l 作业:l 论述从原料到纺纱各工序如何改善条干和重不匀。 l 纱线不匀包括哪些考核指标,它们之间的关系如何? 第七章 成纱强力l 一、对后道的影响l 纱强影响纺纱工序顺利进行,影响织造顺利及织物强力。l 二、纱强的组成:l P=Q+Fl Q:全部断裂纤维所构成的部分强力l F:全部滑脱纤维所构成的部分强力l 提高纱线强力应从这两方面入手,即选用强力高的纤维;另一方面,提高纤维抱合性,增加纤维的接触面积。l 三、影响单纱强力因素l 1 原料性状l 1)长度,纤维间接触机会增加,抱合力增加从而减
16、少滑脱,当长度达到一定值时,再增加长度,强力提高不明显。l 棉16mm以下短绒:浮游纤维,粗细节,条干恶化,强力不匀,强力l 2)细度l A 当N纱一定时,纤维细,根数多,接触面积大,纤维细,断裂长度长,所以F、Q增加纱强增加。l B 纤维细柔软,内外转移机会多纤维间联系力大l C 纤维细天然卷曲多纤维间联系力大l 3) 断裂长度:长,纱强增加。l 4)成熟度 成熟度增大,纤维强力增加,但细度低,一般选用成熟度适中的纤维。纺细特纱时,着重考虑纤维细度,成熟度可稍差,由于根数多,纤维间抱合力增大,成纱强力反而不低,而纺中粗特纱时,着重考虑成熟度。5 )其他因素l 车间温湿度 吸湿横截面,延伸性,
17、纤维柔软,抱合力。 l 2 纺纱工艺 1)开清、梳理工序 工艺参数配置要利于开松、梳理,增加纤维分离度,排除杂质和短绒,同时要减少纤维损伤;棉卷结构良好;梳理应“紧隔距强分梳”,加强梳理,减少损伤和短绒。 开清参数:打手速度、打手与罗拉与尘棒PT、尘棒间PT、打手型式等l 梳理参数:刺辊n、分离工艺长度、除尘刀位置、锡林与盖板PT、盖板速度。l 2)并条、粗纱l 提高纤维平行顺直度,提高条干均匀度。l 粗纱适当提高温湿度,使回潮率在7%,一定回潮率有利牵伸,加强对纤维运动的控制,降低粗纱不匀。l 3)细纱工艺对成纱强力的影响l 细纱工艺配置要有利于条干,条干不匀,强力。l 细纱捻度l 临界捻度
18、l 捻度:l a 纤维间的联系力l 加强,滑脱减少,l 增加了纤维断裂根数,强力l b 纱轴向承受的有效分力减少,强力l c 内外层不同,纤维应力分布不同。使纤维断裂的不同时性加剧l d ,纤维受张力,应力,使可承受的拉力,强力。l 故存在临界捻度。l 捻不匀 捻不匀,强力差异大 故锭速要小捻不匀,强力不匀前罗拉输出的须条结构要有良好的紧密度。 即牵伸区选用合适的集合器,使前罗拉输出须条紧密。l 纺纱张力适当,可使纤维伸直、纱条紧密。 l 1.简述强力的构成及其对后道的影响。l 2.论述从原料到纺纱各工序影响成纱强力的因素。 第八章 成纱结粒和毛羽l 短纤维棉纺:l 一、影响:l 1、纱、布外
19、观,印、染色差;l 2、条干不匀:粗节内棉结占18;l 3、断头:由于强力和张力突变。l 二、分类: 1、杂质:破籽屑、尘土、不孕籽屑、软籽表皮、带纤维籽屑、僵片。 2、棉结纤维相互扭结而成的小棉团。 有:松棉结结构松散周围有长纤。 紧棉结短绒扭结染后色浅。 状态棉结短纤或纤维包含僵片等杂质。 3、白星:死纤维形成。l 4、毛羽:纤维头端、短绒、飞花、纤维扩散形成。l 三、测试 1、棉结(白星)杂质,可用黑板目测计数和Uster仪器检测。l 2、毛羽检测l 目:目测l 显微镜l 光:光电计数l 重:烧毛失重l 四、减少棉结杂质l 1 原棉性质l 1) 原棉本身杂质、不孕籽、棉籽、破籽。l 2)
20、 成熟度l 成熟度与细度、短绒率、僵棉呈负相关;而细度、短绒率、僵棉与棉结杂质呈正相关。l 成熟度正常,抗弯、抗压、抗打击性能好,成纱棉结杂质少。成熟度系数一般选1.51.6以上。l 3)短绒l 不易伸直平行、易扩散粘附l 短纤维难控制,梳理中易绕l 大部分是较脆弱的未成熟纤维l 4)轧棉质量l 锯齿棉:纤维损伤大,棉结索丝多,含杂少。l 皮辊棉:纤维损伤小,但无排杂装置,僵棉、软籽表皮多,棉结少,含杂多。l 2、纺纱工序 1) 棉结的产生和排除 棉结的排除、形成和分裂贯穿在整个工序中。 从原料到清棉,结杂、短绒增加,到梳棉,排除多于产生数,经并条和粗纱,棉结杂质:粒数,粒重。 牵伸增加棉结,
21、由于纤维间磨擦所致。 梳棉是控制棉结、杂质、短绒的关键工序:l 刺给棉板,锡盖板,锡道夫:易形成棉结和分裂棉结,原大变小,原松变紧。l 2) 清钢合理分工l 粘附力较大的带纤维籽屑,粘结纤维的杂质,应在梳棉上清除。l 原棉含杂3,则棉卷应含杂11.5l 清棉:落棉率与原棉含杂率的比率为80110; 落棉含杂率在5068; 除杂效率5060。l 梳棉:总落棉率34 后车肚落棉对棉卷含杂的比为120220 落棉含杂40以上 除杂效率:刺辊5060 盖板510 吸尘10l 3) 提高分梳质量l 喂入棉卷结构良好l 紧隔距强分梳l 减少搓转l 增加分梳件l 除尘刀:低刀(落杂大、)大角度(回收)。l
22、4)精梳工序除杂最有效的工序l 5)温湿度:清棉60,棉卷回潮6.57,梳棉5560,生条回潮率6.5。l 6)并条部分提高纤维平行顺直。l 五、减少白星l 死纤维棉结,它的形成和防止与棉结相同。l 六、减少毛羽l 1.种类:通常以2mm以上计(以纱干为主体)分顺向、倒向、两向、浮游毛羽。l 2.形成:l 纤维弯钩、短绒;l 牵伸过程中纤维扩散;l 气圈离心力;l 加捻部件不清洁;l 飞花。l 3 .控制: 减少原料中的短绒量; 精梳落棉毛羽; 提高粗纱捻系数; 进行集束,防止扩散; 钢领钢丝圈,特别是钢丝圈:重量、截面形状、圈形、通道、交叉缺口。l 长纤维毛麻绢纺l 一、减少毛麻绢成纱的结粒
23、l 1、毛粒的成因和控制l 1) 原料在预处理过程中产生毡并,初加工工艺要适当防止湿热状态下的毡缩l 2) 梳毛条中毛粒过多l 主要是:净毛含油多、土杂多、隔距不当、针布不锋利、回潮大、速比不当、操车周期过长。l 3) 针梳条毛粒过多l 主要是:针板不良、缺针、断针、清洁机构工作不良、毛条通道不洁。l 4) 精梳条毛粒过多l a 、毛网正面毛粒多l 喂入过大、厚薄不匀、园梳梳理不良、隔距过大、始梳位置不当、小毛刷过高、拔取隔距不符工艺要求、喂给长度过长。l b 、毛网反面毛粒多l 顶梳位置过高、产生拉毛、顶梳不洁、缺针或抬起过早。l 必须从原料开始,各道严格把关。l 2、麻粒成因与控制l 1)
24、 成因l 与纤维的机械物理性质有关:l 纤维愈长、细,则易于弯曲形成麻粒。l 梳理过程中纤维断时,由于急弹性而产生回缩卷曲形成麻粒。l 喂入量过大、隔距过大、针布不锐利、缺针、断针、纤维绕锡林,在针面间搓转,产生麻粒。l 回潮过高,易于缠结,易绕锡林,降低梳理效率。l 工艺参数不当,清洁工作不力,易生麻粒。l 针、并、精梳条,麻粒过多,与毛粒成因一样。l 2) 麻粒控制l 针对性地在原料、加油、回潮、各道设备状态,清洁工作,操作程序方面加强管理。l 3、绵粒的成因与控制l 1) 绵粒成因:即l 原料本身存在l 精练过熟l 纤维细长易缠结形成绵粒l 梳理工艺不当l 2) 绵粒控制l 减少绵粒,从
25、原料抓起。l 对原料状态、加油水、回潮率应严格控制;l 各道工艺设计,设备状态,操作规范,清洁工作加强管理。特别应加强精梳及烧毛工序,清除绵粒的作用。l 论述从原料到纺纱如何减少成纱的棉结杂质。 布面疵点l 直至现在为止,国际间还没有任何认可布料检定标准,但西欧和美国等地均有其常用十分制评法、四分制评法以控制处理布料疵点,这两个是最常用的制度。l l)十分制评法此检定标准适用于任何纤维成份、封度和组织的梭织坯布及整理布上。由于一般买家所关心的是布料因疵点所剪掉的数量及引致的投诉,并非是疵点的成因,所以此评分法只是根据疵点的大小来评核等级。评核方法是检查人员根据疵点评分标准查验每匹布料的疵点,记
26、录在报告表上,并给处罚分数,作为布料之等级评估。 。l a.疵点评分以疵点之长度分经线不同之扣分方法。 经疵长度 处罚分数 10-36吋 10分 5-10吋 5分 1-5吋 3分 1吋以下 1分 经疵长度 处罚分数 全封度 10分 5吋至半封度 5分 1-5吋 3分 1吋 1分 除特别声明外,否则验布只限于检查布面的疵点。另外,在布边半吋以内的疵点可以不需理会。每码布料的经疵和线疵评分总和不得超过10分;换言之,就算疵点很多或非常严重,最高处罚分数都只是10分。若疵点在一个很多的长度重复地出现,在这情况下,就算处罚分数的总和较被查验的码数小,该匹布料也应评为次级l b.等级评估根据检查的结果,
27、将彷匹评估为首级品质或次级品质。如果处罚分数的总和较被查验的妈数小,该匹布料则被评为首级;如果处罚分数的总叻超过被查验的码数,该匹布料则被评为次级。由于较阔布封附有疵点的机会比较大,所以当布封超过50吋首级。布料的处罚分数限制可以约略放宽,但不应多于 10。 l 2) 四分制评法该评分法主要应用于针织布料上,但亦可应用于梭织布料。四分制跟分制的基本概念和模式非常相似,只不过是判罚疵点分数上不同而已。该评核方法跟分制J一样,检查人员跟据疵点评分标准查验每匹布料的疵点,记录在报告表上,并给予处罚分数,作为布料之等级评估。a.疵点评分疵点扣分不分经纬向,依据疵点表长度给予一恰当扣分。 疵点长度 处罚
28、分数 3吋或以下 1分 超过3吋但不超过6吋 2分 超过6吋但不超过9吋 3分 超过9吋 4分 较大的疵点(有破洞不计大小)每1码计四分检查评定 除特别声明外,否则只须检查布面的疵点。另外,在布边一吋以内的疵点可以不需理会。不论幅宽,每码布料的最高处罚分数为4分。特殊瑕疵如破洞、轧梭,一律扣4分。l c.等级评估不论检查布料的数量是多少,此检定制度须以一百平方码布料长度的评分总和为标准。若疵点评分超过40分,该匹布料则便被评为次级及不合标准。 d.计算公式为:100平方码平均扣分数=(总扣分X 100 X 36)检查总码数X规格幅宽(吋)除非面料 的规格不对,否则表面不可见的疵点不计分数,小疵
29、点不做记录。在一码内不允许超过4分,任何连续性疵点均做4分评定,例尺寸不良、破洞做4分。象横档、色差,狭幅、,皱纹、斜路、,甚至织物不完整,均按4分/码计算。不必考虑长度破洞(纱被剪或断纱,或少了针迹),下面的情况做4分处理: 有手臂长的油污迹, 明显的抽纱或粗纱, 纬纱不良, 缺色, 少经少纬。下面的疵点按照长度来决定,染色条,稀缝,裂缝 水平或垂直方向的纹路,皱纹,轻重纱头,横档。l 三.面料 检查l 下面几点是指导性的原则,以便在检查布的过程中得到应用。l 1.有下列现象就的返工l 1).色差超过允许范围l 2).连续性的起球,或明显的折痕或修补痕迹l 3).规格误差+-超过5%印花疵点
30、(指的规律性或成批性)成品规格不符合l 4).长度少于25码打结纱超过1处,在大批时允许多个打结纱但其间距不得少于25码不熟棉或坏棉影响成品的外观。l 5).结纱距少于25码有明显的色差,l 例.边到边l .边到中心l .头到头在长度方向同幅内不得超过下面的标准,以免导致面料 结构的扭曲。 l A. 45英寸1 1/2英寸; l B. 60英寸2英寸; l C. 70英寸3英寸; l D. 120英寸4英寸; l E.不允许有下列现象:松布或波纹状、皱纹单边或两边布边紧、折痕布波纹状; l F.由于布身的皱纹,导致拉布不平和裁剪的疵点。l #: 在查布时,在布边内超1/2“连续3码疵点,不必打
31、分 视做返工,连续的疵点须剪掉。l 2.物理结构检查l 1).重量检查 l 重量(规格)允许+-5%,重要可以用单位长度(码),盎司或单位面积码平方(同样可用公制表示),由于是平幅布,l 平方面积规格是全幅基础上,并非可裁部分(即包括无用边布)面积,长度也同样。按面积计算重量,以单位长度为准,l 指一定长度下的重量,例一批/一匹为基础按面积计算,保留两位小数,例8.65盎司每码平方,每磅1.85英尺长度以机器l 的计数器记录为准,桌上测量的数字不接受,长度可以接受,+-15%,罗纹和弹力组织+-3%允许。重量(磅,盎司)在 l 综合 的订单中不超过(单个颜色)10%,被认为是可以接受的。捡查人
32、员可以利用电子磅来检定布料的重量,利用圆形切样器,在每匹布料不同部位,切出一百平方厘米的标准面积,然后放在测量布重电子磅上,屏幕便立即准确地显示该块布料的重量。 l 2).缩率检查l 布样长度 1米 X 1米 ,80C 洗2小时, 拿出放 , 再洗2次, 测量缩后,长度 X 宽度 = ? l 3).幅宽检查l 在查验过程中,随意在每匹布料上度取三个阔度,幅宽三点测量:开头、中间、结尾,布幅测量时需要用硬尺,然后将结果记录在验布报告表上。,每个颜色至少一卷,当抽验数大于10卷按发货颜色总数的比例进行抽验。 幅阔测量和记录最接近的是1/8英寸,当布幅少于1/4英寸宽度时,此卷应帖上狭幅标签,l 所
33、有狭幅布料如果不返修需要重新拟订价格。当幅宽少过1/2英寸时,有必要?处理。大货布宽度,针织布从染边内l 或针孔测量,圆筒布或无边布则全部测量。筒子布最少可裁尺寸+1英寸,例表示为30-31英寸,最小为30英寸+1英寸即为l 31英寸。开幅布最小可裁尺寸+2英寸,例60-62英寸,最小为60英寸,加2英寸为最大。l l 4).长度检查l 将准备检查的布卷,逐一放在验布机上,利用米表或码表量度每匹的长度,然后将所得长度与布卷标签上长度核对,并将结果记录在验布报告表上。 l 5).色差、色牢度检查每批布颜色对照色卡,要在允许色差范围内对照色板,不是绝对准确相同,但必须是在可接受的范围之内。在同批货
34、同缸内有色差,应该发出质量好的,扣下不良部分,而且被认为一致的,除非全程对布进行编号,严格控制。每缸每色都需要一块色板,包括核色板放在一起进行对照,以便控制,对每个颜色的色牢度须保存在主档案中。检查人员可以利用对色灯箱来检定布料颜色。使用灯箱有点必须留意,这就是不论色办或货料,每次所用光源必须一致,否则所有颜色比较都是没意思的。6).纱支 由于纱支限重量成正比例,所以可以利用天秤或电子磅来检定纱线的细度。检查人员首先从批核样办中抽出一个长度的经纱,放在夭秤的一边,然后从来布中抽出同一长度的经纱,放在天秤的另一边。如果天秤保持平衡,这表示来布和批核样办的经 纱支数是相同的;但如果天秤出现不平衡,
35、这便表示两者支数存着差异。检查员可以重复以上办法来检定纬纱的细度。7.)经纬密度检查人员可以利用放大镜或布镜将布料的密度放大,利用肉眼点算在一平方吋内经纱和纬纱的数目,然后将所得数目与规格或批核样办相比,便可知道来布的密度是否合符标准。8.)组织结构跟检查经纬密度一样,检查人员可以利用放大镜或布镜,观察布料的平纹、斜纹、缎纹等的组织结构是否正确。l 四.通常布面疵点1.疵布表磨损点:布面由于摩擦或非正常力的作用,使布面有所损坏。2.背面的印渍:在印花过程中,常常背面有垫布,使染布的背面有印花的痕迹。3.横档:在织造过程中,造成的质量问题。4.斜纹路:针织,梭织布,纹路不直,或非直角状,构成斜纹
36、路。5.弓纱:弓经或弓纬(梭织和针织都有,往往是张力不匀引起。6.粗纱:织造过程中由于纬纱用光而带来的引起的粗纬或弓纬,也有其它因素引起的可能7.斑点,粒子:当纬纱用完时,一个尾巴结入织物中,把它钩出来在织物中留下的空档 8.飞色:A.纱或织物颜色B.象夹着染色物一样,引起的原因是仿纱或织造过程中的杂物和飞尘造成9.带色:色织物较多,梭织布的色纱经过布机时没,织布机上留下颜色所致,会使织物花形,图案的不全,针织布纱在导圈上留下颜色,同样造成图案和花形不良10.少色:印花过程中,阔色时,由于不平直导致未在布上沾上颜色。11.色污:印花过程中,被粘污或图案被破坏12.折痕:不同于织档,它有可能贯穿于整个布面,而折痕仅仅是成品检验,折叠过程中折布造成很难在后道工序中把它清除掉13.直档:筒子布,在染色过程中的挤压导致,布面呈现直档14.吊经:由于布机布面张力太大,超过正常的要求,通常断头引起15.筘路:由于针和筘的关
温馨提示
- 1. 本站所有资源如无特殊说明,都需要本地电脑安装OFFICE2007和PDF阅读器。图纸软件为CAD,CAXA,PROE,UG,SolidWorks等.压缩文件请下载最新的WinRAR软件解压。
- 2. 本站的文档不包含任何第三方提供的附件图纸等,如果需要附件,请联系上传者。文件的所有权益归上传用户所有。
- 3. 本站RAR压缩包中若带图纸,网页内容里面会有图纸预览,若没有图纸预览就没有图纸。
- 4. 未经权益所有人同意不得将文件中的内容挪作商业或盈利用途。
- 5. 人人文库网仅提供信息存储空间,仅对用户上传内容的表现方式做保护处理,对用户上传分享的文档内容本身不做任何修改或编辑,并不能对任何下载内容负责。
- 6. 下载文件中如有侵权或不适当内容,请与我们联系,我们立即纠正。
- 7. 本站不保证下载资源的准确性、安全性和完整性, 同时也不承担用户因使用这些下载资源对自己和他人造成任何形式的伤害或损失。
评论
0/150
提交评论